A jigger (jigging machine) is a piece of equipment that implements the gravity separation process. The process in which the material is sorted according to density differences, mainly in a vertically rising and falling stream of variable speed media. The difference in size and shape of the material has an effect on the result of the separation. The medium used in jigging can be either water or air. When water is used as the sorting medium, it is called hydraulic jigging; when air is used as the sorting medium, it is called wind jigging.
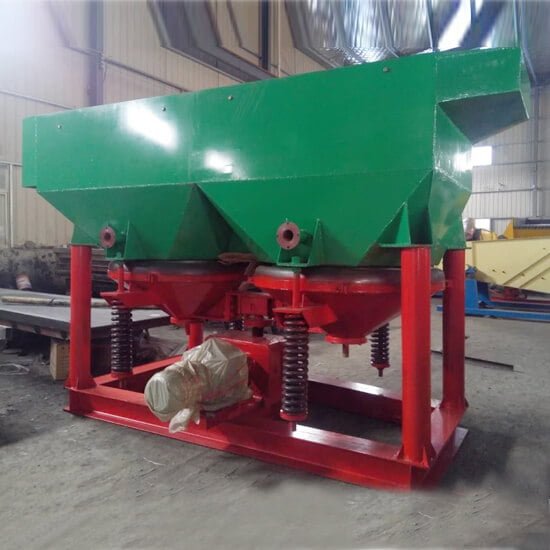
Working Principle
Jigger working principle: Jigger belongs to the deep tank type re-election equipment. All jigging machines have a jigging chamber. The jigging chamber is equipped with a jigging mechanism, a water movement mechanism and a product discharge mechanism. The screen inside the jigging chamber is made of perforated steel plates, woven iron screens or grates. The water flowing through the screen into the jigging chamber should make the bed rise to a small height and be slightly loose, with the denser particles entering the bottom layer due to the local pressure and greater settling speed, and the less dense particles moving to the upper layer. When the water flow down, the density of fine particles can also enter the lower layer through the gradually tight bed gap, supplemented by the density of the stratification of the drum water movement of the mechanism in the early years of the piston, the piston chamber is located in the side of the jigging chamber, the lower connected, driven by the eccentric linkage mechanism piston up and down movement.
Applications
The jigger is a fixed screen type, suitable for sorting metal ores, such as alluvial ores containing tungsten and gold, selected tin ores, etc. It can be used for both fine grain and coarse materials, with a maximum feed size of 6-8 mm, but in individual cases of sorting alluvial ores, the maximum size is 12 mm.
Classification
According to the different equipment structure and water flow movement, it can be roughly divided into the following categories: piston jigger, diaphragm jigger, air pulsation jigger, and dynamic screen jigger.
Selection Guide
Jig machine selection steps: first and jig machine manufacturer telephone contact, by asking some technical questions, you can roughly understand whether this manufacturer is professional, the next step is to carry out mineral processing tests, this step is critical, you bring ore to the jig machine manufacturer, the general situation is 30-40 kg of raw ore, the regular manufacturers have small jig machine available for free test, the test is not as good as the actual production indicators, but also The test is not as good as the actual production indicators, but also from the side to grasp the ore beneficiation indicators, and jigger manufacturer’s technology is perfect, if the test link can reach the ideal indicators, then this manufacturer has a certain strength, and then is to order equipment links, look at the quality of jigger equipment, external viewing jigger working principle is reasonable, and according to your site conditions for improvement, of course, the important issue is the price, the price is also based on the above The price is also based on the above cases of negotiation, the final order products, jigger manufacturers have professional technical staff to install and commission until you produce qualified products.
Maintenance
Maintenance of the jigger in the production process.
1, the correct choice of lubricant. When the equipment gears rotate with lag or heat, add lubricant to the equipment in time to reduce the wear and tear of the components.
2, pay attention to the impact of the environment on the equipment, such as rain, sand, impurities, etc., to prevent the occurrence of rusting and aging of equipment components.
3, for the equipment five days a maintenance, ten days a maintenance, three months to repair or replace some serious wear parts, such as bearings.
(1) Check whether the diaphragm and screen of the jigger are broken, and replace them in time if they are broken.
(2) Check whether the screen plate is pressed against the screen frame, if it is loose, press it in time.
(3) Check the wear of the eccentric linkage bearing, and replace the bearing in time if it is worn out too much.
(4) Check whether the water pipe under the screen is intact.
(5) Check whether the motor has abnormal sound, whether it is hot, if it is, timely overhaul.
Cautions
Jigger commissioning precautions.
1, the adjustment of the bed thickness needs to be determined according to the size of the selected minerals and specific gravity difference and other factors, suitable, after the bed is too low processing capacity and recovery rate, the bed is too thin, the concentrate grade is not high.
2, the role of water under the screen is to weaken the inhalation strength of the falling water flow to improve the quality of the concentrate, jigger and can enhance the speed of the rising water flow to enhance the looseness of the bed, which is conducive to mineral particles, especially coarse mineral particles by specific gravity stratification. The amount of make-up water varies with the feed load, particle size of the feed material, the specific gravity separation of the minerals, the thickness of the material layer or the looseness of the bed. Generally speaking, the feed material load, coarse particle size, mineral specific gravity, material layer thickness or bed is too tight, the amount of make-up water is large, and vice versa, the amount of make-up water is small.
3, jigger in mineral processing requires a certain medium as an artificial bed, the selection of media and particle size configuration are required to determine the actual situation, the nature of the media selected for different mineral jigging beneficiation are not the same. Media selection and configuration is also one of the main factors affecting mineral processing plant.
Troubleshooting
Jigger machine common fault analysis.
1, jig machine screen plate failure
(1) screen plate damage: screen plate due to the impact of coal and water and heavy products along the screen surface and wear, resulting in screen plate rupture or perforation. In this case, you should immediately stop to repair or replace the screen plate.
(2) sieve hole blockage sieve plate on the eye blockage is the size of the selected material between the aperture of the material more, which in the selection of sieve aperture size, should pay attention to. Sieve hole blockage is not serious, can wait for normal parking, the use of large wind and small water drumming rinse, or drive in the bed set some thin, with iron pipe or iron bar pounding a pounding sieve plate; if blockage is serious, should immediately stop, clean up the sieve plate, otherwise it will affect the sorting effect.
(3) sieve plate pressure side off (guard plate off) or screw loose situation is not serious, can wait for normal parking to clean up the bed, give treatment; if the situation is serious, should immediately stop to deal with.
(4) screen plate inclination angle change: daily cleaning screen plate and processing screen hole blockage, due to improper way and method will cause sinking or deformation of the screen frame, as well as the sinking or deformation caused by the impact of the screen plate by coal and water transfer to the screen frame. This situation is generally not easy to detect, need to regularly check, if the situation is serious, need to adjust.
2、Failure of air valve
(1) air valve exhaust port spraying water
The reason may be the wind pressure is too high or the bed is too thick, sieve plate orifice blockage and so on to find the cause of this timely treatment.
(2) air valve stroke is not enough
The reason may be improper adjustment of CNC, wind pressure is not enough, bad air valve, etc., to find the cause of this timely processing, or affect the sorting effect.
(3) the valve action and CNC is not coordinated
The reason may be a failure of the solenoid valve, or improper wiring of the circuit. This requires timely processing.
3、Float failure (float does not move)
A common fault is the buoy wear leakage, or the mechanical part of the buoy is jammed by debris. When the bed “too dead” will also appear this situation. This will need to find the cause of “the right remedy”.
4、Solenoid valve failure
(1) electromagnetic block after the power is not sucking sound cause: poor wiring contact or coil disconnection. Need to be wired correctly, replace the coil.
(2) electromagnetic block humming sound is: moving iron pistil, static iron pistil between the debris; moving iron pistil under poor sealing; voltage is lower than the allowable value. In this case, you need to clean up the iron pistil; repair or replace the gasket; adjust the voltage.
(3) electromagnet, bleed hole air leakage is too large cause: dynamic iron pistil seal or on the gasket damage, then need to replace the gasket.
(4) commutation does not work or exhaust leakage is: air source, air pressure is lower than the rated value; orifice blockage; cylinder sealing ring bad. Treatment: check whether the air source pipeline leakage; unclog the exhaust hole to replace the seal ring; check the cylinder to replace the seal ring.
5、Discharge fault investigation
The main reason is that the size of the raw coal is over the upper limit; it may also be the iron debris in the raw coal. When the discharge port is stuck, the vertical gate should be closed small to prevent running coal, and manipulate the actuator to assist in discharging, and then turn to normal work after the fault is removed. When the gangue is serious, it should be stopped immediately to remove; if the automatic discharging device is damaged due to the gangue, it should be repaired immediately and can be driven only after normal. In addition, the discharge hopper often has the phenomenon of being pressed, which is mainly due to improper operation of emissions too large or bed emptying is not found in time.
Of course, there are also reasons due to the equipment, such as: the bucket is too loose, the chain plate up, the square wheel is severely worn and so on being stuck caused by the pressure of the bucket, the bucket fell off the road, the pin was hit and so on.