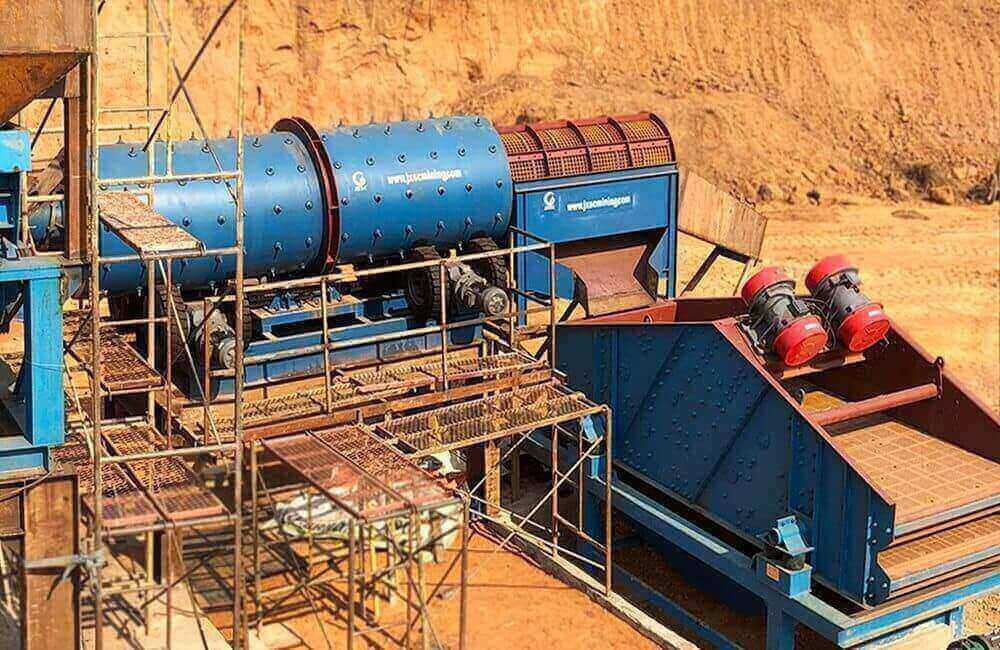
Diamond Wash Plant
Diamond wash plants, also known as diamond processing plants or diamond recovery plants, are specialized facilities designed for extracting and processing alluvial diamonds in rivers, beaches and diamond-rich deposits.
Diamond mining and processing involves complex operations that require compliance with various environmental and regulatory standards.
Diamond Mining Process
Diamonds often exist in the form of alluvial and also contain rock ore. Diamond processing plant is a facility used in the mining industry to separate diamonds from surrounding gravel or ore, usually by crushing, washing, screening, dense media and jig separation, magnetic separation, etc.
1. Crushing: Once the diamond-bearing ore is collected, it is transported to the primary crusher. The primary crusher is responsible for reducing the size of the ore into smaller, more manageable pieces.
2. Scrubbing and screening: Scrubbing and sieving the raw material removes clay, mud, and other contaminants that may adhere to the diamonds, helping to break down the material and release the diamonds.
3. Separation process
Jigging and Dense Media Separation (DMS) are used in diamond-washing processes to separate diamonds based on density differences from other impurities.
- Jig uses the action of water flow and vibration, diamonds and heavier impurities settle to the bottom or heavier layers, while lighter impurities float above the water flow.
- Dense Media Separation(DMS)sorting uses a suspension medium (such as heavy liquid or magnetic liquid) as the sorting medium. The raw ore is soaked in the suspension medium, and diamonds and heavier impurities will settle to the bottom, while lighter impurities float above the suspension medium.
The specific choice of which process to use depends on the characteristics of the raw ore, the expected separation effect and economic considerations. These two processes can also be combined in practical applications to improve the sorting effect and efficiency.
4. Diamond recovery: The heavy fraction containing the diamonds is further processed to recover the diamonds. Various methods can be employed, including X-ray sorting, grease tables, and hand sorting, depending on the size and quality of the diamonds.
5. Final grading: Recovered diamonds are sorted according to size, shape, color and clarity. They may undergo further grading and evaluation to determine their value and potential use in the diamond market.
Diamond processing Plant
alluvial diamond wash plant
JXSC supplied this alluvial diamond wash process plant. It’s also used for diamond washing and separation from kimberlite and other alluvial rocks.
The diamond wash plant main flow as follows:
- Feeding stage: First, use a vibrating feeder with sieve bars to remove large-sized stones.
- Washing stage: Smaller particles enter the trommel scrubbers to clean the diamond ore. The ore washing machine has two layers of screens of 2mm and 25mm, which mainly separate 2-25mm particles.
- Screening stage: Because the 2-25mm material is likely to be mixed with some particles of other sizes. Therefore, it is necessary to use a high-frequency vibrating screen to separate the 2-25mm material again and remove the -2mm and +25mm particles.
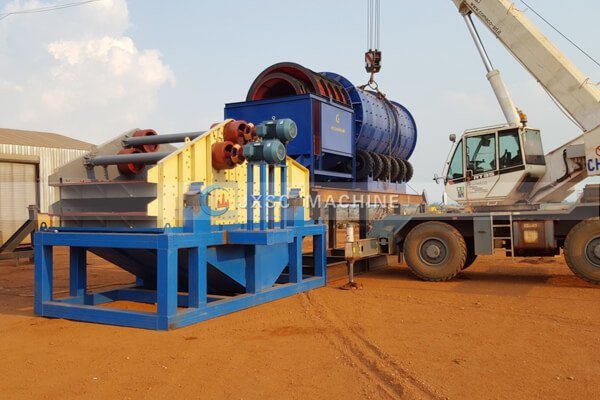
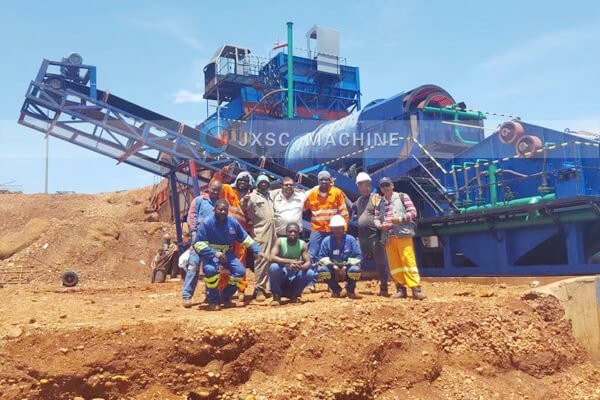
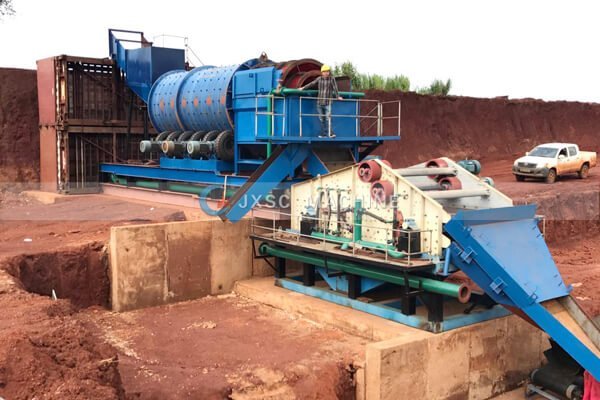
Note: If the material is not very sticky, the drum scrubber can be replaced with a trommel screen. If the concentrate needs to be concentrated, jig separators can be added later. Machine quantity is for reference only and depends on your production capacity.
The production capacity can be based on requirements such as 10tph, 50tph, 100tph, 200tph, etc. It is also possible to design a one-stop diamond washing plant (jig concentrator + trommel screen/rotary scrubber). Contact us to customized suitable diamond processing plants for you based on your detailed information.
Contact Us Now
Ask us about mineral processing configuration and equipment quote! (No job, No investment)
Notice:
- We only provide mineral processing equipment and solutions; not buy and sell minerals/ ores/ materials.
- We do not recruit, don’t offer jobs, and are not interested in investments or partnerships.
- We value your privacy and keep your information safe.