Fluorite(fluorspar) is a common mineral in many geological environments and is widely used in various industries such as metallurgy, ceramics, glass, cement production, and chemical processing. The most important application of fluorite is as a source of fluorine for the production of hydrofluoric acid, which is used to manufacture refrigerants, plastics and other chemicals. Flotation is commonly used to extract fluorspar from the ore because it selectively separates minerals based on their physical and chemical properties. The different symbiotic mineral components can be divided into quartz-type fluorite, sulfide-type fluorite, calcite-type and barite-type fluorite. The nature of each mineral is different, and its flotation method is also different.
About Fluorite Ore
Fluorite, also known as fluorspar, is a mineral commonly found in nature. It is widely used in metallurgical, ceramic and chemical industries due to its unique properties. It is also known as fluorspar and comprises calcium fluoride (CaF2). Fluorite ore properties are distinctive, making it a valuable resource for various applications.
The demand for fluorite has increased significantly over the years due to its optical clarity, low refractive index, low dispersion level and high hardness. These properties make it an ideal material for manufacturing lenses, prisms and other optical components. Its use as a flux agent in steel production makes it an essential industry component. One of the major applications of fluorite is in producing hydrofluoric acid, which is used in producing aluminum and other chemicals.
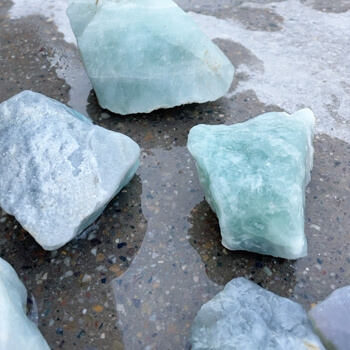
1. Quartz-Fluorite Ore Flotation
It mainly comprises fluorite (about 85%) and quartz, with only a small amount of calcite, barite and sulfide. Reducing silicon in concentrates is the focus of this type of ores, and the requirements for silicon content vary according to different usage requirements. In the process of beneficiation, grinding is a factor that greatly affects the flotation of quartz-type fluorite ore, and it is necessary to dissociate the quartz and fluorite monomers through grinding. Since most quartz-type fluorite ores have conjoined bodies of quartz and fluorite, the grinding particle size is too fine, leading to excessive fluorite crushing and affecting the recovery rate. Therefore, the stage grinding process is generally adopted, which reduces the silicon content of the concentrate product after fluorite flotation and increases the recovery rate of the fluorite concentrate. Using the process flow of stage grinding stage flotation, high-grade fluorite concentrate can be obtained after multiple selections.
This type of fluorite ore can be divided into two types, coarse-grained and fine-grained, according to the embedded characteristics of useful minerals.
1. Coarse-grained embedded fluorite is easy to select, using fatty acid collectors, ore slurry adjuster as sodium carbonate, quartz inhibitor as water glass, and high-quality fluorite concentrate can be obtained through a coarse-multiple refining process.
2. The flotation reagents of fine-grained embedded ore are the same as those of coarse-grained embedded quartz-type fluorite ore. However, due to the fine particle size embedded in the target minerals, it is necessary to strengthen the grinding, and the staged grinding stage is adopted for the separation process.
Quartz-fluorite type ore beneficiation process: raw ore crushing-grinding-roughing-rough concentrate regrinding-multiple selection.
2. Calcite-fluorite ore flotation
The main minerals of calcite-fluorite type ore are fluorite and calcite (the content is as high as 30%), some contain a small amount of quartz, and sometimes quartz-calcite-fluorite type ore can be formed, which is a refractory ore.
The main reason why this type of ores is challenging to separate is that both calcite and fluorite are calcium-containing minerals with similar surface physical and chemical properties. The mutual transformation between minerals is easy to occur when the solution coexists, and selecting appropriate collectors and inhibitors is the key to separating fluorite and calcite.
To achieve the separation of calcite and fluorite, the pH value of the slurry must be adjusted, and then a collector can be used to achieve a good separation effect.
Calcite-fluorite type ore beneficiation process: raw ore crushing – grading - jig concentrator – grinding – roughing – multiple separations.
3. Sulfide fluorite ore flotation
In actual production, sulfide fluorite-type ore beneficiation technology is mainly based on the flotation method. First, the sulfide ore is preferentially floated with xanthate collectors, and fluorite is the flotation tailings treated as fluorite ore separately. Use fatty acid agents for many selections.
When classifying such ores, sulfide ore collectors are generally used to preferentially flotation metal sulfide minerals, and then fatty acid collectors are used to classify the flotation tailings to recover fluorite.
To better extract valuable metals and decompose fluorite, sometimes, in fluorite flotation operations, a small amount of sulfide ore inhibitor (such as cyanide) is added to inhibit residual sulfide and ensure fluorite concentrate quality.
Sulfide fluorite type ore beneficiation process: Ore crushing – grinding – preferential flotation of sulfide minerals – tailings flotation of fluorite – fluorite rough concentrate has been separated many times.
4. Barite-fluorite ore flotation
The main minerals of barite-type fluorite ore are barite and fluorite, and the content of barite is generally 10%-40%, often accompanied by pyrite, galena, sphalerite and other sulfide minerals.
This kind of ore beneficiation is generally mixed and flotation to obtain a barite-fluorite mixed concentrate, and then barite and fluorite are separated. According to the order in which barite and fluorite emerge, it can be divided into two schemes:
- Inhibiting barite flotation to fluorite, this method can obtain high-grade barite concentrate and fluorite concentrate;
- Inhibiting fluorite flotation barite, this method first obtains barite concentrate, adds fatty acid collectors and sodium silicate to the tailings, and selects fluorite to concentrate several times (7~9 times). The process of this method is simple, easy to operate, and qualified barite concentrate can be obtained, but the grade of fluorite is often not high.
In actual production, the separation of fluorite and barite mostly adopts the process of inhibiting barite with pumice fluorite, and uses fatty acid flotation reagents as fluorite collectors, caustic starch, dextrin and other organic inhibitors.
From our analysis of four different ore types, it is clear that the optimal conditions for flotation vary according to the specific properties of each sample. JXSC can customize a suitable flotation plant for fluorite ore, which can greatly increase fluorite’s recovery rate while reducing the environmental impact. Gain a thorough understanding of the various fluorite beneficiation plant and equipment to make informed decisions to achieve the best results regarding efficiency, cost-effectiveness and environmental sustainability.