The copper-zinc-iron ore flotation process is an important method in mineral processing and involves the separation of valuable minerals from gangue through chemicals and air. This complex process utilizes various reagents to extract and separate different minerals selectively through froth flotation. Using state-of-the-art flotation technology, valuable minerals can be separated from gangue, and high-grade concentrates can be obtained. Considering the complex nature of these ores, a key aspect is the optimization of reagent schemes and flotation conditions. It improves recovery and overall efficiency during the extraction process.
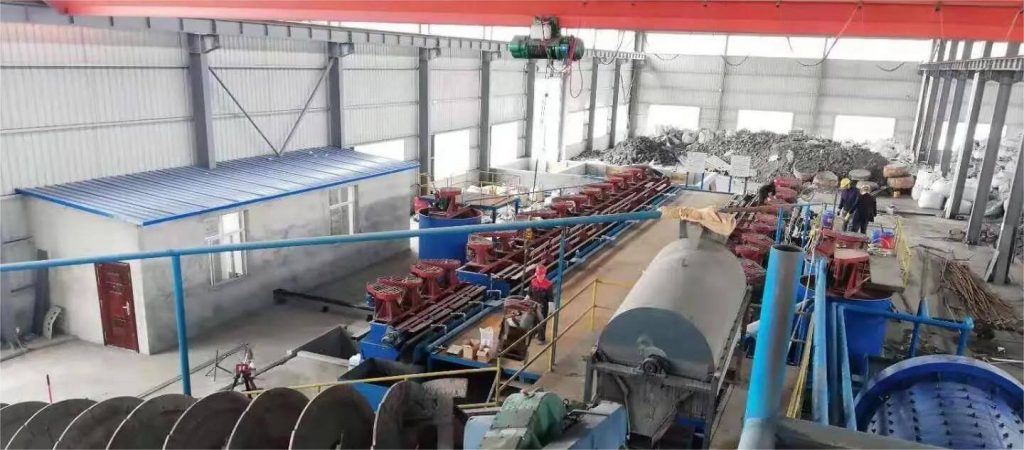
Mineral composition analysis
- Copper Mineral:Often identified by its distinctive green or blue color, it is often found along with sulfide ores. Additionally, minerals such as chalcopyrite and bornite indicate the potential for copper deposits.
- Zinc Mineral:Can be identified by its association with sphalerite, a black ore that often contains high levels of zinc. In addition, the identification of smithsonite and hemimorphite provides further evidence for nearby zinc deposits.
- Iron Minerals:Magnetite is an important indicator because it is highly magnetic and easily distinguished from other minerals.
copper-zinc-iron ore Flotation Technology
Flotation technology has dramatically changed the way copper, zinc, and iron ore are extracted from their respective deposits. The process involves using hydrophobic chemicals to separate these valuable minerals from the gangue selectively. As flotation technology advances, ore processing becomes more efficient and cost-effective. One of the innovations is the development of new collectors and frothers to improve the selectivity and recovery of copper, zinc, and iron ore during flotation.
In addition, JXSC flotation equipment allows better control of parameters such as particle size distribution, pH value, and airflow. This precise control optimizes mineral separation while minimizing energy consumption and environmental impact.
Optimization
Advanced beneficiation technologies are necessary to maximize the recovery and grade of copper, zinc, and iron minerals.
- One innovative approach involves using high-pressure grinding rollers (HPGR) to enhance the release of valuable minerals from the ore. By applying high pressure to the ore and breaking it into finer particles, HPGR technology increases the surface area for chemical reactions, ultimately increasing recovery rates and improving mineral grade.
- The most cutting-edge method is selective flotation, which extracts specific minerals during beneficiation. Mining operations can significantly improve concentrate grades while maximizing recovery efficiencies by tailoring reagent dosing and pH control to target copper, zinc, or iron minerals for selective extraction. In addition, advances in froth flotation equipment design can help increase selectivity and improve overall process performance.
Understanding the copper-zinc-iron mineral mix and release characteristics is critical to designing efficient flotation circuits that maximize value extraction while minimizing costs. Adopting environmentally friendly practices, such as water recycling systems and energy-saving processes, helps reduce operating costs, minimize environmental impact, and improve resource utilization. Inhibitors can also selectively inhibit certain mineral surfaces and increase the recovery of valuable minerals. In addition, combining innovative equipment and automation systems can further improve the productivity of copper-zinc-iron ore processing plants, thereby achieving sustained profitability in a highly competitive market environment.