There are several different types of iron ore, each with its own unique characteristics and chemical composition. The iron ore beneficiation process aims to remove impurities and enhance the iron content in the ore, making it suitable for use in steel production.
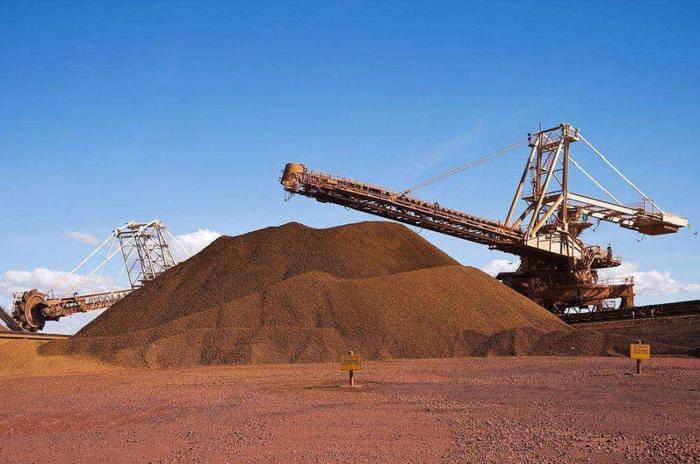
Iron ore beneficiation Process
Limonite Beneficiation
Because the theoretical iron grade of limonite is low, and often with calcium and magnesium, manganese is symbiosis. Hence, using physical beneficiation methods, iron ore concentrate grade is challenging to reach more than 45%, but after roasting, because of the large burn loss, it significantly improves the grade of iron ore concentrate. The more economical beneficiation method is gravity separation, which is a strong magnetic separation, but it is difficult to effectively reduce the content of impurities in the iron ore concentrate. Strong magnetic separation – flotation combined process can effectively reduce the content of impurities in iron ore concentrate. Iron ore concentrate roasting is still a high-quality raw material for ironmaking.
Oolitic hematite beneficiation
Oolitic hematite embedded in very fine particle size and often with rhodochrosite, oolitic chlorite and phosphorus minerals symbiotic or mutual wrapping, so oolitic hematite is currently recognized as the most difficult type of iron ore selection at home and abroad. In the past, a lot of experimental research work on this type of iron ore beneficiation, including reduction roasting – weak magnetic separation process of the selection index is relatively good, but because of its technical difficulties is the need for ultra-fine grinding, and the current conventional beneficiation equipment and chemicals are difficult to recover effectively -10μm microfine particles of iron minerals, so this type of iron ore resources not utilized.
Relevant preliminary research results prove that ultra-fine grinding – selective flocculation (agglomeration) – strong magnetic separation or flotation, reduction roasting – ultra-fine grinding – selective flocculation (agglomeration) – weak magnetic separation or flotation and other high-efficiency beneficiation process or combined electrometallurgical process has shown its superiority.
iron ore contain high sulfur, phosphorus Beneficiation
The common processes used to remove sulfur from iron ore concentrates are flotation and roasting. At the same time, the latter is costly and produces environmental pollution, so the main direction of research is to strengthen flotation.
A large number of research results prove that iron ore concentrate phosphorus removal can be used magnetic separation, reverse flotation, selective flocculation (agglomeration), acid leaching, chlorination roasting – acid leaching, bioleaching and its combined process, etc., of which magnetic separation – reverse flotation, selective flocculation (agglomeration) – reverse flotation combined process is more economical.
Iron Ore Beneficiation Process Flow
- One popular beneficiation method is mechanical crushing and screening, which involves breaking down large chunks of ore into smaller pieces and separating them based on size. This method is particularly effective for low-grade ores where the iron content is not very high.
- Another common method of beneficiation is through magnetic separation, which exploits the difference in magnetic properties between iron minerals and gangue minerals. By subjecting the crushed ore to a magnetic field, the iron-rich particles can be separated from other non-magnetic particles, resulting in a concentrate rich in iron content. This process is highly efficient and has been extensively used for beneficiating magnetite ores.
- In recent years, innovative methods such as flotation have also gained popularity for beneficiation purposes. Flotation involves adding chemicals to modify the surface properties of minerals, allowing them to attach to air bubbles and float to the surface while leaving unwanted materials behind. This technique has proven effective for separating silicate gangue minerals from haematite or other oxide ores.
Overall, there are numerous methods available for beneficiation depending on factors such as the nature of the ore deposit, mineralogy, and desired product quality. As technology advances further, new breakthroughs may offer even more efficient ways to extract valuable iron content from various types of ores.
The beneficiation of various types of iron ore is a complex process that requires careful analysis and planning. Whether it is hematite, magnetite, or any other iron ore, implementing effective beneficiation technology can significantly improve the economic viability of a mining operation. The specific beneficiation technology used depends on the characteristics of the ore, such as its chemical composition, mineralogy and physical properties; by understanding the characteristics of each ore and the desired end product, JXSC supports customized beneficiation plants and equipment to maximize The value and quality of the final product.