Tungsten ore is mainly divided into scheelite and wolframite. Wolframite is the oxide of tungsten, and scheelite is calcium tungsten. Although scheelite reserves are large, there are fewer rich ores, lower grade, and more difficult-to-select ores, so the mining volume only accounts for about 10% of tungsten ore production. Because scheelite often coexists with various calcium and magnesium phosphates, sulfates, carbonates, and fluorides, which have similar floatability, it is usually challenging to select qualified concentrates. On the whole, if you want to obtain ideal tungsten concentrate, you need to realize enrichment through effective processing technology. Scheelite processing has good natural floatability and is usually beneficiated by flotation.
Scheelite flotation process and equipment
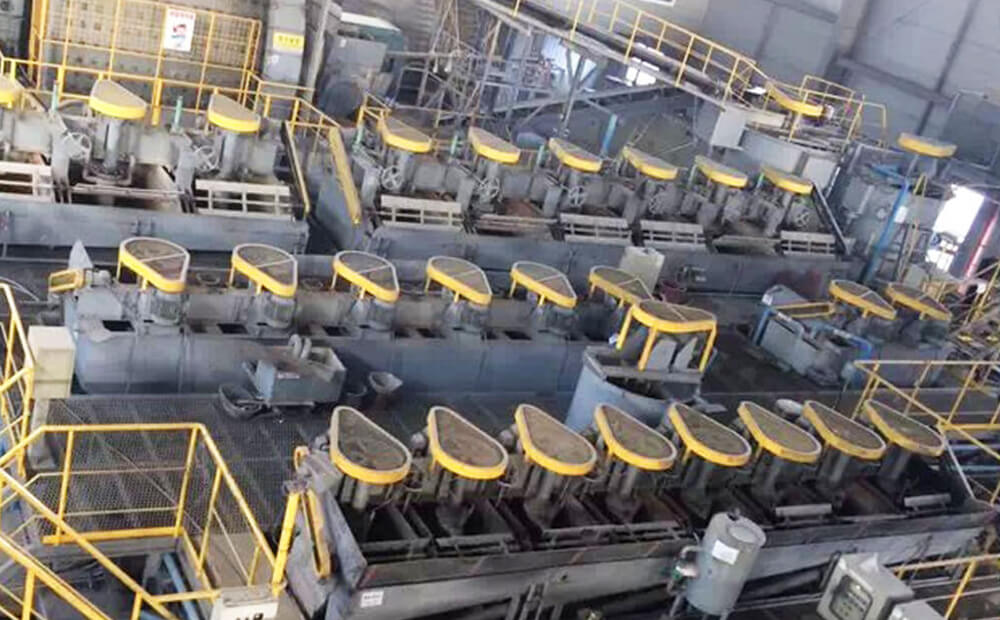
The scheelite flotation method is one of the most critical beneficiation steps. Among them, the quality of scheelite concentrate produced by re-election is higher, close to the special grade; the quality of scheelite concentrate obtained by flotation is slightly lower. Roughing is mainly to maximize the recovery of scheelite, while concentrating is to get qualified tungsten concentrate, in order to get qualified tungsten concentrate. Therefore, scheelite beneficiation is mainly carried out by the combined process of flotation and gravity separation.
1. Scheelite Gravity Separation
Scheelite has a unique high specific gravity ranging from 5.0 to 6.0 g/cm³, which can be effectively separated from lighter vein material using various gravity methods. When the difference in density between scheelite and chalcopyrite minerals is large, gravity separation is usually carried out using jig separators and shaking tables, spiral chutes. The scheelite particles are first released from the associated minerals by crushing or grinding. The jigger or shaking table can maximize the particle stratification and effectively recover the concentrate from the complex ore matrix.
2. Scheelite Flotation
The key aspect lies in the choice of traps, and selective traps explicitly designed for scheelite must be used to improve the recovery efficiency during froth flotation. Typically, fatty acids have long been the main reagents for scheelite flotation, but the potential of new biosurfactants can improve selectivity by reducing the slime coating on the mineral surface. However, the use of agents varies for different mineral situations. Selective inhibitors that we need to target specific chalcopyrite minerals can further fine-tune this parameter to improve overall floatability without compromising efficiency. Scheelite flotation equipment typically includes mechanical agitator flotation machines, aerated agitator flotation machines, or columns. Specific flotation machine models will be selected based on ore conditions and beneficiation requirements.
Scheelite flotation plant
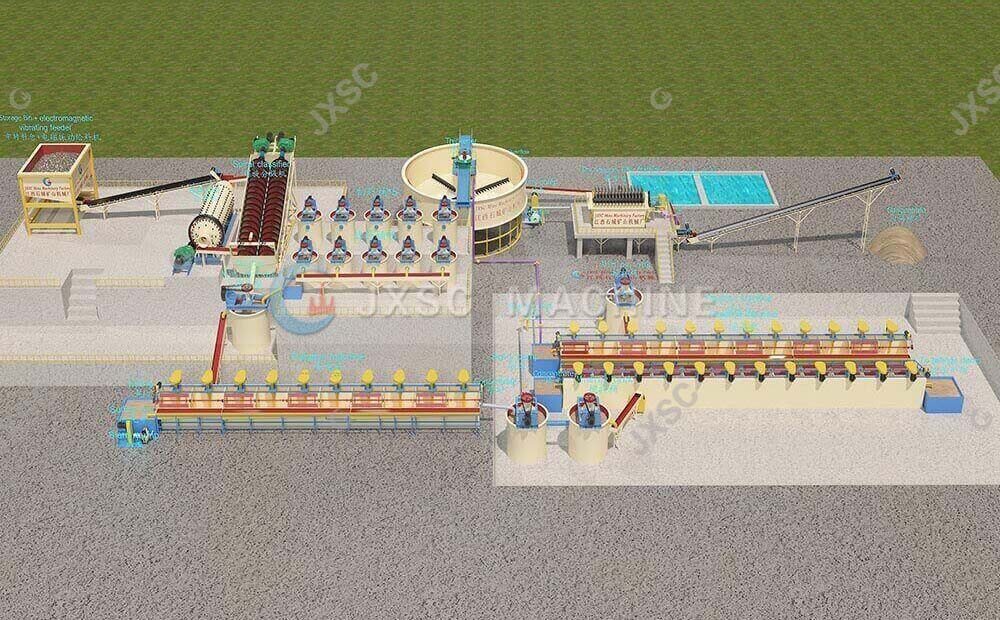
500TPD Scheelite flotation process plant
Characteristics of scheelite ore: scheelite has good floatability. There are many gangue minerals containing calcium in the scheelite ore, such as calcite, fluorite, apatite and so on, which complicate the flotation process.
This flowchart design is for a complete 500tpd scheelite ore flotation process plant. The details flow as follows:
1. Already crushed ore less than 20mm is unloaded to a fine ore bin. An electromagnetic vibrating feeder is installed under the fine ore bin to evenly feed less than 20mm fine ore to the belt conveyor, then to the ball mill.
2. The ball mill uses 2.4m diameter by 4.5m length, which can achieve 500 tons capacity daily. The output of the ball mill goes to the spiral classifier for classification of coarse particles and fine particles. The underflow of the spiral classifier is coarse particles, which will be back to the ball mill for grinding again. The overflow of the spiral classifier is fine particles,which are qualified materials and go to the flotation process. The function of the spiral classifier here is to work with a ball mill together aimed to form a closed grinding circuit. The spiral classifier here uses double spirals by 1.5meters diameter, also can use single spiral by 2 meters diameter to match 2.4×4.5m ball mill.
3. The qualified materials from the spiral classifier go to a material mixing tank, there are 5 chemical mixing tanks and 5 chemical storage tanks next to it. After the materials are mixed with chemicals, then go to the flotation machine.
4. The flotation process is divided into three stages:
1). The function of the first stage of flotation is to remove the sulfide in the raw ore. 10 cells of flotation machines are used, respectively: cells for roughing separation once, 6 cells for scavenging separation twice, and 3 cells for concentrating separation once, all of which use SF-4 model flotation machine.
2). The function of the second stage of flotation is to remove the easy floating impurities in the raw ore. 18 cells of flotation machine are used, respectively: 4 cells for roughing separation once, 12 cells for scavenging separation thrice, and 2 cells for concentrating separation once, all of which use SF-4 model flotation machine.
3). The function of the third stage of flotation is to remove the gangue containing calcium in scheelite. 18 cells of flotation machine are used, respectively: 4 cells for roughing separation once, 8 cells for scavenging separation twice and 6 cells for concentrating separation quintic. SF-2.8 flotation machine is used for roughing separation, scavenging separation and the first concentrating separation, and SF-0.7 flotation machine is used for the second to fifth concentrating separation.
After the three-stage flotation process, impurities such as sulfide and calcium-containing gangue were removed, making the final scheelite concentrate with high grade and good quality.
5. Finally, the scheelite concentrate after flotation is sent to thickener by slurry pump for adjusting the slurry density that is required by the disc vacuum filter, then the underflow of thickener is sent to disc vacuum filter by slurry pump for filtering and dewatering concentrate. The overflow of thickener is clear water which goes back to the return water pool.
Scheelite flotation is a more effective method for separating and extracting tungsten concentrate. Its efficiency largely depends on the selection and configuration of equipment, such as flotation machines and conditioning tanks, which must be optimized for specific ore characteristics. In addition, understanding and managing key variables such as pH and reagent type can further improve recovery. JXSC supports customized mineral processing solutions and complete equipment; contact us for more details!