Tantalum always appears with niobium, which has similar chemical properties in nature. It is generally found in tantalite, columbite, and coltan. Among them, coltan is mainly composed of tantalite, columbite, and pyrochlore and has corrosion resistance, gas absorption, superconductivity, and high strength. Nearly 80% of the world’s niobium is used to make high-strength, low-alloy steel, while tantalum is the key to the world’s electronics industry. Therefore, coltan is a relatively important metal mineral with high beneficiation value. The coltan beneficiation adopts gravity separation, flotation, magnetic separation, electric separation, smelting, and other combined processes.
What Is Coltan?
Coltan is the name for the composite mineral niobium-tantalite; a dark black metal mineral containing tantalum and niobium. Coltan is a basic component of a range of electronic devices, from smartphones to laptops to advanced computer medical devices. It has a wide range of uses in the industrial field. It can be used to make niobium oxide and tantalum oxide, and can also be used to extract tantalum and niobium minerals. It is usually necessary to beneficiate it to obtain concentrate for industrial application, and its economic value is extremely high.
Coltan beneficiation process
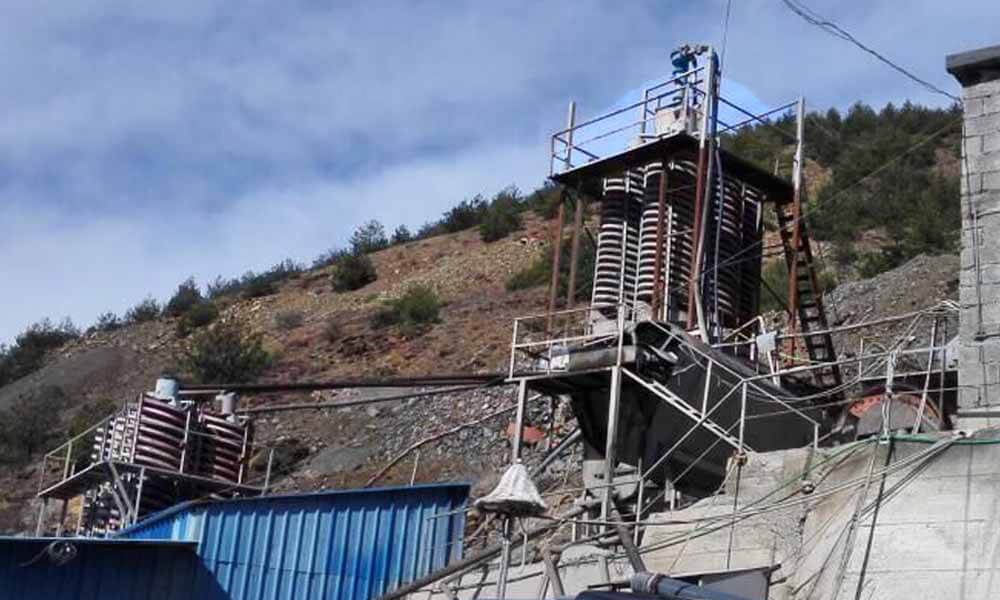
1. Washing: When dealing with fine ore or ore with high primary mud content, washing is essential to reduce the mudification of tantalum-niobium minerals.
2. Crushing: The mined ore is initially crushed to break large aggregates into easy-to-handle sizes. This is not only convenient for transportation but also reduces the material to a smaller particle size for further processing. Crushing also increases the surface area of the ore, making its interaction in the beneficiation process more effective. Special equipment such as jaw crushers or cone crushers is usually used to ensure finer particle sizes without excessive wear on the machine.
3. Grinding & Classification: Further reduce the ore’s particle size to prepare for the feed particle size of the next gravity separation equipment.
4. Gravity separation: Due to the low grade of tantalum-niobium and the relatively high density of useful minerals, a relatively low-cost gravity separation method is most suitable for rough separation.
5. Magnetic separation: A three-disc magnetic separator is often used. It can separate three minerals at once and boasts a high concentrate recovery rate, ensuring the audience of the process’s efficiency.
Coltan beneficiation plant
Alluvial Coltan Washing beneficiation Plant
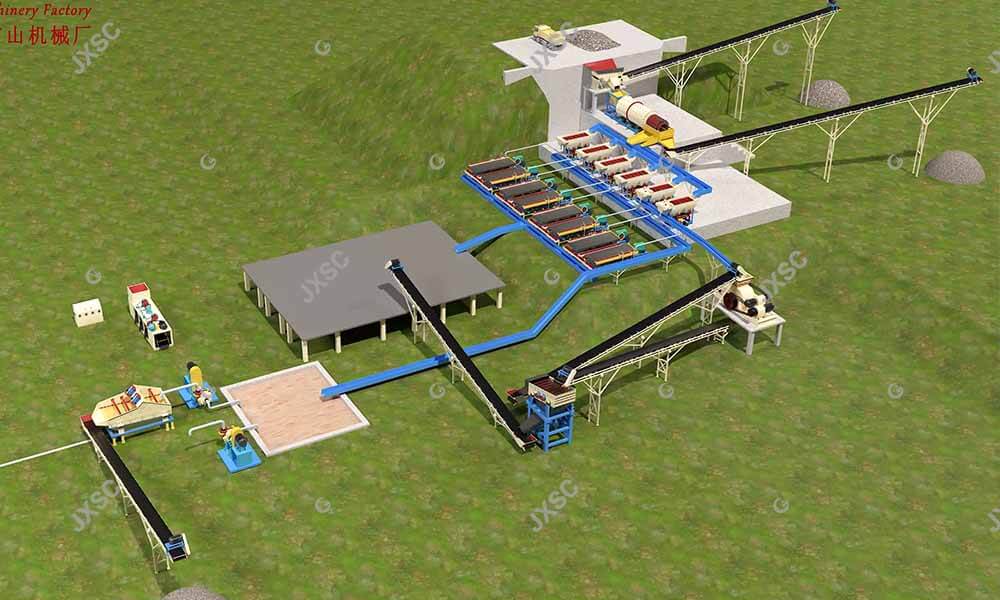
This is a complete coltan, tin, tungsten processing plant, the details as follows:
- It is configured with vibrating feeder to feed raw material and remove oversized rocks.
- Trommel scrubber is used to wash off the sticky mud from raw ores, and screen out three size ranges, the Ta-Nb, Tin grains will be released more easily from the cleaned ores.
- Jig separator is a gravity roughing concentration machinery, the over-screen big-grained concentrate of Jig will be crushed & sieved by double roller crusher & vibrating screen, in order to get -2mm fine concentrate and transport to shed for drying in the sun. The under-screen concentrate of jig will feed to shaking table for further concentration.
- The shaking tables have a very high recovery ratio for processing coltan and cassiterite, its concentrate will also convey to the shed for drying.
- The final concentration equipment is the three-disc dry magnetic separator, widely used for Tin, cassiterite, and coltan separation.
Rock Coltan crushing processing Plant
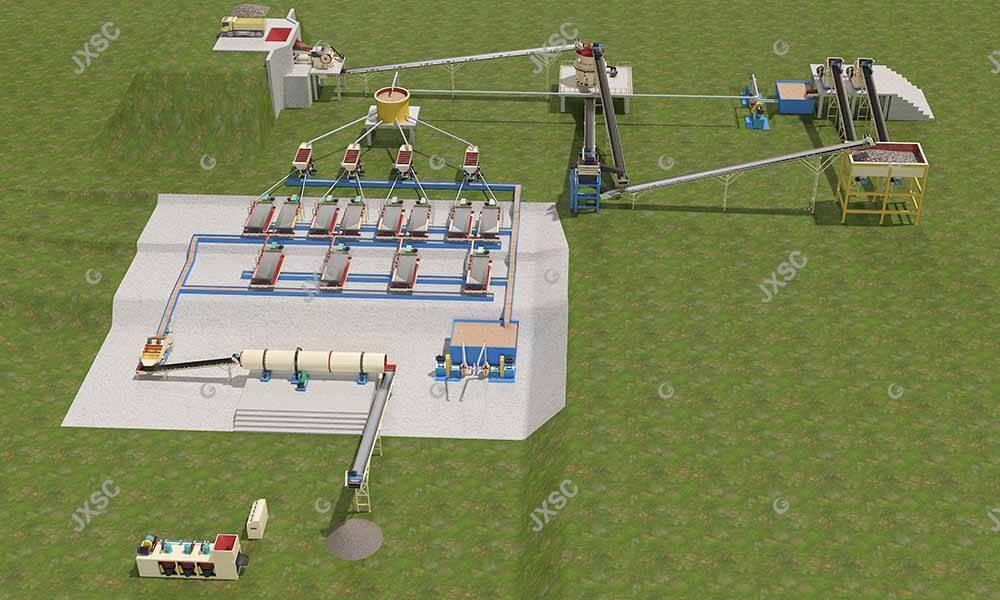
This setup is a rock coltan tin ore processing plant, the following is flow details:
- The vibration feeder efficiently feeds raw material to the jaw crusher, which is then processed by the cone crusher, a secondary crushing machine. The vibration screen, with a 30mm screen mesh size, efficiently screens out the desired material, ensuring a smooth and productive process.
- The storage bin’s 0-30mm material will go to the hammer crusher, a fine grinding machine, to grind it into a 0-2mm fine powder. To release the coltan and tin from the rock, the output 0-2mm slurry from the hammer mill will be pumped to a jig separator to concentrate heavy coltan and tin. The primary heavy concentrate ore discharged from the jig separator will be sent to a shaking table to concentrate again.
- The shaking table has an extremely concentrated effect for heavy minerals; in order to get a higher purity of coltan and tin, the middling from the 1st stage shaking table will go to the 2nd stage shaking table to concentrate again, so can reach the highest recovery ratio and high purity coltan tin mixture. All the 0-2mm coltan tin concentrate ore discharged from two stages of the shaking table will be sent to the dewatering screen for dewatering water. Depending on the customer, the concentrated ore will be sent to the drying machine or dry in the sun.
- The dry heavy minerals mixture will finally be sent to a high-intensity 3pcs disc dry magnetic separator. The gauge is adjustable to separate each heavy mineral, such as iron, ilmenite, hematite, coltan tin concentrate, etc., to get high-grade coltan and tin ore. Usually, the final coltan and tin grade can reach about 60-65%, depending on raw material conditions.
Coltan is a key component in shaping a wide range of modern electronic devices. The beneficiation process is key to extracting valuable tantalum and niobium from coltan, ensuring that these minerals can be used efficiently and sustainably. JXSC supports customized coltan beneficiation plants and equipment, contact us for more details!