The high-temperature problem of the ball mill is a common concern of many manufacturers and operators, and it is also a common problem that affects the efficiency and performance of these industrial equipment. Excessive heat generated during grinding can lead to equipment damage, reduced efficiency, and even production delays. As ball mills are widely used in various industries such as cement, mining, chemical industry, etc., ensuring the best performance and prolonging the machine’s service life is very important.
High temperatures can cause many problems, including reduced yields, increased energy consumption, and equipment failure. We will explore four practical ways to help alleviate high-temperature problems in ball mills. Each approach has unique benefits and challenges, from optimizing ventilation systems to implementing insulation techniques. By implementing these strategies, operators can mitigate overheating problems and extend the life of the ball mill while optimizing production processes.
1. Adjust the water cooling system
Over time, dust and debris can accumulate in the cooling system of the ball mill, resulting in reduced efficiency and increased heat generation. Insufficient cooling can lead to problems such as reduced efficiency, increased wear on components, and possibly even damage to the mill itself. You can increase your cooling efficiency by keeping your cooling system clean and free from obstructions. Mainly through the following methods:
- Check the cooling system: First, make sure the cooling system is working correctly. Check whether the cooling water supply and circulation are regular, and ensure that the water pumps, coolers, and cooling pipes in the cooling system are not blocked or faulty.
- Increase the flow of cooling water: If the temperature of the ball mill is too high, consider increasing the flow of cooling water. By increasing the working pressure of the water pump or adjusting the speed of the water pump, the flow of cooling water can be increased, thereby effectively reducing the temperature of the ball mill.
- Improved cooler design: The cooler is an important cooling system part. Optimizing the design of the cooler can improve the cooling effect. Consider increasing the area of the cooler, increasing the number of cooling fans, or increasing the speed of the fans to increase heat dissipation.
- Installing additional cooling equipment: Additional cooling equipment can be considered if the existing cooling system cannot meet the requirements. For example, equipment such as cooling towers or cooling coils can be added to increase the cooling effect.
- Using coolant: Adding coolant to the cooling water can improve the heat dissipation performance of the cooling water and further reduce the temperature of the ball mill.
- Control the load: Properly control the load of the ball mill to avoid excessive use or heavy load, which can reduce the heat generated by wear.
- Temperature monitoring and control: Install a temperature sensor to monitor the temperature of the ball mill in real time and adjust the operation of the cooling system as needed.
- Clean the cooling system: Regular cleaning of the cooling system is key to keeping it functioning correctly. Deposits, dirt, and corrosion products can clog the cooling system and affect cooling effectiveness. Regularly check and clean the filters, coolers, and cooling ducts in the cooling system to ensure they are unobstructed.
According to the situation, it may be necessary to take appropriate solutions for a specific ball mill and working environment. It is best to discuss further and consult with a professional equipment manufacturer or engineer to obtain the best solution for the specific situation.
2. Regular Oil Change
Ball mills are key mining grinding equipment used in mineral processing plant, rely heavily on proper lubrication to ensure smooth operation and prevent overheating. However, this oil may degrade over time due to contamination, oxidation, moisture or foreign matter dilution. This degradation impairs its ability to provide effective lubrication and thermal regulation, resulting in elevated temperatures within the mill. Using a high-quality lubricant designed for high-temperature applications reduces friction between moving parts and prevents excessive heat build-up. The root cause of the high temperature needs to be identified before the problem can be addressed. High-temperature problems can be caused by several factors such as friction, poor seals, insufficient lubrication, etc. Checking the equipment and locating the problem is critical. Then proceed to the following method:
- Check the type of lubricating oil: choose high-temperature lubricating oil suitable for the operating conditions and load requirements of the ball mill, which has a high viscosity index and anti-wear performance and can provide effective lubrication and protection in high-temperature environments.
- Regularly change lubricating oil: Even if there is no high-temperature problem, a regular lubricating oil change is essential in maintaining equipment. Regular oil changes can avoid problems caused by oil aging or contamination.
- Use high-quality lubricating oil: Choose high-quality lubricating oil to ensure it can work effectively under high temperatures and high-pressure conditions. High-quality lubricants generally have better high-temperature performance and anti-wear characteristics.
- Reasonable use of equipment: Regularly check the ball mill’s seals, bearings and other key components. Make sure to operate the ball mill correctly and avoid overloading it. Excessive loads can lead to an increase in the temperature of the device and affect the lubrication effect.
3. Environmental conditions for using the ball mill
The high-temperature problem of the ball mill may be caused by friction and energy dissipation, and the following methods can improve the solution to this problem:
- Enhanced ventilation: Ensure adequate ventilation around the ball mill to dissipate the heat. Airflow can be improved by adding ventilation, fans, or air conditioning.
- Control humidity: High-humidity environments can cause condensation or corrosion on the ball mill, exacerbating high-temperature problems. Ensure the humidity is within an appropriate range, and air conditioners, dehumidifiers and other equipment can control the humidity.
- Reduce heat sources: Minimize other heat sources around the ball mill, such as motors or other equipment. These heat sources increase the ambient temperature, which in turn affects the temperature of the ball mill.
- Regular cleaning: Regularly clean the ball mill and its accessories to ensure a dust-free and dirt-free working environment. Dust and dirt reduce cooling efficiency and cause temperatures to rise.
4. Type selection of ball mill
Choosing a ball mill with an excellent structural design and advanced technology is very important. A well-designed ball mill will have effective heat dissipation performance to ensure that the temperature in the cylinder remains within a controllable range during operation. In addition, choosing a machine with good sealing performance can prevent external airflow from entering the cylinder and reduce heat loss. Our ball mills are optimized in design by using highly heat-resistant materials and improving ventilation. You should consult us online, choose a ball mill that suits your needs, and obtain targeted solutions!
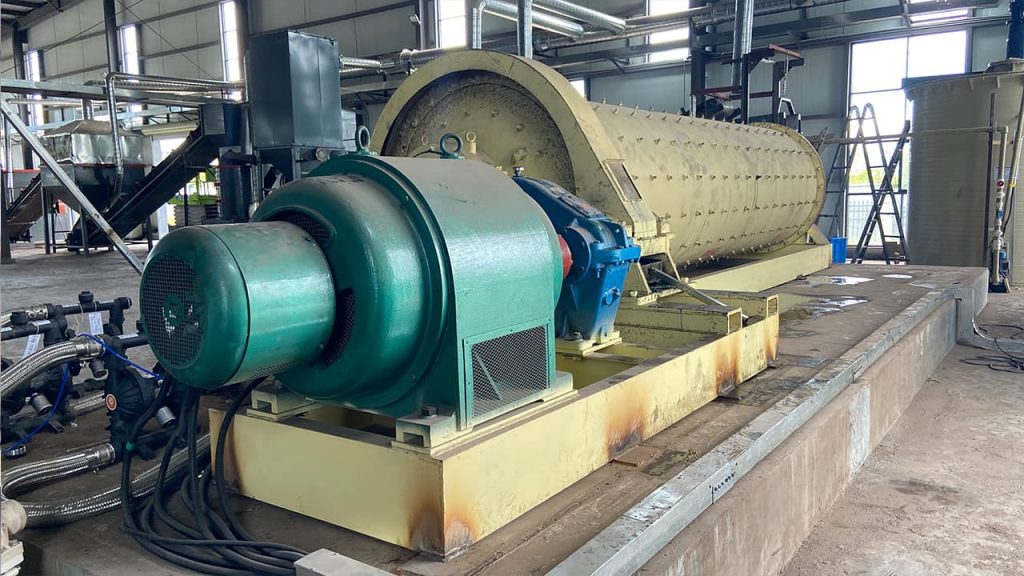
The problem of high temperatures in ball mills is a prevalent problem that needs to be addressed to improve their performance and efficiency. By implementing the solutions discussed in this article, such as proper lubrication, regular maintenance, and the use of cooling devices, the temperature of a ball mill can be effectively controlled. Not only does this prevent the equipment from overheating and potential damage, but it also increases its overall productivity and lifespan. Therefore, operators and manufacturers must proactively mitigate this issue and ensure smooth ball mills operation. Choose our solution to maximize your ball mill’s performance and service life while providing the best safety standards. If you need mining equipment with full quality assurance, it is recommended that you choose a well-known brand and a reputable supplier. JXSC will benefit you a lot!