Common iron ore types are magnetite, hematite, limonite and siderite. Among them, hematite is a weakly magnetic iron ore with uneven particle size and high fine particle content. Hematite is a mineral form that contains iron oxide. It is one of nature’s most abundant and widely distributed iron-bearing minerals. Hematite has become an important raw material for steelmaking due to its high iron content. However, the beneficiation process of hematite requires advanced technology and expertise. This article will outline four hematite beneficiation processes including magnetic separation, flotation, gravity separation and roasting-magnetic separation. The purpose is to help everyone understand how to efficiently and effectively extract valuable minerals from hematite. According to the characteristics of the processed hematite, JXSC supports customized hematite beneficiation plant to improve the recovery efficiency of minerals.
Hematite info
Hematite(iron oxide ore) is one of the most abundant minerals on Earth and an important source of iron. It is known for its distinctive reddish-brown color and high iron content. Hematite beneficiation is the process of extracting iron from hematite ore by removing its impurities. Hematite is an iron oxide mineral common throughout the world. It is abundant in nature and has been used for thousands of years as a pigment, jewelry, and even as a healing stone. However, hematite is also used for industrial purposes such as steel production and manufacturing, and plays an important role in our daily lives. To extract iron from hematite, it needs to go through a process called beneficiation.
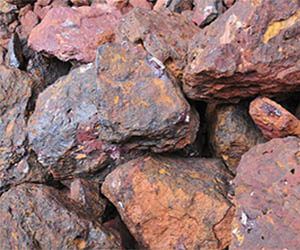
Hematite is widely distributed and involves various minerals, so the beneficiation method is not single. There are mainly flotation, magnetic separation, gravity separation and roasting magnetic separation.
Beneficiation method
1. Flotation Separation
The flotation method is mainly used to separate fine-grained and particulate weak magnetic hematite ore, including positive flotation (positive flotation with anionic collectors) and reverse flotation (reverse flotation with cationic collectors). Commonly used collectors include animal and vegetable fatty acids (soap), oxidized paraffin soap, crude tar oil, chlorinated acid, oxidized kerosene, sodium petroleum sulfonate, corn starch, etc.
- Positive flotation: Hematite positive flotation is a method of using anionic collectors to float iron minerals from raw ore. The flotation method is simple in medicine and low in processing cost, and is especially suitable for single hematite ore. However, it takes several selections to obtain qualified hematite concentrate, and the foam is easy to stick, making the product difficult to concentrate and filter.
- Reverse flotation: Hematite reverse flotation is a method of using anionic or cationic collectors to float gangue minerals from raw ore. The reverse flotation of anionic collectors is mostly used when the pH value is 8-9. It is used to treat minerals containing quartz gangue. After activation by calcium ions, reverse flotation is carried out with fatty acid collectors to obtain hematite concentrate. Cationic collector reverse flotation, the flotation agent used at this time is amine collector, which is suitable for flotation of quartz gangue. The amine collector is ether amine as the first choice, followed by aliphatic amine. The inhibitor of iron ore adopts water glass, tannin and sodium lignosulfonate, and the inhibitory effect is the best when the pH value is 8-9.
From the ore properties of hematite itself, reverse flotation has more advantages than positive flotation. Because the object collected by the reverse flotation process is gangue, and the object collected by the positive flotation process is iron minerals. Therefore, it is difficult to obtain high-quality hematite concentrate for minerals with serious inclusion of gangue minerals.
2. Magnetic Separation
The weak magnetic-strong magnetic separation method mostly processes magnetite-hematite mixed ore. Strong magnetic roughing and sweeping are carried out after the weak magnetic separation tailings are concentrated. Due to the strong magnetic minerals in a small amount of magnetite in the ore, it is easy to cause the blockage of the high magnetic field magnetic separator. Therefore, when the strong magnetic separation process is adopted, the weak magnetic separation operation is usually added before the strong magnetic separation operation to remove or separate the ore. Strong magnetic minerals.
The beneficiation mainly adopts strong magnetic separation process. The magnetic field for magnetic separation must be above 10,000 Gauss, which can be slightly reduced in dry magnetic separation operation. Some earthy hematites and fine grinding operations may require stronger magnetic fields.
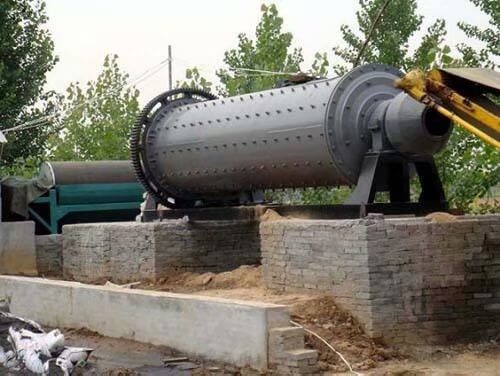
3. Gravity Separation
There are two main types of hematite gravity separation methods: coarse-grain gravity separation and fine-grain gravity separation:
- Coarse-grain gravity separation:the geological grade of the deposit is high (about 50%), but the ore body is thin or there are many interlayers, and the waste rock is mixed in during mining to deplete the ore. For this type of ore, only crushing and no grinding can be used. In the case of coarse particle size, the coarse tailings are discarded through the gravity separation process to restore the geological grade.
- Fine-grain gravity separation: this method is mostly used to treat hematite with fine embedded particle size and high magnetic content. After crushing, the ore is ground to achieve monomer separation of the minerals, and then the fine-grained high-grade concentrate is obtained through the gravity separation process.
However, due to the low grade of strong magnetic separation concentrate of most weak magnetic iron ores, and the low unit processing capacity of gravity separation process, the combined process of strong magnetic separation and gravity separation is often used. That is, the strong magnetic separation process is used to discard a large number of unqualified tailings, and then the gravity separation process is used to further process the strong magnetic concentrate to improve the concentrate grade. The gravity separation of hematite mainly includes jig beneficiation of coarse-grained hematite, centrifugal concentrator beneficiation of fine-grained hematite, and spiral beneficiation and shaking table for medium-grained hematite.
4. Roasting Magnetic Separation
When the mineral composition is complex and other beneficiation methods are difficult to obtain good separation indicators, the roasting magnetic separation process is often used to separate hematite. Mainly, the ore is magnetized and roasted to convert hematite or false hematite into magnetite, which is then separated by a weak magnetic field magnetic separator.
In order to further improve the grade of hematite concentrate, fine screen regrinding and re-selection (which can increase the concentrate grade to more than 65%), regrinding and reverse flotation (which can increase the concentrate grade to 66%) are often used in production. The process further processes the hematite concentrate obtained by magnetic separation.
Improving hematite recovery can significantly increase the profitability of mining operations. The four beneficiation methods outlined in this article—gravity separation, magnetic separation, flotation, and roasting-magnetic separation—offer valuable options for improving recovery. Factors such as ore grade, mineralogy, grain size and final product quality are considered. By choosing the right method, you can maximize efficiency, reduce costs, and ultimately be more successful in your mining operation. So, weighing your options and making an informed decision, JXSC will help you get the most out of your hematite beneficiation process.