As a key raw material for stainless steel and special steel, chromium ore (chrome,chromite) is widely used in metallurgy, chemical industries, refractory materials, and other industries. It is an indispensable strategic resource for the national economy and cutting-edge defense technology. Due to its fine particle size, low grade, high impurities, and harmful elements, there are few chromium ores that can be directly smelted. Generally, ore dressing is required to obtain qualified concentrate. Gravity separation, magnetic separation, or flotation separation are often used for chromium ore dressing. These technologies can maximize production and reduce energy consumption, making the production process consistent with modern environmental protection practices.
What Is Chromium Ore?
Chromium is a silvery white metal that is extremely hard and brittle, and resistant to corrosion; it is an inactive metal. It exists mainly in the form of oxides. The only minerals of economic value are the chromium spinel family, and chromite (chrome ore) is the general name for chromium spinel family minerals. Chromium is a metal known for its excellent hardness and corrosion resistance.
The main mineral of chroium ore is chromite (chemical formula: FeCr₂O₄), which is a black or dark green mineral that usually shows a metallic luster. The main components are iron and chromium, and the chromium content is usually between 40% and 60%. Chrome ore is mainly distributed in countries such as South Africa, Kazakhstan, India, Turkey and Finland. With the advancement of technology and the improvement of environmental awareness, the mining and utilization of chrome ore are also constantly evolving. Ore dressing is usually used to recover high-quality concentrate to meet the needs of stainless steel and alloy production.
Challenges of chromium ore dressing
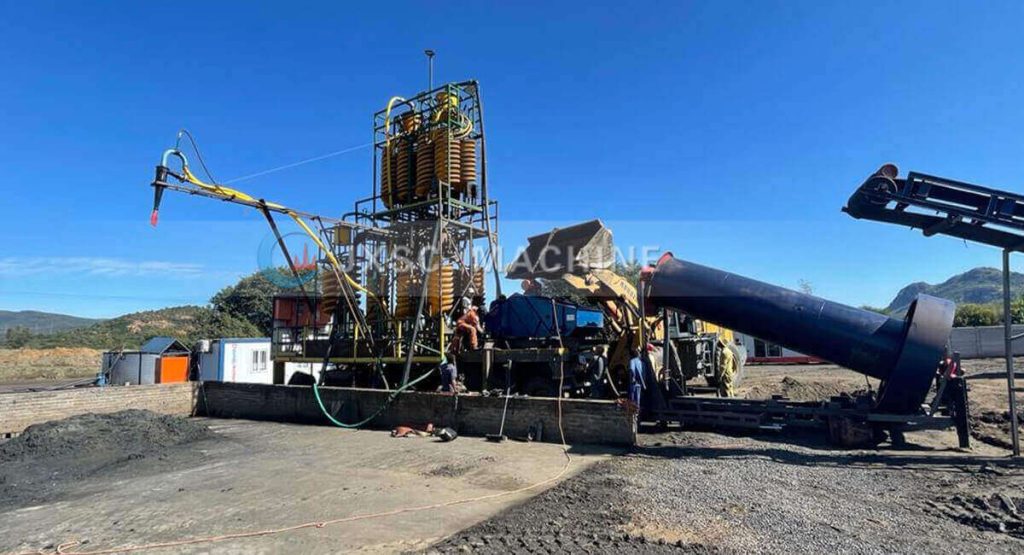
Variations in ore grade and composition: Different deposits can produce chromium of varying qualities while also containing impurities that complicate processing. The heterogeneity of the ore body means that uniform processing techniques may not produce optimal results in different parts of the mine, increasing the efficiency and cost-effectiveness of the dressing operation.
Ore dressing environment: Hazardous substances released during mining can lead to soil and water contamination, causing concern among communities and regulators. Traditional methods often involve toxic chemicals, resulting in large amounts of waste generation, harmful emissions, and habitat destruction. As mining activities become increasingly regulated, stricter compliance requirements increase production costs for sustainable practices. Sustainable and environmentally friendly practices must also include efficient separation technologies and tailings recovery programs.
Chromium ore dressing Process
Chromium ore dressing mainly uses various technologies such as gravity separation, flotation and magnetic separation, which help to improve the quality of chrome concentrate and maximize recovery. Among them, flotation is suitable for the dressing of chromium ore with a large amount of fine particles or rich in silicate minerals, separating chromite from gangue minerals such as talc, serpentine and other magnesium-silicon rich materials. However, gravity separation and magnetic separation are the most widely used beneficiation methods, applicable to a wide range of ore types. Not only can it improve productivity, but also meet increasingly stringent environmental standards and promote more sustainable mining practices.
Chromium ore dressing Flow
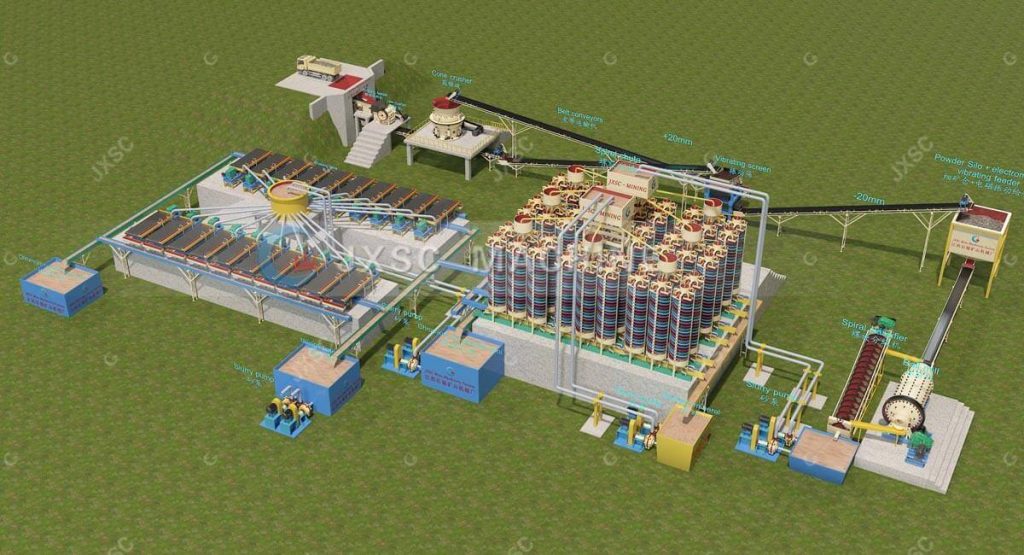
Crushing Stage
If the chromium ore raw material is a larger ore, it needs to be fed into the primary jaw crusher through a vibrating feeder, so the rock chrome ore can be fed smoothly and evenly. The vibrating feeder has grid bars, which screen the large pieces on the grid to the primary jaw crusher, and the small pieces below the grid bars go to the fine crusher through a conveyor. This can improve the crushing effect of the primary jaw crusher.
The primary jaw crusher is used to crush the large pieces of rock chrome ore into smaller sizes, and the output material goes to the next fine crusher, the cone crusher. The cone crusher crushes the rock chrome to less than 20mm, which is suitable for feeding into the ball mill, but it will first enter the vibrating screen to screen out the large pieces + 20mm, and then send it back to the cone crusher for further crushing. The 0-20mm underscreen goes into the storage bin before the ball mill. If the plant has a small capacity, the cone crusher can be replaced with other types of fine crushers, such as fine jaw crushers, hammer crushers or impact crushers.
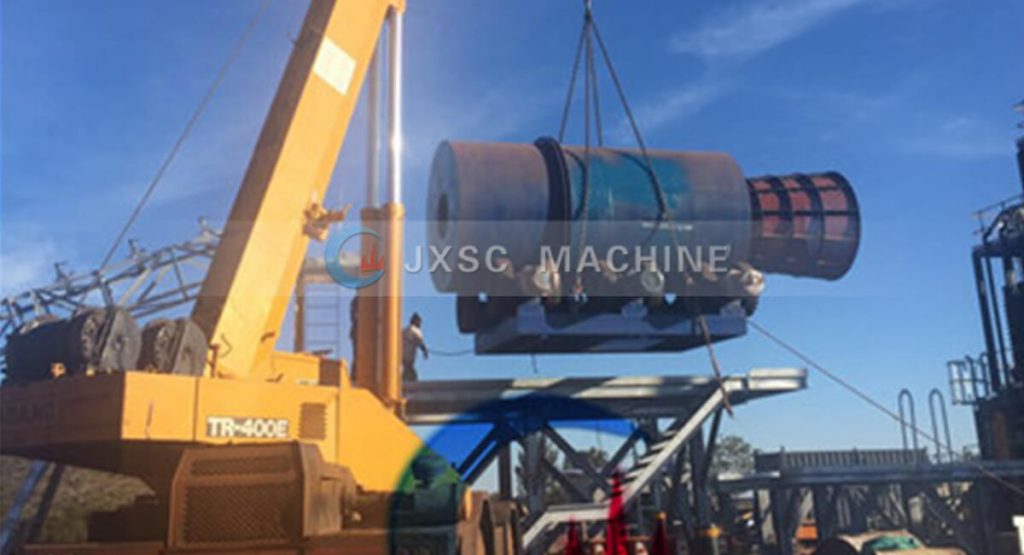
Washing stage
Chromium ore in its natural state usually contains a variety of impurities, including silicates, carbonates and iron oxides. If the surface of the chromium ore contains slime impurities, it needs to be cleaned first. The washed chrome ore has low mud content, low acid consumption value and low turbidity. By thoroughly rotary scrubber or trommel screen washing the ore, these unwanted substances will be greatly reduced, resulting in a higher grade product suitable for a variety of applications.
Grinding and Classification
The 0-20mm powder material will be smoothly fed into the ball mill by an electromagnetic vibrating feeder and a belt conveyor. The ball mill is used to grind 0-20mm into small powder, and it works with a spiral classifier. Therefore, about 80% of the slurry overflowing from the classifier is 200 mesh powder, and the oversized particles from the classifier will return to the ball mill for grinding again to form a closed loop.
Gravity separation
The 200 mesh slurry will be pumped to the gravity separator, spiral chute and shaking table. The spiral chute is used for primary concentration. In order to maximize the recovery of chromium, we use a 2-stage spiral chute separation. The medium material from the first-stage spiral chute group will be pumped to the second-stage spiral group to recover as much chromium as possible. The heavy concentrate discharged from the two-stage spiral group all enters the shaking table for re-concentration to obtain a higher-grade chromium concentrate.
Magnetic separation
If a higher-grade chromium concentrate is required, chromium ore has weak magnetic properties, and you can consider adding a high-intensity magnetic separator in the final stage.
Chromium ore dressing processes mainly include gravity separation, magnetic separation or flotation, and the choice between these technologies depends largely on the specific characteristics of the ore. Complex operating processes require a thorough understanding of mineralogy, equipment efficiency and environmental factors to increase production and reduce waste. JXSC supports customized ore dressing solutions, contact us for details on the best equipment model, process flow, machine price, etc.!