Rutile is relatively pure titanium dioxide, which generally contains more than 95% titanium dioxide. It is an important mineral raw material for extracting titanium, but it has less reserves in the earth’s crust. Separating most of the iron components in ilmenite produces a titanium-rich raw material that is the same as natural rutile in terms of composition and structural properties, and is a high-quality substitute for natural rutile. Ilmenite is the basic raw material for the production of artificial rutile. Mainly due to the depletion of natural rutile reserves, especially high-grade rutile. Although most rutile and hematite are wrapped in each other and are closely related, sorting is extremely difficult. However, it is a new idea to continuously optimize the technical route of sorting rutile, quartz, mica and other minerals. In order to improve resource utilization and economic benefits, reduce the backlog of middle ore and tailings and environmental pollution. After more than 30 years of mineral processing experience, JXSC can enrich qualified high-grade concentrates for rutile processing.
About Rutile Ore
Rutile is one of the main minerals containing titanium. It is brittle, with a hardness of 6-6.5 and a density of 4.2-4.3g/cm3. Those rich in iron, niobium, and tantalum will increase in density, and the higher ones can reach more than 5.5g/cm3. It can be dissolved in hot phosphoric acid. Adding sodium peroxide after cooling and diluting can turn the solution into yellowish brown (reaction of titanium). Rutile can be produced in gneiss, pegmatite, eclogite (flash) rock mass and placer.
Uses of rutile: Rutile itself is one of the necessary raw materials for high-grade welding electrodes, and it is also the best raw material for producing rutile titanium dioxide. Because of its high-temperature resistance, low-temperature resistance, corrosion resistance, high strength, small specific gravity and other properties. It is widely used in military aviation, aerospace, navigation, machinery, chemical industry, seawater desalination, etc.
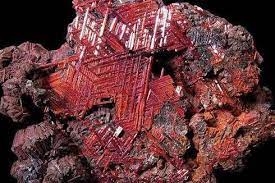
- Natural rutile is relatively pure titanium dioxide, generally containing more than 95% titanium dioxide. It is an important mineral raw material for extracting titanium, but it has less reserves in the earth’s crust.
- Artificial rutile refers to the use of chemical processing methods. Ilmenite is the most important titanium ore and the main source of titanium dioxide. A titanium-rich raw material with the same composition and structural properties as natural rutile is produced by separating most of the iron components in ilmenite.
86% of the natural rutile mines are primary mines, with low grade, fine particle size, complex mineral composition and distribution relationship. This determines that rutile ore processing should adopt a combined beneficiation process.
Rutile beneficiation process
Usually, rutile ore exists in beach sand and ilmenite, and is associated with various other minerals. Such as magnetite, hematite, quartz, feldspar, mica, hornblende, graystone, dareite, garnet, chromite, apatite, etc. Generally, gravity separation, magnetic separation, electric separation and flotation are used for separation.
1. Gravity separation
The density of rutile (TiOz) is 4200 kg/m3, and it often coexists with quartz, tourmaline, garnet, etc., and can be enriched by gravity. This method is generally used for roughing of titanium-containing placer or crushed titanium-containing primary ore. The purpose formula removes most of the gangue minerals and enriches the useful minerals.
Since the density of titanium-containing minerals is generally greater than 4g/cm3, most of the gangue minerals with a density less than 3g/cm3 are removed by gravity separation during the roughing of the placer. In the separation of rutile ore, gravity separation is usually used for desliming, tailings and other operations. A trommel scrubber or a hydrocyclone is often used to discard most of the slime. Using spiral chute, shaker, etc. can remove gangue minerals such as quartz, tourmaline, garnet and white titanium in rutile ore, and realize the enrichment of coarse-grained rutile.
2. magnetic separation
The magnetic separation method is widely used in the selection of titanium-containing minerals. We can use a weak magnetic field magnetic separator to separate magnetite, ilmenite and other magnetic products from rough concentrate. In order to separate ilmenite from other non-magnetic minerals, strong magnetic separation can be used. In industry, both dry and wet magnetic separation are used.
3. Electrostatic beneficiation
It mainly uses the difference in conductivity between different minerals in the titanium-containing coarse concentrate for separation, such as the separation of rutile, zircon, monazite, etc. There are three types of electric separator grades used: roll type, plate type and sieve plate type.
4. Flotation Separation
It is mainly used for sorting fine-grained titanium-containing ores. Commonly used flotation agents are: sulfuric acid, tall oil, oleic acid, diesel oil and emulsifiers.
Rutile Processing Plant
1. Crushing: The shape of the natural rutile ore is relatively large, so the jaw crusher must be used for preliminary crushing, and a vibrating feeder is also needed at this time. The vibrating feeder is used to send the material into the jaw crusher evenly, continuously, and quantitatively, and the rutile material that meets the feeding requirements of the ball mill after coarse crushing enters the rutile ball mill for grinding and crushing.
2. Grinding: The rutile ore minerals ground by the ball mill are classified by the spiral polarizer. The spiral classifier cleans and classifies the rutile material by virtue of the principle that the specific gravity of the solid particles is different and the sedimentation speed in the liquid is different.
3. Separation: Generally, magnetic separation, electric separation, gravity separation and flotation are used, and the configuration is staggered according to the different mineral properties.
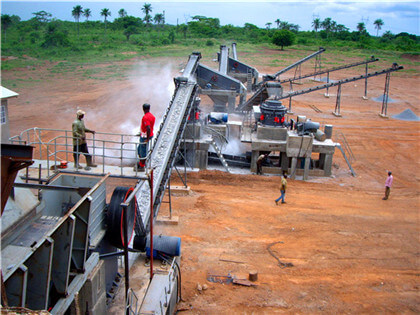
Our high-grade rutile beneficiation process is also suitable for the separation of high-grade rutile concentrate from titanium and beach sand processing. Its seaside placer is composed of ilmenite, zircon, rutile, monazite and other minerals. The rough concentrate is re-selected with a hydraulic shaker to separate the heavy minerals of rutile and cassiterite from a small amount of light minerals of quartzite. Gravity separation concentrate is magnetically separated by induction roller strong magnetic separator to separate ilmenite and monazite magnetic impurities. After magnetic separation, non-magnetic products are preheated in the hopper to above 60°C, and then electrostatic plate-type high-voltage electric separation is used to obtain high-grade rutile concentrate. JXSC supports customized mineral processing plant with good separation effect, high recovery rate and significant economic benefits.