With the long-term mining and utilization of mineral resources, rich ore and coarse-grained mineral resources are increasingly scarce. It is difficult to effectively sort and recover ultra-coarse and fine-grained oxidized minerals, resulting in a large waste of mineral resources. Froth flotation is considered one of the most cost-effective methods in mineral processing. The comprehensive utilization of coarse and fine mineral resources usually adopts flotation process. However, sometime even if the mineral has reached the state of monomer dissociation, its flotation effect is not ideal.
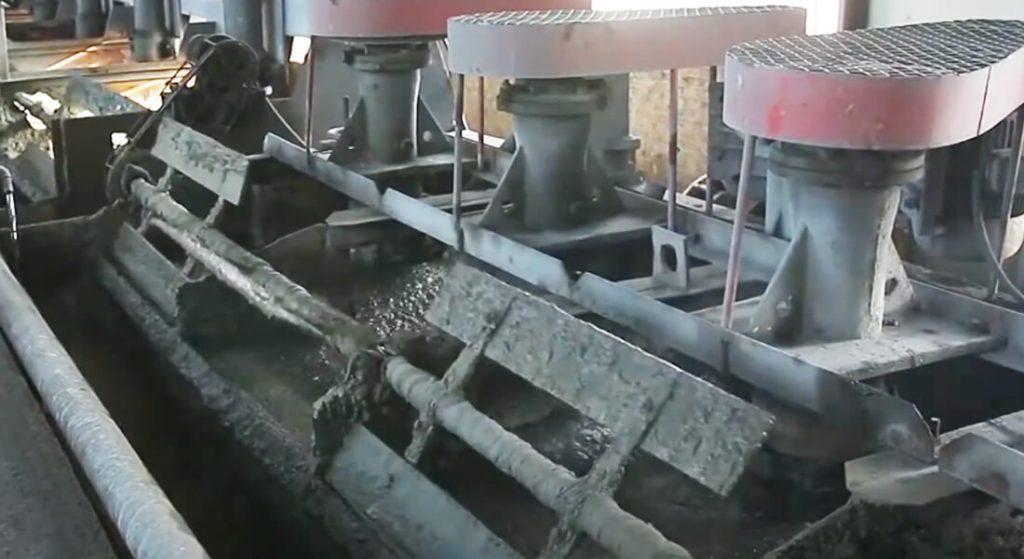
Coarse ore flotation
In conventional better flotation indicators, it is necessary to control the particle size of mineral particles to 10-10μm. Coarse particle flotation generally refers to direct flotation recovery of ore particles with a particle size more than 150 μm. Has the following advantages:
(1) Carry out pre-selection and discarding of tailings on raw ore, reduce the amount of ore processing, and can improve the grade of feed materials in the subsequent grinding and floating process, saving energy consumption;
(2) Coarse-grained flotation technology can be used to re-select coarse-grained tailings such as gravity separation tailings to improve resource utilization, reduce energy consumption, and reduce beneficiation costs;
(3) Many brittle minerals, such as graphite and molybdenite, are prone to over-crushing during the grinding process, which will not only cause energy waste, but also cause metal loss. Using coarse-grained flotation technology can directly select partially dissociated coarse-grained target minerals, avoiding over-grinding and improving recovery efficiency.
However, in the flotation of coarse-grained ore, the interaction between mineral particles and air bubbles is weak, and the flotation of coarse-grained ore is inhibited. The probability of adhesion between mineral particles and air bubbles is low. After the coarser particles collide with the air bubbles, the air bubbles will undergo a large deformation and recover immediately. This process will generate elastic vibration, which lowers the adhesion probability of particles and bubbles. The deformation of bubbles will also increase the gap between particles and bubbles, and many liquid phases will be mixed in the middle. If it is too late to discharge, the ore particles and air bubbles will not stick together. Generally, the degree of dissociation on the surface of minerals increases with the decrease in particle size, and a larger degree of dissociation provides more locations for the attachment of bubbles. Coarse-grained minerals have large particle sizes and small dissociation degrees.
Reasons for poor coarse-grained flotation:
For some unevenly distributed ore, the cost of grinding is high and the ore is easy to be over-grinded, so the rough grinding flotation process is often used. However, the coarse grains are relatively heavy, and are not easy to suspend in the flotation machine, and the chance of colliding with the air bubbles is reduced. After the coarse grains are attached to the air bubbles, they easily fall off from the air bubbles due to the strong shedding force. Therefore, under general process conditions, the effect of coarse-grained flotation is poor.
(1) Useful minerals and gangue minerals have not been fully separated;
(2) It is not easy to suspend in the flotation machine, and the probability of collision with air bubbles is reduced;
(3) Coarse particles move in the pulp and encounter turbulent vibration, causing them to fall off from the air bubbles.
Measures:
Intensive measures are usually taken when handling minerals that must be coarsely ground by flotation:
(1) Use collectors with strong collection capacity, and increase the number of collectors appropriately to enhance the fixation strength of particles and air bubbles. Sometimes auxiliary collectors such as non-polar oil are used together.
(2) Appropriately increase the amount of gas to provide more suitable air bubbles and increase the contact probability between mineral particles and air bubbles. Create conditions for the flotation of coarse particles.
(3) Select the flotation equipment suitable for coarse grain flotation. To prevent coarse particles from settling in the flotation equipment, reduce the depth of the flotation machine tank. Discharge the floating product as much as possible to shorten the buoyancy stroke of mineralization.
(4) Using a higher slurry concentration not only increases the chemical concentration, but also causes the particles to be subjected to a greater buoyancy force. However, it should be noted that when the pulp concentration is too high, the flotation process will deteriorate and the selectivity will be reduced.
Fine ore flotation
Fines generally refer to slimes smaller than 18 microns or smaller than 10 microns. Because fine-grained ore particles (slime) have the characteristics of small mass and large specific surface area, it causes a series of special behaviors of ore particles in the process of pulping and flotation.
For non-metallic minerals such as kaolin, bentonite, feldspar, barite, mica, illite, fluorspar, etc. On the one hand, the mineral has low hardness and is easy to muddy. On the other hand, impurity minerals such as iron and titanium have finer particle sizes, so the flotation particle size mostly belongs to the mud-grade particles mentioned in the flotation process. The quality of mud-level particles is small, the specific surface area is large, and the surface chain force is not saturated, which will have adverse effects on flotation.
Reasons for poor fine-grained flotation:
(1) The specific surface area of fine particles is large, and the surface energy is significantly increased. Under certain conditions, non-selective mutual condensation between different mineral surfaces is prone to occur. On the other hand, it is also because the surface energy of fine particles is large, and although the adsorption capacity of the reagent is high. But choose poor adsorption performance, which makes it difficult to selectively separate fine particles.
(2) Fine particles are small in size and are not easy to collide with air bubbles. The fine particle mass is small, when it collides with the air bubbles, it is difficult to overcome the resistance of the hydration layer between the ore particles and the air bubbles, and it is difficult to adhere to the air bubbles.
Measures:
(1) Add dispersant to prevent coagulation of fine particles and ensure full dispersion. Commonly used dispersants are water glass, sodium polyphosphate, sodium hydroxide (or sodium carbonate) and water glass.
(2) Reduce the pulp concentration and improve selectivity. When the pulp is thin, it can prevent the fine mud from contaminating the concentrated foam and reduce the viscosity of the pulp.
(3) Dosing in stages and in batches to reduce non-selective adsorption. Avoid adding it at one time, it will be absorbed by the slime.
(4) Before flotation, desliming is carried out on the processed materials, and sediment separation is carried out, and a special prescription for the flotation of ore slime is formulated.
To optimize the beneficiation recovery rate of coarse and fine ores, the beneficiation plant must comprehensively consider the design of flotation equipment, the special preparation of flotation agents and their application. Optimal flotation results depend on carefully balancing chemical, mechanical and operational factors. Our flotation process plant has low energy consumption, high recovery rate, and improved resource utilization. Choose the ore flotation solution suitable for the situation of the mineral processing plants, and customize reasonable mining equipment.