Cassiterite (tin ore) is a mineral composed of tin oxide (SnO2) and is the primary ore of tin. In modern industry, cassiterite is often an indispensable and important raw material, such as electronic components for electronic product manufacturing, catalysts in chemical production, aerospace, machinery manufacturing, and other fields. However, cassiterite mined in nature is often low-grade and mixed with many gangue minerals. Suppose you want to obtain high-purity tin products that meet the high standards of various industries. In that case, you need to separate and enrich cassiterite from complex ores, remove impurities, and improve purity through mineral processing. Therefore, the cassiterite beneficiation process and the equipment used are particularly critical. Cassiterite beneficiation process may vary depending on the characteristics of the ore but mainly involve pre-separation (crushing, grinding, washing), gravity separation, flotation, magnetic separation, dehydration and drying (optional), and other processes to separate tin minerals from gangue minerals.
What is cassiterite and its characteristics
Cassiterite has a fairly high density of 6.7-7.1. Most cassiterite is formed in granite, rhyolite, and pegmatite veins. It is also found in alluvial placers, where water carries minerals to new areas (common in stream tin mines). Its crystals are often bipyramidal, bipyramidal columnar, and aggregates are granular or massive.
Cassiterite Beneficiation Characteristics
The main use of cassiterite is to extract tin metal. Tin is a widely used metal with excellent properties, including corrosion resistance, low toxicity, and low melting point. Gravity separation can sort coarse-grained cassiterite (generally larger than 2mm). Fine-grained cassiterite (usually less than 0.074mm) is more suitable for flotation, which is separated by adding suitable flotation reagents. Cassiterite often coexists with minerals such as sulfide minerals such as pyrite, galena, sphalerite, and gangue minerals such as quartz and feldspar.
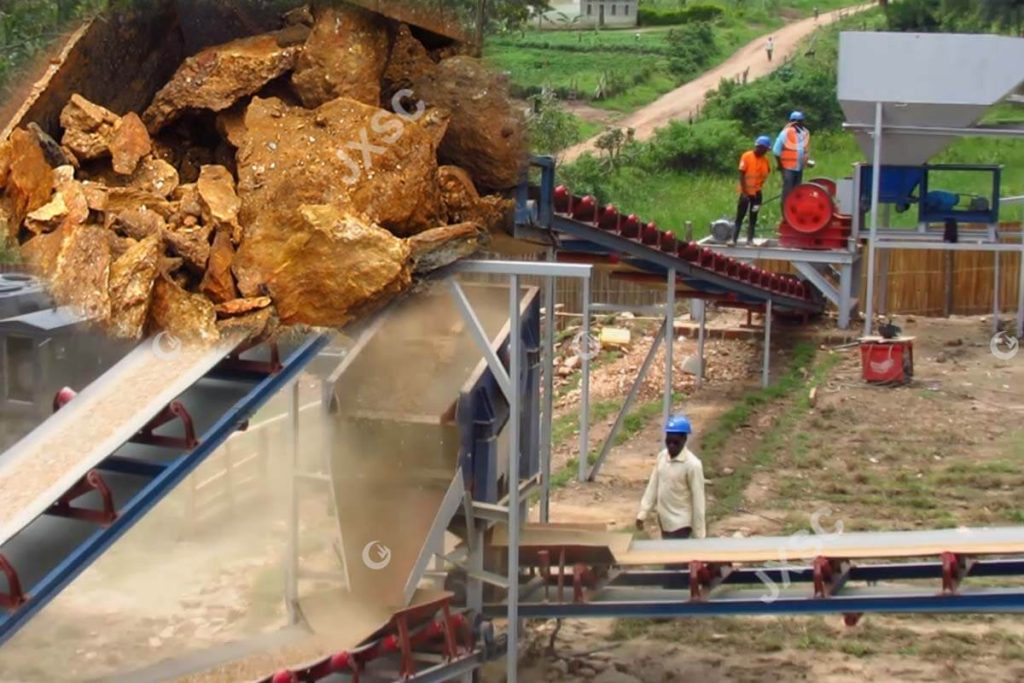
Cassiterite beneficiation process and equipment
Cassiterite has a higher density than paragenetic minerals, and gravity separation is the most common and main cassiterite beneficiation method. As the particle size of cassiterite in the selected ore continues to become finer, flotation process and selective flocculation process have emerged. The specific process selection is mainly determined by the composition and characteristics of the material, production requirements, etc., and a combined process is often used to achieve the best beneficiation effect.
1. Pre-separation
(1) Crushing and grinding: The mined tin ore is usually of large particle size. First, it is crushed by a crusher for coarse, medium and fine crushing, and its particle size is gradually reduced to a suitable particle size. The crushed material is then ground to control the appropriate grinding fineness so that the cassiterite and gangue minerals are fully dissociated for subsequent sorting.
Common crushing equipment: jaw crusher, cone crusher, hammer crusher
(2) Washing: Due to its high hardness, high specific gravity and strong resistance to chemical weathering, it is often enriched into sand ore, called sand tin. Most of the cassiterite is mined from sand ore. It is usually necessary to use ore washing equipment to clean and remove impurities from the material.
Common washing equipment: trommel scrubber, drum screen
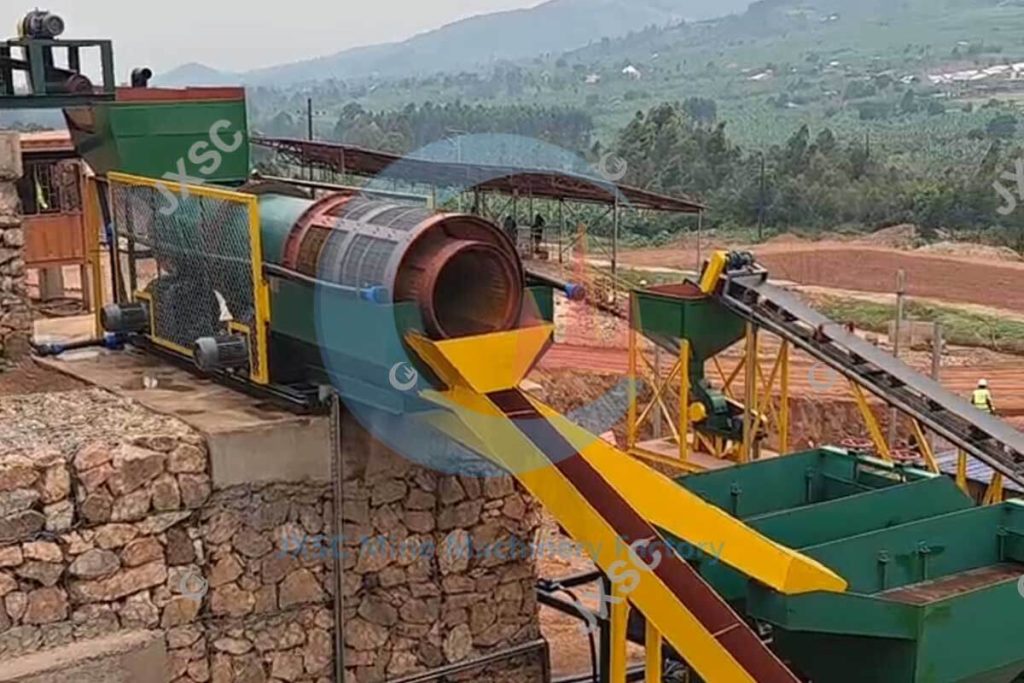
2. Gravity separation
Use the difference in density between cassiterite and gangue minerals for separation. Cassiterite has a relatively high density, generally 6.8 – 7.1g/cm³, while gangue minerals have a relatively low density. In a gravity field or centrifugal field, minerals of different densities settle at different rates, thus achieving separation.
Common gravity concentration equipment: shaking table, spiral chute, jig separator
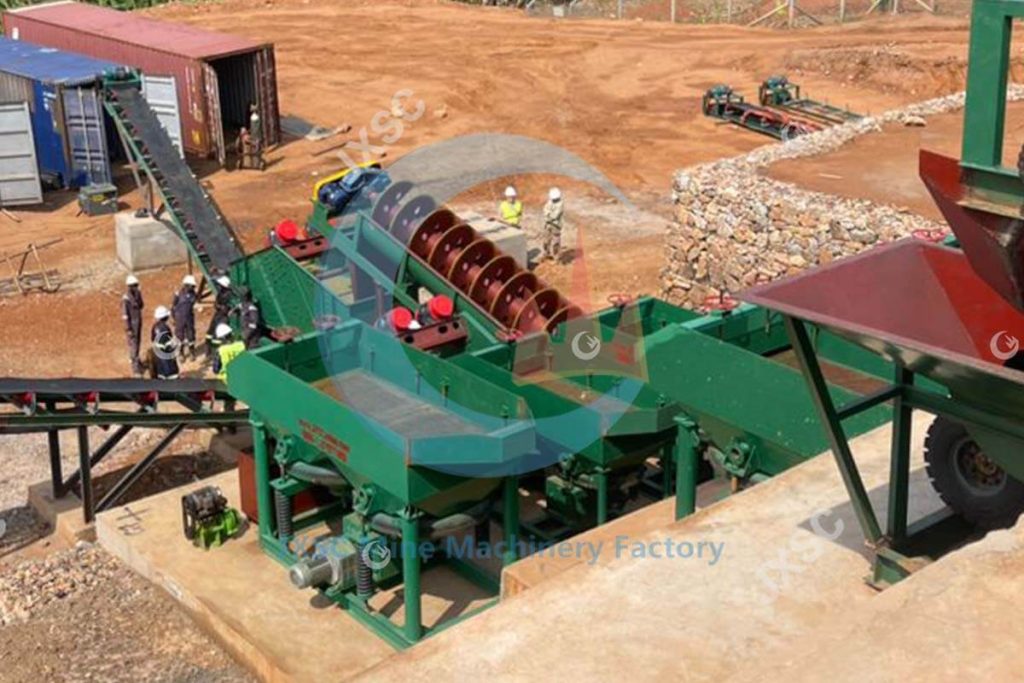
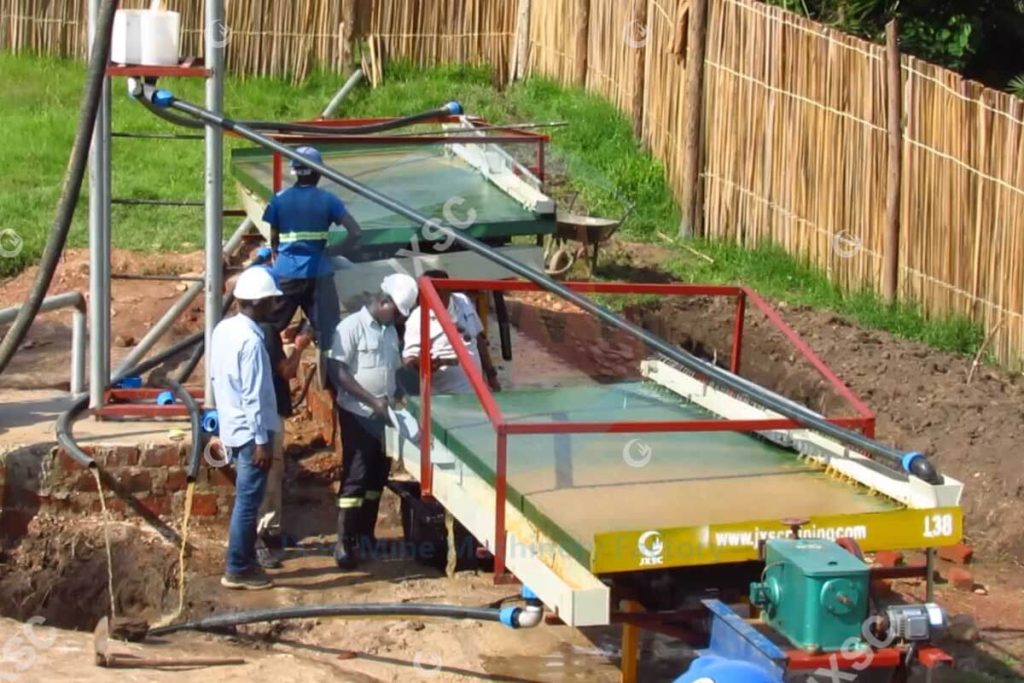
3. Flotation Process
Based on the difference in the physical and chemical properties of cassiterite and gangue minerals, by adding flotation agents, the surface of cassiterite is made hydrophobic and attached to bubbles, thereby separating it from gangue minerals. Cassiterite flotation is used to separate cassiterite of various particle sizes, especially for fine and micro-fine cassiterite.
Common flotation process equipment: flotation machine, stirring tank
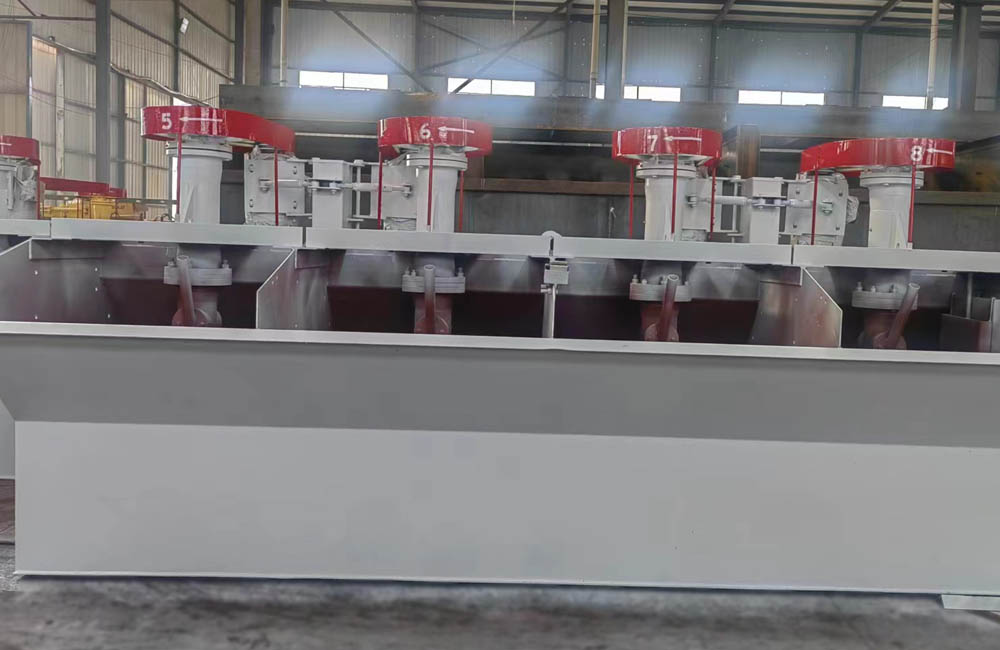
4. Magnetic separation
If the cassiterite ore contains magnetic minerals, and the magnetic difference between cassiterite and magnetic minerals is large, magnetic separation can be used for separation. Under the action of the magnetic field, the magnetic minerals are adsorbed on the magnetic separation equipment, while cassiterite, as a non-magnetic mineral, flows out with the slurry, thereby achieving separation. Magnetic separation is usually used as an auxiliary process. For example, when cassiterite ore is accompanied by magnetic minerals such as magnetite, magnetic separation can remove magnetic impurities before gravity separation or flotation to avoid their interference with subsequent selection operations and improve the efficiency of cassiterite beneficiation.
Common magnetic separation equipment: wet drum magnetic separator, three-disc dry magnetic separator
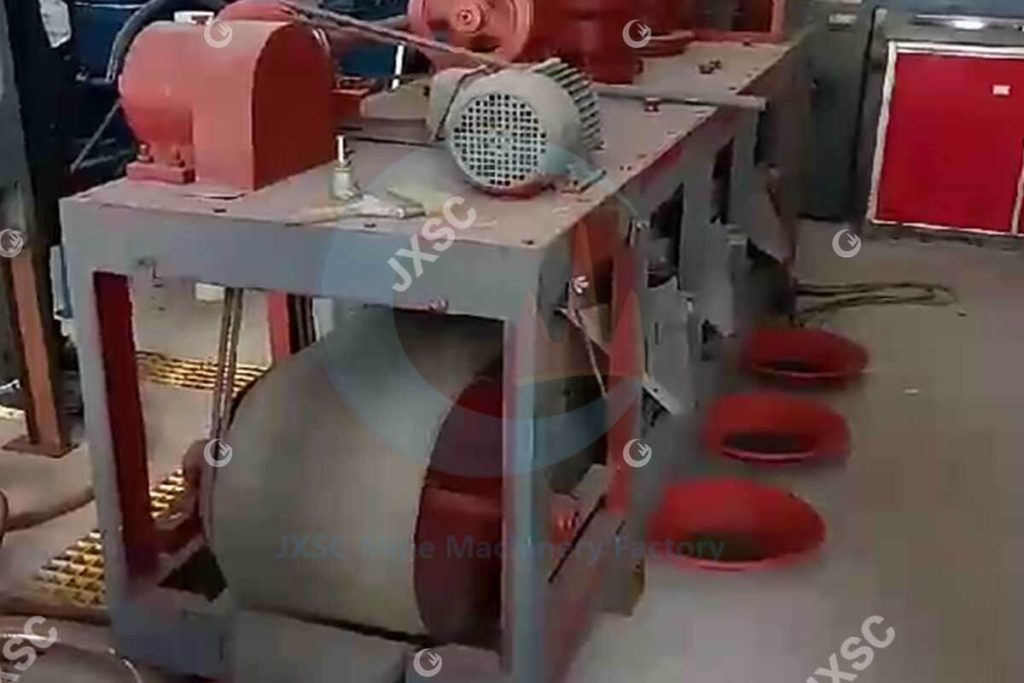
5. Dehydration and drying
The cassiterite concentrate after sorting contains more water and needs to be dehydrated. Then use filtering equipment to further dehydrate and obtain a filter cake with a lower water content. The dehydrated filter cake still contains a certain amount of water. It is dried by drying to make the cassiterite concentrate meet the water content standard required by the product, which is convenient for storage and transportation.
Common dewatering & drying equipment: thickener, filter press, rotary dryer
Cassiterite beneficiation plant
This plant is for rock and alluvial cassiterite ore mixed processing plant. It’s configured with a vibration feeder, trommel scrubber, jig separator, spiral dewatering machine, jaw crusher, fine jaw crusher, vibration screen, ball mill, shaking table, 3 discs dry magnetic separator and belt conveyor, etc.
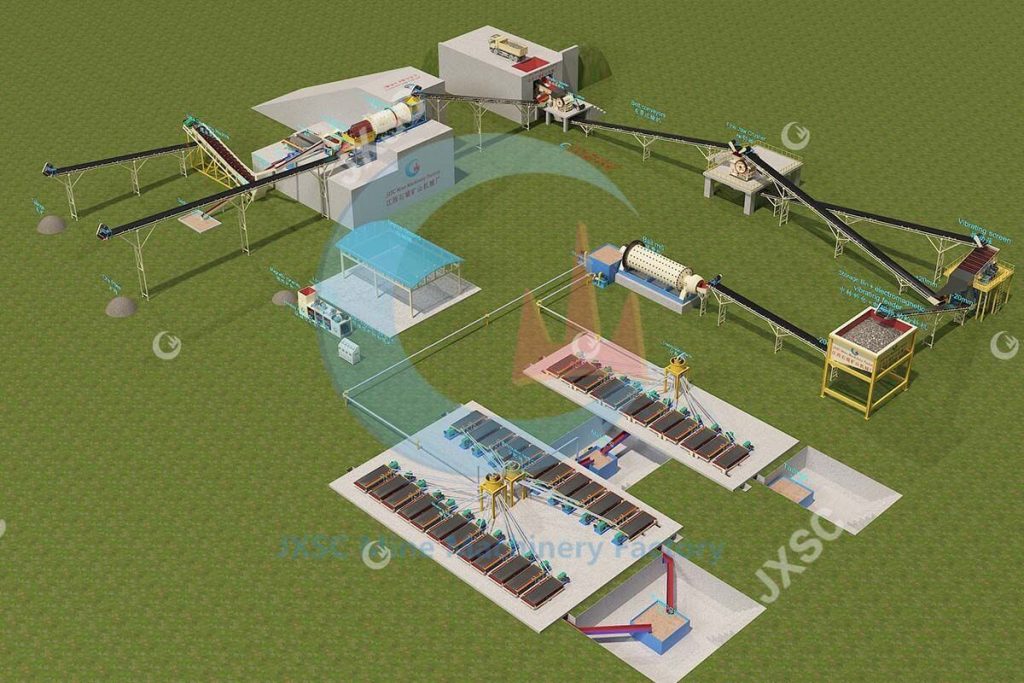
(1). Alluvial cassiterite processing part:
- The raw ore will be fed into the raw ore hopper above the vibration feeder by excavator or wheel loader etc. The vibration feeder designed with grizzly bar, bar gap 50mm.
- Less than 50mm goes to the trommel scrubber for washing away the sticky clay.The trommel scrubber design with 2 layers screens, 2mm and 8mm.
- After washing with a trommel scrubber,+8mm materials will go to one jig separator to separate and get the concentrate. The overflow concentrate will go to a concentrate pool. The 0-2mm materials will go to another jig separator for concentrate separating.The concentrate will be underflow and will go to shaking tables to separate again to reach higher grade.
- The tailings from jig separators and shaking tables will go to a spiral dewatering machine to remove most of the water, then sent away by belt conveyor, so that you can handle the tailings easier.
(2). Rock cassiterite processing Part:
- The larger than 50mm materials go to the jaw crusher for primary crushing. Output from jaw crusher go to fine jaw crusher for secondary cruhsing.Output from fine jaw crusher go to vibration screen.
- The screen has 2 layers, 18mm and 30mm. The larger than 18mm will be sent back to the fine jaw crusher to crush again. The less than 18mm materials will be sent to the transfer bin before the ball mill.
- Under the transfer bin, there is one electromagnetic vibration feeder for feeding the less than 18mm materials into the ball mill more evenly and smoothly.
- After grinding by ball mill, the grinded slurry will be pumped into first stage shaking tables by slurry pump. The middlings from the first stage shaking table will go to second stage shaking tables for second separation and getting more concentrated minerals.
- The concentrates from the shaking tables and jig separators need to be dried in the sun or other ways which can dry, then you can feed the dry concentrates to three pcs disc dry magnetic separator for final refining and get high purity tin concentrates.
Cassiterite beneficiation mainly includes pre-separation (crushing, grinding, washing), gravity separation, flotation, magnetic separation and other processes and equipment. In actual production, it is necessary to flexibly adjust or combine multiple processes and equipment according to the characteristics of the ore to achieve the best beneficiation effect. Only high-purity tin products obtained through fine beneficiation can meet the increasingly stringent quality requirements of various industrial fields. JXSC will customize mineral beneficiation solutions and equipment according to mineral characteristics and specific production requirements. Contact us for more details!