With the development of industry and the progress of society, the application fields of graphite are constantly expanding, and the requirements for graphite in various industries are also getting higher and higher. However, the fixed carbon content of natural graphite ore is generally low, the fixed carbon content of flake graphite raw ore is 3-5%, and the higher one is only 20-25%. The ore fixed carbon content of cryptocrystalline graphite is generally 60-80%. Due to the low fixed carbon content of raw ores, beneficiation and purification are generally required to increase their fixed carbon content and meet industry application requirements. The beneficiation methods of graphite mainly include flotation, gravity separation, and electrical separation.
graphite ore
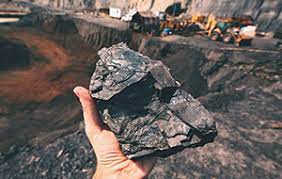
Graphite is one of the crystalline minerals of carbon element. It has excellent properties such as lubricity, chemical stability, high temperature resistance, electrical conductivity, special thermal conductivity, plasticity, and coatability. Its application fields are very wide.
According to the crystalline form of graphite, graphite ores are generally divided into two categories:
- Crystalline (or flake) graphite: flake and block (or dense crystalline) graphite with a crystal diameter greater than 1 micron. The ore grade is generally poor and can only be used after beneficiation in industry. But it is of good quality and versatile.
- Cryptocrystalline (or amorphous, earthy) graphite: The crystal diameter is less than 1 micron, and it is difficult to see the dense graphite aggregate in its crystal form under the microscope. Due to the poor selectivity of ore, the industry has higher requirements on the grade of raw ore so that it can be directly ground into powder for use. Its industrial performance is worse than that of crystalline graphite.
graphite ore Flotation method
Graphite has good natural floatability and hydrophobicity, so most concentrators use the flotation method to purify graphite ore, that is, adding a series of flotation reagents to enrich the selected graphite ore in the gas-liquid interface, and realize the separation of impurities and impurities separation of minerals.
Crystalline graphite flotation:
Flake graphite has good natural floatability and low density, so coarse-grained flake graphite is easier to float. Kerosene and diesel oil can be used as flotation collectors, and pine alcohol oil is commonly used as a foaming agent. Most of the flake graphite ores contain gangue minerals such as calcite and pyrite, and inhibitors such as lime and water glass need to be added; for carbonaceous shale, starch, lignosulfonic acid, etc. can be added as inhibitors. Rare metals such as vanadium contained in graphite ore should be recovered to improve economic benefits.
- Staged flotation: In order to protect the scales from damage, a staged grinding and flotation process is used in flotation; roughing is carried out after rough grinding to obtain rough concentrate and waste tailings, and then the rough concentrate is re-ground and re-grinded for many times.
Multiple selections: The rough concentrate obtained by roughing has a low grade, while graphite products generally require a fixed carbon content of more than 85%, which requires multiple selections.
Cryptocrystalline graphite flotation:
Cryptocrystalline graphite has poor natural floatability and high raw ore grade, which can reach more than 70%-80%. However, the graphite particles are closely embedded with clay, and it is difficult to separate. It is a difficult ore to select. In industrial production, the grade of cryptocrystalline graphite concentrate can be increased to more than 80% by grinding and flotation, but it is difficult to reach 90%, even if the number of regrinding is increased, the concentrate grade will not be improved. Cryptocrystalline graphite flotation can only be used for approximate enrichment, so concentrates and tailings can be sold separately as different grades of products. Cryptocrystalline graphite flotation features: large amount of flotation collector, slow flotation speed, low concentrate recovery rate, and high tailings grade.
Some mineral processing researchers have compared and found that using flotation column as the flotation equipment of cryptocrystalline graphite can obtain better flotation effect.
Precautions for using graphite flotation machine
Graphite beneficiation generally adopts the method of flotation machine flotation, which can be collected with neutral oil. The following points should be noted during the flotation process:
(1) First find out the type of graphite ore. Graphite ore is divided into flake graphite ore and earthy graphite ore. The scaly graphite ore is characterized in that the graphite is scaly or leaf-shaped, and the raw ore grade is not high, generally 3% to 5%, and the highest does not exceed 20% to 25%. This type of graphite has good flotation, and after flotation, the grade can reach more than 90%, so the raw ore grade of 2% to 3% can be mined. Flake graphite has excellent properties and can generally be used to manufacture high-grade carbon products.
Earthy graphite is also known as cryptocrystalline graphite ore. The graphite crystal of this ore is small, generally less than 1um, the surface is earthy, lacking luster, and its industrial performance is not comparable to flake graphite. The raw ore grade of this graphite ore is relatively high, generally 60%~80%, but the floatability is very poor. After flotation, the grade will not be significantly improved. Therefore, the raw ore with a grade less than 65% is generally not mined. , the grade is between 65% and 80%, which can be used after selection. Therefore, for graphite ore, we should not only look at the grade of its raw ore, but should first find out its type, and then decide whether to adopt a flotation scheme.
(2) High requirements for product quality. Graphite products have higher grade requirements. For example, ordinary flake graphite requires a grade of over 89%, and pencil graphite requires a grade of 89% to 98%. Some electric carbon graphite requires a grade of 99%. In order to obtain high-grade graphite concentrate, in graphite flotation, the selection times are generally more.
(3) Pay attention to protecting the large scales during the selection process. Large flake graphite has a wide range of uses, few resources and high value, so care must be taken to protect the large flakes from being broken during production. Usually large flakes refer to +50 mesh, +80 mesh, +100 mesh flake graphite. The measure to protect the large phosphorus flakes is to use multiple grinding and multiple sorting processes in the sorting process. The monomer dissociated graphite obtained by each grinding is selected in time. If the ore is ground to a very fine particle size at one time, the large scales will be destroyed.
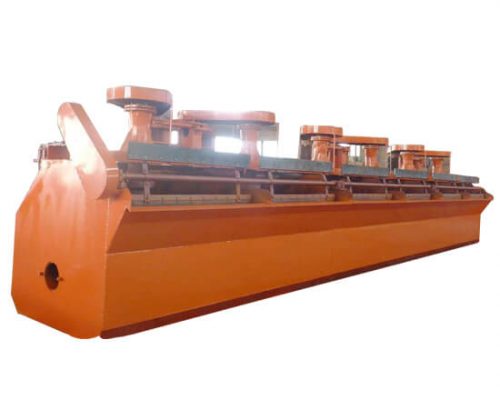
Gravity beneficiation method
Gravity separation is mainly used to pretreat graphite ore, select heavy minerals in it, throw tails in advance, and initially enrich graphite, and then use flotation to further increase the fixed carbon content of graphite. When the ore contains more pyrite, limonite, garnet, rutile, tremolite, diopside and other minerals with relatively large proportions, it can be pretreated by gravity separation to achieve preliminary enrichment. Graphite rough concentrate is obtained. The coarse concentrate is further enriched by flotation. Therefore, gravity separation is only used for pretreatment of graphite ore. In actual production, it is mostly used in conjunction with flotation, and it is rarely used at present.
Electric separation method
Electro-separation is a physical beneficiation method that utilizes different electrical properties of various minerals and materials for separation. For graphite ore beneficiation, graphite ore has good electrical conductivity, while gangue minerals (such as feldspar, quartz, pyrite, etc.) have poor electrical conductivity. Other minerals are separated.
Because graphite has good electrical conductivity, and minerals coexisting with graphite, such as quartz, feldspar, mica and other minerals, have poor electrical conductivity, and the electrical conductivity between graphite and gangue minerals is quite different. Therefore, electrical separation can be used to separate graphite and gangue, but electrical separation is less used due to its small processing capacity and low efficiency.
At present, many graphite mines in the industry use the flotation method for stage grinding and stage separation to recover crystalline graphite, and obtain ideal technical indicators and considerable economic benefits. Graphite flotation provides a reliable technical basis for mine construction, and advantageously promotes the development and utilization of graphite industry and the development of deep processing.