Mineral Processing » Solutions » Chrome Processing plant
Chrome Processing plant
Advanced Chrome Wash Plant & Lateritic Chromite Solutions | ISO Certified Mining Equipment
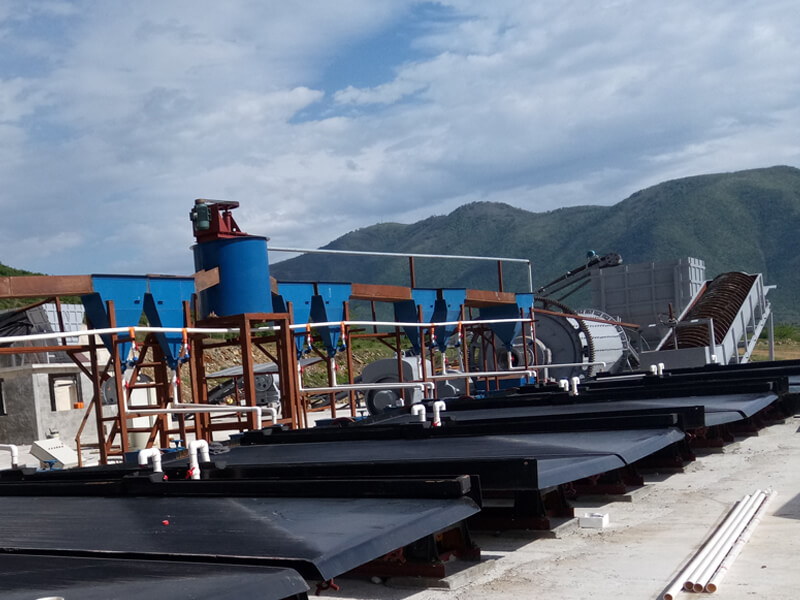
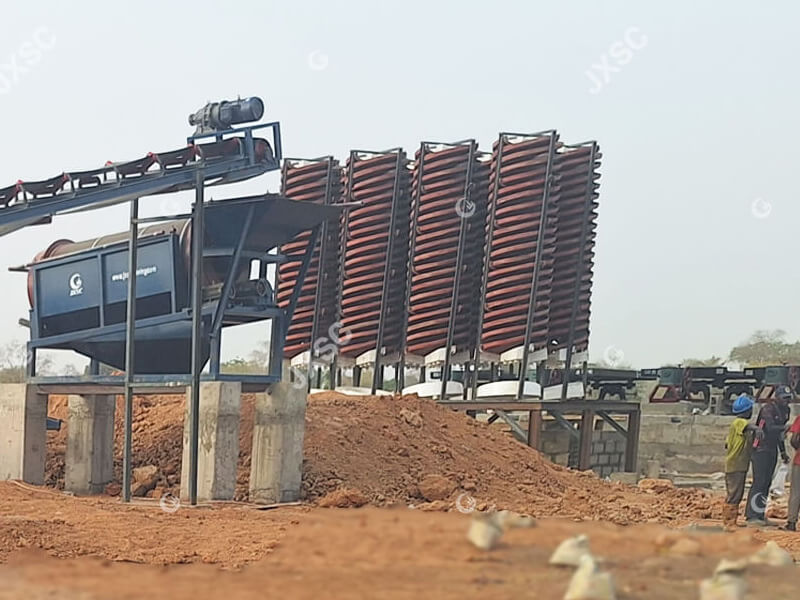
Chrome (chromium, chromite) processing plant is also called chrome wash plant or chrome recovery plant. With 40+ years of experience in mineral processing, JXSC supports customized chrome processing equipment, including washing, crushing, grinding, gravity, flotation, and magnetic separation. The chrome ore beneficiation process is used to extract and refine chromium ore, maximize concentrate grade and recovery rate up to 95%+.
Application: Chrome wash process plant is widely used to handle chromium spinel mineral, alluvial chrome ore, laterite chromite (weathered oxide ore), complex associated minerals, and rock chromite ore, etc.
Chrome Beneficiation Process
Chrome (chromite) ore beneficiation aims to extract chromium minerals from raw ore and remove impurities to obtain a high-quality concentrate. Usually, chrome ore contains a certain amount of iron, so gravity and magnetic separation combined with beneficiation is a relatively common process.
Key Process of Chrome Ore Beneficiation
- Gravity separation: The high density (4.2-4.8g/cm³) characteristics of chromite are used to separate low-density gangue (quartz, feldspar), with a recovery rate of more than 80%. Gravity concentration is used for processing high-density chromite, coarse-grained alluvial ore.
- Magnetic separation: Effectively remove clay and iron oxide impurities in laterite, and the grade of concentrate is increased to 45%-55%. Adapt to process fine-grained chromite and laterite.
- Flotation: Purify low-grade ores by positive flotation; remove silicon and improve quality by reverse flotation, and optimize the chromium-iron ratio. Suitable for the recovery of complex embedded ores, fine particles or associated silicate ores.
Our process is low-cost, energy-consuming, and less polluting. The combined process primarily involves washing, crushing, grinding, and core beneficiation (gravity separation, magnetic separation, and flotation), which is suitable for processing various high and low-grade ores. Contact our expert to custom turnkey chrome processing solutions based on ore characteristics (particle size, paragenetic minerals, degree of oxidation, etc.).
Chrome Ore Processing Plant
Alluvial Chrome Wash Plant
Chrome wash plant process flow
This is a complete 150 t/h chrome wash plant process, from washing, screening, spiral recovery, and other mining equipment. The main equipment and flow details are as follows:
1. Feeding: The excavator or truck sends raw ore into the raw material hopper, through a vibrating feeder, and evenly feeds the trommel screen. The vibrating feeder with grizzly bar, gap 75mm, and over 75mm rock will be sent to the waste stockpile via belt conveyor.
2. Chrome wash stage: 0-75mm material is sent to trommel screen for sieving out 0-2mm and 2-75mm. The belt conveyor sends 2-75mm material to the waste stockpile. Then, 0-2mm material is sent to the slurry tank.
3. Spiral separation: Chrome concentrate from the two stages of spiral chute groups is sent to the concentrated pool. Use the slurry pump to send 0-2mm to the first stage spiral chute group to separate chrome concentrate, middling, and tailing. And tailing enters the tailing pool. Middling from the first stage spiral chute group to the second stage spiral chute group by slurry pump to recover more concentrate.
advantages of JXSC alluvial chrome wash plant:
- 95%+ Recovery Rate
- 30% Cost Savings
- Machine 100% Factory Price
- Modular Designs Turnkey Solutions
Contact us to design reasonable small-to-large chrome wash plants to improve the grade of concentrate and maximize the mineral recovery rate.
Rock Chromite Processing solutions
This setup is a full rock chrome processing plant, from crushing, screening, grinding, gravity separation, and other mining equipment. The following is the specific equipment and process flow details.
Chromite Processing Plant Flow
1. Crushing stage: The vibrating feeder evenly feeds the raw ore into the primary jaw crusher. The primary jaw crusher is used to crush large pieces of chromium ore into smaller sizes, and its output enters the cone crusher for fine crushing, thereby improving the crushing effect.
2. Screening stage: The material is sent to the vibrating screen through the belt conveyor with iron remover, and more than 20mm material is returned to the cone crusher for crushing. Material with a 0-20mm particle size under the sieve enters the storage bin before entering the ball mill.
2. Grinding stage: The electromagnetic vibrating feeder and belt conveyor send the material into the ball mill and grind it to a 0-20mm fine powder. It is combined with a spiral classifier, and about 80% of the slurry overflowed by the classifier is 200 mesh powder. The oversized particles will be returned to the ball mill to form a closed loop mill.
3. Recovery stage: 200-mesh slurry is pumped into the spiral chute and shaking tables. The spiral chute is used for primary concentration, and all the heavy concentrate discharged from the secondary spiral group enters the shaker for re-concentration to obtain higher-grade ore.
advantages of JXSC Rock chrome processing plant:
- 95%+ Purity Output
- 98% Metal Recovery
- Modular Customized Process
- Advanced, Eco-friendly Technology
If higher-grade chrome concentrate is required, it can be considered to add a strong magnetic separator at the final stage. Contact us to customize small or large chromite process plants and get equipment latest price according to your ore situation.
Lateritic Chromite Processing Solutions
Lateritic chromite deposits, characterized by high iron content, clay-bound structures, and variable moisture (2-8%), often contain impurities such as nickel and iron. JXSC specializes in advanced laterite chromite extraction process designed to recover chromium efficiently from complex ores.
Lateritic Chromite Processing Plant Flow
1. Ore Pre-Treatment & Washing – High-pressure rotary scrubbers remove sticky clay coatings and reduce moisture to <3%, critical for downstream processes.
2. Crushing & screening – Three-stage crushing circuit with dual vibrating screens achieves 95% -3mm particle size.
3. Gravity separation – Spiral concentrators + shaking tables recover 82-88% Cr₂O₃.
4. Magnetic separation – High-intensity drum magnets upgrade concentrate to 44-48% Cr₂O₃.
5. Flotation optimization: Reverse flotation with anionic collectors removes residual silica.
6. Tailings management & water recycling – Produce dry tailings by thickener and filter press for safe disposal or repurposing.
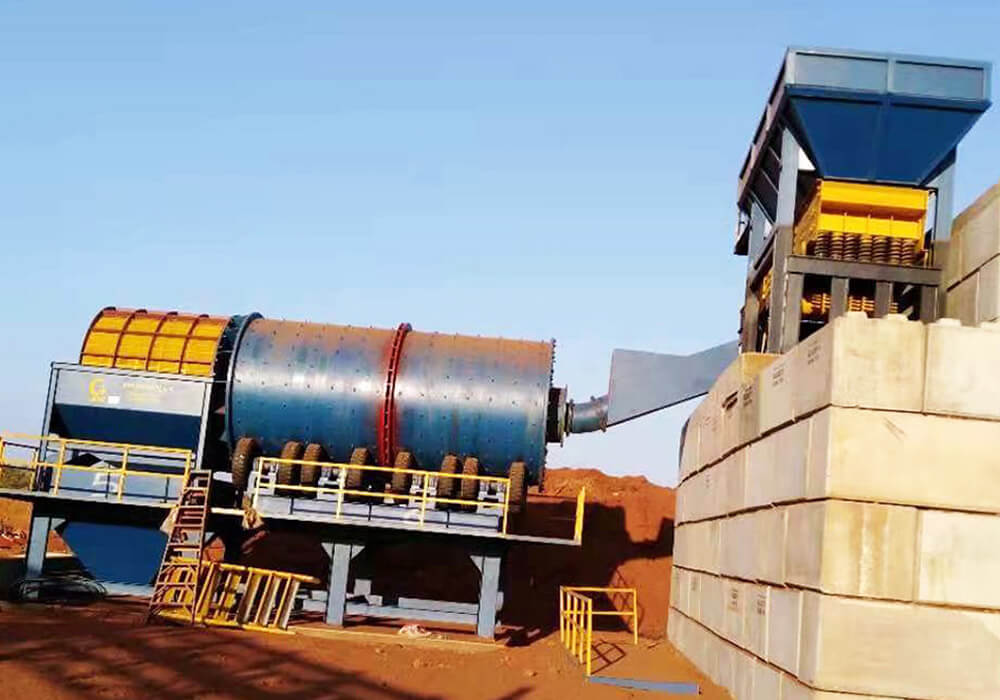
Advantages of JXSC Lateritic Chromite processing plant:
- 95% Recovery Rate.
- Low-Cost Modular Plants.
- 40% lower water use vs. competitors.
- Associated components such as nickel and iron are recycled simultaneously, increasing revenue by 25%.
Our main solution is to integrate gravity separation, magnetic separation or flotation process, which can be applied to various diversified laterite ores. Contact us to tailor-made small/ large laterite chromite processing plants according to your ore properties.
Chrome Plant Equipment
Contact Us Now
Ask us about mineral processing configuration and equipment quote! (No job, No investment)
Notice:
- We only provide mineral processing equipment and solutions; not buy and sell minerals/ ores/ materials.
- We do not recruit, don’t offer jobs, and are not interested in investments or partnerships.
- We value your privacy and keep your information safe.