Fluorite is a non-metallic raw material with strategic significance, mainly used in the three major industries of metallurgy, chemical industry and building materials, followed by light industry, optics, sculpture and national defense industry. In production practice, fluorite ore beneficiation methods mainly include hand selection, gravity separation and flotation. Among them, the hand separation method is often used as an auxiliary means, and the gravity separation method is suitable for producing metallurgical grade lump ore or as a gravity separation operation for the fluorite flotation process. Because of the depletion of fluorite ore and the intercalation of fluorite and gangue, flotation has become the primary beneficiation method for separating fluorite and gangue minerals. The purity of fluorite affects the use of fluorite, beneficiation and flotation technology directly determine the grade and recovery rate of fluorite. Today, with increasingly stringent environmental protection requirements, fluorite flotation also promotes the improvement and application of fluorite gravity separation technology and equipment to a certain extent.
Types of Fluorite Ore
According to the different gangue minerals, fluorite ore is divided into quartz-type fluorspar ore, carbonate-type fluorspar ore, barite-type fluorspar ore and sulfide-type fluorspar ore.
Quartz-type fluorite ore: the main minerals are fluorite and quartz, and the fluorite content can reach 80% to 90%. Contains small amounts of calcite, barite and sulfide. Quartz-type fluorite ore mainly comprises fluorite (range up to about 85%) and quartz, with only a small amount of calcite, barite and sulfide. The key to sorting is mainly to reduce silicon in the concentrate. To separate quartz from fluorspar, quartz and fluorspar monomers must be dissociated through grinding, so grinding is an essential factor affecting quartz-type fluorspar flotation. The most reasonable method is to adopt a staged grinding process, which can reduce the silicon content in the fluorspar concentrate after flotation and increase the recovery rate of the fluorspar concentrate.
Carbonate fluorite ore: the main minerals are fluorite and calcite. The calcite content can reach more than 30%, with a small amount of quartz, sometimes forming a quartz-calcite-fluorite type ore.
Barite type fluorite ore: the main minerals are barite and fluorite, and the barite content reaches 10% to 40%. This type of ore is often accompanied by sulfides such as pyrite, galena, sphalerite, etc. Sometimes, the quartz content increases to form a quartz-barite-fluorite type ore. The flotation of barite-type fluorite ore generally first uses a mixed flotation process and Na2CO3 to adjust the pH value of the slurry and use oleic acid and water glass as collectors and inhibitors, respectively, to obtain fluorite and barite. The concentrate is mixed and the barite and fluorite are separated by flotation.
Sulfide-type fluorite ore: Its mineral composition is the same as quartz-fluorite. Still, it contains more metal sulfides; the lead and zinc content can sometimes reach industrial grades. For sulfide ore-type fluorspar ores, sulfide ore collectors can generally select metal sulfide minerals first. Then, fatty acid collectors can recover fluorspar from flotation tailings. In addition, roasting, leaching, and other processes can also be used to extract valuable metals and decompose fluorspar. The process flow is relatively simple and can produce high-quality fluorspar products while comprehensively recycling valuable metals.
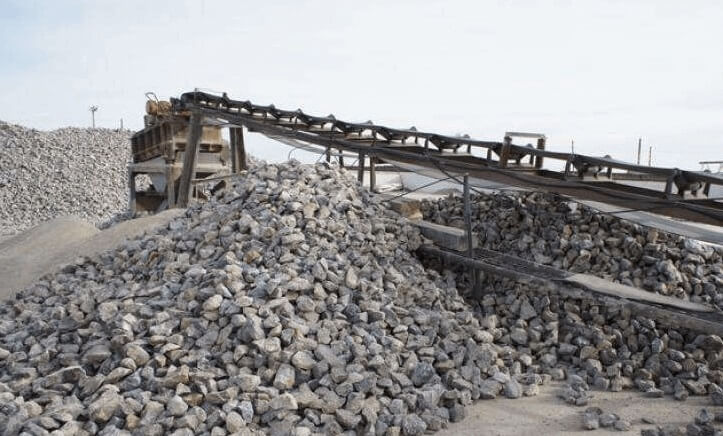
influencing factors of Fluorite Ore flotation
We focus on the complex symbiotic relationship and ore properties between fluorite ore and various gangue minerals such as calcite, barite, quartz, and sulfide. Usually, the fluorite ore flotation beneficiation effect can be improved by improving the above factors from the perspectives of grinding fineness, slurry temperature, flotation reagents, slurry liquid level, slurry pH value, water quality, and flotation process.
Comprehensively analyze the ore’s properties, combine the dressing plant’s actual situation and the investment budget to customize a scientific flotation process, and follow a reasonable flotation reagent system to obtain ideal economic benefits and mineral processing indicators.
1. Suitable grinding fineness
The appropriate grinding fineness must be selected based on the embedded particle size of the effective minerals so that the effective minerals and gangue are usually dissociated and the concatenation of fluorite ore and gangue minerals is minimized. It is necessary to avoid over-grinding of the material in the fluorite flotation process if the ore grinding fineness is too fine.
2. Properly increase the slurry temperature
Appropriately increasing the slurry temperature can also improve fluorspar flotation indicators.
When the temperature is higher, the solubility of the carboxylic acid collector in the slurry increases, it is easier to disperse, the ability to collect fluorite ore is also stronger, and the recovery rate of fluorite ore is higher.
However, the fluorite ore is not completely dissociated. In that case, part of the gangue minerals will be selected together with the fluorite ore, resulting in a lower quality of the fluorite ore.
When the temperature is low, the collection ability of carboxylic acid collectors is weak, but some fluorspar ores with good floatability will still be sorted out. The quality of fluorspar ore is high, but the recovery rate is low. Low.
3. Inhibitor dosage
Inhibitors mainly use water glass, followed by sodium metaphosphate, tannic acid, baking gum, starch, dextrin, lignosulfonate, etc. Water glass is a commonly used inhibitor in fluorite flotation and mineral processing.
To improve the selective inhibition ability of water glass, water glass can be formulated with soluble salts to form a combined inhibitor, or it can be formulated with sulfuric acid in a particular proportion to create acidic water glass.
4. Maintain appropriate slurry liquid level
In the process of fluorspar flotation and beneficiation, fluorspar minerals with better floatability will preferentially reach the top layer of the foam layer. When the slurry liquid level is low, the fluorspar concentrate has a high grade, but its recovery rate is low; when the slurry liquid level is high, the fluorspar concentrate recovery rate is high, but its ore grade is low.
5. Slurry pH value
When oleic acid is used as the collector and the pH value is 8-11, the floatability is good and the fluorite ore recovery rate can reach 80%-90%.
6. Pre-soften water
When the water quality is complex, the water for flotation fluorite must be pre-softened before entering the flotation separation stage, such as adding sodium carbonate for softening.
7. Optimize the flotation process
When the medium ore returns sequentially, part of the gangue ore will continue circulating in the fluorspar flotation system. It cannot be discarded, thus affecting the ore flotation indicators.
The mineralogical characteristics of an ore, such as its composition and crystal structure, play an essential role in determining the effectiveness of flotation. Additionally, the pH and temperature of the flotation process can greatly affect its success. Using JXSC appropriate reagents and flotation techniques can optimize the process and maximize recovery. Understanding and controlling these factors can improve the efficiency and profitability of fluorspar ore flotation operations.