Limonite is a common iron ore that is often associated with other minerals. To extract valuable metals from limonite, various separation methods are used. Gravity separation, magnetic separation and flotation are the most widely used limonite beneficiation methods. Each technique has unique advantages and limitations, so it is critical to understand their differences and choose the most suitable method to maximize the recovery of valuable iron from limonite ore.
About Limonite Mineral
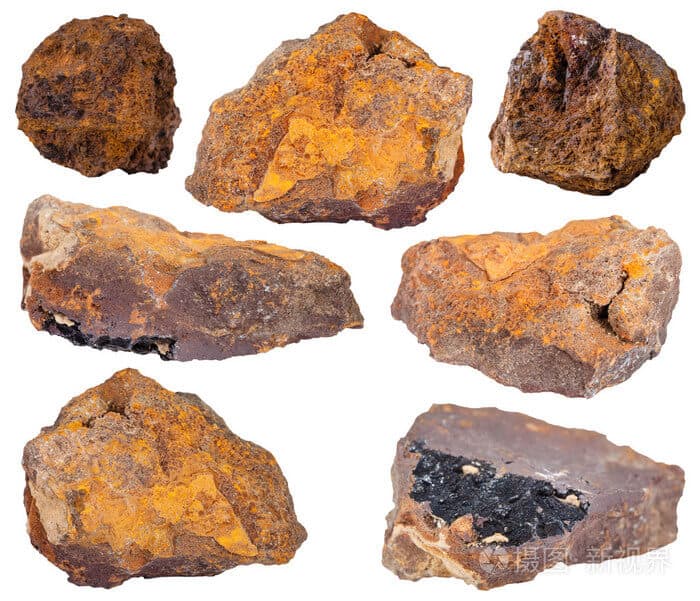
Limonite, also known as bog iron ore, usually contains high iron oxides, and its main component is hematite (Fe2O3). They consist mainly of hydrated iron oxides with varying impurities, such as clay, silica and manganese. Limonite’s special ability to form pseudocubic crystal shapes makes it unique, giving it an aesthetic appeal unlike any other mineral. It has magnetic properties and high water retention capacity. A key characteristic of the limonite mineral is its low iron content compared to other iron ores such as hematite and magnetite, so beneficiation is a complex process.
Limonite Gravity Separation
The gravity separation process is based on the density difference between different minerals, relying on water and gravity to separate them according to weight. The method utilizes the differences in physical and chemical properties of limonite and gangue minerals to achieve separation. Using the gravity separation does not require chemicals or complex equipment, making it cost-effective and environmentally friendly.
A key advantage of the limonite gravity separation process is its versatility. It can be used to separate mineral particles of various sizes and densities. Additionally, the process has proven to be highly efficient at removing impurities from limonite ore, thereby increasing its purity and quality for further processing.
Another notable feature of the limonite gravity separation process is its simplicity. It can be easily adapted to different conditions and scales of operations, suitable for both small miners and large mining companies. Additionally, the process does not produce harmful by-products or waste materials that could harm the environment.
The limonite gravity separation process offers many benefits to the mineral processing industry. Its efficiency, simplicity, versatility, cost-effectiveness and environmental friendliness make it an excellent choice for separating limonite from gangue minerals.
Limonite Magnetic Separation
Magnetic separation utilizes the magnetism of certain minerals in limonite. Using magnets or magnetic fields technology separates the iron-rich particles from the other components of the ore. Magnetic separation is very effective in removing impurities that may affect downstream processes.
- Efficient separation of magnetic minerals: The main minerals in limonite are hematite and magnetite, of which magnetite is magnetic. The magnetic separation process can efficiently separate magnetite from non-magnetic ores and impurities, because magnetite will be attracted and concentrated on magnetic drums or plates under the action of an external magnetic field, thereby achieving separation.
- No chemicals: The magnetic separation process does not require using chemicals or suspending agents, reducing environmental pollution, treatment costs, and the demand for water resources.
- Wide scope of application: The limonite magnetic separation process is suitable for ores of different particle sizes and can be separated from coarse-grained to fine-grained ores. This makes it highly adaptable.
- Improving the grade of the ore: Extracting magnetic minerals from the original ore through magnetic separation can significantly improve the grade of the concentrate; thus improving the efficiency and output of the subsequent smelting process.
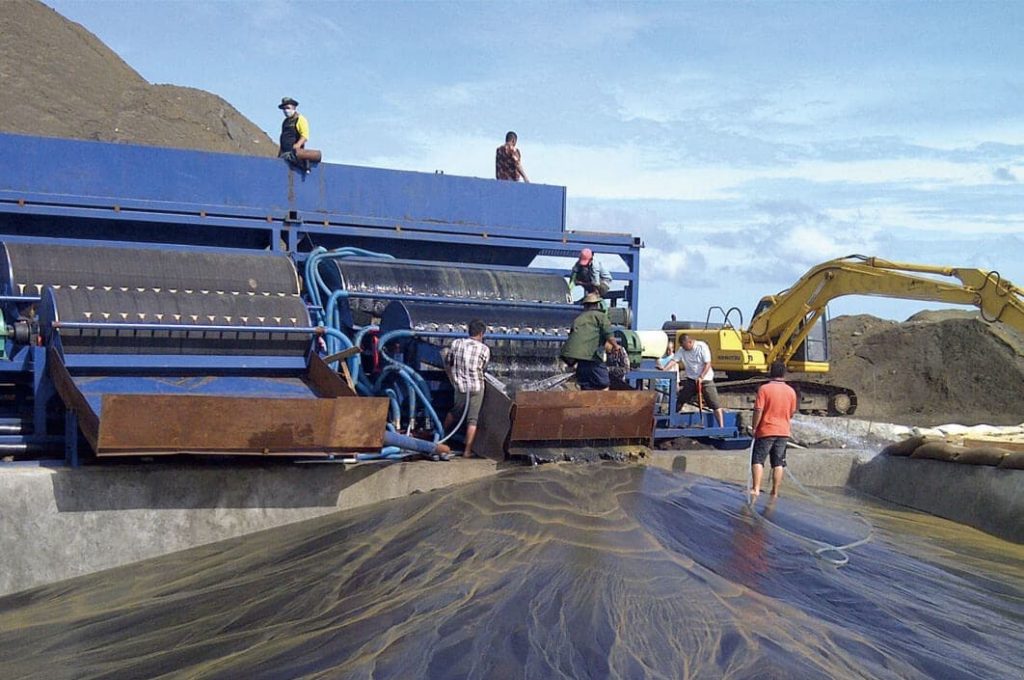
Limonite Flotation Process
Flotation involves adding reagents to make certain minerals hydrophobic while making other minerals hydrophilic. The foam brings hydrophobic minerals to the surface while leaving hydrophilic materials in the pulp phase. Flotation selectively concentrates valuable components such as iron oxide while minimizing impurities.
The separation of limonite minerals from other impurities through a flotation process. The success of this process depends on several factors, including pH control, reagent selection, and particle size distribution.
An emerging trend in limonite flotation is the use of novel collectors. Traditionally, xanthate has been widely used as a collector due to its high selectivity for limonite minerals. However, recent studies have shown that certain organic acids can outperform xanthate in selectivity and recovery. This discovery opens up new possibilities for improving the efficiency of the limonite flotation process.
In addition, advances in foam washing technology can also help improve the overall performance of the limonite flotation process. An innovative foam washing system can selectively remove unwanted gangue minerals from the foam concentrate before further processing. This improves product grade and reduces energy consumption by minimizing downstream processes.
Each process has its advantages and disadvantages when separating limonite ore. Gravity separation offers a low-cost method but may need help recovering fine particles or efficiently removing impurities. Magnetic separation is highly selective but requires large equipment and may produce tailings with lower iron grades. Flotation has many uses, but often results in excessive consumption of reagents and energy. Specific limonite beneficiation methods and combined processes may vary depending on the properties of different ores, production requirements and technological development. In actual operations, JXSC will select appropriate processes and equipment based on specific circumstances or your needs.