Magnetic separator is the basic tool used by mineral processing plants to separate ferrous and non-ferrous metals from extracted ore, ensuring high-quality final products. Its works by attracting magnetic particles such as iron, steel and nickel, and then using powerful magnets or electromagnets to separate these particles from other materials. As technology advances, magnetic separators are more efficient and versatile than ever, making them an invaluable asset to any concentrator. Ultimately we choose a magnetic separator based on your specific needs.
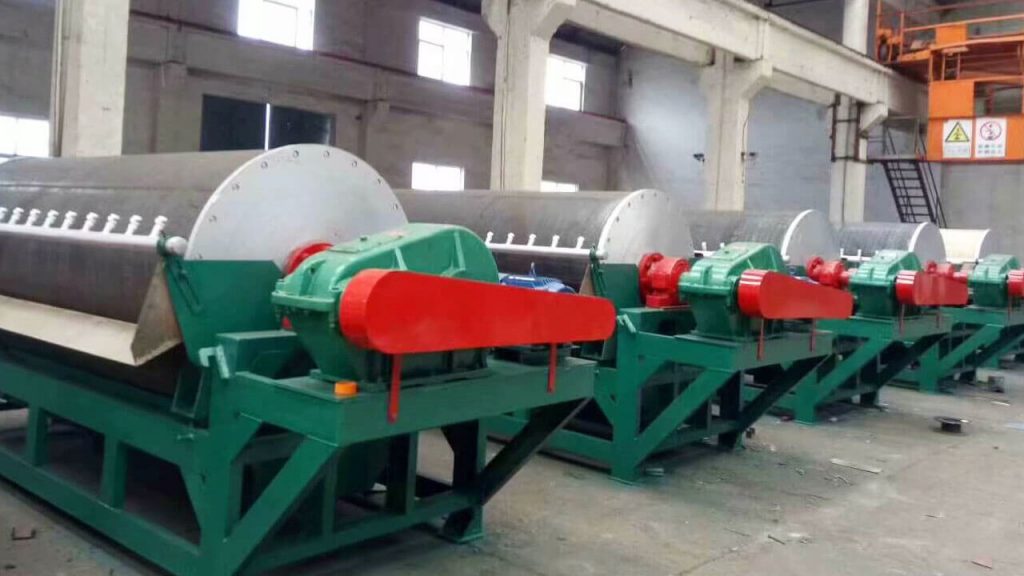
Type of magnetic separator
1. Wet drum permanent magnet magnetic separator
It is suitable for separating strong magnetic minerals and the pulp concentration before filtration or regrinding.
- For roughing separation, weak magnetic separation operations before strong magnetic separators, and enrichment operations, generally a large-diameter magnetic separator with a higher magnetic induction intensity should be selected.
- The concentrate separation should adopt a magnetic separator with a low magnetic induction intensity.
The enhanced mutual adsorption between particles, including magnetic and non-magnetic substances is serious for fine-grained or fine-grained minerals. If the dry method is used for sorting, it is difficult to remove the magnetic substances, so the wet method is generally required. In the case of wet sorting, auxiliary methods such as rinsing and pulsation can usually be added to destroy the inclusions between magnetic and non-magnetic substances. Effectively improve the probability of magnetic objects being captured by the magnetic field.
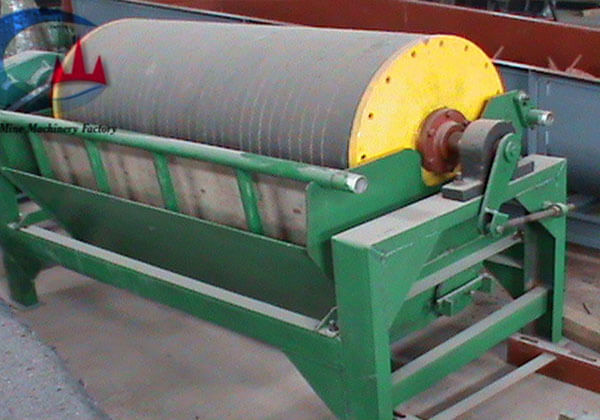
2. Three-disc Magnetic Separator
It is a very important beneficiation equipment for the separation of weak magnetic minerals and rare metal ores. There are two types of three-disk belt magnetic separators. The dry-type three-disk strong magnetic separator is suitable for the separation of various magnetic mineral mixed ores. According to the magnetic difference of minerals, the magnetic field of different strengths can be formed by adjusting the excitation current of the disks at all levels to separate the minerals. It is also possible to adjust the induction distance between the disks at all levels and the mineral particles to be selected to obtain different magnetic field induction intensities to achieve one-time separation of various minerals.
This equipment is widely used in dry separation of ilmenite, monazite, tungsten-tin ore and other magnetic and non-magnetic minerals. It can separate strong magnetic, weak magnetic, non-magnetic and other minerals at one time. It can be adapted to dry operation in water-deficient mining areas.
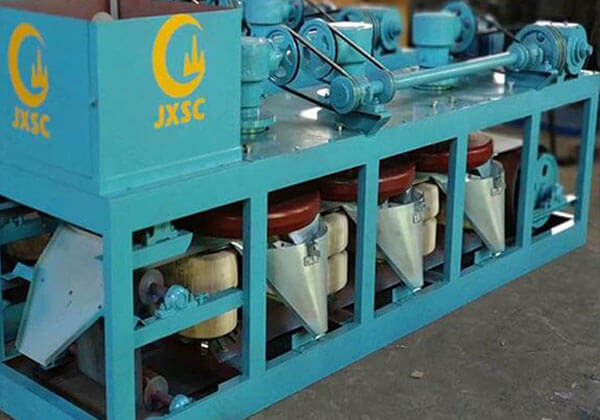
3. High Intensity Magnetic Separator
The strong magnetic separator is an upgraded product of the dry iron remover developed on the basis of the original dry iron remover by improving the magnetic field strength and the arrangement of the magnetic blocks. Its magnetic system is all made of high-performance rare earth NdFeB materials and high-quality ferrite materials, with high magnetic field strength (up to 12000 Gauss). For each group of magnetic media, the direction of flushing the concentrate is opposite to the direction of ore feeding, and the coarse particles can be washed out without passing through the stack of magnetic media, thus effectively preventing the blockage of the magnetic media. The double high advantages of high concentrate grade and recovery rate have been realized.
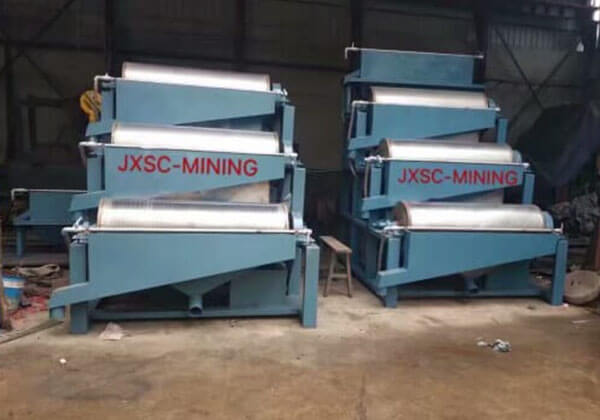
4. Plate magnetic separator
The plate area is large, and the material flows evenly in the entire magnetic field area. The contact area between the material and the magnetic field and the number of rolls of the material in the magnetic field are increased. High-performance NdFeB magnetic material, unique design of magnetic circuit, high surface magnetic field can reach 15000GS. Adjusting the slope according to the material condition can achieve a good iron removal effect.
It is mainly used for iron purification of quartz, feldspar, nepheline ore and kaolin. It can also separate red ore (hematite, limonite, siderite, etc.), ilmenite, wolframite and other weak magnetic metal ores.
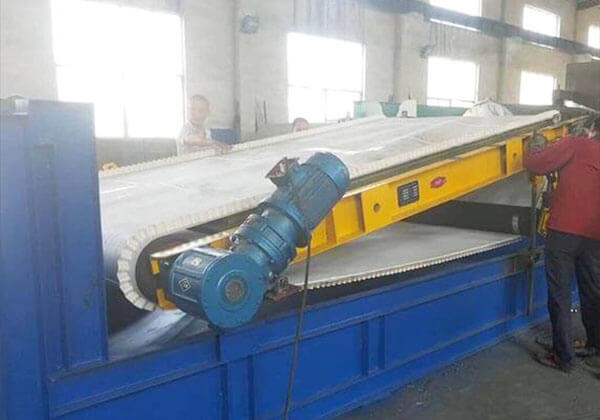
Magnetic separator function
1. Mineral sorting – improving quality
It is mainly used for magnetite, limonite, ilmenite, etc mineral processing plants., and can separate elemental minerals from gangue and sediment. Improve the quality of minerals and provide basic raw materials for industrial and mining enterprises.
2. Media recovery – energy saving and environmental protection
Mainly used for dense medium coal washing, sewage treatment, etc. The magnetic separator can recycle the magnetic medium powder used in the production process. Greatly improve production efficiency, reduce floor space, and reduce labor costs.
3. Mineral purification – high utilization rate
Commonly used in quartz sand, zircon sand, potassium feldspar, albite and other industries. After the iron impurities in the minerals are sorted by a magnetic separator, the purity of the minerals can be improved, which is an indispensable production link.
Magnetic separator is an important equipment to improve the efficiency of beneficiation by effectively removing unwanted metals and pollutants from raw materials. Businesses can achieve higher quality end products while operating at peak efficiency. With its ability to separate impurities and increase mineral purity, incorporating a magnetic separator into your beneficiation operation is a wise investment that will yield long-term benefits. JXSC provides equipment suitable for a variety of concentrator applications, with its solid structure, magnetic separators that can be customized for various production volumes. The use of our mineral processing equipment in your mineral beneficiation plant can greatly improve efficiency and reduce costs.