Gravity Beneficiation, CIP Plant for Gold-Copper Ore Processing
Executive Summary
1.1 Background
In 2008, a substantial preliminary metallurgical program was carried out on ore from the Kalkaroo Copper-gold deposit in South Australia. Four ore types were tested including the oxide saprolite gold cap and native copper, as well as secondary chalcocite and primary chalcopyrite sulphide ore.
Subsequent to the completion of the 2017-2018 work, several metallurgical opportunities were identified where the value of the Kalkaroo project could be materially improved if positive results from further testwork could be achieved.
The primary aim of the Saprolite gold separation testwork was to establish a gold recovery process to improve on the approximately 50% recoveries achieved using gravity-flotation concentration. Based on previous scoping testwork there was indication that improved recovery may be achievable using cyanide leaching where greater than 90% gold extraction to leach solution was demonstrated. However, notable copper from the ore was also extracted to leach solution at concentrations anticipated to cause complexity in downstream processes such as elution and electrowinning.
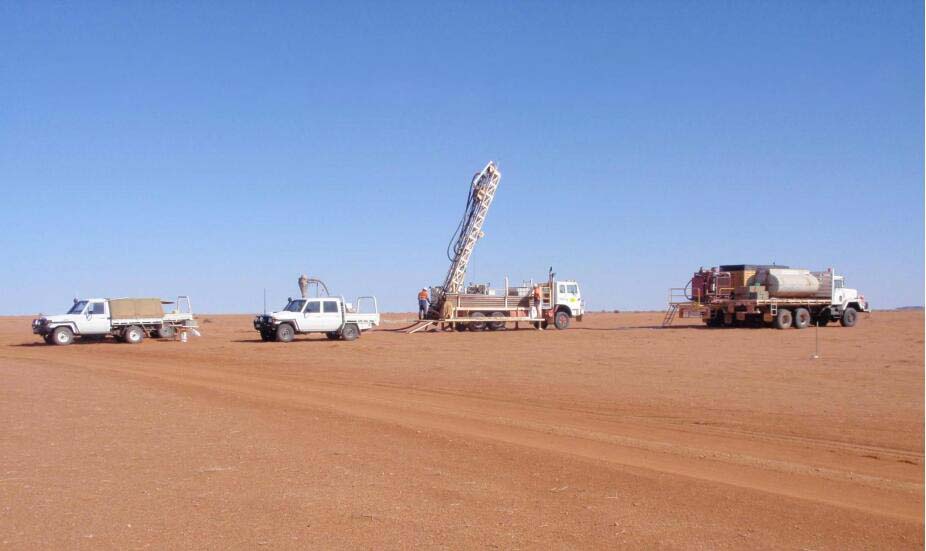
1.2 Objectives
Specific objectives of the 2018-2019 metallurgical program were to:
1. lmprove gold recoveries of Saprolite Gold ore primarily through evaluation of cyanide leaching(CIL/CIP)
processes.
2. Evaluate the opportunity to improve Native Copper ore gold recovery through the use of a cyanide
leaching following copper recovery.
3. Determine attritioning and milling characteristics of oxide ore of varied saprolite composition.
4. Evaluate copper-gold recovery from low grade chalcocite ore to improve on previously extrapolatedresults.
5. Confirm a flowsheet to recover a pyrite concentrate from chalcopyrite and chalcocite ore copper tailingsand determine concentrate marketing specifications.
6.Determine potential of treating pyrite concentrates to extract contained copper, cobalt and gold.
1.3 Testwork & Outcomes
A total of 18 composites described in Table 1.1 were prepared to achieve the desired objectives. Compositesused a substantial quantity of half and quarter PQdiamond drill core recovered from three holes drilled duringSeptember 2018 specifically for the purpose. Additional suitable sample from previous driling programs wasalso used where insufficient fresh sample was available for scoped the testwork. Details of selected intervalsfor each composite are provided in Appendix A.
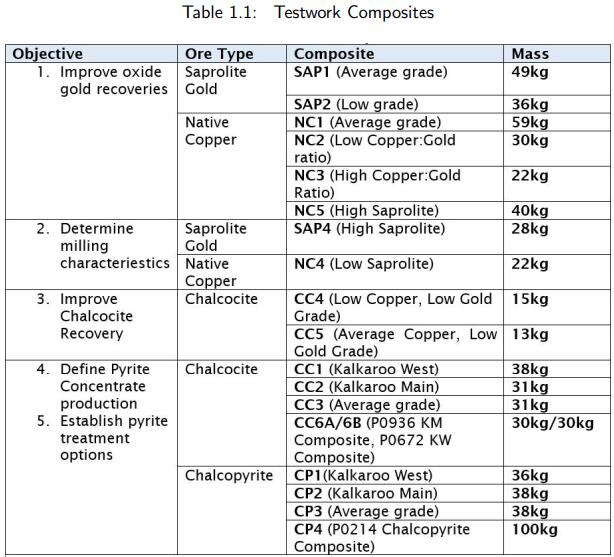
1.3.1 Saprolite Gold
Previous work on the saprolite gold ore indicated that gravity & flotation or cyanide leaching were po-tentially feasible to generate saleable products though each had limitations. Gold flotation only achievedapproximately 50% recovery while cyanide leaching also notable copper creating uncertainty on downstreamprocessing.Evaluating the impact of copper in cyanide leaching and confirming the associated gold recov-eries was the focus of the latest program. Due to the high gold to copper value in the ore type, focus wasgiven to gold recovery only.
On the prepared composites,firstly a small characterisation investigation was undertaken including a sizeassay analysis. Following, prior to cyanidation of the ore, pretreatment methods were also tested to optimisefeed. These methods included gravity concentration, cyclone desliming and acid pre-leaching.Final testworkconsisted of cyanide carbon-in-leach testing followed by caustic cold elution of final loaded carbon.
Key findings from testwork included:
- Greater than 30% of the ore mass was contained in the minus 10um fraction while only containing16% of gold in the life-of-mine sample.Consistent with this finding was cyclone desliming with D50sof between 5 and 10um could remove 20%-30% of mass to be treated while retaining approximately95% of gold. Approximately 25% – 35% of copper would also be rejected.
- Acid pre-leaching of the ore only achieved less than 15% copper extraction. Gravity separation with a Knelson concentrator and superpanner only achieved 25% gold recovery witha relatively low grade concentrate of 130g/t Au.
- Consistent with previous cyanide leaching testwork, greater than 90% of gold was recovered to carbonusing conventional ClL conditions.
- Through CllL testwork it was demonstrated that when increasing gold loading to carbon,copperloading did not significantly increase, therefore likely that acceptable copper:gold loading ratios couldbe achieved.
- Additionally it was demonstrated that cold caustic elution on final carbon could remove between 83%and 97% of copper with minimal gold loss (<1.2%).
Provided with the above findings, it is likely that cyanide ClL treatment would be a viable gold recoverymethod. Thus,further investigation to establish greater certainty in engineering design parameters may bewarranted. This may include, ClL testing with increased gold loading to carbon and optimised ClP triplecontact tests. Following, pilot testwork including elution processing and electrowinning may provide greaterindication of expected plant performance.
For pretreatment of the ore prior to leaching, it is unlikely that an acid pre-leach or gravity concentra-tion would be considered to remove copper and/or produce an additional copper concentrate. However,desliming to remove excessive mass may be beneficial with the additional benefit of removing potentiallynuisance copper. lf demonstrated as feasible through economic trade-off studies,desliming should be usedprior to any cyanide leaching ensure tests reflect the expected process flowsheet.
1.3.2 Native Copper
Previous treatment strategies of Native Copper ore focussed on recovery of coarse native copper usingclassification and gravity methods which was followed by the recovery of a copper flotation concentrate.Previously not explored was the potential to recover an additional gold product through cyanide leaching.This was the focus of the recent program where the desired flowsheet was to consist of initial gravity/flotationconcentration to produce a copper concentrate followed by a cyanide leach of tailings.
Commencing the program,3 composites were made,an average Life-Of-Mine composite, a compositewith moderate copper and gold grades and a composite of low copper to gold ratio, each with a saproliteclay content of approximately 25%. Following,further investigation it was found that approximately 66%saprolite clay in Native Copper ore is expected over the Life-of-Mine, at which point an additional compositewas made to reflect this lithology, however only achieving a saprolite content of approximately 50%. Furthertestwork may benefit from samples a more representative saprolite content.
Testing on the Native Copper ore composites initially focussed on ore characterisation investigation in-cluding size-assay analyses,sequential dissolution analyses and heavy liquid separation to establish processlimitations.Concentration methods including cyclone desliming was then trialled followed by classification,gravity and flotation to determine potential copper recovery through open circuit testing only. Limitedcyanide leaching testwork was then conducted.
Key findings from the testwork included:
1. Cyclone desliming testwork demonstrated that between 16-18% of mass of tested composites couldbe rejected while maintaining 92-93% of copper and gold which was consistent with indications fromsize-assay analyses.
2. Limited copper recovery of a maximum of approximately 73% could be achieved with the new com-posites when using previously developed classification, gravity and flotation flowsheets that yielded83% recovery.This reduction is expected to be primarily associated with representativity of the newcomposites made.
3. Testing of the gold recovery process using cyanide leaching was successful through a single conventionalcyanide leaching test on NC1 gravity tailings that achieved approximately 90% gold recovery. Whileexcessive copper was also leached and adsorbed to carbon, this was shown to be managed through acold caustic elution process where 98% of copper could be removed with negligible gold loss.
ln addition to the work completed as part of this testwork program, to demonstrate a revised flowsheetwith improved copper and gold recoveries (compared to the RPMGlobal work) further investigation andtestwork is required to establish confidence to a pre-feasibility study level. lt is firstly required to confirm thenative copper recovery process that may include some vendor testwork optimisation and potentially furtherbulk open circuit or bench locked cycle testing.Once copper recovery is confirmed with limited nuisancecopper reporting to tailings,cyanide (CIL) leaching is required to be conducted similar to that conductedon the saprolite gold composites to establish carbon loading characteristics and reagent consumptions.
1.3.3 Saprolite Gold Attritioning
As part of the flowsheet from the 2017-2018 PFS by RPMGlobal, the oxide ore preparation circuit includedscrubbing-attritioning processes where only oversize material would be sent to grinding mill. In the studythe relative quantity and hardness of the oversize material was unknown due to limited previous testworktherefore estimations based on saprolite clay contents were used.
To achieve greater certainty for the grinding requirements of oxide ores,2 composites were made onecontaining approximately 75% saprolite clay and the other containing 25%. These were composited from1/2 PQ diamond drill core of appropriate lithology crushed to -12.7mm. Each composite was subjectedto initial dry screening to 600pum to determine initial ore sizing, this was followed by wet screening with a75jum final screen that was expected to simulate an attritioning process. On the composite of high saprolitecontent, lab scale scrubber and attritioning equipment was used to establish ore amenability to the proposedprocess.
1. The wet screening tests indicated that for the ore of high (75%) saprolite content,57% of materialwould not require grinding, while on the ore of low (25%) content,21.3% would not require grinding.
2. Using the lab scale attritioner on the high saprolite composite, approximately 10% more material (i.e.approximately 67%) would not require grinding.
3. Relative Bond Ball Mill Work index (BBMWi) determinations on the +75um fractions of the oredemonstrated that the component of ore requiring grinding had a BBMWi of between 6.3KWh/t onhigh saprolite ore and 8.7KWh/t on low saprolite ore which classifies the coarse component as beingbetween ‘Very Soft’ and ‘Soft’.
Further (vendor) testwork to demonstrate quantity and hardness of material requiring grinding may berecommended. This may include the use of composites with a greater range of saprolite contents.
1.3.4 Chalcocite (Low-Grade)Separation
Previously, testwork on Kalkaroo chalcocite ore was conducted on ore of head grades down to 0.57% Cuand 0.43g/t Au. In the RPMGlobal PFS for chalcocite ore with head grades below this copper and goldrecoveries to concentrates were extrapolated. In the case of gold, this was sometimes to less than 40%.Therefore,using previously established gravity-flotation conditions,two composites (CC4 and CC5) weretested which contained 0.25%Cu,0.21g/t Au and 0.53%Cu, 0.25g/t Au respectively. Initial test resultsindicated some improvement could be made where relatively low copper and gold recoveries were observed.Thus,primary grind size was investigated to yield better results.
Key findings from the testwork included:
1. Aprimary grind size of P80=75yum compared to the previously established P8O=106um could notablyimprove copper and gold recoveries to the final concentrate (by up to 9.6% of copper and 14.6% ofgold).
2. Approximately 20% of gold reported to a prite concentrate that was generated from copper tailings.
3. Approximately,10% of gold in the final copper-gold concentrate was associated with the preliminarygravity separation step,ahead of the copper flotation.
4. Final locked cycle test results resulted in gold recoveries for CC4 and CC5 composites from a flotationprocess being between 50% and 56%,an improvement on previous extrapolation.
To further improve the grade-recovery curve and improve certainty, further testwork may assess a greaterrange of sample, ensuring appropriate lithology and transitional material is understood. To ensure final testsreflected previous testing processes, locked-cycle testing was not conducted on the preferred gravity tailingsfeed and required corrections to be made to establish final recovery results. It may be preferred in furthertesting to have testing conducted directly on gravity tailings.
1.3.5 Chalcopyrite & Chalcocite Ore Pyrite Concentrate Production
Previous testwork on Kalkaroo chalcocite and chalcopyrite ores demonstrated the potential to produce pyriteconcentrates from each ore type. However limited investigation was conducted to optimise the productionof the concentrate or establish marketing specifications. Separately on each chalcocite and chalcopyriteore types, gravity-flotation testwork was conducted as part of the current program to produce a copperconcentrate per best flowsheets developed from the previous test programs, pyrite was then floated fromcopper tailings using a range of flowsheets and testwork conditions.
Key findings from the flowsheet scoping investigation included:
1. 2 pyrite cleaner stages for both chalcocite and chalcopyrite ore are required to produce a clean con-centrate of approximately 90% iron plus sulphur grade.
2. Pyrite concentrates produced from chalcocite ore copper rougher tailings and cleaner tailings havea significant recovery improvement over flotation from cooper cleaner tailings only. While pyriteconcentrates from chalcopyrite ore had limited improvement floating from both tailings streams overthe copper cleaner tails only.
3. There was a significant improvement in copper and pyrite separation as well as in overall metal recoveryin chalcocite ore with a finer grind of P80=75[um compared with the previously used 106pm.However,little benefit was yielded from the finer grind on chalcopyrite ore.
oControlled Potential Sulphidisation (CPS) was required to be conducted on chalcocite ore to recoverup to 50% of the pyrite concentrate that would otherwise be unrecoverable.
Final testwork used the best flowsheet and conditions from above findings in a series of locked cycleflotation tests. These tests were conducted on bulk copper flotation tailings of each chalcocite and chal-copyrite ore. Production of clean pyrite concentrates from each was confirmed at approximately 90% ironplus sulphur. Appreciable levels of copper (0.61%-2.0%) cobalt (2900-3400g/t) and gold (2.43g/t-3.59g/t)were also demonstrated in final locked-cycle testwork. Additionally, through detailed concentrate analysislow levels of penalty elements were observed, e.g. arsenic which remained at 0.10% or less.
Opportunity still exists to further investigate the opportunities to improve copper and prite concentrateseparation through mineralogical diagnostics to establish limitations, then further investigating the effect ofvarying process conditions e.g. alternative reagents and grind size.
1.3.6 Chalcopyrite & Chalcocite Ore Pyrite Concentrate Treatment
Following the establishment of pyrite concentrate production flowsheet in Section 1.3.5 where appreciablecobalt, copper and gold was recovered, there was potential opportunity to extract these metals into furtherrefined products. Testwork to establish this was conducted on pyrite concentrates generated from bothchalcopyrite ore and chalcocite ore. Two primary flowsheets were considered i.e. direct acid leaching of theconcentrate to extract copper followed by cyanide CllL to recover gold; and using a roasting step prior toleaching to enable a greater fraction of cobalt and gold to be leached.
From testwork it was established:
1. Direct leaching of the prite concentrates could extract between 83-89% of copper and negligiblecobalt. While the following cyanide leach was able to recover between 59% and 68% of gold tocarbon.
2. Sulphating roasting,followed by water and acid leaching to extract cobalt and copper, then cyanideClL to recover gold shown as the best recovery process. An approximate 70% increase in cobaltrecovery was observed with a 20% increase in gold recovery when compared to direct leaching (SeeTable 8.7).
3. Dead roasting (conducted at an elevated temperature) to sulphating roasting was showed to notablyreduce leaching amenability and therefore would unlikely be a viable processing option.
The testwork completed to establish the potential of recovering copper,cobalt and gold was to a scopingstudy level only to assesses potential feasibility of the processes. Using findings from this, further processesmay be tested e.g. alternatives to roasting to oxidise the pyrite concentrates prior to leaching.Once thebest processing option is selected, further testing will be required for pre-feasibility study level certainty.
1.4 Conclusions and Recommendations
The majority of objectives set out at the commencement of the testwork program were achieved and success-fully evaluated opportunities to improve metallurgical results used in the existing Kalkaroo PFS. lmprovedgold recoveries through ore types were achieved and pyrite concentrate recovery along with the containedcopper,cobalt, gold recovery opportunities were confirmed. Specifically,with respect to area:
1. Saprolite Gold ore was demonstrated to be amenable to cyanide leaching where greater than 90%of gold was recovered to carbon (c.f. 50% using flotation)while excessive cyanide consumption andcopper loading was not observed. Any excessive copper was shown be managed through the use of acold-caustic elution process,additionally cyclone desliming could both reject ore mass to be treatedand further reduce copper levels.
2. Native Copper ore tested did not perform as expected with respect to the recovery of coarse nativecopper using classification,gravity and flotation that was established in previous programs. However,the cyanide leaching tests performed on gravity tailings still demonstrated the ores amenability tocyanide leaching. Similarly to Saprolite Gold ore approximately 90% stage gold recoveries were achievedwith copper potentially removed from carbon using cold-caustic elution.Copper levels however werehigher and further testwork however will be required to establish PFS certainty.
3. Saprolite Attritioning testing successfully showed that for test composites of high (75%) saprolite
content that the majority of ore would not require grinding.Furthermore,ore that would report tothe mill is classified as being ‘Very Soft’ to ‘Soft’with the BBMWi ranging between 6.3kWh/t and8.7kWh/t.
4. Chalcocite (Low-Grade) testing of ore with head grades previously extrapolated successfully achieved
improved gold recoveries of between 50% and 56%. This was achieved through investigation of effectof primary grind size where a fine grind of P80 of 75yum was identified as best. lt is noted thatextrapolated recoveries in the range of head grades tested was previous below 40%.
5. Pyrite Concentrate Production flotation flowsheets were confirmed for both chalcocite and chal-copyrite ores through the investigation of reagent schemes, grind size, number of cleaning stagesand use of copper cleaner and/or rougher tailings as feed. Ultimately through locked-cycle flotationtesting, clean pyrite concentrates (90%iron + sulphur) were shown to be produced with appreciablelevels of copper (0.61%-2.0%), cobalt (2900-3400g/t) and gold (2.43g/t-3.59g/t) and low deleteriouselement levels such as aresenic (<0.10%).
6. Pyrite Concentrate Treatment was shown possible using a direct leach approach using an acid leach,recovering approximately 83-89% of copper then 59-67.5% of gold with a cyanide leach. For improvedrecovery, a sulphating roast as a preliminary process could improve gold recoveries by approximately20% and also allow cobalt to be leached with approximately 70% extraction rates achieved.
Although testwork conducted was overall successful in achieving the majority of objectives, there still ex-ists a number of opportunities to improve results and better gain certainty in metal recoveries and processingconditions. This is expected to include for:
1. Saprolite Gold ore,to further investigate of cyanide leaching to establish greater certainty in en-gineering design parameters. This may include,ClL testing with increased gold loading to carbonand optimised CIP triple contact tests. Following, pilot testwork including elution processing andelectrowinning may provide greater indication of expected plant performance.
2. Native Copper ore, confirming the copper recovery process that may include some vendor testwork
optimisation, and potentially further bulk open circuit or bench locked cycle testing.Once copperrecovery is confirmed with limited excess copper reporting to tailings, cyanide (CIL) leaching is requiredto be conducted similar to that conducted on the Saprolite Gold ore to establish carbon loadingcharacteristics and reagent consumptions.
3. Saprolite Attritioning, further (vendor) testwork be conducted to demonstrate quantity and hardness
of material requiring grinding. This may include the use of composites with a greater range of saprolitecontents.
4. Chalcocite (low-grade) recovery to test a further range of sample ensuring appropriate lithology andtransitional material is understood.Additionally, to ensure further testing is conducted directly on thepreferred gravity tailings as feed.
5. Pyrite Concentrate Production to investigate further the opportunities to improve copper and
pyrite concentrate separation through mineralogical diagnostics to establish limitations. Then furtherinvestigating the effect of varying process conditions e.g. alternative reagents and grind size.
6. Pyrite Concentrate Treatment to investigate the use of alternative process not tested in this pro-gram, particularly alternatives to roasting to oxidise the pyrite concentrates prior to leaching, or moreaggressive leach conditions.