Tin ore is also known as cassiterite. As a kind of ore with high density and fine particle size, the traditional beneficiation process cannot recover tin ore, so new methods must be found. However, flotation is an effective means to recover the fine-grained tin minerals from tin ore to tailings. Recovery is the percentage of valuable minerals successfully extracted from ore during the flotation process. During the flotation process, the pH value of the solution, particle-bubble interaction, metal ions and flotation reagents significantly impact the flotation of tin ore.
In this article, we will explore four key points that can help improve the recovery rate of tin ore flotation. These points are based on many years of research and practical experience in mineral processing. By implementing these strategies, mineral processing plants can significantly increase their efficiency and profitability while minimizing environmental impact.
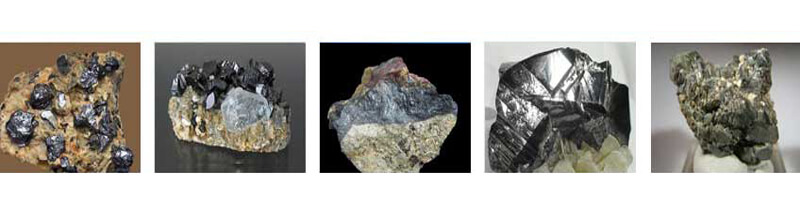
1. PH Value
The PH value is one of the important factors affecting the flotation of tin ore. However, the adsorption capacity of tin minerals on collectors gradually changed as the pH value increased. With the increase of pH value, the adsorption capacity of tin minerals to collectors first increases and then decreases. In the pH range of 3-5, the adsorption of tin minerals to collectors reaches its peak. Therefore, controlling the pH value in the range of 3-5 is more suitable for recovering fine-grained tin minerals. When the pH value of the tin ore concentrate slurry in the flotation column is low, white bubbles are prone to occur. If copper sulfate and other agents are used in tin ore flotation, when the pH value is too high, the foam will turn black and white, and white foam will quickly form in the flotation column. If lime is used to adjust the pH value of the slurry to an appropriate range, the foam will be more stable.
Due to the particularity of the cassiterite flotation process, it may not be easy to control when a single agent is used. Therefore, beneficiation tests should be conducted according to the reagent combination when the tin ore flotation process conditions change to determine the appropriate pH value range.
2. Particle-bubble Interaction
The collision between particles and air bubbles plays an important role in the selectivity and recovery of tin ore flotation. When the bubbles and tin mineral particles approach each other and collide, due to the physical adsorption characteristics of the surface of the tin mineral particles, a large energy difference is generated between the bubbles and the tin mineral particles, which is beneficial for the bubbles to capture the tin mineral particles. Appropriately reducing the bubble diameter can increase the probability of bubbles colliding with tin mineral particles, making it easier for fine-grained tin mineral particles to attach to the bubbles, thereby providing more favorable conditions for the subsequent mineralization process. The process of tin mineralization can be changed by changing the bubble diameter, thereby improving the recovery efficiency of tin mineralization. However, under the same flotation conditions, the larger the bubble diameter, the more unfavorable the tin ore flotation. If additives such as bubble collectors are used, the diameter of the bubbles can be reduced.
3. Various Metal Ions
The main symbiotic minerals of cassiterite are biotite, pyrrhotite, pyrite, etc., and rhodochrosite, serpentine, etc., are also symbiotic with it, and secondly, it is also symbiotic with dolomite and magnesite. Since tin minerals are often associated with other metal minerals, many free metal ions are often produced in the ore by other mechanical actions such as crushing, grinding, and mineral dissolution. The flotation pulp usually contains other metal ions, such as iron, copper, calcium, lead, magnesium, etc. The physical and chemical effects of these metal ions on the surface of tin minerals have a greater impact on the flotation of tin minerals.
- Iron ions play a very important role in the process of tin flotation. During the flotation process of tin minerals, iron ions will destroy the film on the surface of tin minerals, causing the surface of tin minerals to be oxidized, thus making the flotation of tin ores difficult.
- Copper ions can form water-insoluble copper-tin salts with tin on the surface of tin ore and can inhibit the process of tin flotation through electrostatic interaction.
- Calcium ion is a vital metal ion in tin flotation. When calcium ions enter the tin ore, they will form water-insoluble calcium salts with tin, affecting tin ore flotation.
In actual production, the mineral composition of tin ore is complex, and many kinds of metal ions significantly impact the recovery of tin ore. According to the mineral composition of the tin ore, we should select the appropriate combination of agents through the beneficiation test in a targeted manner to reduce the impact of metal ions on the recovery of tin ore.
4. The Selection Of Flotation Agents
There are two main types of flotation reagents: one is anion collectors and the other is cationic collectors. Due to the poor natural buoyancy of tin minerals, some cassiterite impurities that cannot float out are enriched in the concentrate, resulting in excessive tin content in the tailings and high density. Therefore, tin ore collectors have higher selective adsorption requirements and generally require anion collectors, such as fatty acids, phosphonic acids, arsine acids, hydroxamic acids, etc. In order to improve the adaptability of flotation agents to tin ore, combined reagents are usually used for flotation.
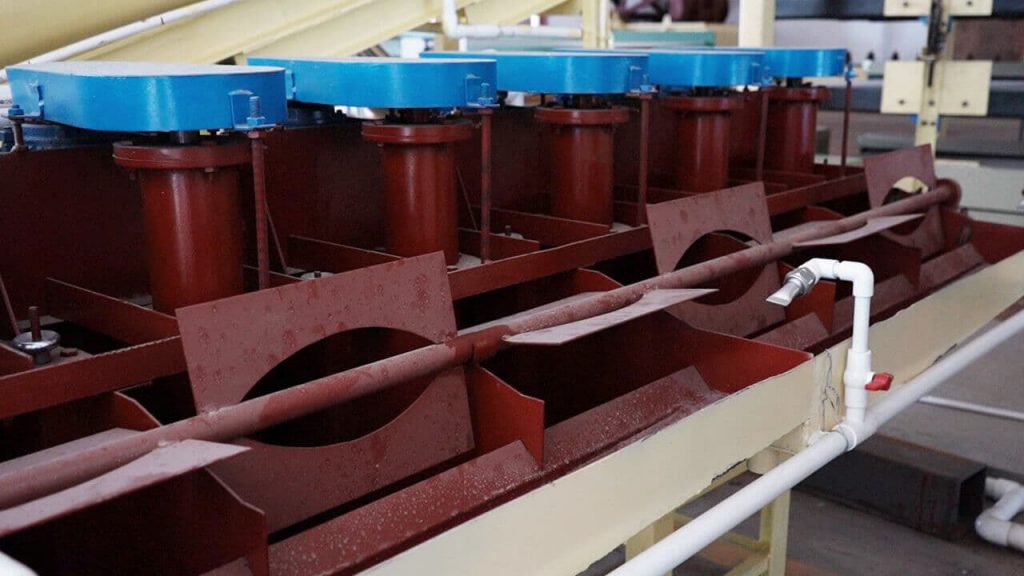
Attention to these four points can greatly improve the flotation efficiency of tin ore. Firstly, please select the appropriate collector and adjust its dosage according to the characteristics of the ore. Second, control the pH value and add appropriate activators and inhibitors. Third, ensure proper pulp density and stirring speed. Finally, please choose a suitable flotation machine and optimize its operating conditions. Although we have highlighted many important aspects, this is not the whole story. The methods described above may require trial and error to find the best combination for a particular ore body. Both mining companies and researchers must prioritize these points by improving the flotation process and achieving higher recovery rates. By improving the mineral processing solution and achieving higher recovery rates, JXSC continue to strive to maximize the efficiency of this valuable resource.