Manganese ore is a mineral with a very high utilization value, generally grayish-white with a metallic luster. Manganese ore has a wide range of industrial uses, mainly for iron smelting and alloy manufacturing, as well as in the chemical, light, building materials, and other industries. In the steel industry, the use of manganese ore is as high as 90~95%, and most of them are poor ores, so ore dressing is needed for effective separation and enrichment. There are 150 known manganese minerals, among which manganese oxide ore and manganese carbonate ore are the most economically valuable. However, manganese ore processing requires a complete understanding of the ore’s composition, properties, and characteristics to select the best beneficiation equipment to achieve the best ore-dressing effect. Usually, the processing of manganese oxide ore mainly adopts gravity separation, and the processing of manganese carbonate ore mainly adopts magnetic separation. According to the nature of the ore, crushing, screening, grinding, washing, and other processes are also indispensable in the entire processing line.
Manganese Ore Process
Manganese Oxide Ore Beneficiation Process
It is mainly composed of secondary manganese oxide ores from weathered deposits and primary and secondary manganese oxide ores from certain sedimentary and hydrothermal deposits. The manganese minerals in the ore are mainly pyrolusite, pyrolusite, and manganese ore; the gangue is mainly silicate minerals, and there are also carbonate minerals; it is often accompanied by iron, phosphorus, nickel, cobalt, and other components. Different types of manganese oxide have different colors, including black, brown-black, and pink. The hardness of manganese oxide ore process is relatively low, and manganese ore process is easy to crush and grind, so attention should be paid to over-crushing during ore dressing.
- The main method for beneficiating manganese oxide ore is gravity separation. This method uses the density difference between manganese ore and gangue material to achieve effective separation without excessive chemical intervention. Shaking tables, spiral chutes, or jigs are often used to achieve higher recovery rates while minimizing the impact on the environment.
- Weathered manganese oxide ore often contains a large amount of ore mud or other impurities, and the washing-gravity separation method is usually used in production. This process involves washing the raw ore to remove the fine mud on the surface, disperse, and separate the ore, and then using a shaking table, spiral chute, or jig to achieve a higher recovery rate while minimizing the environmental impact.
- If it is a sedimentary native manganese oxide ore, due to mining dilution, heavy media and jig gravity separation are used in production to remove gangue and obtain block concentrate.
- The iron mineral is mainly limonite if it is an iron-containing manganese oxide ore. Iron and manganese are difficult to separate by gravity separation, flotation, or strong magnetic separation, and a reduction roasting magnetic separation method is required. Because the surface of manganese oxide ore is easily wetted by water, it has poor floatability and high flotation costs. The industry usually adopts the washing-reduction roasting magnetic separation-re-selection process.
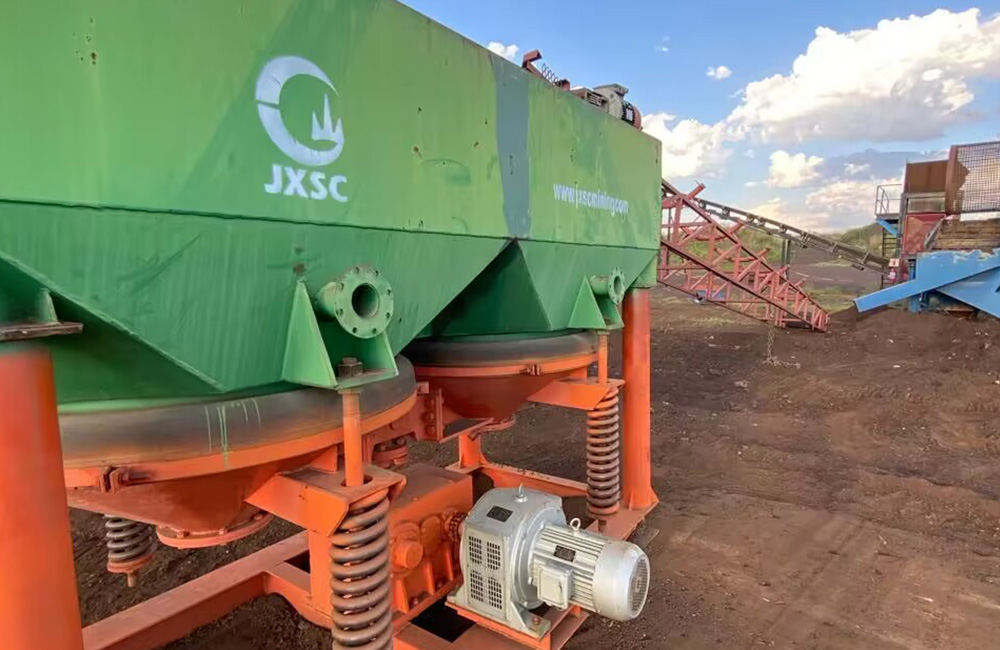
Manganese carbonate ore process
The main manganese minerals in sedimentary manganese carbonate ore are rhodochrosite, calcium rhodochrosite, manganese-containing calcite, and rhodochrosite. Gangue includes silicate and carbonate minerals; impurities such as sulfur and iron are also often associated. The ore is generally complex, and the manganese minerals are embedded in microns and cannot easily dissociate. However, manganese carbonate ore is a weakly magnetic mineral, and most of the associated gangue is non-magnetic silicate minerals. Therefore, strong magnetic separation is an important means to separate and enrich manganese carbonate. The processing of manganese carbonate ore mainly adopts strong magnetic separation, heavy medium separation, and flotation.
- The industry adopts the sequential priority flotation process for carbonaceous shale, pyrite, and manganese minerals in sedimentary sulfur-containing manganese carbonate ore.
- The flotation-strong magnetic separation process is often used for hydrothermal lead-zinc manganese carbonate ore. For some sulfur-containing manganese-rich ores, the manganese minerals are mainly sulfomanganese ore, and the sulfur can be removed by roasting.
- The production of manganese carbonate-rich ore also uses roasting to remove volatile components and obtain finished ore.
Both manganese oxide and manganese carbonate ores contain some difficult-to-separate ores. Manganese is closely coexisting with iron, phosphorus, or gangue, and the embedded particle size is extremely fine, making it difficult to separate. Therefore, it can be considered to be treated by smelting methods.
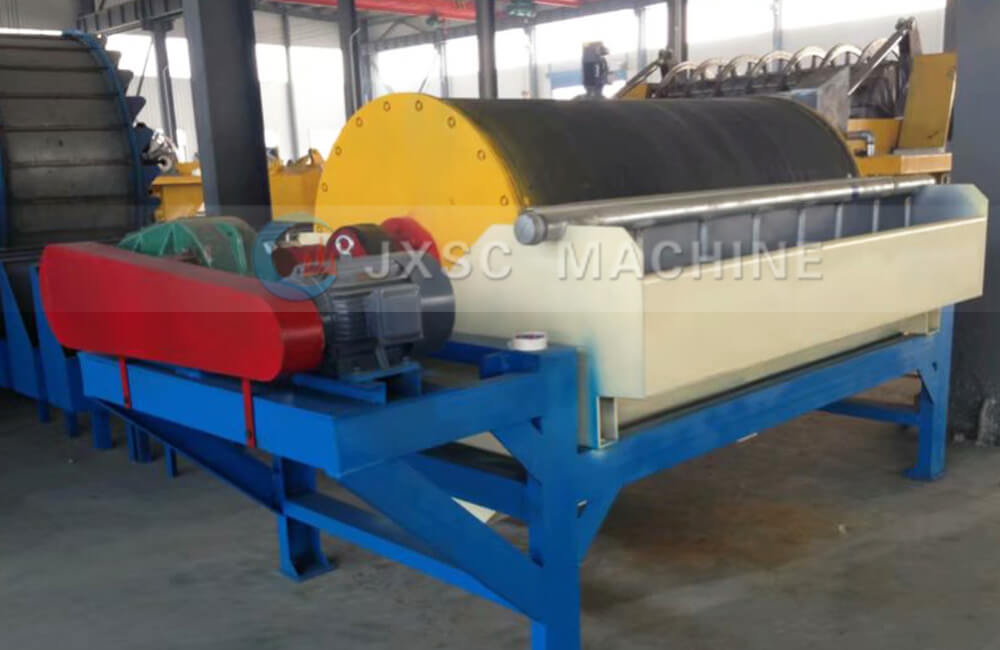
Manganese Ore Process plant Flow
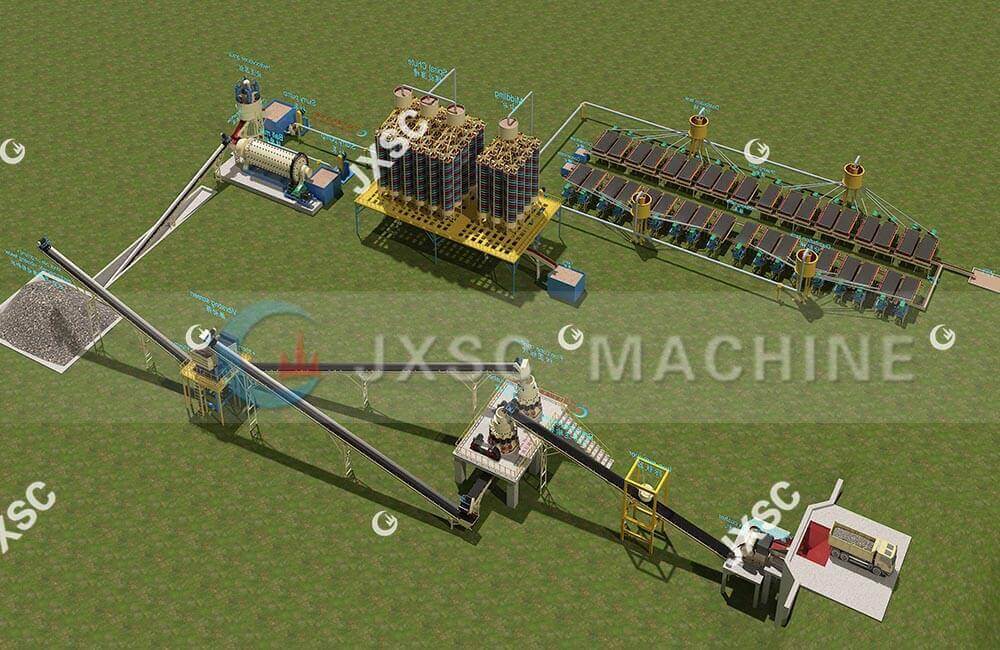
Manganese Ore Process flow
This setup is a 1500 tpd rock manganese ore process plant, it is configured by a feeding crushing system, grinding system, and 3-stage gravity separation system.
The crushing system is 150 tph capacity, 10 working hours per day. The grinding systems and gravity separation systems are about 62-63 tons per hour, 24 working hours per day. The max raw material size is 600mm and then grind till 0-1mm to release the manganese.
- Truck loads material to the hopper of the feeder. The feeder will feed the 0-600mm material to the jaw crusher evenly.
- The jaw crusher crushed the 0-600mm material to 0-180mm, then sent to the first compound cone crusher to fine crush by conveyor belt.
- The output of the first cone crusher will be sent to one vibrating screen with a 25mm mesh screen to separate.
- The 0-25mm will be sent to an underground silo. And the more than 25mm material will be sent back to another fine-crushing cone crusher. Both cone crusher’s output use the same conveyor belt.
- An Electromagnetic vibrating feeder under the underground silo will feed the 0-25mm material to the ball mill evenly.
- The ball mill will grind the 0-25mm material till around 1mm. Then use the slurry pump to send the material to the hydrocyclone to separate.
- The +1mm material will flow back to the ball mill again. And the 0-1 mm slurry will be sent to the first stage 30 pcs spiral chutes.
- The middle ore of the first 30 pcs spiral chute will be sent to the other 10 pcs spiral chutes to separate again.
- All the concentrate of two-stage spiral chutes will be sent to the distribution tank and then flow to 36 sets of shaking tables to further concentrate.
- The customer will get high-grade manganese concentrate from the shaking table. The Trommel screen is designed with mobile wheels, easy to move.
The capacity for this processing plant can be customized as per request such as 50 tph, 100 tph, 200 tph, 300 tph, etc.
Manganese oxide and manganese carbonate ores contain some refractory ores. Manganese coexists closely with iron, phosphorus or gangue, and the embedded particle size is extremely fine, making it difficult to separate. Usually, it is necessary to use crushing, grinding and classifying, washing, gravity, magnetic separation and other processes for processing. Before manganese beneficiation, it is necessary to first understand the properties and composition characteristics of the ore, and JXSC support customize the best manganese ore equipment for you to maximize the beneficiation indicators. Contact us to get more details!