What is Zirconium Ore?
Zirconium ore is the name of a mineral, formerly known as zircon, hyacinth stone. There are 38 independent zircon minerals, and zircon (ZrSiO4) and baddeleyite (SiO2) are the main zirconium-containing minerals with industrial value. Zirconium is a mineral composed mainly of zirconium, silicon, and oxygen crystallized from magma during the formation of igneous rocks. Its theoretical composition is 67.1% zirconium dioxide ZrO2 and 32.9% silicon dioxide SiO2. It is mainly used in casting, metallurgical lining, refractory materials, ceramics, military armored shells, and other industries.
types of zirconium ore
The world’s zircon ore reserves are mainly distributed in Australia, South Africa, Ukraine, India, and Brazil. The global annual zircon reserves are about 40 million tons: among them, Australian zircon ore contains ilmenite-associated ore, accounting for one-third of the output; South Africa’s is rutile-associated ore; India has garnet monazite-associated ore, and Malaysia has tin zircon-associated ore.
Uses of zirconium ore
Zirconium ore is divided into two categories according to its main use: metallic and industrial zirconium. Metallic nuclear-grade zirconium is at the top of the zirconium industry chain, and industrial zirconium is mainly used in chemical acid-resistant and alkali-resistant equipment, the electronics industry, and other fields. Among them, more than 63% of zirconium is used in the fields of ceramics and refractory materials in the form of zirconium silicate and zirconium oxide, about 13% is used in the field of zirconium chemicals, and only 3% to 4% of zirconium ore is processed into metallic zirconium.
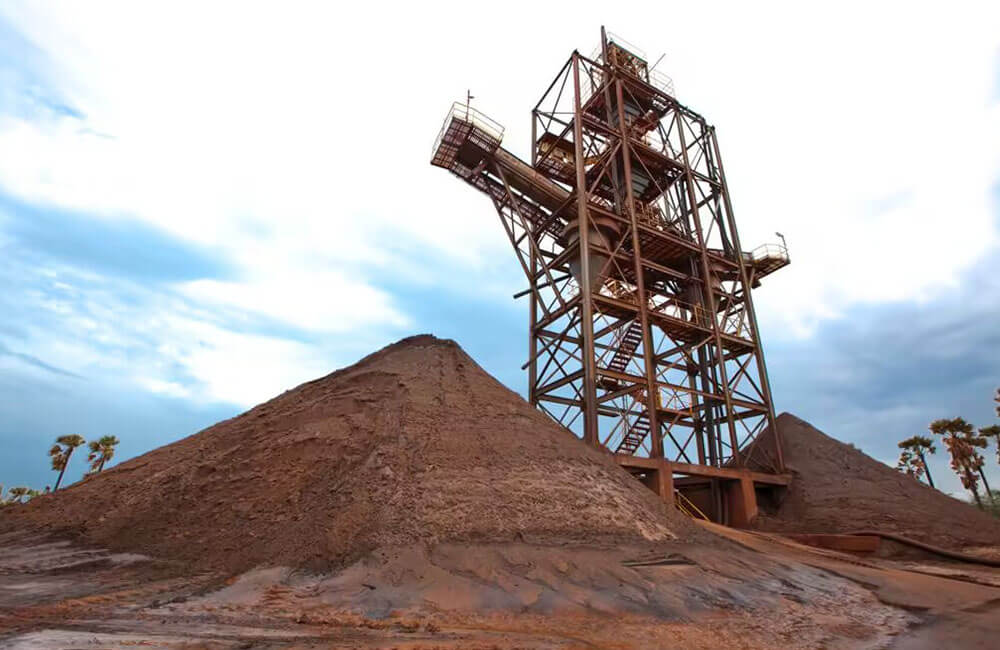
Why zirconium ore needs beneficiation?
Zircon is widely used in the nuclear industry, ceramic manufacturing, jewelry, and other fields. It is an important mineral material in the defense and aerospace industries and zriconium ore beneficiation technology can provide high-quality zircon raw materials to support the development of these high-tech fields. Usually, zircon is found in seaside sand mines and is the main source of metal zircon for worldwide steel. Usually, the grade of seaside sand ore is only 0.2%; weathered rock is 0.8%; primary endogenous ore is 8%, but mineral processing is complicated and rarely mined. Moreover, zircon ore usually contains various impurity minerals, such as ilmenite, rutile, monazite, etc. These impurities will affect the application effect and product quality of zircon. Among them, most of the zircon particles are 0.1-0.63mm.
In addition, the application of zircon in ceramics, steelmaking, and nuclear industries requires strict purity requirements. Combined with the mineral information and important uses of zircon ore, the maximum utilization rate of zircon resources can be achieved. All of the above require mineral processing to separate and purify the valuable mineral components in the ore, remove impurities, and increase the zircon content in the zircon ore.
Among them, the quality standard for steelmaking requires zirconium with a purity of more than 65%. Through zirconium beneficiation, impurities such as ilmenite, rutile, and monazite can be removed to improve the purity of zircon and meet the standards of specific industrial applications.
How To Beneficiate Zirconium Ore
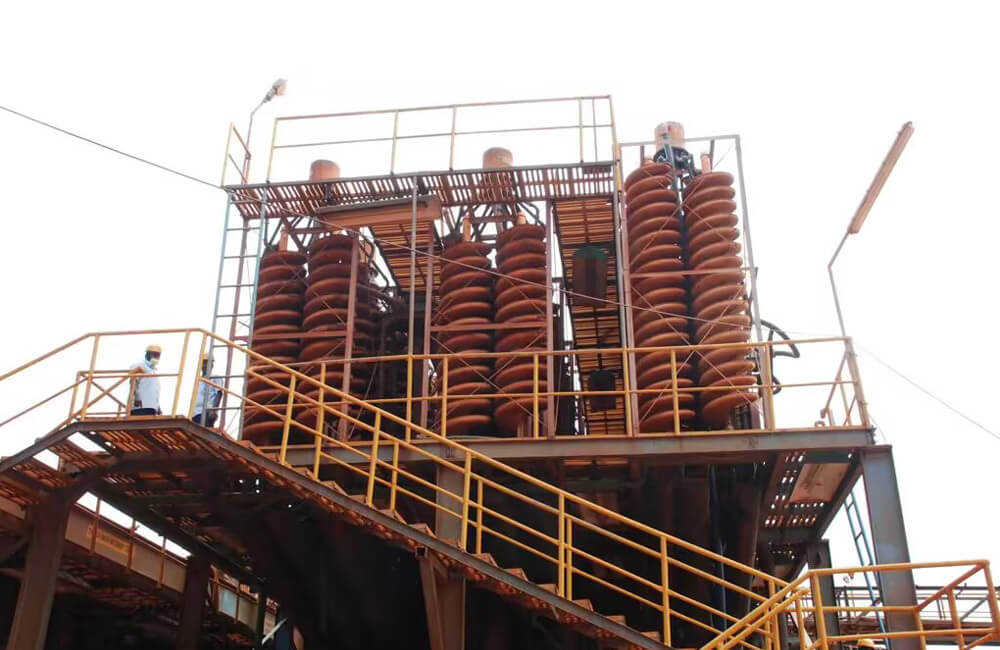
Zirconium Ore Beneficiation Process
1. Zirconium ore Gravity separation
Gravity separation is one of the basic methods for zirconium ore beneficiation, which uses the difference in mineral density for separation. For example, a shaking table can effectively separate heavy minerals (such as zircon) from light minerals (such as quartz and feldspar).
2. Zirconium ore Flotation
Flotation is achieved by changing the surface properties of minerals to change their hydrophilicity or hydrophobicity. Commonly used collectors include fatty acids (such as oleic acid, sodium oleate), etc.
3. Zirconium ore Magnetic separation
Magnetic separation uses the magnetic difference of minerals for separation. Dry and wet magnetic separation can be used for beneficiation, and wet magnetic separation is particularly suitable for the separation of fine-grained zircon ores.
4. Zirconium ore Electrostatic separation
Electrostatic separation uses the difference in mineral conductivity for separation. Desludging, classification, drying and dosing are usually required before electrostatic separation.
Usually, a combination of gravity separation, flotation, magnetic separation and electrostatic separation is required to more effectively separate valuable minerals from zircon ore and obtain zircon products that are most suitable for the specific needs of industries such as nuclear industry, ceramic manufacturing, and steelmaking.
Zirconium Ore Beneficiation Case
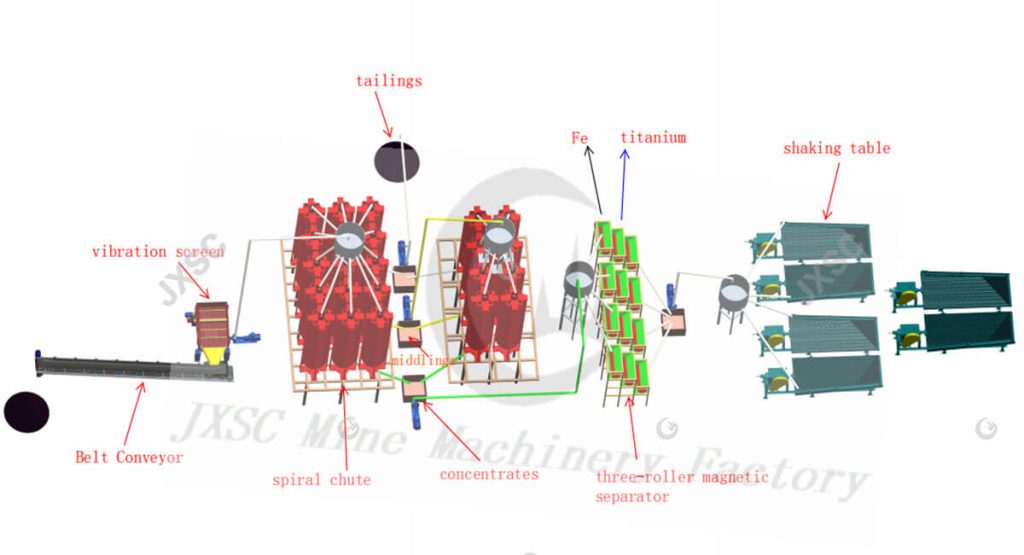
The original ore informaction of the case: single zircon sand containing ilmenite and iron ore, 5% ZrO2, 8.93% TiO2.
Zircon ore srpatation process flow: First, 0-2mm can be screened out through a vibrating screen, and those larger than 2mm are transported to the waste pile. The 0-2mm material enters a two-stage spiral chute group for sorting. Then, the concentrate is sent to a weak magnetic separator to select magnetite, and then to a medium magnetic separator to select ilmenite. Finally, the materials in the concentrate pool are sent to a distribution bucket, and then to a shaking table for re-separation.
This set of zirconium ore beneficiation equipment can achieve and get 64.47%, ZrO2 concentrate grade, with a recovery rate of 84%; the TiO2 grade is 49.2%, with a recovery rate of 57.94%.
The zirconium ore beneficiation includes multiple steps, such as crushing, grinding, screening, gravity separation, magnetic separation, flotation and magnetic separation. It not only helps to increase the added value of zirconium products, but also reduces environmental pollution and improves the recycling rate of resources. Zircon ore processing can provide better materials for various industries. JXSC will carefully design each step to achieve the maximum extraction of zircon and the maximum removal of impurities. Contact us for more mineral processing solutions and the latest quotes for equipment!