Tungsten ore is an indispensable key mineral resource in modern industry. It is widely used in various industrial fields such as cemented carbide manufacturing, electronics industry, steel, aerospace, chemical industry, national defense, etc. In the mining and utilization industry chain of tungsten ore, ore dressing has always been the most critical link, which directly determines the quality and subsequent application value of tungsten ore products. However, when faced with tungsten ore with slime, the beneficiation work has encountered many difficult challenges. It not only contains various types of clay minerals, but also may be mixed with impurities such as organic matter. However, how to reasonably configure a tungsten beneficiation plant that can effectively and accurately handle tungsten ore with slime? Due to its complex composition, ordinary beneficiation processes are difficult to meet the processing needs, so we will specially configure a tungsten (with slime) ore beneficiation plant to achieve the extraction and recovery of high-purity concentrates.
characteristics Analysis of tungsten ore with slime
The main components of tungsten ore: wolframite and scheelite. Wolframite is brown-black to black, with metallic luster, weak magnetism, hardness 4-4.5, and density 7.1-7.5 g/cm³. Scheelite often appears as tetragonal bipyramidal crystals, mostly white, grayish white, sometimes with light yellow or light brown, non-magnetic, hardness 4.5-5, density 5.8-6.2 g/cm³.
The impact of tungsten ore with slime
Originally, tungsten ore has a certain hardness and density. In tungsten beneficiation plant, if slime is attached, the looseness of the ore decreases and becomes more compact, resulting in the equipment needing to overcome greater resistance in the early processing links such as crushing and grinding.
process design for contain slime tungsten beneficiation
1. Washing operation
Add a special washing link at the front end of the ore dressing process, use high-pressure water gun or strong water flow to wash the tungsten ore with slime, and minimize the interference of slime in the subsequent process. It can be equipped with vibrating screen, trommel scrubber, drum screen and other ore washing equipment, and screen at the same time during the washing process, so that the washed slime and impurities can be separated from the ore in time.
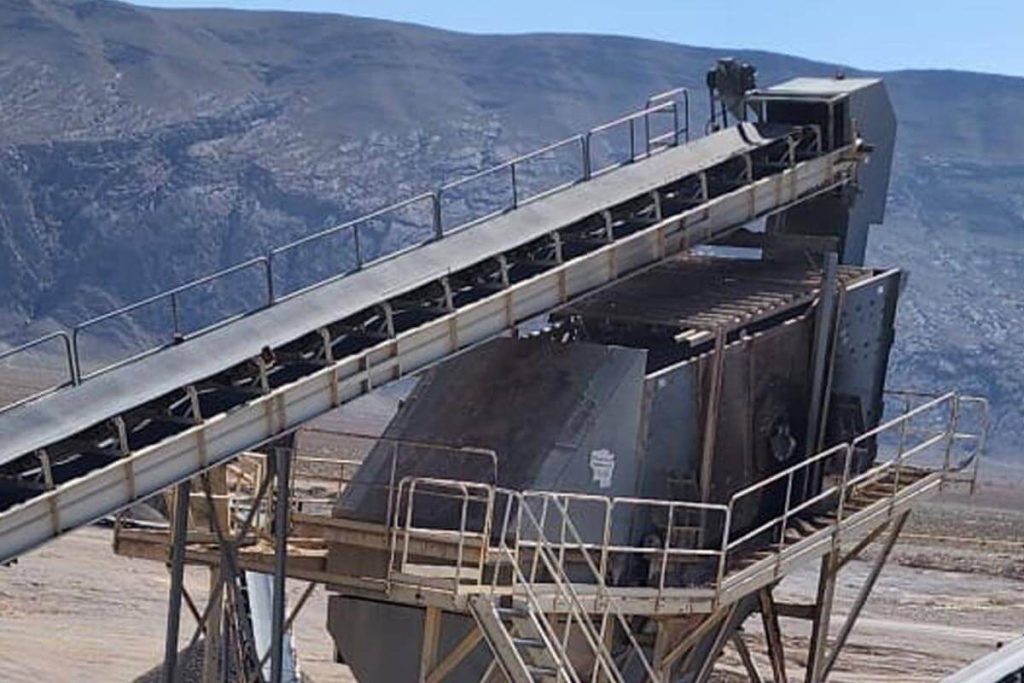
2. Pre-drying before crushing (depending on the situation):
If the slime content is high and the humidity is high, it is possible to consider moderate pre-drying of the ore before crushing. By natural drying or using special drying equipment, the humidity of the ore can be reduced, the slime can be dried and brittle, and the risk of equipment blockage caused by slime can be reduced.
3. Crushing process:
Jaw crusher is used for primary crushing, cone crusher or other crushing equipment is used for fine crushing, and the ore is gradually crushed into smaller pieces by extrusion crushing. In order to prevent slime from clogging in the crusher, a vibrating feeding device can be set to ensure uniform feeding, and a cleaning scraper can be installed on the inner wall of the crusher to regularly clean the adhered slime.
4. Grinding process
Depending on the properties of tungsten ore and product requirements, determine whether to use dry grinding or wet grinding. In view of the slime situation, wet grinding may be preferred, and water can be used to wash away some of the slime. Reasonably control the grinding concentration and time, determine the optimal parameters based on the ore characteristics and slime content, and ensure that the ore particles are fully dissociated. Usually, a ball mill and a spiral classifier are used in combination to achieve the best grinding effect.
5. Sorting process
According to the mineral composition and physical and chemical properties of tungsten ore, determine to use one or more combinations of gravity separation, flotation, magnetic separation and other separation methods. For wolframite separation, gravity separation is mainly used; for scheelite beneficiation, flotation is mainly used. According to the selected separation method, select the corresponding equipment, such as shaking table, spiral chute, jig concentrator (gravity separation); flotation machine (flotation process); magnetic separator (magnetic separation), etc.
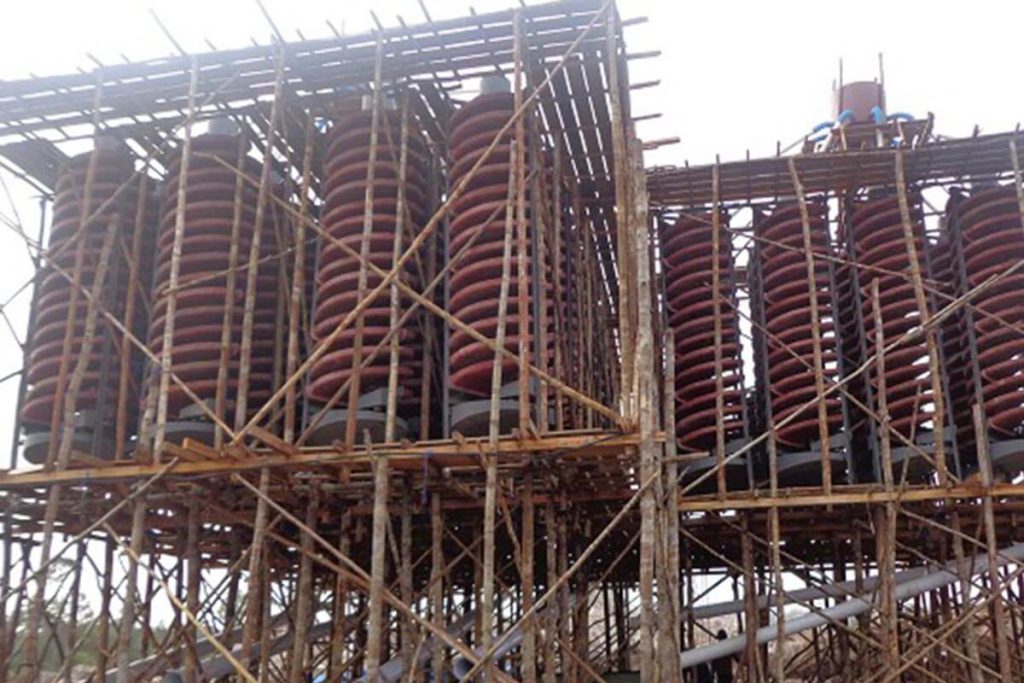

6. Dehydration and drying process
Plan the dehydration operations at different stages such as coarse dehydration and fine dehydration to gradually reduce the moisture content in tungsten concentrate. Choose appropriate dehydration equipment, such as thickener (coarse dehydration), filter (fine dehydration), etc.
Tungsten Beneficiation Plant
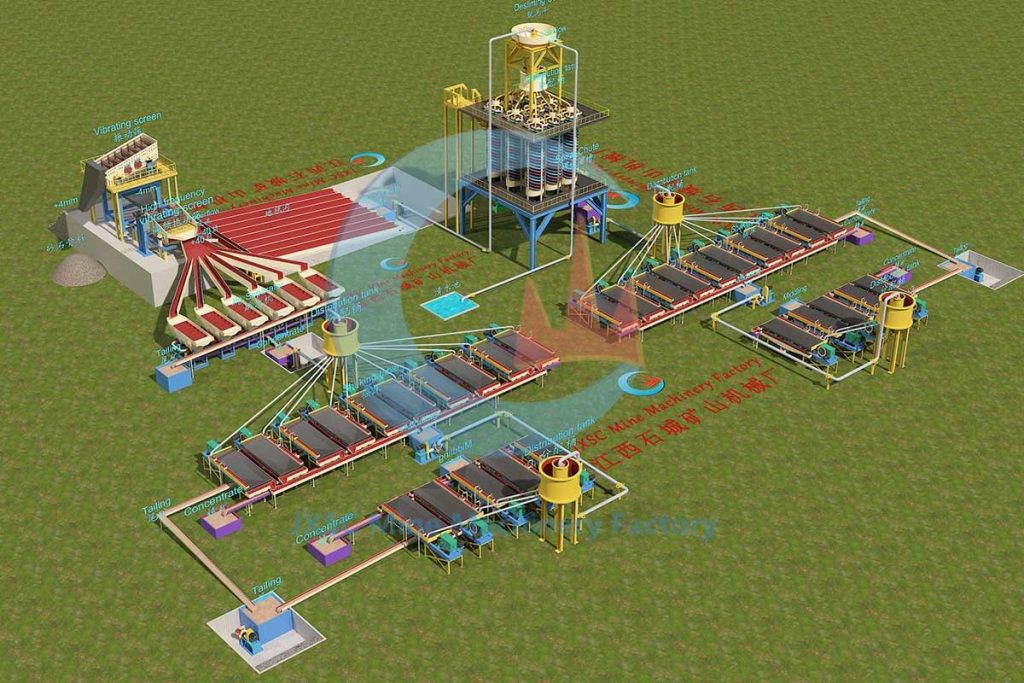
tungsten washing processing plant
This setup is a tungsten washing plant, main machine and process details as follows:
- Raw material will feed to the vibrating screen for sieving larger than 4mm waste sand and 0-4mm materials to the high-frequency vibrating screen.
- High frequency vibrating screen for sieving 0-40 mesh materials to the tailings blanket recycling machine, 40 mesh -4mm materials will to the jig separator.
- Jig separator for recovering the tungsten concentrate roughly. The shaking table for refining the concentrate from the jig separator, and the mid concentrate from the 1st stage shaking table will go to the 2nd stage shaking table for recovering again.
- Tailings blanket recycling machine for recovering the tungsten from the 0-40 mesh materials.
- The spiral chute is for refining the concentrate from the tailings blanket recycling machine.
- The shaking table for refining the concentrate from the spiral chute, and the mid-concentrate from the 1st stage shaking table will go to the 2nd stage shaking table for recovering again.
- All tailings from the jig separator, shaking table, tailings blanket recycling machine, and the spiral chute will flow to the tailing pool, before the spiral chute, the shaking table will have the distribution tank.
This tungsten washing plant is very suitable for raw materials and contains no sticky clay. If the raw ore contains much sticky clay, we recommend a trommel scrubber instead of a vibrating screen. The capacity for this washing plant can be customized as per request such as 10tph, 50tph, 100tph, etc.
How to configure a tungsten beneficiation plant that can effectively treat slime-containing tungsten ore? Usually, many factors need to be considered, such as tungsten ore characteristics, scientific process planning, and reasonable equipment configuration. Only by comprehensively considering and carefully planning each link can efficient and accurate ore dressing operations be achieved and high-quality tungsten ore products be produced. JXSC supports customized ore beneficiation solutions and equipment, contact us for more details!