With the continuous mining of iron, high-grade, easy-to-select ores are increasingly depleted, and more and more attention is paid to low-grade, high-impurity-containing, and difficult-to-smelt iron ore resources. Limonite is a common iron ore mineral that often contains high levels of phosphorus, which can compromise the quality of steel produced from it. Traditional beneficiation methods struggle to effectively remove phosphorus from limonite, resulting in substandard results during the steelmaking process. However, a new innovative approach has emerged specifically targeting phosphorus removal from limonite, with remarkable success.
This new method combines advanced technologies such as magnetic separation, gravity separation, flotation and leaching to target the removal of phosphorus in an efficient and environmentally friendly way. By selectively extracting phosphorus while leaving iron content unchanged, the beneficiation process ensures high-quality iron ore for steel production. The main purpose of beneficiation is to remove phosphorus and obtain high-grade limonite concentrate, in order to obtain high-grade limonite concentrate. Next, let’s learn about the phosphorus removal and beneficiation methods of limonite!
Characteristics of limonite ore
Limonite ore is a common iron ore found in sedimentary rocks and is known for its unique properties. One of the main characteristics of limonite is its brownish-yellow color, which sets it apart from other iron ores. Additionally, limonite has a high water content and is relatively soft compared to other minerals.
Another interesting property of limonite is its variable composition and structure. This change results in a different physical appearance, ranging from smooth and shiny to a dull, blocky texture. Additionally, limonite often forms nodules or nodules within a rock matrix, adding to its unique visual appeal within geological formations.
Due to its complex mineral composition and low iron content, limonite ore processing requires innovative technologies tailored to its specific properties. Magnetic separation, gravity separation, flotation and other combined mineral processing methods have shown good results in effectively increasing the iron content of limonite ore.
Limonite ore beneficiation methods
Crushing & grinding
Since limonite is a relatively soft and brittle mineral, the first step in the process involves breaking large limonite ores into smaller pieces through crushing equipment such as jaw crushers or impact crushers. This initial stage is crucial to increase the surface area of the ore, making it easier to extract in subsequent processing steps.
The use of advanced grinding technology, such as ball mills or vertical roller mills, is used to further reduce the particle size of the crushed ore to significantly improve the efficiency of the mineral processing process.
By achieving a finer grind, the surface area of the ore is increased, thereby enhancing its reactivity in subsequent beneficiation steps.
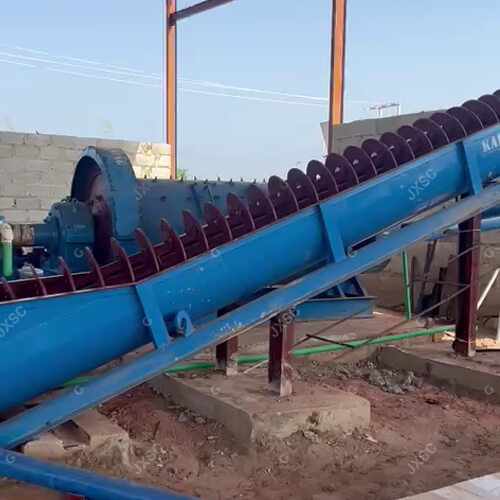
Magnetic separation
The method involves using magnets to separate magnetic iron particles from non-magnetic materials, resulting in a concentrated iron-rich product. Mainly the importance of controlling variables such as particle size, magnetic field strength and feed rate to achieve optimal separation efficiency. By fine-tuning these factors, miners can improve the purity and quality of the final iron concentrate.
High-intensity magnetic separators are usually used to achieve efficient separation of iron minerals. This device generates the strong magnetic fields needed to effectively attract and separate iron particles. Additionally, advances in magnetic separation technology have made the process of extracting iron from limonite ore more efficient and environmentally friendly, reducing waste and energy consumption in the mining industry.
Gravity separation
Limonite gravity separation processing is a complex and efficient method used in the mining industry to separate iron ore particles from waste materials. The process involves exploiting the differences in gravity between different minerals, enabling the selective separation of valuable ores. Various equipment such as jigs, shaking tables and centrifugal concentrators are often utilized to assist in the separation process. These machines work together to ensure efficient and precise separation of different ingredients based on their specific weight. Through careful calibration and monitoring, operators can achieve high recoveries and produce iron-rich concentrates.
Flotation
The process involves multiple stages, starting with grinding the ore to obtain the optimal particle size for flotation. Subsequently, specific reagents that selectively bind to phosphorus minerals are added, allowing them to attach to the bubbles and subsequently be removed in the form of foam. Flotation machines then separate the limonite concentrate from other minerals, producing a purified product ready for further processing.
A key challenge in limonite flotation processing is the presence of various impurities that can interfere with process efficiency. The method provides flexibility in adjusting parameters such as pH, reagent dosage, and stirring speed to optimize performance based on specific ore characteristics. The development of innovative methods and technologies in flotation continues to improve its effectiveness in removing phosphorus from limonite ore, paving the way for more sustainable mining practices.
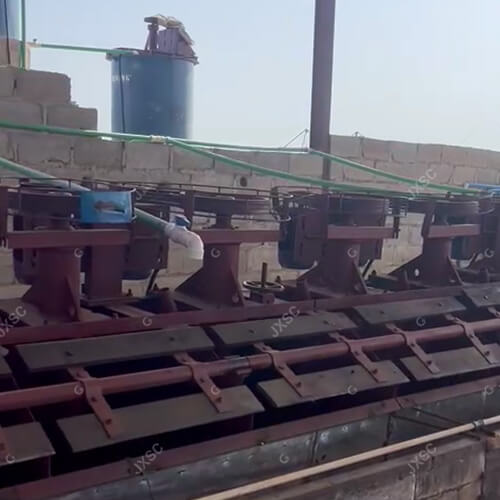
Leaching
By utilizing acidic or alkaline leaching solutions, the phosphorus in the limonite can be selectively dissolved and removed, leaving a purer iron ore product.
Additionally, the leaching process can be tailored to target specific impurities in limonite, making it a versatile and efficient ore beneficiation technology. The use of advanced technologies such as bioleaching or electrochemical leaching further enhances the effectiveness of this method and provides new opportunities for optimizing phosphorus removal from limonite. The use of leaching as a means of phosphorus removal not only improves the quality of the final product but also reduces the overall environmental impact of mining operations.
Through a combination of physical and chemical processes, the phosphorus content is significantly reduced, making the ore more suitable for a variety of industrial applications. These methods include gravity separation, magnetic separation, flotation and leaching, etc., which can significantly reduce the phosphorus content, thereby obtaining higher quality iron ore products. JXSC supports customized mineral processing solutions, flow design, equipment supply, and EPC services. Contact us online to get a quote!