What is kaolinite clay?
Kaolin, kaolinite clay, also known as china clay, Guanyin clay, white eel mud, bentonite, bentonite, sweet clay, bentonite, clay, porcelain clay, white mud, is called kaolinite in mineralogy. It is usually composed of kaolinite, dickite, pearlite, halloysite and other kaolinite cluster minerals. It is also an important non-metallic mineral, clay and clay rock mainly composed of kaolinite clay minerals.
It can be used as raw materials in many industries, and is often used in fiberglass, sunscreen, agriculture, ceramics, building products, driveway sealants, paints and coatings, as well as roof tiles, soft rubber applications, papermaking, etc. In daily life, it has a particularly wide range of applications and is a very important “universal ore”.
Kaolinite Clay Beneficiation Process
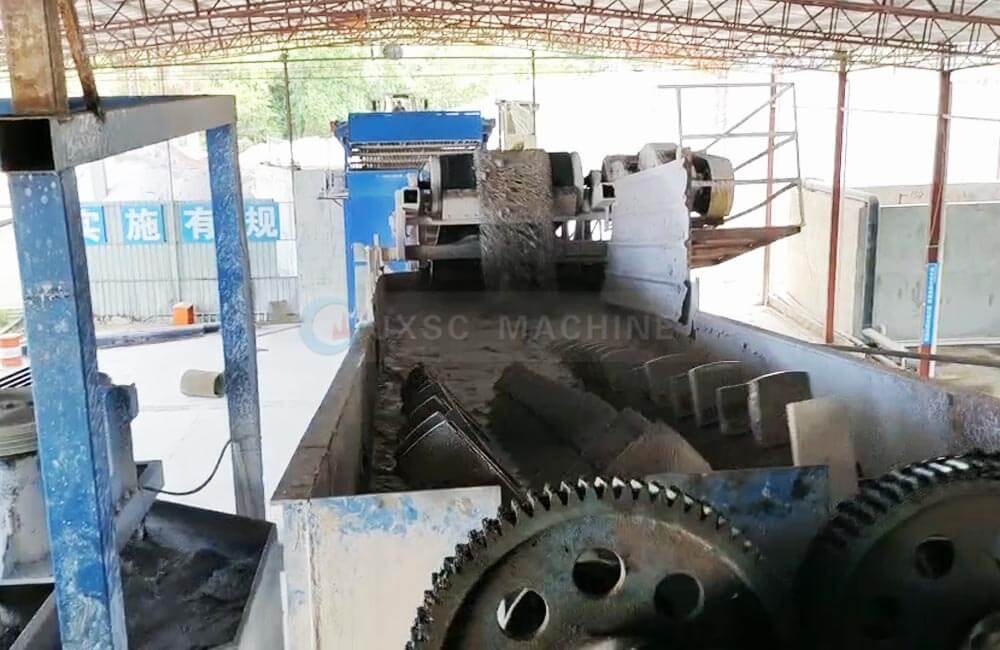
However, kaolinite clay is an inert, non-swelling, low-oil-absorption hydrated aluminum silicate mineral; it may contain quartz, feldspar, mica, iron, titanium minerals, etc., which are harmful impurities. Therefore, it is necessary to combine the beneficiation process for purification to be more suitable for various industrial uses. Kaolinite clay beneficiation mainly includes sand removal, iron removal, sulfur removal and other projects. There are two processes used in industrial production: dry and wet process. Usually, hard kaolin is produced by dry process and soft kaolin is produced by wet process. Specific kaolinite clay beneficiation processes include washing and sand removal, scrubbing, grading, gravity separation, magnetic separation, and flotation.
1. Washing and sand removal
First, the kaolin ore is stirred and dispersed in the presence of water and dispersant, so that the mineral is dissociated in the water in the form of granular monomers, and the particle size is measured in microns or even smaller. Usually, mechanical assistance such as drum ore washer, spiral sand washer, trough ore washer or drum screen is used to remove surface impurities.
2. Scrubbing (slurry adjustment)
Add appropriate dispersant into the stirring tank so that the raw ore, water and dispersant can be fully dispersed. While removing larger particles, the slurry of appropriate fineness can be prepared to meet the requirements of the next step of the mineral processing process.
3. Classification
Use the difference in size or density of mineral particles to separate minerals. Hydrocyclones, spiral classifiers or vibrating screens are often used for particle size classification, which can remove a large amount of coarse sand.
4. Gravity separation
Gravity separation mainly uses the density difference between the two to remove some coarse quartz and impurity minerals.
5. Magnetic separation
A method of separating mineral particles in a magnetic field by using the magnetic difference of minerals. Kaolin raw ore contains a small amount of iron-titanium minerals, which can be removed efficiently by a strong magnetic separator.
6. Flotation
It mainly adds a certain reagent in the flotation machine to adsorb fine impurity minerals onto the carrier, so that the impurities are separated to achieve the purpose of purification and whitening.
Kaolin Processing Plant
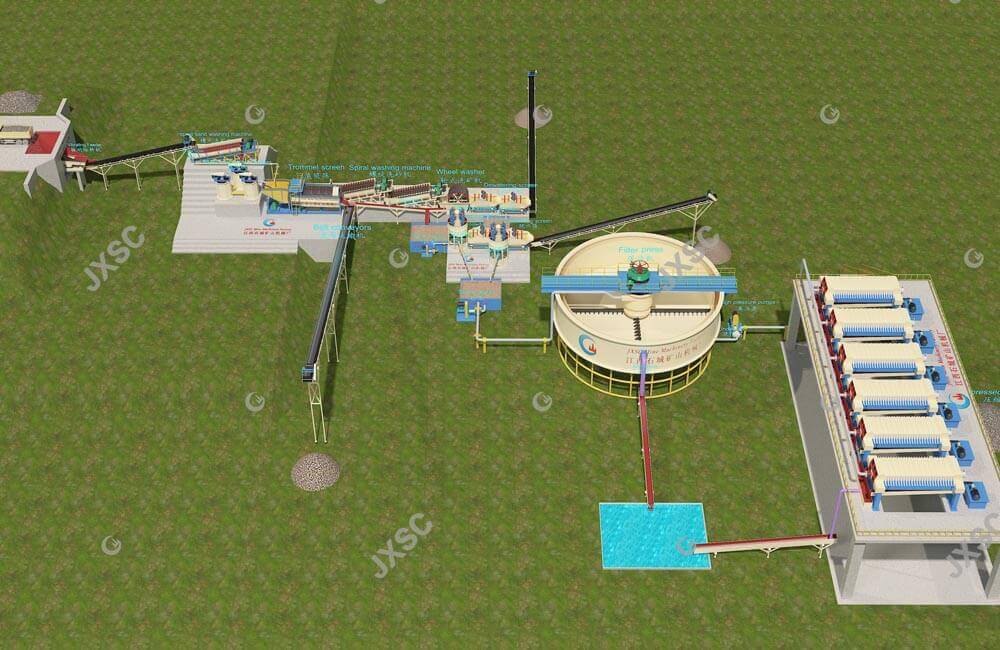
This is a complete kaolin processing plant, including a feeder, belt conveyor, spiral washer, attrition scrubber, trommel screen, wheel washer, dewatering screen, hydrocyclone, thickener, and filter press.
Flowchart Explanation Of Kaolinite clay processing plant
- Use a forklift or excavator to feed the raw materials to the hopper, through an electromagnetic vibrating feeder evenly feeds the raw materials to the belt conveyor, and the belt conveyor will send the raw materials to the spiral washer. The function of the spiral washer is to disperse, stir, and clean the agglomerated kaolin clay.
- Enter the attrition scrubber for further cleaning. The function of the attrition scrubber is to rub better and fall off the sticky slime from the kaolin
- After washing by the attrition scrubber, enter the trommel screen to sieve out big waste stones, which are sent to a far place by belt conveyor, and the material under the screen enters the double spiral sand washer
- The overflow of the first stage of the double spiral sand washing machine is kaolin concentrate, the underflow goes to the second stage of the spiral sand washer for washing, and the overflow of the second stage is kaolin concentrate. The underflow goes to the wheel sand washer.
- The overflow from the wheel sand washer is the concentrate; the underflow goes to the dewatering screen.
- The under-screen materials of the first dewatering screen are the kaolin concentrate, the over-screen materials go to the second dewatering screen for dehydration, and the over-screen materials of the second dewatering screen are coarse particle waste. Use a belt conveyor to send away, under the sieve is the concentrate. Kaolin concentrates under the screen of two dewatering screens in the No.2 pond. Kaolin Concentrate from the overflows of the two spiral sand washers and wheel sand washers into the No.1 pool.
- Use a slurry pump to send the No.1 pond concentrate into the No.1 cyclone group. The overflow of the cyclone group is kaolin concentrate, and the underflow flows to the dewatering screen for dehydration. Under the dewatering screen is a concentrate, which goes into the No.2 pond. Over the screen, materials are medium particles of waste, which are transported away with a belt conveyor.
- The under-screen concentrates of 4 dewatering screens are all in the No.2 pond and pumped to the No.2 hrdrocyclone group with a slurry pump. The underflow of the No.2 hyrdocyclone group goes to the dewatering screen, and the overflow is kaolin concentrate.
- Finally, the overflow of the two cyclone groups (kaolin concentrate) will flow to the final kaolin concentrate pool.
- Use a slurry pump to send kaolin to concentrate into the thickener for concentration, then through the slurry pump, send it to the filter press for dehydration, and finally, get the dry kaolin to concentrate without water.
The kaolin processing plant designed by JXSC has a high degree of mechanization, which can reduce labor and reduce the labor intensity of operating staff. The entire beneficiation process uses less water, effectively protects groundwater resources, and reduces a large amount of waste gas emissions, which promotes the protection of the ecological environment. Each mineral has different properties, it is recommended to conduct beneficiation experiments first and then decide on the final beneficiation plant design. We support customized kaolin beneficiation solutions and equipment, contact us for more details!