The copper ore flotation method can be divided into forward flotation and reverse flotation according to the separation of valuable components: discharging useless minerals (gangue minerals) in the slurry as tailings are called forward flotation. Otherwise, it is called anti-flotation. Copper is one of the important non-ferrous metals. In the production process, the flotation method is often used for separation. According to the different oxidation rates of ores, they can be divided into copper sulfide, copper oxide, and mixed copper ores. The flotation methods of various types of copper ores will be different in the specific application process. It mainly involves multiple stages to separate the valuable copper minerals from the gangue material.
1. Three types of copper ore flotation
- For sulfide ores, the most commonly used flotation method involves adding collectors to the ore-water mixture to enhance the hydrophobicity of the copper sulfide particles. These hydrophobic particles can be separated from the gangue minerals and collected as a foam concentrate by attaching them to the bubbles.
- Due to the mineralogical properties of copper oxide ores, they usually require different flotation methods. In this case, acid leaching is often used before flotation to dissolve the oxide minerals and expose the copper sulfide surface for efficient recovery.
- For these complex mixed copper ores, a combination of different collectors and modifiers may be required to recover oxide and sulfide minerals while minimizing unwanted interactions selectively.
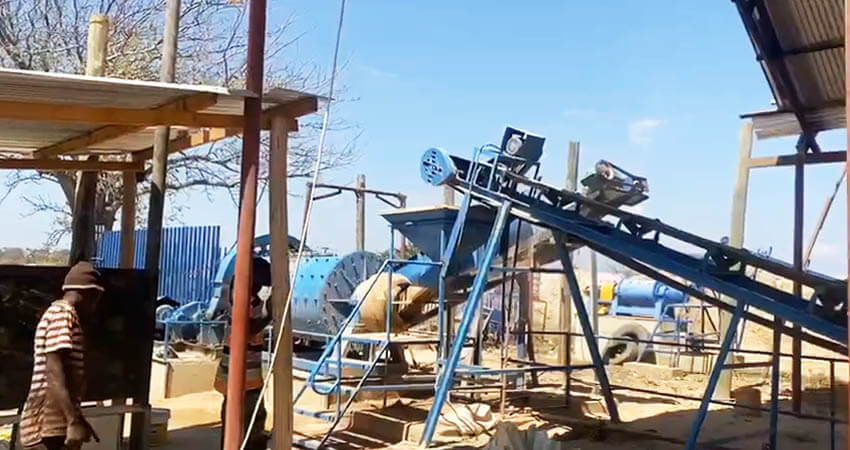
二. Copper Ore Flotation methods
(1) Copper sulfide ore flotation
Copper sulfide ore is a copper ore with a meager oxidation rate. Almost all copper sulfide ores have iron-containing sulfides. In a sense, it is essentially the separation of copper sulfide and iron sulfide. When the content of iron sulfide minerals in copper ore is very high, the priority flotation process should be used; conversely, mixed copper and sulfur flotation and then separation should be given priority, but the priority flotation process is not excluded.
The process involves several basic steps, including crushing and grinding the ore to a fine size, then introducing chemicals such as collectors and frothers to create the right environment to separate the copper minerals from the priceless material. Air or nitrogen also helps create bubbles within the flotation cell to which copper sulfide particles attach and are subsequently recycled as concentrate.
Since the copper-sulfur raw ore grade has declined, the copper-sulfur recovery rate and the concentrate grade have increased to varying degrees. Using the JXSC copper sulfide ore flotation process, the copper concentrate grade is increased by 3.42%, the sulfur is increased by 2.95%, the copper recovery rate is increased by 2.88%, and the sulfur recovery rate is increased by 28.83%.
(2) Copper oxide ore flotation
With the increasing depletion of easy-to-smelt copper sulfide ore resources, using copper oxide ore resources has received increasing attention. The minerals in oxide copper ore are complex, and improving the copper grade through mineral processing and enrichment is difficult. There are inevitably oxidized ore zones on the surface of most mineral deposits. Due to long-term weathering, the ores are loose and finely crushed with high mud content. This type of ore is enriched using conventional beneficiation processes, with low metal recovery rates and poor economic benefits.
Flotation is the main method for processing copper oxide ores. Flotation mainly includes direct flotation and sulfide flotation. The direct flotation method is the earliest applied and is suitable for copper oxide ores with simple mineral composition and uncomplicated properties. The focus of its research is on the search for flotation reagents. The sulfide flotation method refers to adding a sulfide agent to sulfide copper oxide minerals and using ordinary copper sulfide ore flotation agents for flotation.
(3). Mixed copper ore flotation method
Mixed flotation method: When the ore contains two or more valuable minerals and is beneficiated by flotation, the various useful minerals are selected into a mixed concentrate (then the different valuable minerals are separated). The process begins by grinding the ore into a fine powder and then mixed with water and chemicals such as collectors and frothers. The mixture then goes through a series of flotation stages in which air bubbles through, causing the copper to attach to the bubbles and rise to the surface while leaving behind non-copper minerals.
This process is more advantageous for copper-sulfur ores where the raw ore contains low sulfur and the copper minerals easily float. Copper and sulfur minerals are mixed and floated in a weakly alkaline slurry. The mixed concentrate is added with lime to separate copper and sulfur in a highly alkaline slurry.
Our flotation process adopts an automation and control system that fully guarantees the best operating results of the mineral processing production line by monitoring key parameters in real-time and promoting adjustments for optimal performance. Implementing these technologies improves operational efficiency, helps utilize energy better, and reduces environmental impact. Continuing advances in JXSC’s flotation methods for various types of copper ores highlight the multiple factors in optimizing the mineral beneficiation process to increase yields and improve environmental sustainability.