Circular Vibrating Screen VS Linear Screen
introduction
There are many types of vibrating screens, which can be divided into circular vibrating screens and linear screens according to the movement trajectory of materials. These two types are commonly used screening equipment.
A few days ago, a customer left a message asking about the difference between them and wanted to know how to choose. Here we will make a comparison from 9 points to help customers quickly distinguish between circular vibrating screen and linear screen.
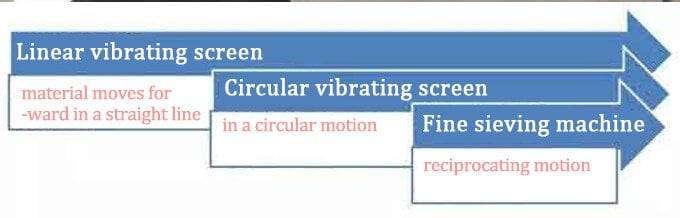
There is no essential difference between the style and structure of the circular vibrating screen and the linear vibrating screen. The materials are screened through the vibration of the screen surface, but the difference in the vibration track will directly affect the screening purpose.
Before comparing the circular vibrating screen and the linear vibrating screen, let’s take a look at their respective working principles.
Circular vibrating screen
The motor drives the eccentric block of the vibration exciter to rotate at a high speed through the V-belt, which produces a large centrifugal inertial force, which stimulates the screen box to produce a circular motion with a certain amplitude. The material on the screen is affected by the impulse transmitted by the screen box on the inclined screen surface. A continuous throwing motion is produced, and the particles smaller than the sieve hole are passed through the sieve when the material meets the screen surface, thereby achieving classification.
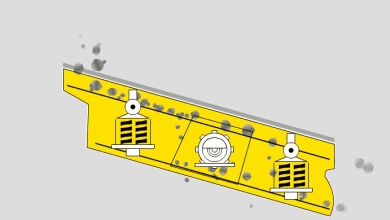
Linear vibrating screen
Vibration motor is used as the source of vibration, so that the material is thrown up on the screen while moving forward in a straight line. The material enters the inlet of the screening machine evenly from the feeder and produces several specifications of screens through the multi-layer screen. The upper and lower objects are discharged from their respective outlets.
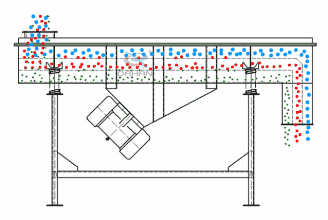
comparison
1. Movement track
The material on the circular vibrating screen moves in a circular motion, and the material on the linear screen moves forward in a straight line.
2. Vibration exciter
The circular vibrating screen is also called a single-shaft vibrating screen because the exciter is a shaft and uses an inertial motor to work. The linear vibrating screen is composed of two shafts and works on the principle of vibration motor excitation, so it is also called double Shaft vibrating screen.
3. Hole blocking phenomenon
The material of the circular vibrating screen moves in a parabolic circular trajectory on the screen surface, so that the material is dispersed as much as possible, thereby improving the bounce force of the material, and the material stuck in the screen hole can also jump out, reducing the hole blocking phenomenon.
4. Installation and layout
Due to the small inclination of the screen surface, the linear vibrating screen reduces the height of the screen, which is convenient for process layout.
5. Screen surface inclination
According to the particle size of the material, the circular vibrating screen can change the inclination of the screen surface, thereby changing the moving speed of the material along the screen surface and increasing the processing capacity of the screen machine. Generally speaking, the inclination angle of the screen surface of the linear vibrating screen in production is small.
6. Material
Under normal circumstances, the circular vibrating screen is made of thick plates, and the box is made of manganese steel to resist the impact of materials during the screening process. The materials for the production of linear vibrating screens are mainly light plates or stainless steel plates.
7. Applicable fields
The circular vibrating screen mainly screens materials with high specific gravity, large particles and high hardness, and is widely used in mining industries such as mines, coal, and quarries.
Linear screens mainly screen fine particles, light specific gravity, and low-hardness materials, mainly dry powder, fine granular or micro-powder materials, and are generally used in food, chemical, building materials, and pharmaceutical industries.
8. Processing capacity
For the circular vibrating screen, because the exciter is arranged above the center of gravity of the screen box, the elliptical long axis at both ends of the screen box is in a lower eight shape, and the upper end of the elliptical long axis at the feeding end faces the discharge direction, which is beneficial to the rapid material The upper end of the elliptical long axis of the discharge end is opposite to the discharge direction, which reduces the movement speed of the material, which is conducive to the penetration of difficult-to-screen materials, and the arc-shaped screen surface increases the effective area of the screen, thereby improving its Processing power.
In addition, for materials that are difficult to screen, the circular vibrating screen can turn the main shaft, so that the direction of vibration is opposite to the direction of movement of the material, and the moving speed of the material along the screen surface is reduced (when the screen surface inclination is the same as the spindle speed) to improve screening effectiveness.
9. Environmental protection
The linear vibrating screen can adopt a fully enclosed structure without dust spillage, which is more conducive to environmental protection.
conclusion
In the field of mining and quarrying, circular vibrating screens are more widely used. In actual production, the choice of circular vibrating screen or linear vibrating screen mainly depends on the type of material handled by the user and the application field. The screening requirements are different, the selected equipment will be different.
Products
Send Us A Message
More Posts
related materials
- Placer Gold Process Plant
- Diamond Mining Process
- Silver Flotation Process
- Gold Flotation Process
- Gold CIL Processing Plant
- Gold CIP Processing Plant
- Dense Media Separation(DMS) Process
- Copper Processing Plant
- Lead Zinc Ore Processing
- Tungsten Ore Processing
- Magnetite Separation Plant
- Manganese Ore Processing
- Chrome Processing Plant
- Quartz Beneficiation Plant
- Phosphate Rock Processing
- Fluorite Ore Processing
- Tantalum Niobium Ore Processing
- Tin Ore Processing Plant
- Titanium Beneficiation Plant
- Graphite Ore Processing
- Hematite Separation Process
- Iron Ore Beneficiation Plant
- Kaolin Processing Plant
- Limonite Ore Dressing
- Lithium Processing Plant
- Magnetite Separation Plant
- Molybdenum Flotation Process
- Cobalt Ore Processing
- Nickel Ore Beneficiation
- Antimony Ore Processing
- Barite Ore Beneficiation
- Feldspar Processing Plant
- Coal Washing Process
- Beach Sand Beneficiation Plant
- Tailings Processing
- Chrome Wash Plant