Lead-zinc are widely used in the electrical, mechanical, military, metallurgical, chemical, light, and pharmaceutical industries. In addition, lead metal also has many uses in the nuclear industry, petroleum industry, and other sectors. Lead and zinc usually coexist in nature, so the mining and beneficiation of lead and zinc ores often need to consider the extraction of these two metals simultaneously. The purpose of lead and zinc ore beneficiation is to maximize the recovery of valuable metals and minimize the generation of waste. By designing and optimizing reasonable crushing, grinding, flotation, concentration and dewatering process, the industrial utilization and efficient recovery of lead and zinc resources can be achieved. Next, we will analyze these four processes!
About Lead-Zinc Ore beneficiation
Lead-zinc ore is a mineral rich in metallic elements such as lead and zinc. Among them are 11 kinds of lead industrial minerals and six kinds of zinc industrial minerals, among which galena and sphalerite are important. Lead-zinc ore is usually not a single lead or zinc mineral but a symbiosis of multiple lead-zinc minerals, such as galena (PbS), sphalerite (ZnS), and pyrite (FeS2). The development of industries such as the automobile, transportation, construction, and telecommunications industries is the main driving force for the strong momentum of demand for lead-zinc ore. However, lead-zinc ore must be processed and purified as a mineral resource before it can be used in industrial production.
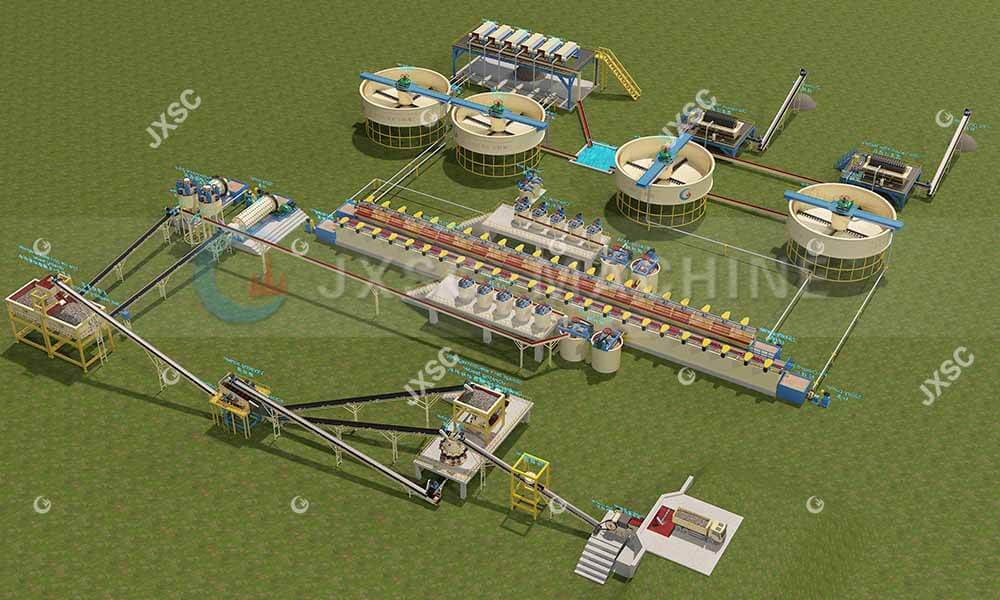
Lead-zinc Ore Beneficiation Process
Lead-zinc ore beneficiation usually requires a comprehensive process flow to ensure efficient recovery of lead and zinc and minimize the loss of other valuable elements. Lead-zinc ores usually contain a variety of valuable metals. Flotation can extract lead and zinc and recover other metals through corresponding reagents and process design. Therefore, the main processes include crushing, grinding, flotation, concentration and dewatering. Due to the differences in ore characteristics, the specific beneficiation process needs to be optimized and designed according to its specific mineralogical characteristics.
1. Lead-zinc Crushing Process
The lead-zinc ore crushing stage is the first link in the entire ore dressing process. Its purpose is to crush the mined lead-zinc ore from larger blocks into smaller particles for subsequent grinding and beneficiation operations. It usually includes two sub-stages: coarse crushing and fine crushing. In the coarse crushing stage, jaw crushers are usually used to coarsely crush large pieces of ore for subsequent transportation and processing. In the fine crushing stage, cone crushers, impact crushers, and other equipment are used to crush the ore into smaller particles further to reach a particle size suitable for grinding and prepare for subsequent process steps. The design of the crushing stage should be determined according to the physical properties of the ore and the required final product particle size, while also considering the stability and energy efficiency of the equipment.
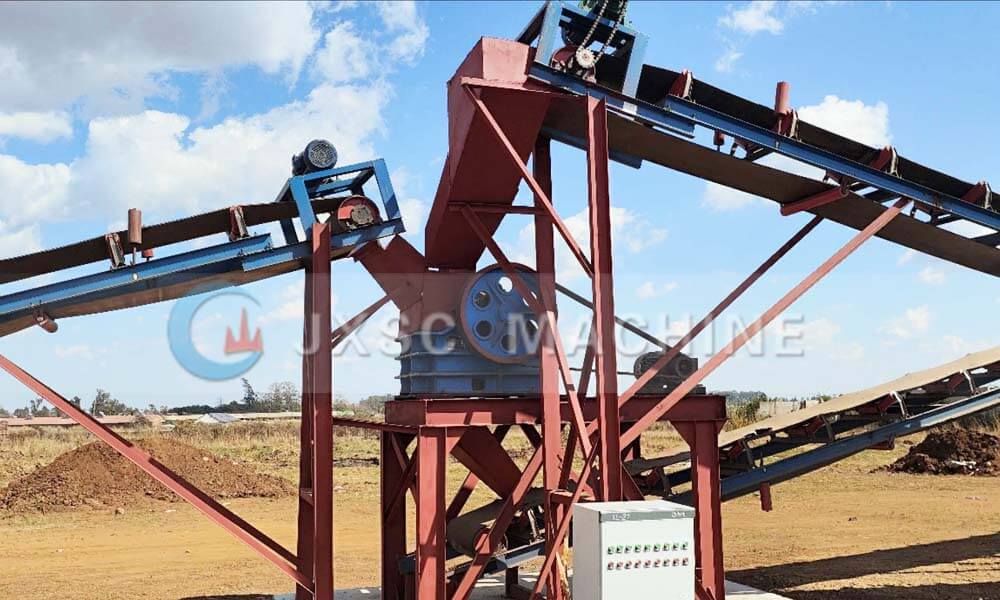
2. Lead-zinc Grinding Process
The grinding stage of lead-zinc ore is a key link in the ore dressing process. Its purpose is to grind the crushed lead-zinc ore further so that the valuable minerals, such as galena and sphalerite, can be fully exposed. Equipment such as ball mills or rod mills are usually used in the grinding stage, which grind the materials through internal grinding media (such as steel balls or steel rods). The grinding process grinds the ore into fine particles, even up to micron size, for the subsequent flotation process. The selection of grinding media and the control of grinding conditions (such as mill speed, grinding time, grinding media filling rate, slurry concentration, temperature, etc.) directly affect the grinding efficiency and product particle size distribution. In addition, the slurry after grinding is usually classified by classification equipment (such as spiral classifier, hydrocyclone) to separate qualified fine-grained products to ensure the uniformity of the particle size of the grinding product, and finally obtain a slurry suitable for flotation.
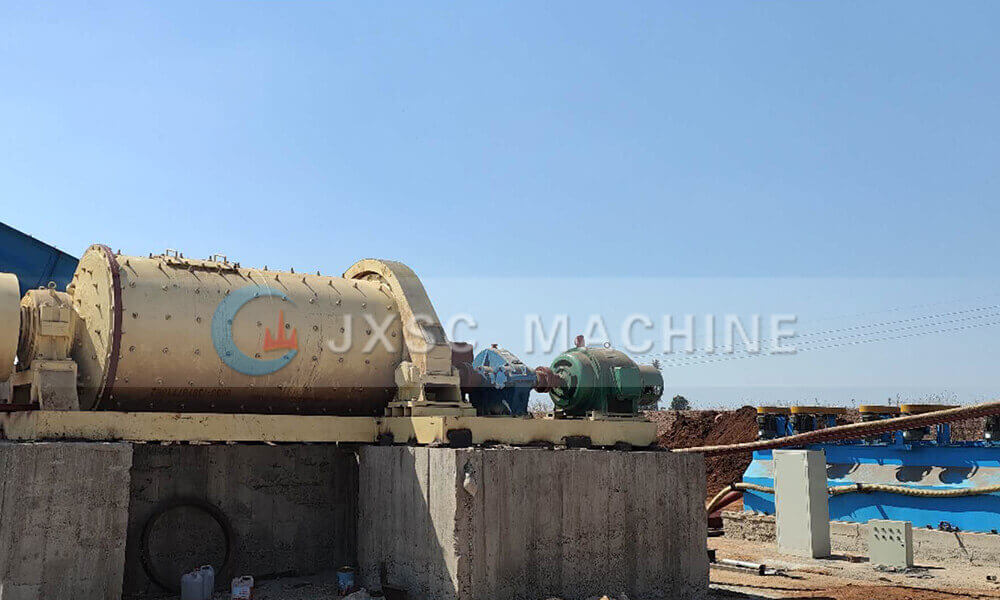
3. Lead-zinc Flotation Process
The flotation stage of lead-zinc ore is a key method for extracting metals from lead-zinc ore. Flotation reagents separate the target minerals (galena, sphalerite). In this stage, the fine particles formed by grinding the ore are mixed in a slurry containing an appropriate amount of water and stirred with specific reagents to form bubbles. These bubbles can selectively attach to the surface of the target minerals, such as galena and sphalerite, making them hydrophobic. Subsequently, a scraper scraps the mineralized froth layer to obtain a concentrate product with a higher concentration of lead and zinc. A scraper scrapes off the mineral particles in the froth layer or a bubble collection device to form a concentrate product with a higher lead and zinc content. The flotation process usually includes roughing, separation, and scavenging stages, which can efficiently recover lead and zinc minerals.
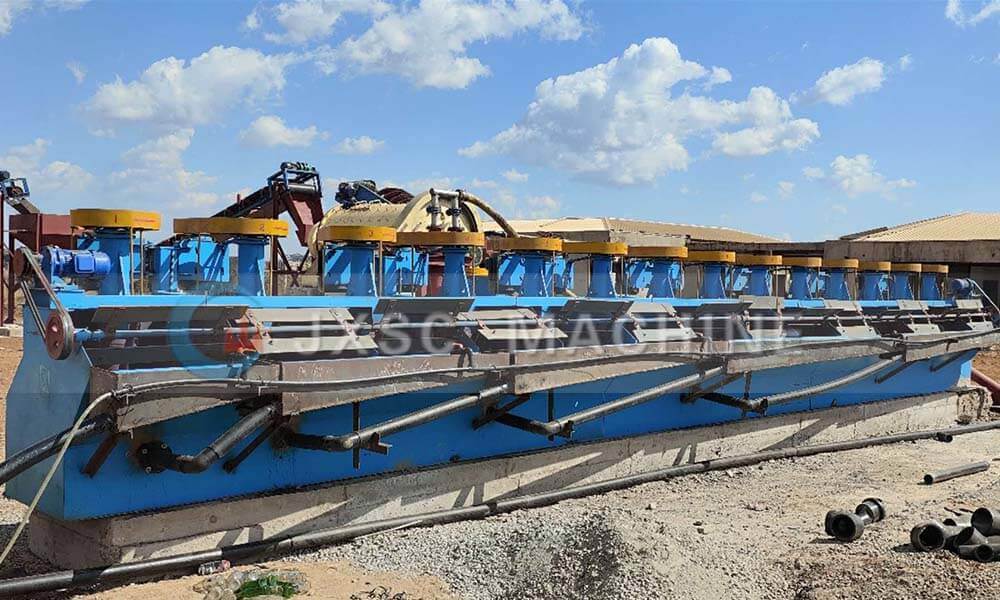
3. Lead-zinc Concentration and dewatering process
Lead-zinc ore concentration and dewatering stage is usually the last step of the mineral processing process. The solid particles in the concentrate slurry are separated from the liquid mainly by gravity or centrifugal force to reduce the moisture content. This usually uses a thickener to separate the solid particles from the liquid by gravity or centrifugal force, and the concentrated concentrate has a high-concentration concentrate slurry. The concentrated concentrate still contains a lot of water, so it needs to be further sent to the dewatering stage. Dewatering treatment is required to remove moisture and obtain a dry concentrate product. Generally, equipment such as plate and frame filter press or vacuum filter separates solid mineral particles from the liquid by physical or mechanical filtration to obtain a relatively dry concentrate. The dehydrated lead-zinc concentrate can meet the packaging and transportation requirements, providing pure and high-grade raw materials for further processing of lead and zinc metals.
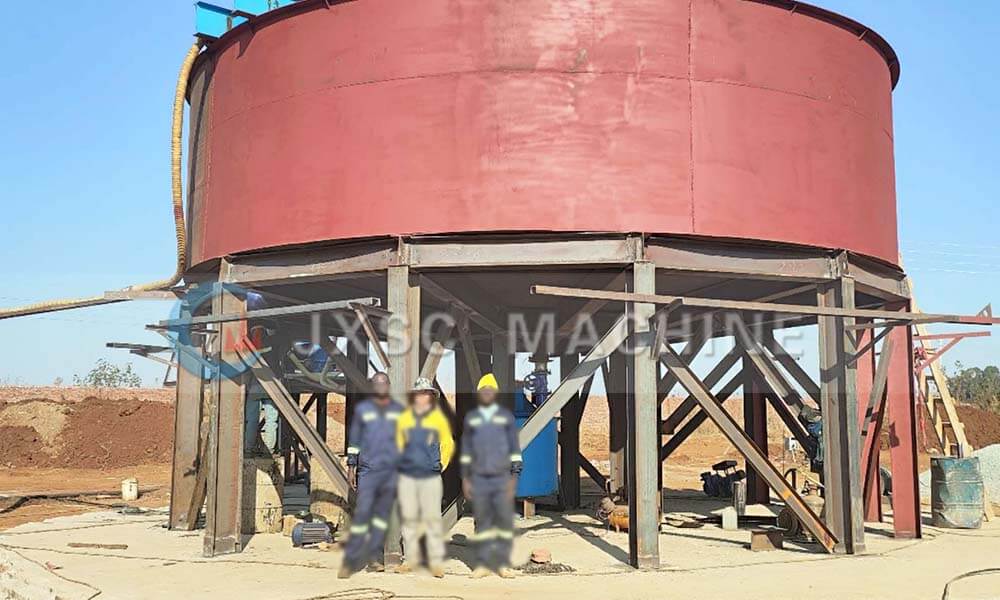
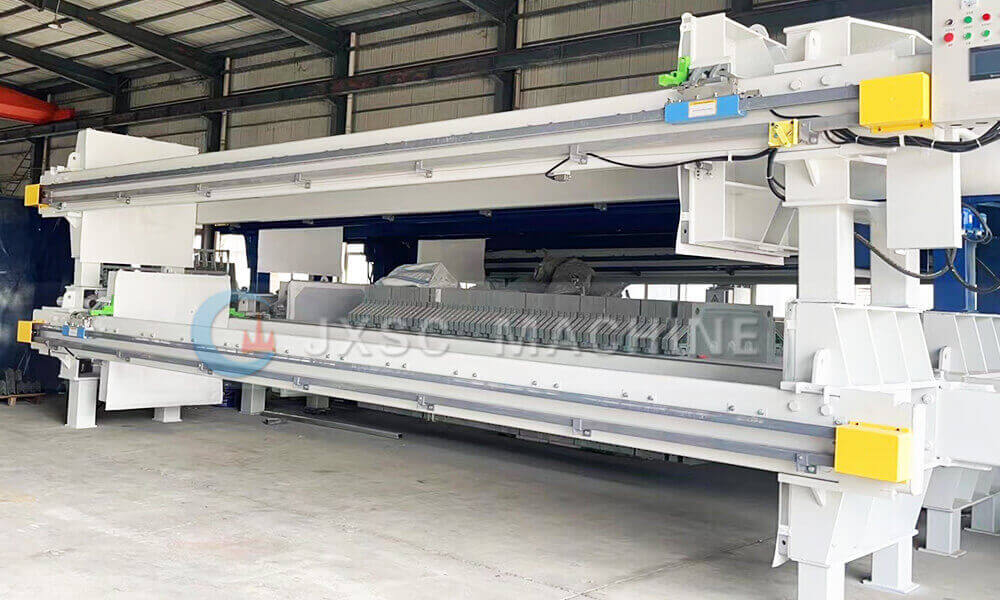
The beneficiation process of lead-zinc ore usually starts with crushing and grinding, breaking the ore into fine particles to release the mineral particles. Then the mineral is enriched by flotation, and then enters the concentration and dehydration stage to obtain a high-grade and dry concentrate product. The specific beneficiation process and equipment need to be determined according to the characteristics of the mineral. JXSC can provide carefully customized ore beneficiation solutions and equipment to improve efficiency and metal recovery while reducing energy consumption and environmental impact. Contact us to get process details and machine latest price!