Ultimate Guide to Solve Vibrating Screen Blocking
It is not uncommon for the vibrating screen sieve holes blocked with materials and cause damage to the screen, especially when the screen mesh is small.This article analyzes the common causes of screen blocking holes and proposes improvement methods.
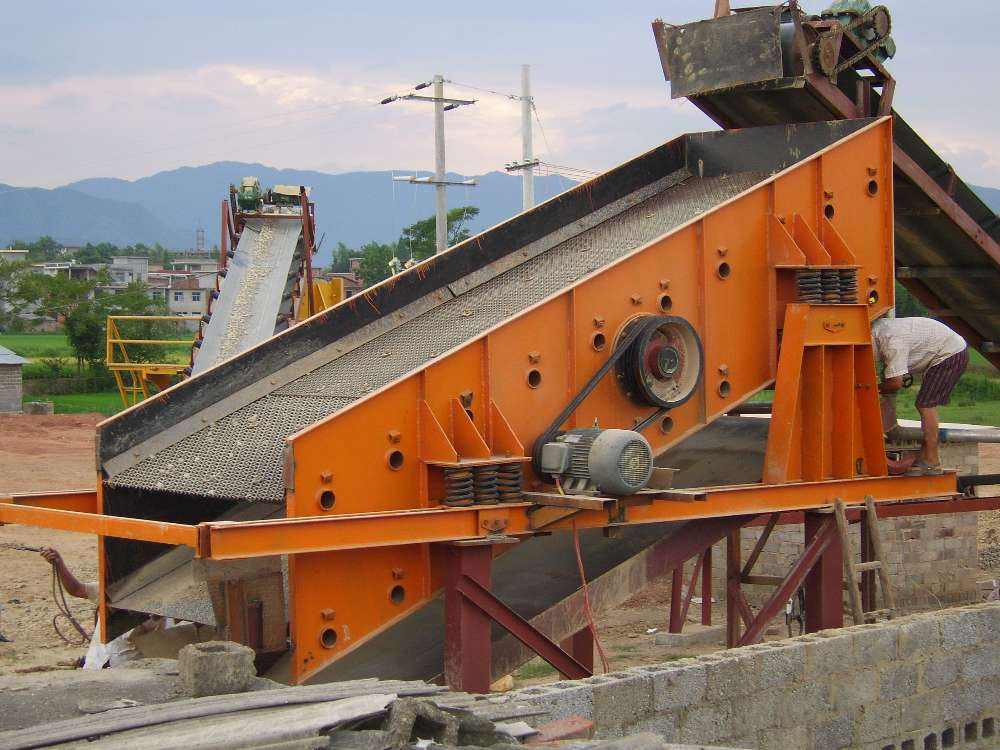
1. Main causes of screen blocking
1) Contain a large number of critical material particles close to the separation point. That is to say, the particle size of the crushed stone is critical to the mesh size of the screen. During the screening of the stone, such particles are stuck in the mesh and cannot pass through the sieve smoothly, which is called critical hole blocking.
2) There are many materials that have multiple contact points on the screen.
3) There are many flake particles. Due to the crushing or the stone itself, there are many flake materials in the stone material, and the flake materials cannot be smoothly passed through the sieving. At the same time, the flake materials are intertwined into a net shape, which hinders other materials from sieving and blocking holes.
4) The diameter of the steel wire for the screen is too thick.
5) The screened material contains high moisture and viscous materials such as mud and sand. Because there is a lot of mud in the stone, or when the stone requires water washing, the fine-grained stone will stick to each other into agglomerates due to the intervention of water on the one hand, and the soil will stick to the screen surface on the other hand, making it difficult to screen the material and causing blockage. .
Except for the fourth type, the first and second types are inevitable. The third and fifth types are more or less existent. The fixed mesh screen cannot effectively overcome the impact of critical material particles on the screen hole. Blockage, resulting in low screening efficiency of the vibrating screen. Generally, the screening efficiency of a vibrating screen with a fixed mesh screen is less than 50%. Even if the amplitude is increased, it cannot effectively solve the blockage. Moreover, increasing the amplitude may affect the service life of the screen.
2. solutions to the blockage
By changing the form of the mesh structure of the screen, the clogging problem can be effectively solved. The following introduces several anti-blocking screens.
(1) Under the premise of meeting the construction requirements, deform the mesh and use a certain proportion of rectangular holes. For example, the original requirement of 3.5mm*3.5mm mesh is changed to 3.5mm*4.5mm rectangular holes (as shown in the figure 1).
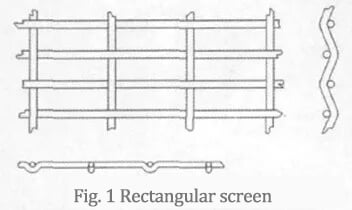
(2) Use diamond-shaped hole anti-blocking screen (as shown in Figure 2). This screen is made of the same two adjacent screen bars with small vibrations, which has a better anti-blocking effect.
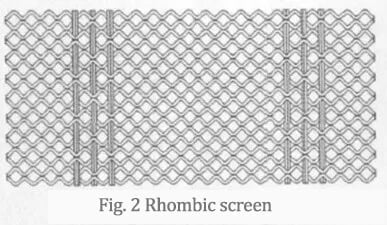
(3) In order to further improve the anti-blocking effect of the screen, we have made a triangular hole anti-blocking screen (shown in Figure 3). The feature of this screen is that of the two adjacent screen bars, one is a static screen and the other is a dynamic screen.
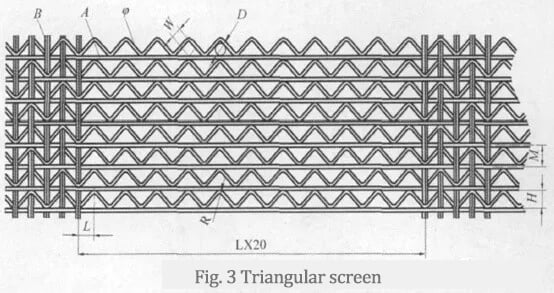
Principle of Anti-blocking of Triangular Mesh Screen
Extend the planar two-dimensional fixed holes to three-dimensional and three-dimensional variable meshes, and use the secondary vibration generated by the adjacent screen bars in the random vibration to establish an effective vibration difference, and realize the continuous change of the screen holes in the screening. There is relatively no fixed critical particle stone.
Specific approach
Among the two relatively immobile static screen bars, a movable screen bar with a relatively large vibration amplitude is set. The movable screen bar can bounce or sift the stones during the jam. According to the characteristics of the material, the relative elasticity and vibration amplitude of the static and dynamic screens can be adjusted accordingly to make the screen in the best screening state. The screening efficiency can be increased by about 30% compared to the fixed mesh screen. The self-cleaning function of the screen is realized, and the blockage of the screen hole is greatly reduced.
Features
The static screen of the screen is thicker than the dynamic screen, so it not only increases the wear resistance of the screen, but also improves the screening efficiency. At the same time, the screen bar structure of the screen can minimize the contact point between the material and the screen hole and reduce the occurrence of hole blocking.
3. the properties comparison of three types of wire meshes including square, rectangular and triangular
Compare the performance of screens with square holes, rectangular holes and triangular holes. As can be seen from the table below, among this kind of screens, the triangular hole anti-clogging screen is the preferred small mesh screen with high screening efficiency and not easy to block holes.
Screen mesh shape | Square | Rectangular | Triangular |
Advantages | high control accuracy of material particles | It increases the efficiency and reduces the plugging slightly compared with the square mesh screen | Not easy to plug holes, high screening efficiency |
Disadvantages | Screen holes are easily blocked, especially under 8mm mesh | Can only be used without affecting the production process, and the material particle requirements are not high | Only after the correct conversion of the mesh can it replace the square mesh screen |
4. application of triangular mesh screen
1) Materials suitable for screening: crushed stone and gravel, limestone, iron ore, coke, sintered ore, ridge clay and similar materials.
2) The maximum temperature of the screened materials is not more than 120°C, and the ambient temperature is -40~+60°C.
3) The height of the material at the feed inlet falling between the screens is not more than 300mm.
4) The maximum particle size on the screen surface is not more than 5 times the size under the screen.
5) Chemical resistance. Acid and alkali are suitable for pH 4~9, and stainless steel wire can be used for those with stronger pH.
6) Maximum feed weight. When the screen is screened by a horizontal vibrating screen, the thickness of the material layer should not be more than 5 times the aperture.
5. conclusion
The screen may block holes for various reasons during use. The way to solve the hole blocking is to expand the mesh of the screen from a two-dimensional fixed hole to a three-dimensional variable mesh. This is a very effective method, especially in the screening of materials with particles below 5mm, which can effectively reduce the occurrence of material blocking.
In the installation of the screen, it should be noted that the screen is always in a tight state on the screen to avoid loosening the screen and causing secondary vibration.
Products
Send Us A Message
More Posts
related materials
- Placer Gold Process Plant
- Diamond Mining Process
- Silver Flotation Process
- Gold Flotation Process
- Gold CIL Processing Plant
- Gold CIP Processing Plant
- Dense Media Separation(DMS) Process
- Copper Processing Plant
- Lead Zinc Ore Processing
- Tungsten Ore Processing
- Magnetite Separation Plant
- Manganese Ore Processing
- Chrome Processing Plant
- Quartz Beneficiation Plant
- Phosphate Rock Processing
- Fluorite Ore Processing
- Tantalum Niobium Ore Processing
- Tin Ore Processing Plant
- Titanium Beneficiation Plant
- Graphite Ore Processing
- Hematite Separation Process
- Iron Ore Beneficiation Plant
- Kaolin Processing Plant
- Limonite Ore Dressing
- Lithium Processing Plant
- Magnetite Separation Plant
- Molybdenum Flotation Process
- Cobalt Ore Processing
- Nickel Ore Beneficiation
- Antimony Ore Processing
- Barite Ore Beneficiation
- Feldspar Processing Plant
- Coal Washing Process
- Beach Sand Beneficiation Plant
- Tailings Processing
- Chrome Wash Plant