The spiral chute combines the advantages of a spiral concentrator, shaking table, and centrifugal concentrator. It is an essential tool for mineral processing and recycling. It can effectively extract different minerals based on specific gravity. The versatility and adaptability of spiral chutes make them suitable for various mineral processing applications, resulting in increased recovery and reduced waste. It can result in significant cost savings for mining operations while minimizing environmental impact.
Additionally, adjusting the chute angle and speed allows for fine-tuning the separation process based on the characteristics of the processed minerals. This level of control improves overall recovery and the quality of extracted minerals to meet stringent market demands. Essentially, utilizing spiral chutes revolutionizes mineral processing by optimizing recovery rates and sustainably streamlining operations.
一、Introduction to spiral chute
Spiral chute, also known as a spiral separator, is commonly used in iron ore, ilmenite, chromite, pyrite, zircon, rutile, monazite, tungsten ore, chrome, niobium ore, tin and other non-ferrous metals, rare metals and non-ferrous metals, and metal ore separation solutions. In particular, the effect of placer mining on seashores, riversides, sandy beaches, and creek channels is more significant. The spiral chute mainly uses the gravity, inertial centrifugal force, water flow force and groove surface friction force experienced by light and heavy mineral particles in the downward flow along the spiral slope to sort.
working principle
It mainly comprises six parts: ore distributor, ore feeding trough, spiral trough, ore cutting trough, ore receiving bucket, and trough bracket. Stand the spiral chute up, calibrate the vertical line, and fix it in place with an iron frame or wood. The ore is sent to the two feeding ports on the top of the spiral by a sand pump, and supplementary water is added to adjust the concentration of the ore paddle. The ore paddle naturally swirls from high to downwards, generating an inertial centrifugal force in the rotating slope flow rate. Based on the difference in specific gravity, particle size and shape of the ore, the ore and sand are separated by the gravity and centrifugal force of the swirling flow. The concentrate flows into the concentrate hopper and is connected through a pipeline; the tailings flow into the tailings hopper and are connected to the sand tank through a pipeline. Then, a sand pump is drained away, completing the entire mineral processing process.
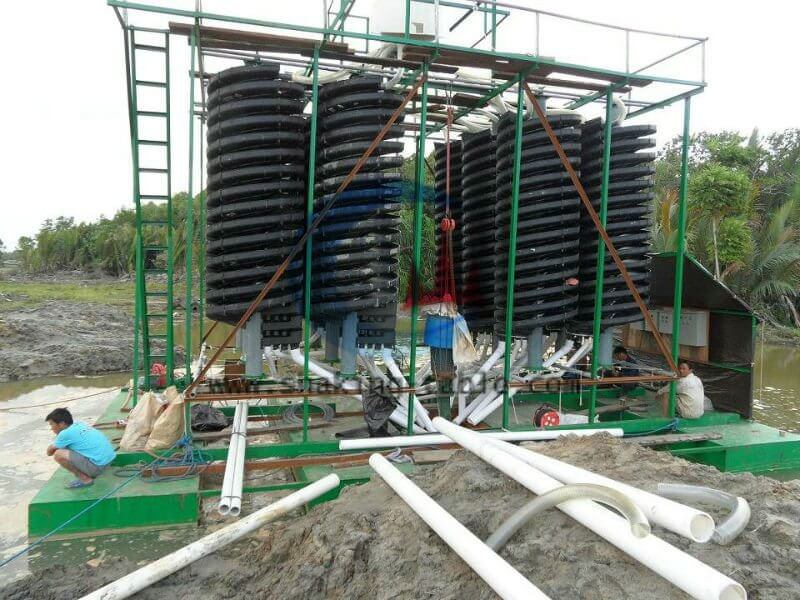
二、Application of spiral chute in mineral processing plant
1. Spiral chutes application in Gold Processing
Spiral chutes effectively separate valuable gold ore from other heavy minerals. Its unique spiral design allows for a smooth and controlled material descent, ensuring high recovery rates and minimal waste. This innovative device is particularly effective at handling fine-grained materials, making it an indispensable tool for the gold processing industry. Its ability to handle a wide range of particle sizes provides flexibility for processing various types of gold ore. Notably, the gentle handling of the material by the spiral chute minimizes the abrasion of the ore particles, maintaining their integrity throughout the separation process. Additionally, the efficient gravity separation provided by the spiral chute reduces the need for complex chemical processes, promoting environmentally friendly gold processing practices. By using gravity to separate gold from gangue minerals, the equipment contributes to sustainable and responsible mining operations.
2. Spiral chutes application in manganese Processing
The spiral chute plays a vital role in the separation and concentration of manganese ore. Using gravity and centrifugal force, the spiral chute allows the manganese particles to descend slowly, minimizing breakage and ensuring a high-quality end product. The continuous and automated nature of the equipment allows for a steady flow of material, increasing productivity and reducing downtime. In addition, the customizable configuration of the spiral chute enables precise control of the size and grade of separated manganese ore, thereby increasing overall productivity and output. Smooth flow and controlled descent within the chute minimize turbulence and agitation, which are critical to maintaining the integrity of brittle or irregularly shaped manganese particles.
2. Spiral chutes application in Chrome Processing
Spiral chutes provide an efficient and reliable method of separating valuable chromite ore from waste. These devices use gravity and centrifugal force to separate heavier chromite particles from lighter gangue minerals. In chrome processing, spiral chutes are particularly suitable for handling fine particles, making them ideal for processing chromite ore, which is often difficult to separate. Its gentle movement and precise design prevent excessive crushing or damage of valuable ore, ensuring higher recovery rates and minimizing product loss. Additionally, spiral chutes help reduce chromium processing plants’ energy consumption and overall operating costs by effectively concentrating chromite ore prior to further processing steps. This unique perspective highlights what makes spiral chutes a cost-effective solution for chrome processing plants looking to optimize operations.
2. Spiral chutes application in copper Processing
Applying spiral chutes in copper processing plants has revolutionized how raw materials are separated and processed. Using gravity and centrifugal force, the spiral chute effectively separates the copper ore from the gangue minerals, resulting in an efficient and cost-effective extraction process. In copper processing, spiral chutes can handle various particle sizes without the need for adjustments or additional equipment. The consistent material flow through these chutes makes the production process more stable. It is a practical and reliable option for copper processing plants, contributing to overall operational stability and cost savings. Gravity beneficiation improves the overall efficiency of a copper processing plant and reduces environmental impact by minimizing the use of chemicals and energy.
Advantages of spiral chute
- The spiral separator can efficiently and smoothly transfer minerals from one layer to another, reducing the risk of damage or loss during processing.
- The operation process is simple, helping minimize downtime, achieving continuous production and retaining valuable resources for maximum productivity.
- The gentle descent function it produces ensures that fragile minerals maintain their integrity throughout transportation, thereby maintaining product quality and market value.
- They can effectively process various types of minerals with different properties, increasing the versatility of mineral processing operations and helping to improve overall operational efficiency.
- The spiral chute can make materials flow continuously and smoothly without frequent manual adjustment or maintenance.
Mineral processing efficiency is a key factor in the mining industry, and by harnessing gravity, spiral chutes can quickly and accurately separate ore particles, thereby increasing purity and overall production. Its versatility and allows for custom configurations to meet specific processing requirements, making it an adaptable solution for a variety of mineral processing operations around the world. Low maintenance requirements and long-term durability make it a sustainable choice for mineral processing operations. Consider using JXSC spiral chutes in today’s mineral processing plant to maximize efficiency and reduce costs while increasing overall productivity.