Tin ore is a valuable mineral used in various industrial applications, making tin ore flotation an important process. This method separates tin from other minerals and impurities, ensuring its purity and availability in various industries. Flotation is vital in tin ore extraction and can effectively separate valuable minerals from gangue. By exploiting these differences in particle surface properties, flotation can selectively attach to air bubbles and separate them from the slurry. It is crucial because tin ore is often mixed with other elements, such as sulfur and iron, making their separation difficult.
Tin’s widespread use in electronics, packaging materials and welding makes it an integral part of modern society. Obtaining pure tin would be highly challenging and costly without the flotation process. By efficiently extracting and purifying tin through flotation, we can ensure a stable supply of this important material to meet growing global demand while minimizing its environmental footprint.
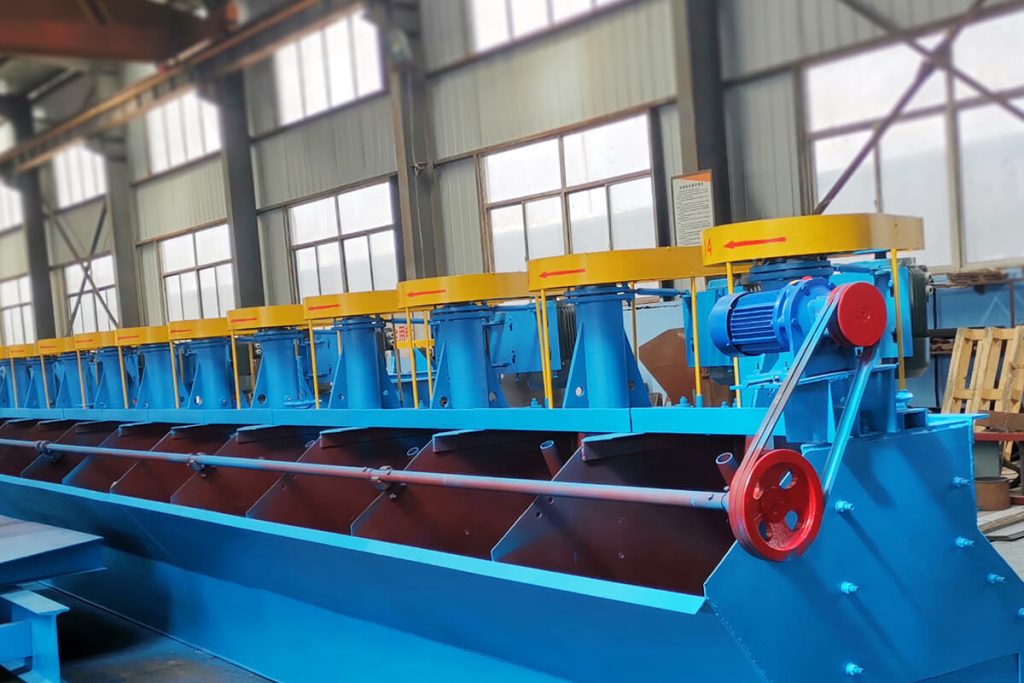
Pretreatment operations before tin ore flotation
Before the flotation of tin ore, some necessary pretreatment operations need to be carried out. These operations are critical to optimizing the efficiency and effectiveness of the flotation process, ensuring maximum recovery of tin from the ore.
(1). Grinding
It involves reducing the size of tin ore particles. It is usually accomplished through crushing and grinding stages using various types of equipment, such as jaw crushers and ball mills. The purpose is to obtain a suitable particle size range for effective separation during flotation.
(2). Grading
This operation determines the size of the particles that will undergo flotation and the size that will be discarded as waste. By properly sorting the particle size, maximum recovery of tin ore can be more easily achieved without excessive energy consumption or reagent usage. The well-graded feed allows for better control of froth stability during flotation, which is critical for separating valuable tin minerals from gangue material.
(3). Desulfurization
Desulfurization treatment is a vital pretreatment operation before tin ore flotation. Its purpose is to remove sulfur compounds from the ore, which interfere with the flotation process and reduce the overall recovery of valuable minerals.
Desulfurization methods primarily involve leaching, where a chemical solution is added to dissolve sulfur compounds in the ore particles. This technology has advantages over roasting because it operates at lower temperatures and reduces environmental pollution caused by gas emissions.
Whether by roasting or leaching methods, removing these compounds ensures higher recovery of valuable minerals while mitigating the environmental impacts of excess gas emissions or chemical use.
(4). Iron removal
A common problem that needs to be solved in tin ore flotation is the presence of iron particles, which can significantly affect the efficiency and effectiveness of flotation.
To successfully remove iron from tin ore, various techniques can be employed. One widely used method involves magnetic separation, in which magnets attract iron particles and separate them from the ore. Another method is gravity separation, which uses the density difference between iron and tin to separate them. Additionally, chemical methods such as baking or leaching can dissolve iron or convert it into a more soluble form for easier removal.
Additionally, minimizing the presence of iron increases production efficiency and improves downstream processing, such as smelting or refining.
(5). Adjustment
Chemical substances called reagents are added to the ground tin slurry. These reagents play a vital role in changing the surface properties of the minerals in the slurry, making them more susceptible to air bubbles adhering to during the flotation process. This step typically involves adjusting the pH and adding collectors and frothers, which help promote selective flotation by enhancing particle-bubble interaction.
Tin ore flotation retreatment process
Among them, these tailings after flotation are leftover materials from the initial extraction process of tin ore and may contain high concentrations of valuable metals such as copper and zinc. It would be better to reprocess the tailings to recover more valuable metals and reduce the environmental impact of their disposal.
Traditionally, these tailings have been stored in large impoundments or deposited on land, leading to potential water contamination and ecosystem degradation. However, with modern technology and multiple beneficiation combined processes to further improve the tin grade, such as magnetic separation, flotation, electrostatic separation, etc., valuable metals can be effectively separated and extracted from these waste materials.
Properly executed these treatment methods can improve concentrate grade. Using two treatment methods in tin ore flotation is critical to maximizing the recovery and grade of tin concentrate. By effectively removing impurities and upgrading ores, pretreatment technologies such as gravity separation and magnetic separation enhance flotation performance and maximize the recovery of valuable tin minerals. Additionally, tailings reprocessing not only helps minimize environmental impact but also extracts other valuable minerals that were previously discarded. JXSC will support customized tin ore beneficiation plants and equipment that will contribute to sustainable mining practices and ensure the long-term availability of mineral resources.