More than 20 types of tungsten ore have been found in nature, among which scheelite and wolframite are of higher mining value and are also the main sources of tungsten ore resources. Tungsten is a rare metal widely distributed and exists in almost all kinds of rocks. However, wolframite and scheelite are mostly ores with complex components and fine-grained distribution of useful minerals, so it isn’t easy to separate them. In addition, it is associated with other metals, making it even more difficult to develop and utilize. The correct tungsten beneficiation process is critical to achieving optimal yield and purity levels. Discover the wolframite and scheelite beneficiation process that suits your needs and maximizes mineral recovery.
Wolframite and Scheelite Ore Features
Wolframite has greisen type, quartz vein type, porphyry type and other mineralization types. The main components are Wolfite (FeWO4) and Wolframite (MnWO4).
(1) Shape: There are two kinds of monoclinic crystal systems and orthorhombic columnar crystal systems. The crystal form is plate or column, and the aggregates are mostly plate.
(2) Color: It becomes darker with the increase of iron content, generally maroon to black. It has metallic or semi-metallic luster, the streaks are lighter in color, wolframite is yellowish-brown-yellow, and wolframite is dark brown-black.
(3) Application: Mainly used for smelting tungsten and making tungstate.
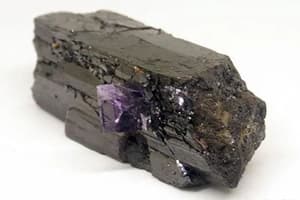
Scheelite is a transparent to translucent mineral in granular or massive shape. The main component is calcium tungstate (CaWO4). Usually produced in contact metasomatism skarn, high-temperature hydrothermal veins and greisen.
(1) Shape: The crystals are tetragonal bipyramids close to octahedrons, and the aggregates are mostly irregular granular and less densely massive.
(2) Color: generally gray, light yellow, light purple or light brown.
It has glass luster or diamond luster, and the streaks are yellow-green.
(3) Application: It is mainly used to produce Ferro tungsten and can also be used to make permanent magnets.
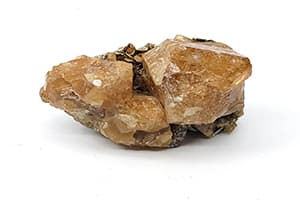
Wolframite Ore Beneficiation Process
Wolframite is unevenly distributed in the quartz gangue, and the large-grained crystals in the quartz vein can reach more than 100mm. Wolframite is in the shape of thick plates or fine veins, and the veins are narrow and uneven in thickness. According to the easily identifiable characteristics of wolframite surrounding rocks and gangues and the differences in surface physical properties.
The main sorting process of wolframite beneficiation is gravity separation. The technological process includes four parts: pre-selection, grading and re-selection, selection and comprehensive recovery, and fine mud treatment. Among them, early harvesting by jig separator and tail loss by shaking table are the core of gravity separation. The symbiotic ore of tungsten also uses the process of strong magnetic separation and flotation. Large and medium-sized tungsten concentrators have a comprehensive recovery process for selected and associated metals. The rough concentrate of the small-scale tungsten concentrator is sent to a special concentrator for beneficiation and comprehensive recovery.
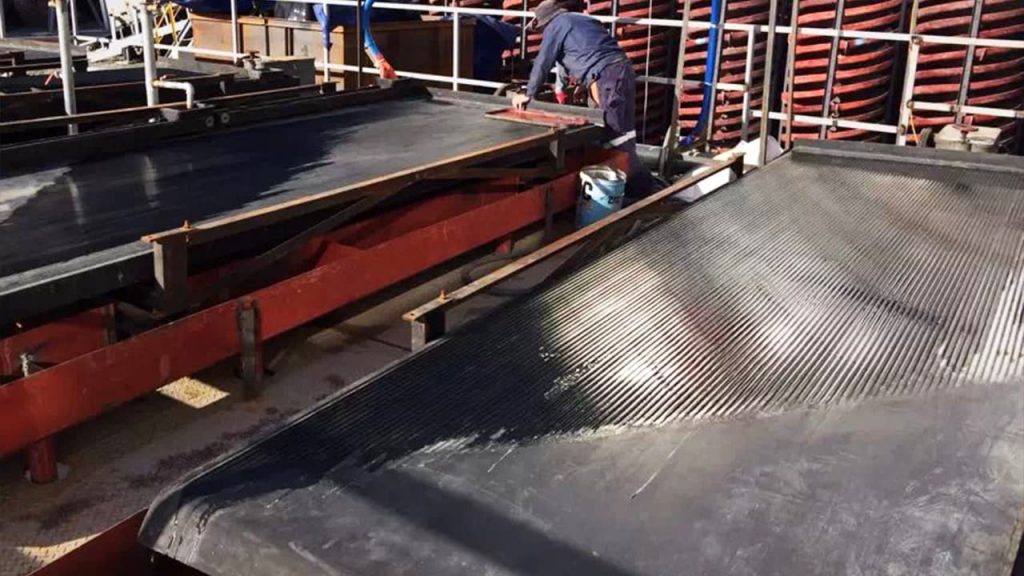
The first-stage grinding adopts rod mill, and the second-stage grinding adopts ball mill or rod mill. The shaking table is used for beneficiation to further improve the grade of tungsten concentrate, and magnetic separation and electric separation are used for the separation of wolframite, cassiterite and niobium-tantalum ore. Comprehensive recycling can obtain more than 20 kinds of products such as tin, molybdenum, copper, lead, zinc, bismuth, sulfur, gold, silver, antimony, beryllium, lithium, potassium, arsenic, rare metals, rare elements, crystals, etc. from tungsten ore.
Scheelite Ore Beneficiation Process
Coarse-grained scheelite is still recovered by gravity separation, and fine-grained scheelite is generally recovered by flotation separation. Scheelite has good floatability and is commonly used in flotation process. At present, the flotation process of scheelite mainly includes normal temperature method and heating method. The normal temperature method is more commonly used in quartz vein mines and mines with low calcium mineral content. Heating flotation has strong adaptability to ore and stable selection index, and is widely used in scheelite-calcite-fluorite mines.
It is generally divided into a roughing section and a concentrating section. The purpose of the roughing section is to maximize the grade of the rough concentrate, and the purpose of the concentrating section is to meet the market demand for tungsten concentrate. Therefore, to obtain qualified tungsten concentrates, it is often necessary to adopt more complex processes and multiple separation to achieve the goal.
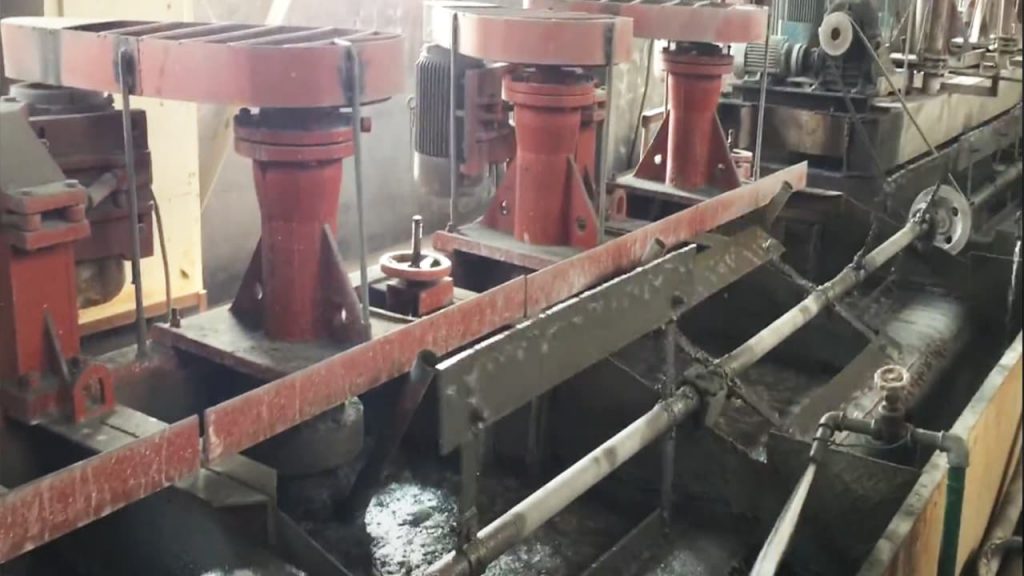
In conclusion, the correct wolframite and scheelite beneficiation process is the key to releasing these minerals, ensuring the extraction of these valuable minerals with minimal loss. Wolframite and scheelite have unique properties that make them viable resources for many applications, so providing the right beneficiation process can be a major advantage. Partnering with an experienced mineral processing company and using the latest technology is critical to getting the best results from your beneficiation. JXSC provides wolframite and scheelite processing plants, process design and equipment, an effective and efficient process for recovering tungsten from ore and concentrating it into salable products.