Lithium is an important strategic resource material, the lightest metal element in nature, and has strong electrochemical activity. Widely used in emerging fields such as batteries, ceramics, glass, aluminum, lubricants, refrigerants, nuclear industry and optoelectronics. Therefore, lithium is known as “the new energy metal of the 21st century”, and lithium is also known as “an important element that drives the world forward”.
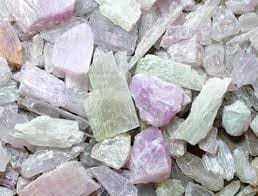
However, spodumene is a lithium-bearing aluminosilicate mineral, and lithium resources are mainly found in salt lakes and granitic pegmatite deposits. Among them, salt lake lithium resources account for 69% of global lithium reserves and 87% of global lithium reserves. It is prolific in granite pegmatite, and sometimes can form coarse crystals. Spodumene (Kunzite) is a high-quality mineral source for the industrial extraction of lithium. But the beautifully colored and crystal-clear Kunzite (emerald spodumene, purple spodumene) is used as a gemstone material. Usually gem-quality spodumene can weigh more than 1 carat, and it is not uncommon for spodumene to exceed 5 carats.
In order to separation high-quality spodumene minerals, it is necessary to use different separation methods for sorting. The separation methods of spodumene mainly include hand separation method, thermal cracking method, flotation method, magnetic separation method and gravity separation method.
1. Hand Separation method
In the 1950s and 1960s, manual beneficiation was one of the main beneficiation methods in the production of lithium concentrate and beryl concentrate at home and abroad. For example, in 1959, the hand-selected beryl concentrate in Xinjiang, Hunan and other provinces and regions in my country reached more than 2,800 tons. In 1962, the world’s beryl concentrate production was 7,400 tons, of which hand-selected concentrate accounted for 91%. This is mainly because most of the lithium ore comes from pegmatite deposits, and the main industrial minerals such as spodumene and beryl have large crystals and are easily selected. The manual selection method has low technical requirements, simple operation process, no need for special sites and equipment, and only needs to be carried out on a simple hand selection belt or a hand selection console, which can preliminarily separate the ore from the gangue and improve the ore. selection quality. At present, however, manual separation is still the main method of producing lithium concentrate in developing countries where labor is cheap.
2. flotation separation method
Spodumene is one of the main sources of lithium. It is produced in muscovite-type and lepidolite-type granite pegmatites, and is a metasomatic mineral in the process of pegmatite action. It often coexists with lepidolite, beryl, niobium-tantalite, tourmaline, muscovite, etc., and belongs to silicate minerals with these gangue minerals. In flotation separation, spodumene often adopts flotation method to purify lithium ore. Spodumene commonly used are positive flotation, reverse flotation and combined flotation, etc.
- Positive flotaion: The positive flotation of spodumene is completed in an alkaline medium, and an anionic collector is often used, and the ground minerals are added to a strong alkaline medium for high-concentration and strong stirring operations. The high-concentration pulp is treated with sodium hydroxide, and the pulp is removed under the action of alkali. After several times of scrubbing and desliming, fatty acid or soap collectors are added to directly float spodumene.
- Reverse flotation process: The spodumene reverse flotation process is also completed in an alkaline medium, mainly using lime, starch and dextrin as inhibitors, and terpineol oil as a foaming agent. Under the condition of alkaline medium (pH value of 10.5~11.0), dextrin can effectively inhibit spodumene, and then amine cationic collectors are used to collect silicate gangue minerals such as quartz, feldspar, and mica.
- Combined chemical-flotation process: suitable for use in salt lake lithium mines, from which lithium salts are extracted by this method. The method is to evaporate the brine on the drying field, so that the sodium salt and potassium salt are precipitated, and the concentration of lithium chloride is increased to about 6%. It is then sent to a factory where the soda process is used to convert the lithium chloride into a solid product lithium carbonate.
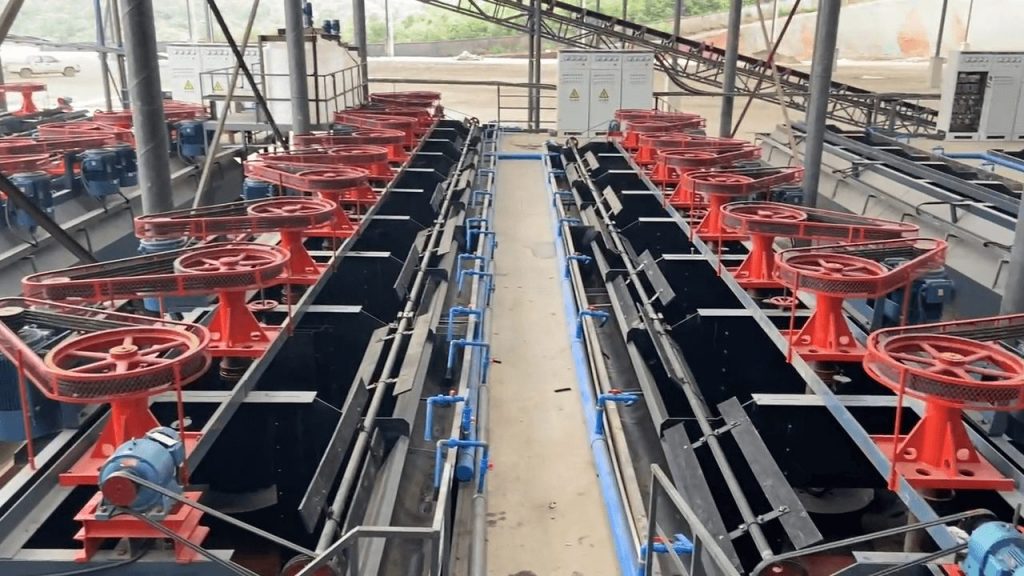
3. Magnetic separation method
It is often used to remove iron-containing impurities in lithium concentrates or to separate weakly magnetic lepidolite. In production practice, spodumene concentrates obtained by flotation are used. Sometimes there are many iron impurities, in order to reduce the content of iron impurities, the magnetic separation method can be used for treatment. The magnetic separation equipment is a permanent magnetic drum magnetic separator, a wet strong magnetic plate magnetic separator, and a vertical ring high gradient magnetic separator. The spodumene tailings are mainly composed of feldspar, and vertical ring high gradient magnetic separator and electromagnetic slurry magnetic separator can also be used for impurity removal to obtain feldspar products that meet the requirements for ceramic raw materials.
4. Dense medium beneficiation method
Because the density difference between spodumene and associated gangue minerals is not large, the usual gravity separation methods such as jigging, spiral beneficiation and shaking table are not suitable for the separation of spodumene ore. But heavy medium beneficiation or heavy liquid beneficiation is an effective method for spodumene beneficiation. For example, the mineral processing staff of the United States Bureau of Mines also used tetrabromoethane as the heavy liquid (density 2.9529 g/cm3) to carry out a continuous test of the heavy liquid cyclone separation of spodumene ore. Satisfactory results have been obtained, the feeding particle size is -35 mesh, containing 20% spodumene, the obtained concentrate contains 92~95% spodumene, the recovery rate is 86~89%, and the recovery rate of heavy liquid is 95% above. Years of practice show that as long as there is good protection, tetrabromoethane can be used on a large scale.
5. Thermal cracking method
It is a method of separating spodumene ore. The method is based on the fact that when natural spodumene is roasted at about 1100 °C, its crystals change from α-type to β-type, and at the same time, the volume expands and is easily broken into powder, so that spodumene and gangue can be obtained by selective grinding and screening. separation between minerals.
Two points must be paid attention to when applying the thermal cracking beneficiation method: ①Control the roasting temperature around 1100℃. When the temperature is too high, the mica present in the ore will sinter; when the temperature is too low, the transformation of spodumene from α to β is incomplete. ②The ore cannot contain a large amount of minerals that are easy to melt during roasting or other minerals with thermal cracking properties, otherwise the purpose of separating spodumene will not be achieved.
Which separating method is used to cooperate with each other to complete the selection of target minerals and make the product meet the requirements of sales grade, it needs to be selected according to the embedded characteristics of minerals, mineral composition and optionality. In the selection of spodumene, flotation separation is undoubtedly the most studied, the most mature, and the most utilized process. The optional test before ore dressing is very necessary. JXSC conducts ore analysis and beneficiation process design for the spodumene concentrator, with stable production indicators and good economic benefits.