Is your mineral processing efficiency limited by the wrong centrifugal concentrator? Centrifugal concentrators are the backbone of modern mineral separation, using centrifugal force to precisely separate precious metals (such as gold and platinum) from heavy minerals in ore pulp. This equipment is vital in mining operations, recovery systems and laboratory analysis, and even a 1% increase in recovery can translate into significant economic benefits. But the question is: does choosing a full automatic, semi-automatic or manual centrifugal concentrator really affect your bottom line? We’ll discuss the differences between these three generations of centrifugal concentrators in depth to help you make an informed choice.
Full automatic centrifugal concentrators can maximize pure gold recovery up to 95%, and are ideal for 24/7 operation, while manual units rely heavily on the operator’s skills. Semi-automatic models offer an intermediate solution, but may still require some supervision. Commonly used for gold beneficiation or tailings enrichment, the specific choice of these three centrifugal concentrators depends mainly on your budget size, processing volume and other specific needs.
What Are Centrifugal Concentrators?
Centrifugal concentrators are industrial equipment that use the principle of centrifugal force to separate mineral particles. They are mainly used to efficiently enrich precious metals (such as gold and platinum) or heavy minerals (such as tungsten and tin) from ore slurry. Its core function is to quickly separate the target minerals from waste rocks and light impurities through physical density differences, significantly improving resource recovery rates. This type of equipment is widely used in gold mining, tailings reprocessing, electronic scrap metal recovery, and laboratory mineral analysis. Compared with other gravity concentrators (such as shaking tables, chutes, and jig separators), centrifugal concentrators have the advantages of fast processing speed, small footprint, and adaptability to fine particles (up to 10 microns), and are particularly suitable for processing low-grade ores or raw materials with complex components.
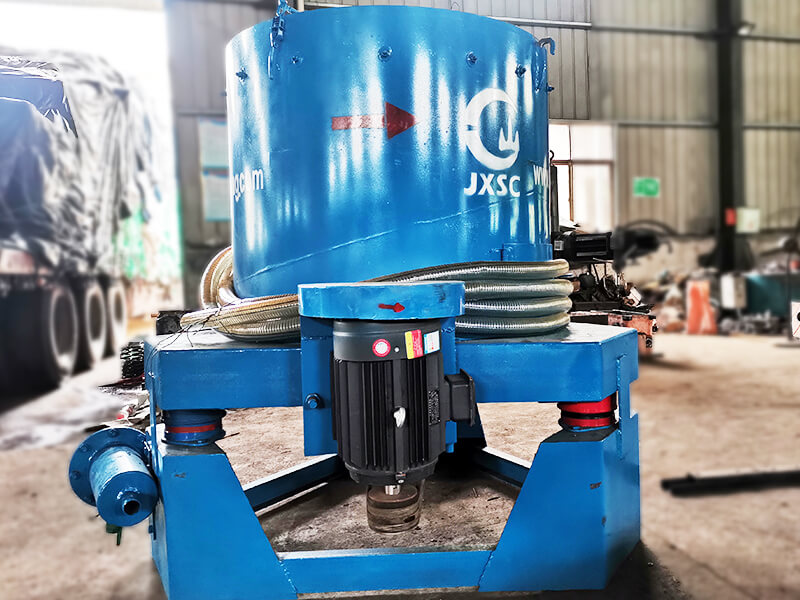
Working Principle
The operation of the centrifugal concentrator is based on the synergy of centrifugal acceleration and density difference. When the motor drives the drum to rotate at high speed, the ore slurry enters the enrichment tank on the inner wall of the drum through the central feed pipe. Under the action of centrifugal force, the mineral particles with higher density are thrown to the outer edge of the drum and deposited in the grooves in the tank, while the impurities with lower density are washed to the tailings outlet by the continuous water flow due to insufficient centrifugal force. After the sorting is completed, the equipment collects the enriched concentrate by stopping or automatically unloading the device.
Types Of Centrifugal Concentrators
Type | Control Level | Typical Use Cases | Throughput |
Fully automated with PLC/sensors | Large-scale mining, 24⁄7 operations | 10–100+ tons/hour | |
Semi-Auto (Auto) | Partial automation (e.g., auto rinse) | Medium-scale plants, intermittent processing | 2–20 tons/hour |
Operator-controlled (speed/feed) | Artisanal mining, labs, small-batch testing | 0.1–2 tons/hour |
Full Auto vs Auto vs Manual: Pros and Cons of Each Type
1. Fully Automatic Centrifugal Concentrators
The fully automatic centrifugal concentrator is made of polyurethane material as a whole, with removable internal and external vertebrae for easy maintenance and replacement. It has an optimized sorting tank structure with no dead corners and no shedding. Fully automatic PLC control system, tilted dynamic backwash flow type, maximum gravity speed change 120G. Moreover, the fully automatic equipment adopts a new filtration system and is easy to operate. Multiple detection points can automatically alarm when failure occurs. It is very effective for fine-grained gold ores or monomer (coarse) gold ores, and consumes less water resources. It is suitable for environmental protection projects such as large-scale gold mining and large-scale gold processing solutions of high-grade ores, saving labor costs in the long term.
Advantages of full auto Centrifugal Concentrators:
- It can operate continuously for 24 hours, with a processing capacity of 50-200 tons/hour, suitable for large-scale gold mines or tailings recovery projects, and the recovery rate is stable at 90%-98%.
- Integrated PLC control system and sensors, automatically adjust centrifugal force, feeding speed, flushing frequency, and reduce human errors.
Disadvantages: high equipment cost, high requirements for power facilities, regular replacement of wear-resistant parts, and complex maintenance.
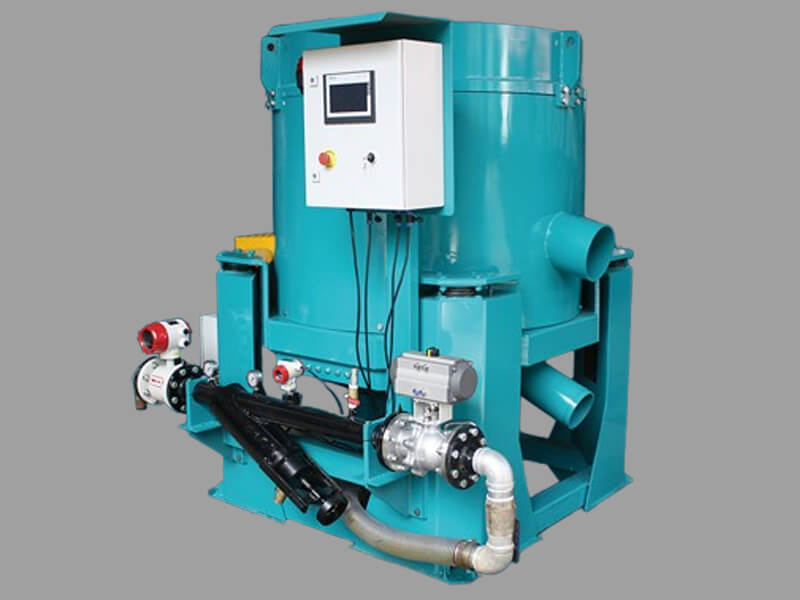
2. Semi-Automatic Centrifugal Concentrators
The whole is made of stainless steel welded stainless steel wear-resistant rings, and the inner and outer vertebrae are of one-piece design. It has a rectangular trough or similar trough tank. Usually, the rebound of the vertical wall of the vertebra is very difficult to repair, and the dead corner is easy to harden. This semi-automatic centrifugal concentrator adopts a simple PLC control system, with a maximum gravity speed change of 60-90G, and is mainly used to recover monomer coarse gold ore. If this centrifugal concentrator is used to select a small amount of money, there is no detection alarm prompt, and water consumption is high. It is suitable for gold beneficiation scenarios in medium-sized mining companies, with limited budgets but plans to gradually automate, and relatively stable ore composition.
Advantages of auto Centrifugal Concentrators:
- The price is moderate, and cost-effective, and the automation functions are concentrated in key links: automatic ore discharge, timed flushing, and reduced labor fatigue.
- Suitable for medium-sized concentrators or seasonal production, such as concentrated mining of placer gold mines in the rainy season.
Disadvantages: The operator needs to monitor the uniformity of the feed and manually adjust the parameters (such as centrifugation time), which may be caused by novices, and some manual operation is still required.
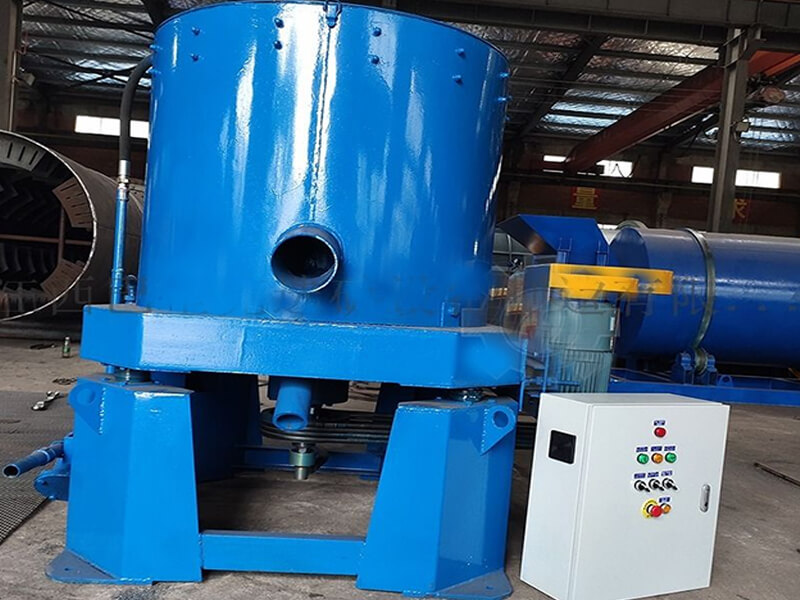
3. Manual Centrifugal Concentrators
The whole is made of stainless steel, and the inner and outer vertebrae are of one-piece design. It has a rectangular tank. Usually, the rebound of the vertical wall of the vertebra is very difficult to repair, and the dead corner is easy to harden. This manual centrifugal concentrator mainly adopts a manual discharge control system, a gravity speed change of 60G, a simple filtration system, and no detection alarm function. It is suitable for small-scale gold mining plant projects such as individual miners and laboratory sample purification.
Advantages of manual Centrifugal Concentrators:
- Simple structure (no electronic components), maintenance only requires regular cleaning and lubrication, and low cost.
- No special power requirements, light weight, can be used for field exploration or mobile use of small placer gold mines.
Disadvantages: It is heavily dependent on operator skills and manually adjusts the feeding speed. The processing capacity is only 0.1-2 tons/hour, which cannot meet the needs of continuous production.
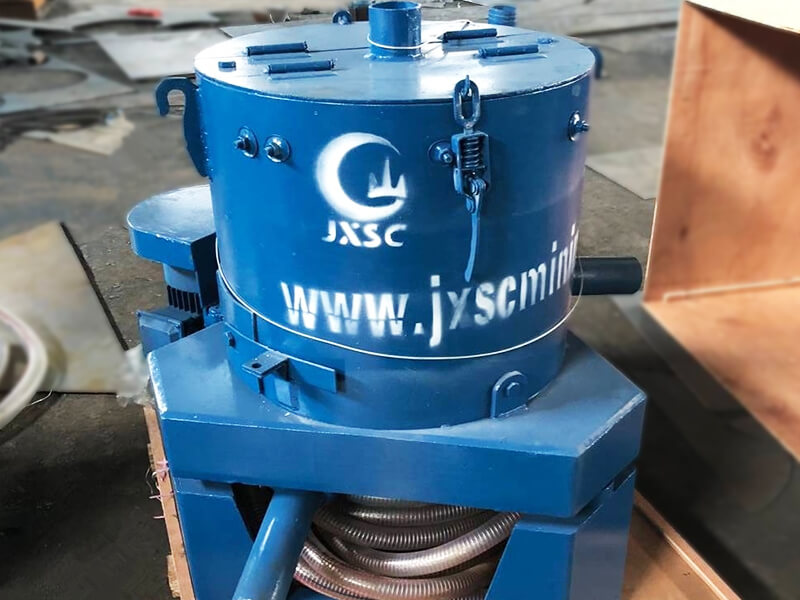
Fully automatic centrifugal concentrators are suitable for high efficiency, low manual intervention, and large-scale processing. Semi-automatic centrifuges can balance cost and automation. Manual centrifugal concentrators are low-cost and easy to use. If you need to further compare specific model parameters or obtain a quote for a centrifugal concentrator, you can provide your ore type (such as placer gold, rock gold), monthly processing volume, power conditions and other requirements, and JXSC will customize gold mineral processing recommendation solutions, contact us now!