The sand and gravel industry is changing rapidly. Traditional sand making methods often harm the environment. Dust flies, noise disturbs people, and energy is wasted. Many mining operations have difficulty meeting environmental standards while maintaining production efficiency. JXSC has been committed to solving these problems for many years. If you think that all sand making equipment is cookie-cutter, you are wrong. The benefits of modern environmental solutions go far beyond basic crushing functions. Today’s eco-friendly VSI sand makers use breakthrough technology to provide better sand making results while protecting nature.
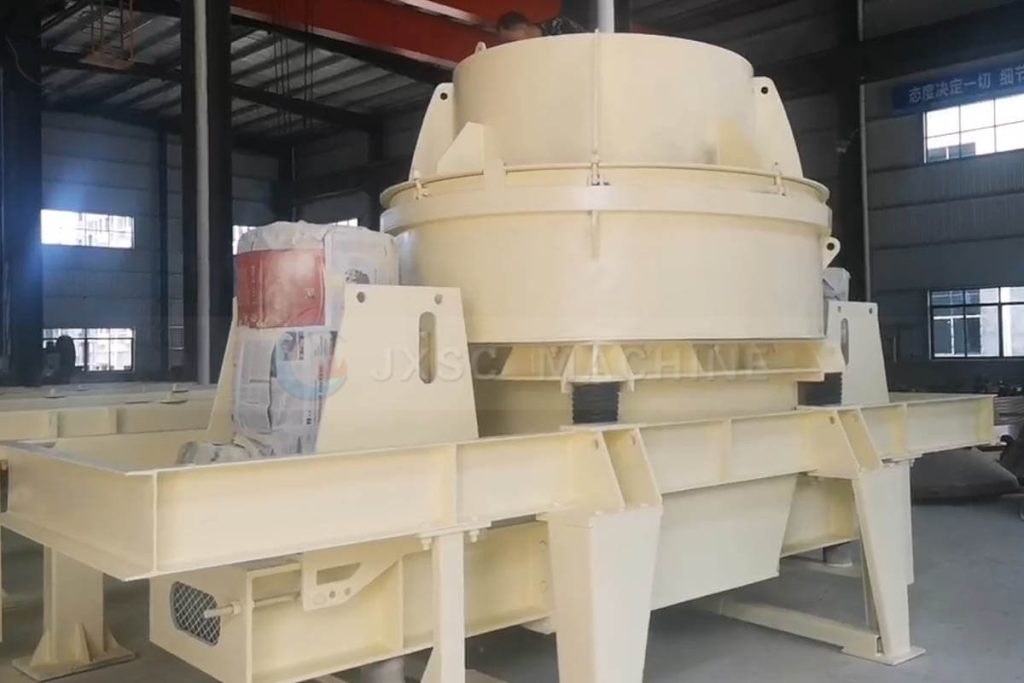
Modern eco-friendly VSI sand maker mainly relies on six core technologies: 1) Intelligent dust removal system, which can capture 99% of dust. 2) Closed noise reduction design. 3) Integrated crushing and shaping technology. 4) Automatic control system, variable frequency energy-saving device, saving electricity. 5) Water recycling system to achieve zero wastewater discharge. 6) Wear-resistant composite materials to extend the service life of wearing parts.
What is eco-friendly VSI sand maker?
Eco-friendly VSI sand maker is a crushing equipment optimized for reducing dust, noise and energy consumption. Compared with traditional sand making machines, it adopts a closed structure, efficient dust removal system and intelligent control technology to ensure that the whole production process meets environmental protection standards. It is suitable for construction, mining, water conservancy, and other fields with strict environmental protection requirements, and is the key equipment for green sand and gravel production.
Working Principle
Based on the dual core principles of “impact crushing + intelligent environmental protection”, the centrifugal force is generated by the high-speed rotation of the vertical shaft impeller, and the material is ejected into the crushing chamber at an adjustable speed, and the material is crushed by impacting the impact plate or material lining.
The stone is first evenly fed into the crushing chamber through a vibrating feeder, and is accelerated and ejected under the drive of the high-speed rotating impeller, and is crushed by high-speed collision with the surrounding guard plates or other materials. The crushed materials are graded by the screening system, and qualified sand materials are output, and substandard materials are returned for further crushing, forming a closed-loop sand making process, which is more efficient and avoids waste of resources.
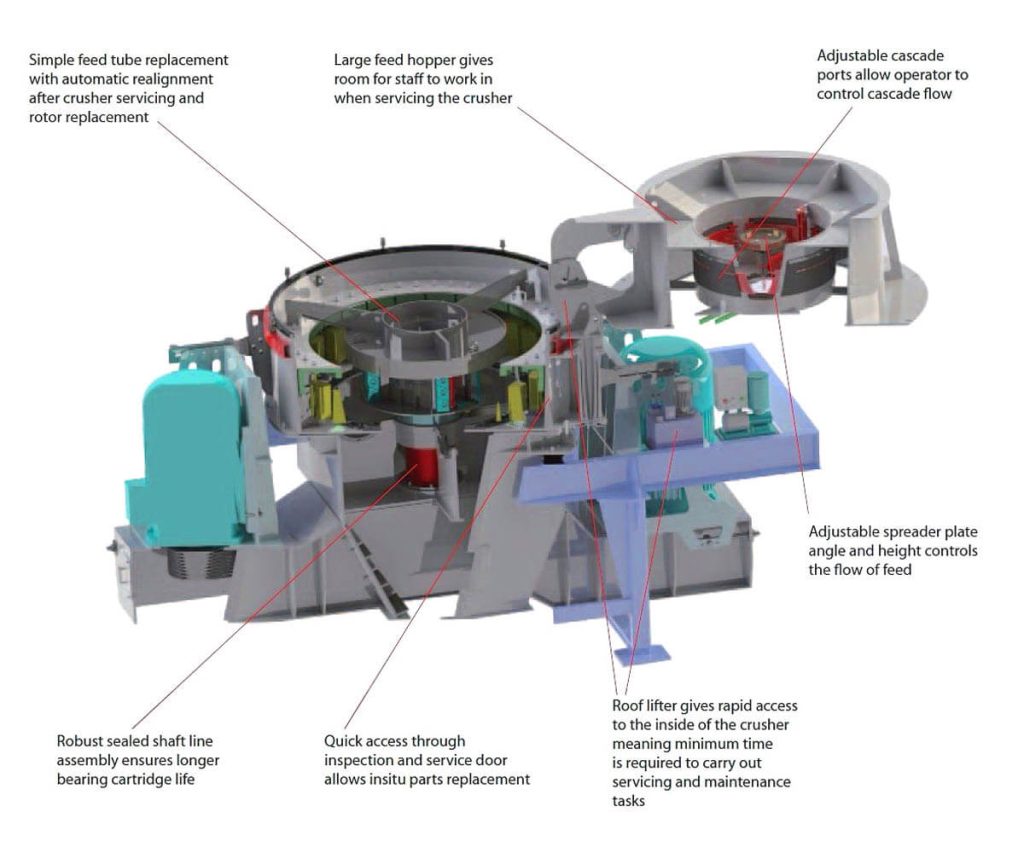
6 core technologies of eco-friendly VSI sand maker
1. Dust Suppression: Clearing the Air
The dust control technology of the eco-friendly VSI sand maker is the core link to achieving green production. It achieves ultra-low emissions through the dual mechanism of “source suppression + terminal collection”. The equipment adopts a vortex cavity airflow self-circulation design, using the airflow generated by the impact of materials to form a negative pressure cycle in the closed cavity to reduce dust spillage. The body is equipped with a high-efficiency venous dust collector, which has a filtration accuracy of 0.3 microns through the filter bag, and cooperates with the fan’s variable frequency speed regulation system to ensure that the dust removal efficiency is stable at 99%.
2. Quiet Operation: Turning Down the Noise
Noise control is achieved through the triple technology of “material optimization + structural shock absorption + sound wave offset“. Key parts of the VSI sand maker such as impellers and impact plates are made of high-chromium alloy cast iron and polyurethane composite materials, and their internal porous structure can absorb high-frequency vibration noise. Spring shock absorbers and rubber buffer pads are installed between the machine body and the foundation to reduce vibration transmission efficiency by 60%. The internal rubber lining of the crushing chamber absorbs high-frequency sound waves and offsets most of the noise by emitting reverse sound waves.
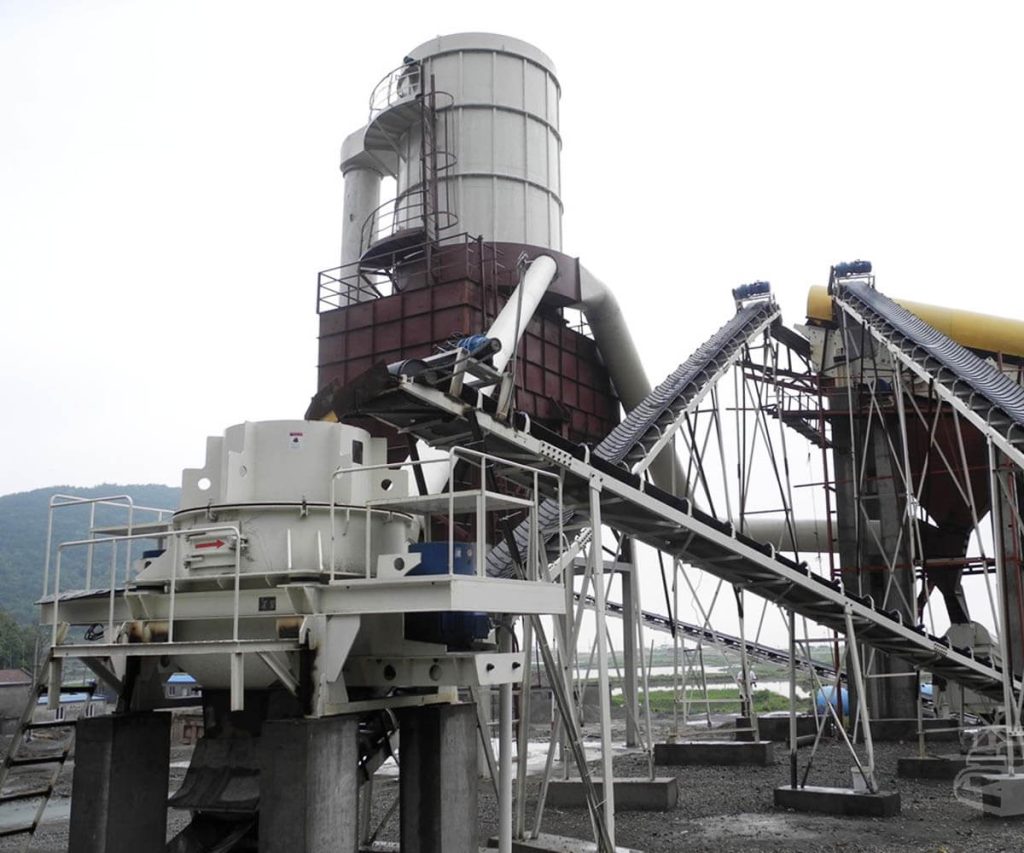
3. Vertical shaft impact crushing and shaping integrated technology
This technology breaks through the traditional sand making “crushing-shaping” step-by-step operation mode, and realizes “one machine for two purposes” through the vertical shaft impeller structure. The hyperbolic volute crushing chamber extends the grinding path, and the fine powder content of the finished sand is increased by 15%, and the proportion of needle-like particles is less than 5%. The built-in eddy current powder selection device of the equipment can separate the super coarse particles in real time and return them to the crushing chamber for secondary processing. The finished sand grading meets the “construction sand” Class I sand standard.
4. Wear-resistant parts strengthening technology
Because of the pain point of the rapid wear of the vulnerable parts of the sand making machine, “material innovation + structural optimization” is used to extend the service life. The throwing head adopts WC-Co tungsten carbide alloy powder metallurgy technology, with a hardness of more than HRC85 and super impact resistance. The peripheral guard plate is symmetrically designed and can be flipped for use after wear, which improves the utilization rate.
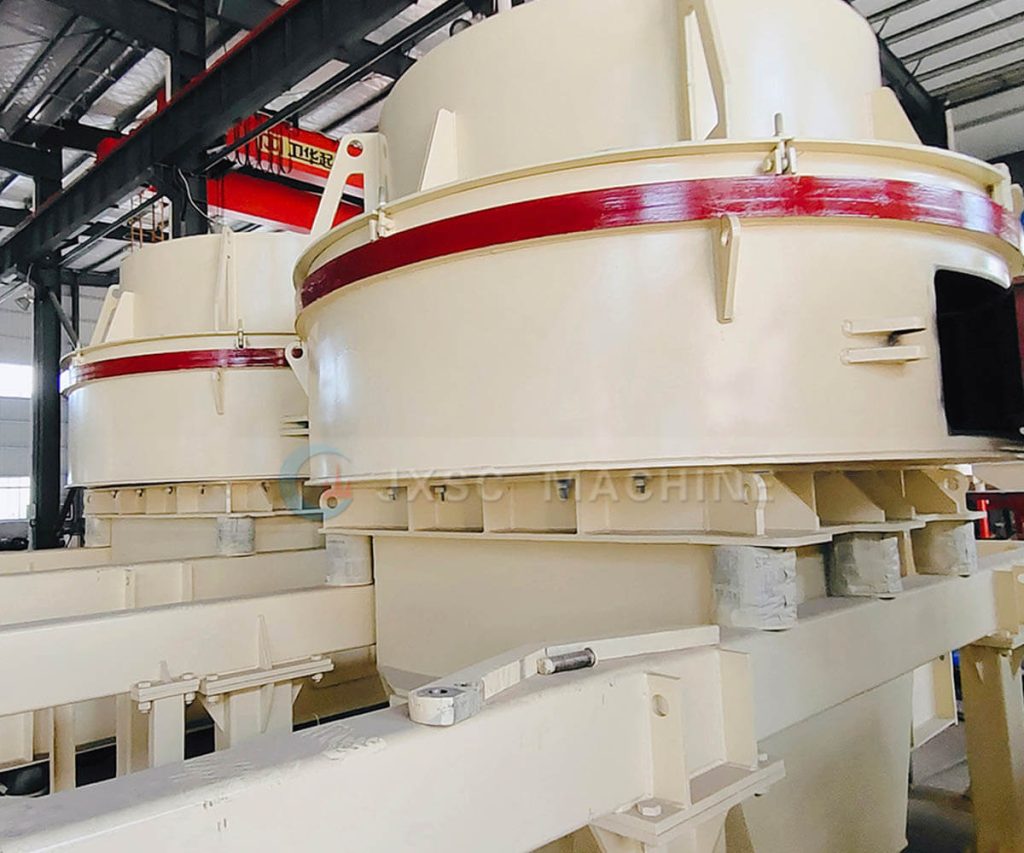
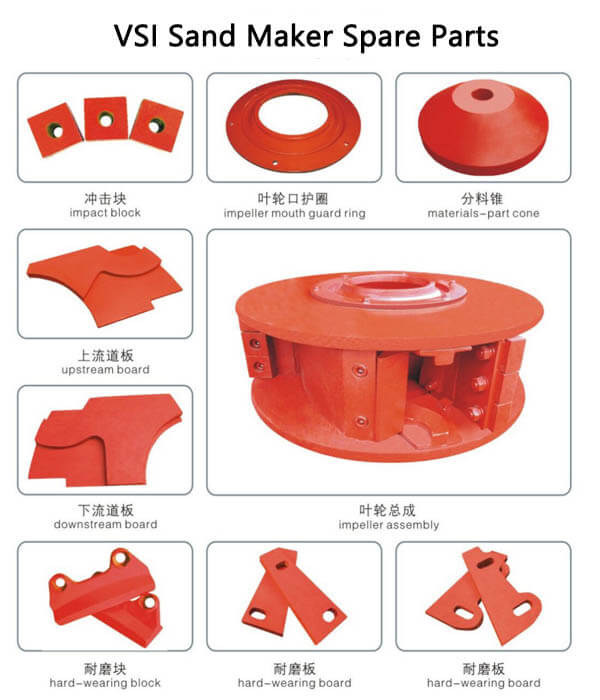
5. Intelligent and energy-saving control technology
The thin oil circulation lubrication system is adopted, and the flow and temperature of the lubricating oil are monitored in real time. The electric heating device is used to ensure normal startup in a low-temperature environment. The motor adopts permanent magnet synchronous frequency conversion technology, which saves 15-20% energy compared with traditional asynchronous motors. The combined impeller realizes independent replacement of blades and shortens maintenance time.
6. Multifunctional crushing chamber design
The modular chamber structure realizes “one machine with multiple functions” and can quickly switch between the “stone hitting stone” and “stone hitting iron” crushing modes. The “stone hitting stone” technology achieves self-crushing through high-speed collision between materials, reduces metal wear, and is suitable for processing high-hardness materials (such as granite and basalt). The finished product has a rounded particle shape and low powder content. The “stone hitting iron” technology achieves higher crushing efficiency through the collision of materials and wear-resistant blocks. It is suitable for crushing medium and low hardness materials (such as limestone). The two are quickly switched through the hydraulic system. This technology extends the life of the equipment by more than 30%, while reducing energy consumption by 15%, taking into account both high efficiency and environmental protection.
Eco-friendly VSI sand maker‘s core technologies include environmental compliance brought by dust removal technology, night operation permits obtained by noise reduction technology, electricity savings created by energy-saving technology, and intelligent control systems, which help to reduce environmental impact while improving operational efficiency. Mainly through the integrated process of “crushing-shaping-grading“, while improving the quality of sand, it can achieve source control of dust, noise and energy consumption to meet green production requirements.
As a mining equipment manufacturer with more than 40 years of experience, JXSC’s team continues to develop more advanced aggregate crushing, sand making and mineral beneficiation solutions to meet the ever-changing industry needs.