Alluvial and rock gold beneficiation methods are critical to maximizing the extraction and recovery of gold from various ores. These methods involve physical, chemical and mechanical processes to separate gold particles from surrounding impurities.
Alluvial gold beneficiation methods
Placer/alluvial gold usually exists as fine gold particles in geological environments such as rivers, river beds, gravel, and dunes. These gold particles typically settle at the bottom of the sediment due to their high density. Alluvial gold is generally coarse with varying particle sizes and can be relatively easily separated by physical methods such as gravity beneficiation, screening and washing.
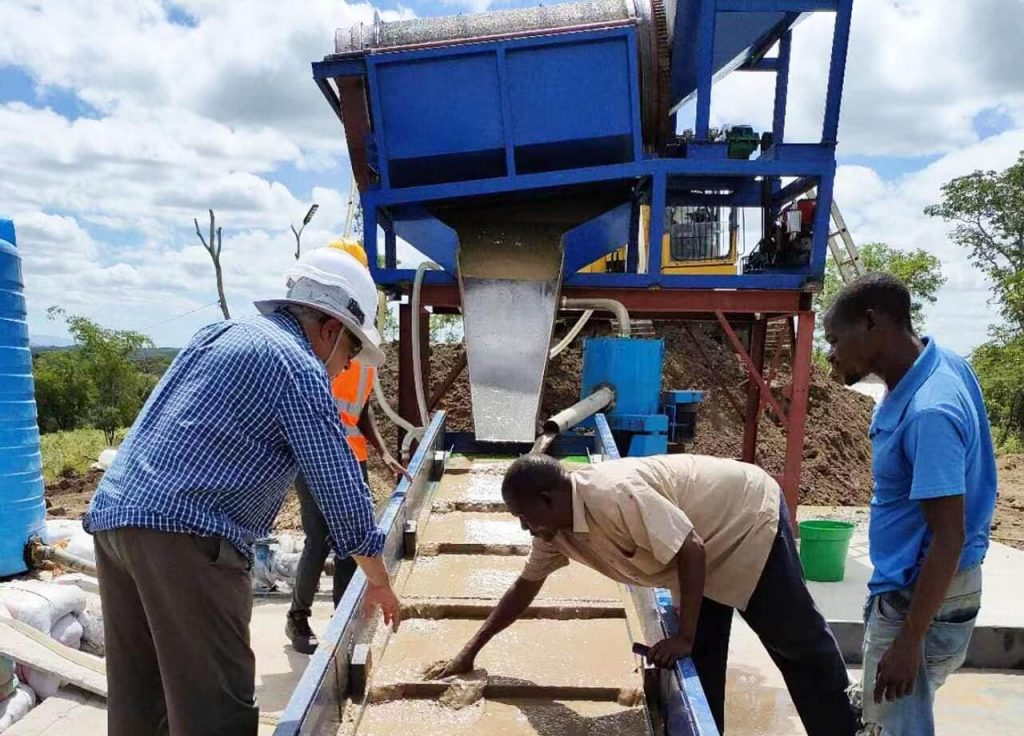
- Gravity Separation: Alluvial gold is generally heavier and can be separated through gravity separation equipment, including shaking tables, spiral chutes, jig separators, centrifugal concentrators, etc. These devices do this by separating placer gold from other impurities.
- Flotation: If alluvial gold contains sulfide minerals, flotation can be used. In the flotation process, alluvial gold is immersed in water containing a foaming agent, and then the gold particles are separated from impurities through the action of bubbles.
- Screening and Washing: Alluvial gold is usually found in river beds, river banks, or sand dunes. The most common method is to collect placer gold deposited on river beds in open pit mines. This usually involves using gold mining tools such as gold pans, skips, or sand separators to separate the gold particles through screening, washing and sedimentation.
- Cyanidation: Some special chemical methods can extract gold from alluvial gold. However, these methods require specialized knowledge and equipment and must be performed cautiously.
Rock gold beneficiation methods
Rock gold is an ore embedded in hard rock in the form of fine grains, tiny particles or refinements, usually found in veins, gangue, and sulfide minerals. The adhesion of gold particles to rocks is very strong and usually requires more complex extraction methods, including a combination of chemical and physical methods such as crushing, grinding, cyanide leaching, oxide ore leaching, carbon leaching, etc. This is because the gold particles in rock gold are typically smaller and require multiple processing steps to extract fully.
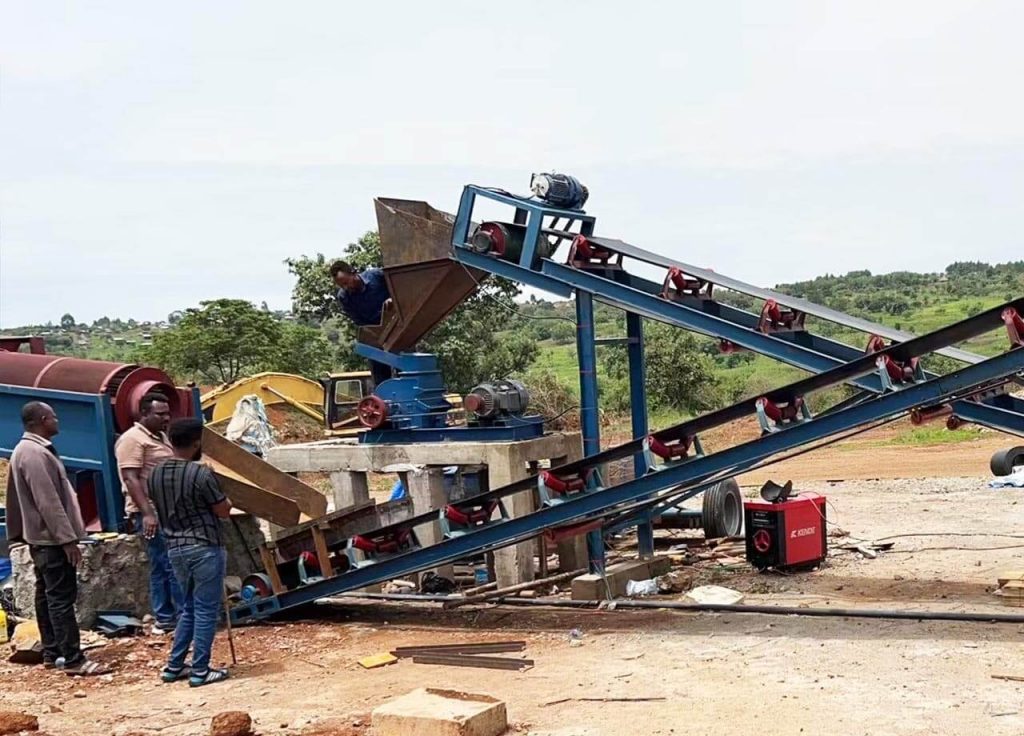
- Crushing and Grinding: Rock gold is often embedded in hard rock, and the rock first needs to be ground and broken to release the gold ore.
- Gravity separation: Similar to placer gold, rock gold can also be initially separated by gravity separation. This can be achieved using vibration tables, centrifuges, spiral chutes and other equipment.
- Flotation: The flotation method can be used if the rock gold ore contains sulfide minerals. This usually involves grinding the rock gold ore and then using flotation equipment to separate the gold ore.
- Cyanidation method: Cyanidation can also be used for rock gold ores containing sulfur minerals. This involves exposing gold ore to a cyanide solution to dissolve the gold and subsequently extracting the gold from the solution through an electrolysis or adsorption process.
- Carbon leaching (CIP): gold carbon-in-pulp is a common extraction method that involves contacting gold with activated carbon, adsorbing the gold from a gold-containing solution onto the carbon, and extracting the gold from the carbon.
Gold Beneficiation Plant
50 TPH alluvial gold and rock gold processing plant
- The rock stone part is crushed around 5 tons per hour, and the later stage for grinding & gold separation of the rock stone part is about 3 tons per hour.
- The raw ore feeds into the trommel screen for washing a few little clays and can separate the gravel or stone, which needs to be crushed and ground to get the inside gold; the separated rock can be transferred to the next jaw crusher by the belt conveyor. For this flowsheet, the trommel screen is designed with mobile wheels, which can easily move from one site to another. Or you can choose a stationary one. The trommel screen is designed with a layered screen.
- The bigger than 6 mm goes to the jaw crusher(the maximum input stone shall be less than 210mm), which can crush the big rock into smaller parties around 40-60mm.
- The output from the jaw crusher goes to the hammer crusher via the belt conveyor. The hammer crusher crushes the smaller stones less than 10mm into a wet pan mill for grinding.
- The wet pan mill grinds the 10mm gravel stone less than 1mm to release the inside gold.
- Since the grinding is 3 tons per hour, two shaking tables are required for the gold separation.
- The smaller size 6mm from the trommel screen, goes to a slurry pump; use two slurry pumps to pump the slurry into the gold concentrator to catch the gold first. The concentrates from the gold concentrator go to the shaking table to separate the gold again to update the recovery rate.
- Each gold concentrator matches one sluice box for the tailings on this part—and two shaking tables for matching each gold concentrator accordingly.
- After shaking the table, all the collected gold concentrates will be sent to the gold smelting furnace to melt the gold bar.
Understanding the various alluvial and rock gold beneficiation methods provides valuable insights into maximizing gold extraction rates. Each method has advantages and limitations, depending on factors such as ore type and particle size distribution. Before undertaking any gold beneficiation process, detailed exploration and experimental studies should be conducted to determine the most suitable processing method. If you plan to extract gold from ore, it is recommended to consult with JXSC‘s professional mining engineers to ensure safe and efficient operations.