Flotation is a material separation method with air bubbles as the medium, also known as froth flotation. It is a beneficiation method with wide application and good effect in the separation of fine-grained materials. It is suitable for the separation of metal minerals and non-metal minerals, and can also be used for the recovery, separation and purification of many raw materials, products or wastes in metallurgy, papermaking, agriculture, food, medicine, microorganisms, environmental protection, petroleum, water treatment and other industries. Among them, more than 80% of the separation process of non-ferrous metal mineral resources is realized by froth flotation. Flotation is at the heart of mineral processing plant operations, the solution for maximizing recovery and profitability.
Flotation process
The surface properties of minerals have differences in hydrophobicity and hydrophilicity. Flotation uses this difference to separate minerals in the gas-liquid-solid three-phase interface system. This process generally includes 4 processes:
Grinding and dissociation: the ore is ground first to dissociate useful minerals from other minerals or gangue minerals;
Slurry adjustment and dosing: adjust the pulp concentration to meet the flotation requirements, and add the required flotation reagents to improve efficiency;
Flotation separation: the pulp is aerated and floated in the flotation machine to complete the separation of minerals;
Product treatment: After flotation, foam products and tailings products are dehydrated and separated.
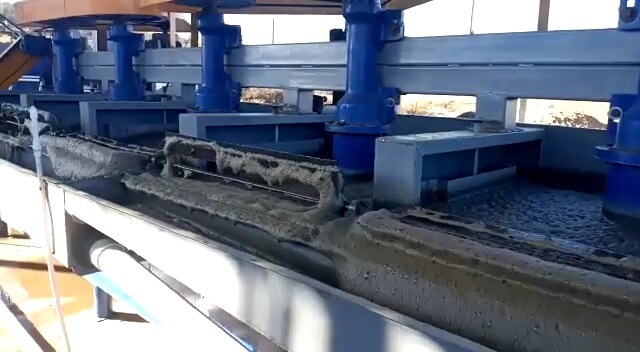
At present, the basic processes of common ore flotation plants include priority flotation, mixed flotation, partial mixed priority flotation, equal flotation, branch series flow, flash flotation, and fast flotation processes.
1. Priority flotation
When the ore to be processed contains polymetallic ores with two or more useful components, one of the minerals is first floated and the other is suppressed. Then activate and float another mineral, this process of sequentially recovering useful minerals is the priority flotation process. Generally, it is suitable for useful minerals with coarse particle size, high content of useful minerals in the ore, or large differences in buoyancy.
2. Mixed flotation
Mixed flotation is to select various useful minerals together when the processed ore contains two or more minerals, and then separate them one by one. It is mainly used for scheelite flotation, polymetallic ores with low mineral grade or useful minerals embedded in aggregates.
3. Partial mixed-priority flotation
First mix some useful minerals in the flotation ore, and suppress other minerals. Then activate other useful minerals that are inhibited in flotation, and float the mixed concentrate that was first floated out again. Applicable to general minerals where there are several useful minerals with similar floatability and different floatability conditions, partial mixing priority flotation process can be used. For example, copper molybdenum, copper lead, copper zinc, lead zinc and other minerals in raw ore.
4. Equal flotation
According to the equivalence or similarity of mineral buoyancy, the minerals to be recovered are divided into two parts which are easy to float and difficult to float, and then separated by flotation in the order of easy and difficult. It is suitable for processing the same kind of minerals, including complex polymetallic sulfide ores that are easy to float and hard to float. For example: in a certain sulfide ore, useful minerals include galena, sphalerite, and pyrite, among which, sphalerite has two minerals that are relatively easy to float and difficult to float.
5. Asynchronous flotation
The process is mainly applied according to the difference in ore properties and the special requirements of the concentrator for products. It is suitable for the flotation of minerals whose raw ore is mainly lead and less sulfur.
6. Branch streaming flotation
Branched series flow flotation is to divide the raw ore pulp into two or more branches, and the foam of the former roughing is combined with the raw ore pulp of the latter. Then they are properly “connected in series” and equipped with corresponding pharmaceutical systems. But it is only suitable for concentrators with more than two flotation series.
7. Flash flotation
The useful minerals that have been dissociated in the grinding process are quickly floated out as concentrates. To prevent it from re-entering the grinding circuit to cause over-grinding and sliming, and to realize the beneficiation principle of “capable harvest and early harvest”. It is mainly suitable for non-ferrous metal, sulfide ores processing,containing precious metals with uneven distribution particle size.
8. Fast flotation
According to the different particles of the target minerals, especially the difference in flotation speed between the dissociated minerals and the associated minerals, the shorter flotation time is used to preferentially float the part of the minerals with the fastest flotation speed. It is suitable for the selected materials whose target mineral particle size distribution is uneven and needs to be regrinded for coarse concentrate or medium ore.
Ore Flotation Processing plant
Flotation process equipment is mainly composed of jaw crusher, ball mill, classifier, mixing tank, flotation machine, thickener and dryer and other main equipment. It is used for sorting non-ferrous metals such as copper, zinc, lead, nickel, gold, etc. It can also be used for rough selection and selection of ferrous metals and non-metals.
1. Crushing and screening: The raw ore is transported to the mine warehouse by the mine car for storage, and then sent to the jaw crusher through the vibration feeding machine for a stage of crushing. The crushed material is transported to the vibrating screen for screening. The screened product is transported back to the fine jaw crusher through the belt for the second stage of crushing.
2. Grinding and classification: The ore in the ore bin is sent to the ball mill for grinding by the electric vibration feeder, and the grinding product is sent to the spiral classifier for classification. The underflow of the classifier returns to the ball mill for regrinding, and the overflow is transported to the stirring tank by the pipeline for stirring.
3. Beneficiation stage: the stirred product enters the flotation machine for flotation, and the ore pulp undergoes a roughing, a second beneficiation, and a scavenging to obtain a concentrate.
4. Concentrate dehydration: The concentrate is transported to the deep-cone multi-cone high-efficiency thickener for concentration, and the overflow water is returned to production for reuse. The concentrated underflow enters the plate filter press for filtration, and the belt conveyor transports the filter press to the concentrate bin for storage.
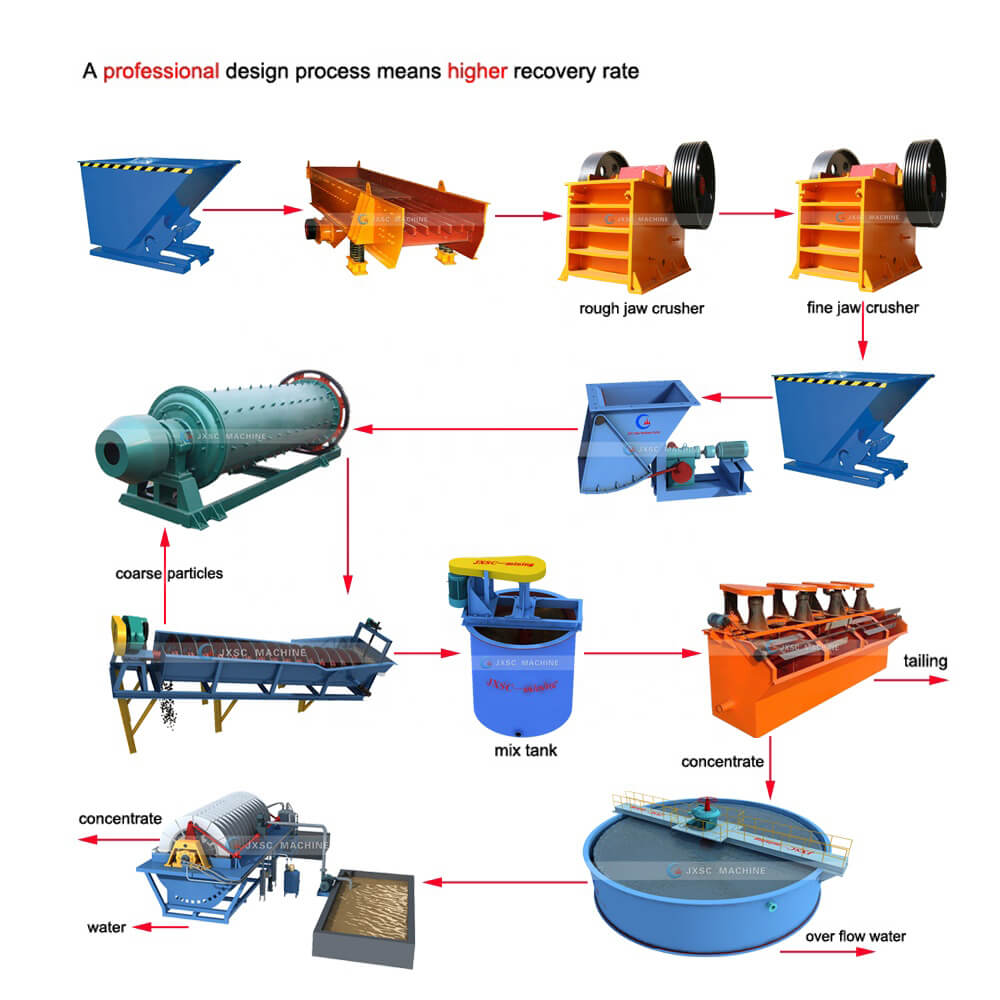
All of our ore flotation solutions address your process holistically, helping you optimize your flotation circuits for higher selectivity, recovery, taste and ultimately cost efficiency. Flotation separation is one of the most important processes, and it is widely used. The beneficiation process of general minerals can be clearly seen in the flotation flow chart designed according to the standard process, and the flotation machine is an important equipment. The most important step in the process is the selection and operation of flotation agents, so as to achieve a good beneficiation purpose. According to the standard flow process design, JXSC complete mining equipment can be customized according to customer requirements and different optimizations.