Fluorite ore beneficiation is a complex process involving various stages of extracting the fluorspar mineral from its original form. The process typically involves crushing, grinding and flotation methods to separate valuable fluorspar from other impurities. An interesting aspect of fluorspar ore beneficiation is the use of advanced technologies, such as gravity separation and magnetic separation, which have proven effective in improving the quality of fluorspar concentrates.
Fluorite ore can be processed to improve its purity and quality using various beneficiation technologies such as gravity separation, flotation, and magnetic separation. This is critical for industries such as glass production, steelmaking, and chemical manufacturing that require high-quality fluorspar. In addition, efficient beneficiation helps extract valuable by-products from the ore, contributing to sustainable development and maximizing resource utilization. By gaining a deeper understanding of these intricacies, stakeholders can make informed decisions that contribute to sustainable mining practices and ensure a stable supply of high-grade fluorspar material to various industries.
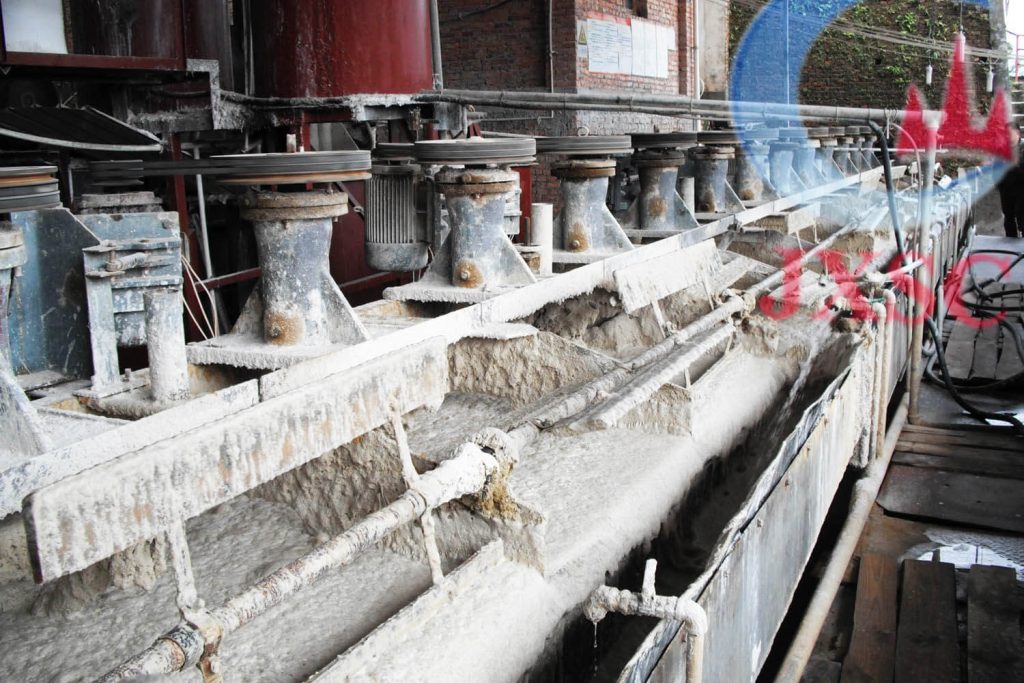
1. Geological factors: formation and distribution of ores
Fluorite ore beneficiation is affected by many factors, such as the formation and distribution of fluorite deposits. The first factor to consider is the geological environment in which fluorspar deposits were formed. These deposits are often associated with hydrothermal veins, granite, and sedimentary rocks, and specific geological conditions play a crucial role in determining the quality and quantity of fluorspar
Another important factor is the chemical composition of the parent rock, as this affects the concentration and accessibility of fluorspar in the ore. In addition, regional tectonic activity also plays an important role in the formation and distribution of fluorite deposits. Areas with active faulting or folding activity are more likely to have concentrated fluorspar deposits, whereas stable regions may have more extensive but lower-grade deposits. In addition, environmental factors such as temperature, pressure, and fluid composition also influence the formation and subsequent distribution of fluorite ore within a specific deposit. Understanding these factors can provide valuable insights into optimizing mineral processing processes to extract high-quality fluorspar from the ore.
2. Chemical Composition: Impact on processing methods and efficiency
Changes in the content of impurities such as calcium, silica, and other gangue minerals can significantly affect the choice of mineral processing technology. For example, fluorspar ores with higher calcium content may require a more aggressive flotation or gravity separation process to effectively remove impurities and obtain higher purity fluorspar concentrate.
Additionally, understanding the chemical composition can provide a tailored approach to selecting the best reagents for the flotation or leaching process. High silica content may require different modifiers to promote the selective hydrophobicity of fluorite particles while suppressing undesired gangue minerals. In addition, trace elements in fluorspar ore can affect downstream processing and product quality, and it is best to conduct a thorough chemical analysis before formulating a beneficiation strategy.
3. Physical Properties: Influence on beneficiation and separation processes
The physical properties of fluorspar ore play a vital role in its beneficiation and separation process. An important factor is the density of the ore, which affects its ability to separate from other minerals. For example, if fluorspar ore has a higher density than gangue minerals, it can be easily separated using gravity separation techniques such as jigs or shakers.
On the other hand, if the density difference is small, more sophisticated techniques such as flotation or magnetic separation may be required to achieve effective beneficiation.
Another important physical property is particle size distribution. The size of the fluorspar ore particles affects the efficiency of the beneficiation process. Finely ground particles provide greater surface area for interaction with reagents during flotation, thereby increasing separation efficiency. In contrast, coarse particles may require additional grinding steps for optimal release and separation. Understanding these physical properties allows custom beneficiation processes to be developed to maximize fluorspar recovery.
4. Market Demand: Influence on processing strategies and technologies
Market demand is crucial in formulating mining companies’ fluorspar ore beneficiation strategies. As the demand for fluorine derivatives continues to increase in various industries, such as steel, aluminum, and chemical production, there is also an increasing demand for high-quality fluorspar concentrates. This has prompted the company to invest in advanced beneficiation technology to meet the stringent quality requirements of end users. In addition, changing market demands have also led to adopting flexible beneficiation processes that can quickly adapt to changing market demands, allowing the company to take advantage of price fluctuations and changes in consumer preferences.
Furthermore, the impact of market demand is broader than the quality and quantity of fluorspar concentrate produced. It also affects the geographical distribution of concentrators and production facilities as operators seek proximity to major consumption areas or transportation routes. This ensures a reliable supply chain responding quickly to market changes and minimizing transportation costs. In addition, market demand has driven innovation in mineral processing technology and stimulated research into more efficient and environmentally friendly processes.
5. Environmental Considerations: Sustainable Mineral Processing
Fluorite ore beneficiation practice is mainly based on economic considerations. However, as society becomes increasingly aware of the potential long-term impacts of mining and mineral processing activities on the environment, there is an increasing emphasis on the environment. For example, traditional mineral processing methods often involve chemicals and large amounts of water, leading to severe pollution and ecosystem damage. This has prompted industry players to explore alternative methods of minimizing environmental impact while enabling efficient fluorspar ore extraction and refining.
An emerging trend is adopting cleaner production technologies, such as dry beneficiation processes, which eliminate excessive water use and reduce chemical emissions. In addition, advances in sustainable technologies offer the opportunity to use renewable energy to power mineral processing operations, reducing the carbon footprint. These shifts toward environmentally friendly practices help mitigate ecological hazards and open the door to improved regulatory compliance and increased public awareness in the fluorspar mining industry. By integrating sustainable methods into these processes, it can actively reduce its ecological footprint while ensuring the industry’s long-term viability.
Fluorite ore beneficiation uses gravity separators, flotation machines, and magnetic separators to improve its purity and quality. Because there are many types of fluorspar ore, understanding its mineral composition is critical to determining the most effective beneficiation process. Optimizing fluorspar ore beneficiation requires carefully balancing factors such as mineralogy, processing technology, and environmental factors. Engineers can achieve maximum efficiency, ultimately increasing the productivity and profitability of fluorspar mining operations. In addition, JXSC, using advanced mineral beneficiation technologies and innovative methods, can improve the efficiency, cost-effectiveness, and sustainability of fluorspar ore beneficiation operations.