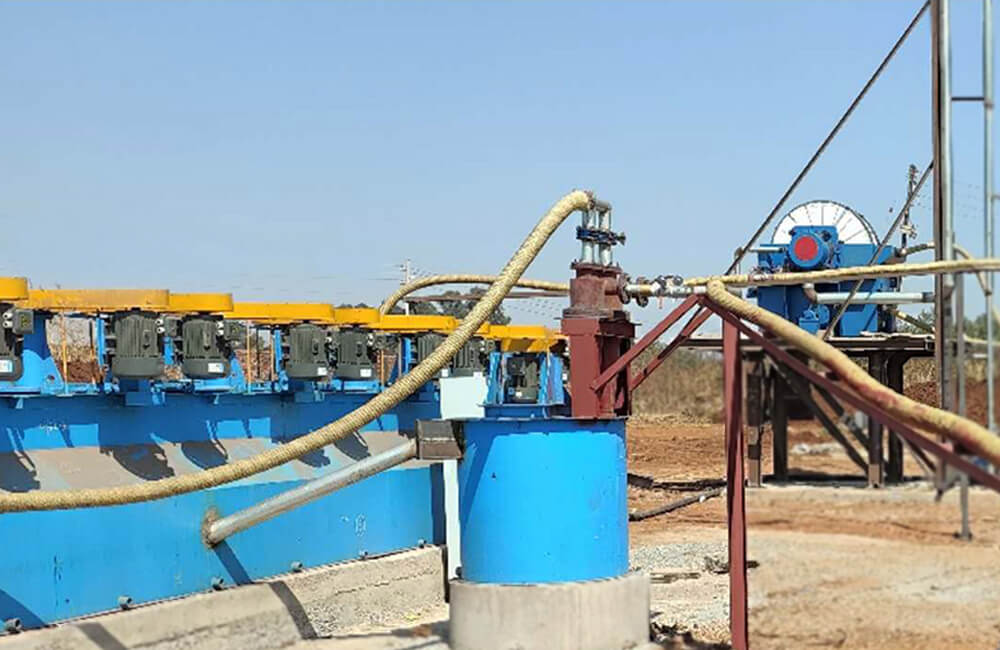
Antimony Ore Processing
Antimony ore is divided into antimony oxide and sulfide, and its beneficiation methods are hand selection, crushing, grinding, gravity separation, and flotation.
The antimony ore processing plant can be used for the beneficiation of various antimony ores, such as antimony sulfide ore, sulfide-oxidation mixed antimony ore, stibnite, tungsten-antimony-gold polymetallic sulfide ore, tin-lead-antimony-zinc polymetallic sulfide ore, etc.
Antimony Beneficiation process
1. Hand Selected
Antimony ore is often produced as coarse monomer crystals or massive aggregate crystals. Due to the large differences in color, luster, and shape between antimony-containing minerals and gangues in antimony ore, it is convenient to hand-select.
To improve the efficiency of manual separation, ore washing should be carried out first to remove sludge impurities. Due to the relatively large volume of the original ore of stibnite, it needs to be crushed to be sorted in the next step.
2. Antimony ore Gravity Separation
Gravity separation is mainly suitable for the antimony oxide ore and coarse-grained stibnite processing, and can also be used for pre-selection and enrichment of antimony sulfide ore before flotation. The common stibnite, yellow antimony, red antimony and antimony are minerals with high density and coarse particle size separated from gangue by gravity separation. Especially for the pre-selection of low-grade antimony ore, it has a very good effect.
3. Antimony ore Flotation Process
Flotation is applied to fine-grained disseminated antimony sulfide ore. It has high beneficiation index and recovery rate.
- The commonly used single flotation method is suitable for processing single antimony ore.
- The combined gravity separation-flotation method is suitable for treating antimony ore with uneven particle size. For example: tungsten-antimony-gold polymetallic sulfide ore, antimony-arsenic-gold polymetallic sulfide ore, tin-lead-antimony-zinc polymetallic sulfide ore, antimony-lead-zinc-mercury polymetallic sulfide ore and arsenic-antimony-gold polymetallic sulfide ore, etc. The purpose of re-election is to discard a large amount of waste rock and reduce the cost and equipment investment of subsequent flotation.
Antimony Ore Processing Plant
sulfide antimony flotation plant
This is cpmplete 300TPD sulfide antimony flotation process plant with spiral chutes for tailing. It mainly includes the following equipment and flow details:
- Chute feeder
- Jaw crusher
- Fine jaw crusher
- Vibration screen
- Electromagnetic feeder
- Ball mill
- Slurry pump
- Spiral classifier
- Flotation machines
- Thickener
- Disc vacuum filter machine
- Spiral chute
- Shaking table
- Cone thickener
- Plate filter press
300TPD Antimony flotation plant flow
(1). Crushing & screening: The chute feeder automatically feeds the stones to the jaw crusher. The jaw crusher crushes the big stones into small materials; then the fine jaw crusher makes the stones into fine sands. The vibration screen is for sieving more than 20mm back to the fine jaw crusher, and 0-20mm to the storage bin.
(2). Grinding stage: The storage bin+electromagnetic feeder automatically feeds the materials to the ball mill. The ball mill grills the fine sands to 0-1mm, combined with the spiral classifier to ensure the final product’s size is 0-0.074mm.
(3). Flotation stage: The No.1 slurry pump transports the overflow from the spiral classifier to the flotation machine. The flotation machine is for getting the antimony concentrate with chemicals.
(4). Gravity separation: The tailings of the flotation machine will pump to the spiral chutes to recover the antimony, and the antimony concentrated from the spiral chute will go to the shaking table concentrate again.
(5). Concentrate & drying: The antimony concentrate of the flotation machine will go to the thickener and then to the disc vacuum filter machine to get dry final products. The tailing of the spiral chute and shaking table will pump to the cone thickener and then to the plate filter machines to recycle the water from the tailings.
Notes: The capacity for this complete flotation plant can be customized as per request, such as 10tph, 50tph, 100tph, etc. Furthermore, a centrifuge concentrator can replace the spiral chutes in the process flow. Antimony ore after gravity separation is usually purified by flotation; the actual needs need to be modified according to the mine conditions. Contact us immediately to get the ex-factory price of antimony ore processing equipment!
Contact Us Now
Ask us about mineral processing configuration and equipment quote! (No job, No investment)
Notice:
- We only provide mineral processing equipment and solutions; not buy and sell minerals/ ores/ materials.
- We do not recruit, don’t offer jobs, and are not interested in investments or partnerships.
- We value your privacy and keep your information safe.