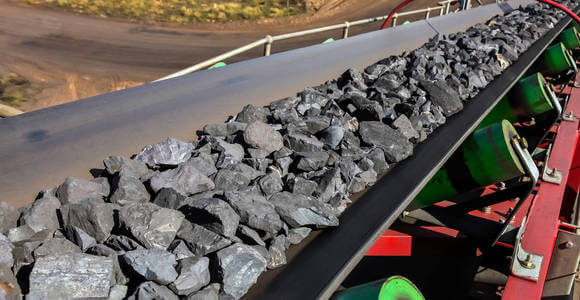
Manganese ore is a key element in steel and battery production and has received widespread attention in recent years due to growing demand. Choosing appropriate beneficiation technology is crucial to improving manganese ore’s grade and recovery rate.
Manganese ore beneficiation technology is used to extract manganese from manganese-containing ores. It mainly includes crushing and grinding, gravity separation, magnetic separation, flotation or combined technologies for beneficiation. These methods have been proven to optimize ore quality and improve extraction efficiency.
1. Manganese ore crushing and grinding Technology
After primary crushing, manganese ore goes through another stage called secondary crushing. It involves using a finer crusher or grinder to crush the particles into smaller sizes. The grinding and classification method separates manganese ore into particles of different sizes through grinding and classification for further processing. The process involves crushing manganese ore into smaller particles, sorted according to their size. Commonly used equipment includes ball mills, jaw crushers and vibrating screens. Grinding reduces the size of the ore and exposes more surface area, making it easier for chemical reactions to occur during subsequent processing. Classification using equipment such as screening machines, spiral classifiers or hydrocyclones ensures that only high-quality manganese ore with optimal particle size is further processed, increasing efficiency and product quality.
2. Manganese ore gravity separation Technology
Gravity separation is the most common beneficiation method for low-grade manganese ore. Density differences between ore and gangue minerals are used to separate them. This technology is effective for coarse particles but less efficient for fine particles. Generally, it is only suitable for sorting manganese ores with simple structures and coarser particle sizes, especially manganese oxide ores with higher density. Gravity separation methods include heavy media, jig, and shaking table beneficiation. Before gravity separation, the manganese ore is first crushed (6-0mm or 10-0mm) and then classified. The coarse-grained manganese ore particles enter the jig for sorting; the fine-grained ore particles are sent to the shaker for sorting. Commonly used equipment includes gravity separators, spiral separators, etc. This technology offers several advantages over other beneficiation processes, including low capital and operating costs, simplicity of operation, and high efficiency.
3. Manganese ore magnetic separation Technology
Manganese ore magnetic separation is widely used to separate valuable from gangue minerals. It uses the magnetic differences between various minerals to separate them. Applying a magnetic field to a mixture of ore and gangue minerals attracts magnetic particles to the area, while non-magnetic particles are repelled or pass through unaffected. Magnetic separation is particularly effective in separating high-strength and low-strength magnetic minerals. This technology has huge potential to improve resource recovery while minimizing the environmental impact of mining operations worldwide.
4. Manganese ore flotation separation Technology
Manganese flotation is a method of separating manganese minerals from other minerals by air bubbles. This method is usually used for fine-grained ores. During this process, a blowing agent is added to create air bubbles, which selectively attach to specific mineral surfaces according to their hydrophobicity or hydrophilicity. Usually, beneficial chemicals like sodium oleate, resorcinol, and oleic acid are added to enhance the interaction with collector molecules, ensuring better flotation. Since this method can effectively improve the quality of manganese concentrate, it has been widely used in many industries such as mining and metallurgy.
5. Magnetic-gravity, magnetic-flotation method
Gravity separation can be integrated into a multi-stage process with other technologies, such as magnetic separation or flotation to improve the concentrate’s grade and quality. This combined approach maximizes overall efficiency and reduces environmental impact by minimizing tailings generation.
By efficiently breaking down large chunks of ore through grinding and then separating them based on size through grading technology, manufacturers can produce high-quality products that meet stringent requirements. Typically, gravity separation, flotation, magnetic separation or combined processes can effectively separate mineral particles from gangue material, thereby maximizing mineral recovery. The selection of appropriate manganese ore beneficiation technology depends on factors such as the characteristics of the original ore, the desired product grade and recovery rate, and the scale of production. JXSC supports customized mineral processing plants, equipment, and process design to achieve the best beneficiation results.