Separation Equipment
We provide mineral separation equipment including flotation machines, magnetic separators, electrostatic separators, etc.
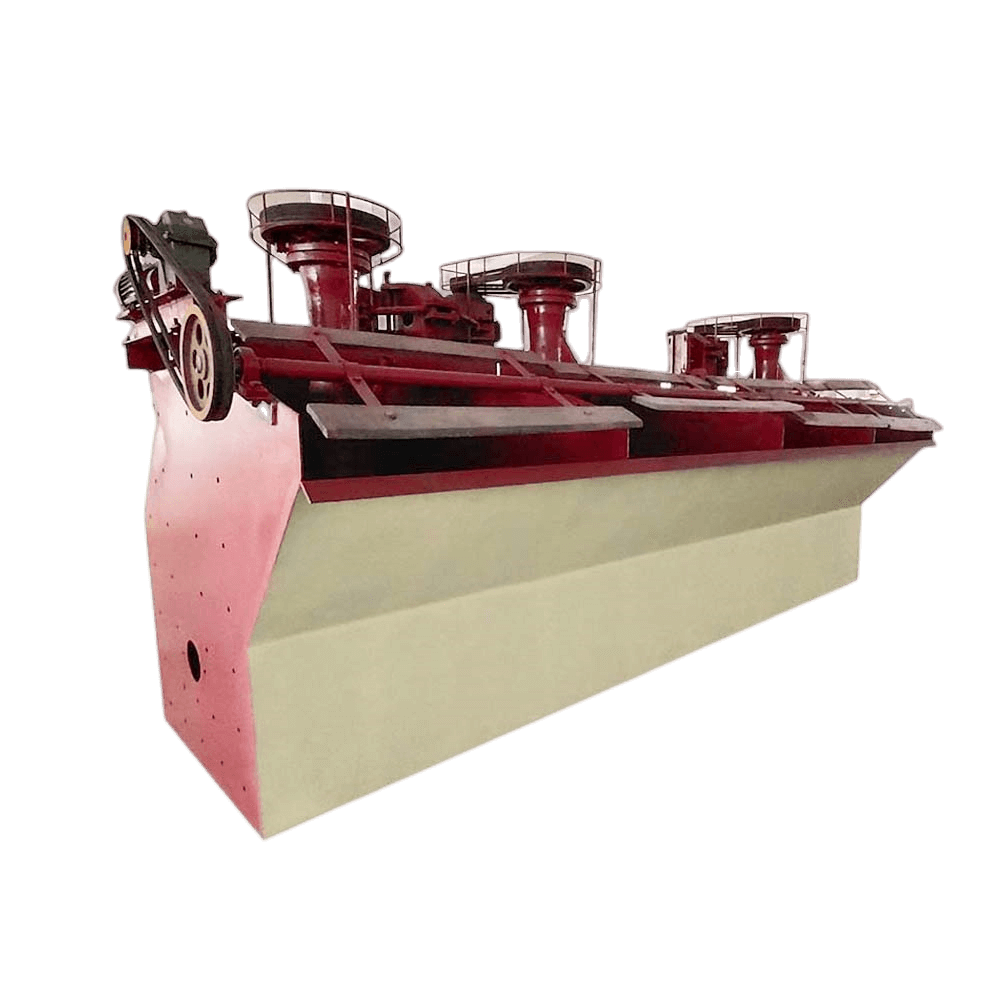
flotation machine
Capacity: 0.18-50m³/min per cell Application: Recovery copper, gold, zinc, lead, nickel, fluorite, molybdenum ore, slag, feldspar, talc, rutile and other mineral processing plants.
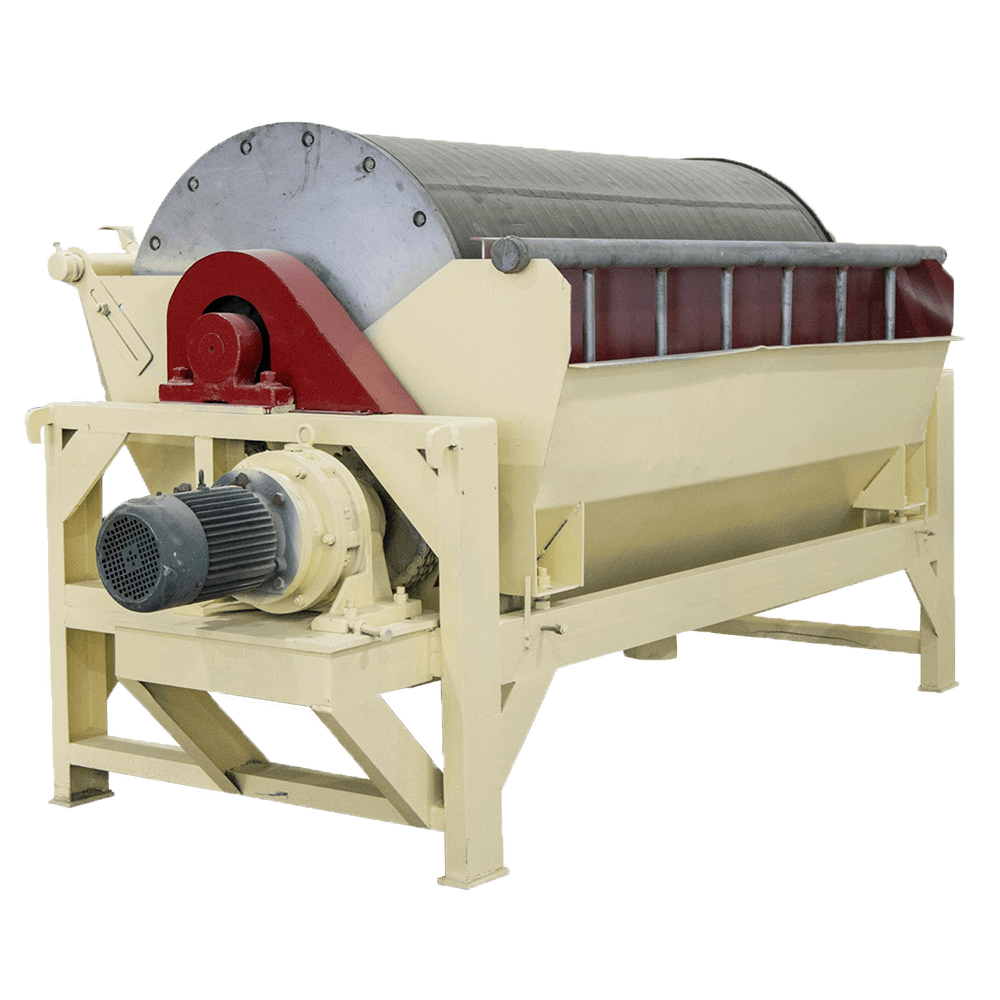
wet drum magnetic separator
Capacity: 0.5-180 t/h
Application: Commonly used for wet magnetic separation of pyrite, magnetite, ilmenite, manganese, iron ore and other materials with particle size below 3mm.
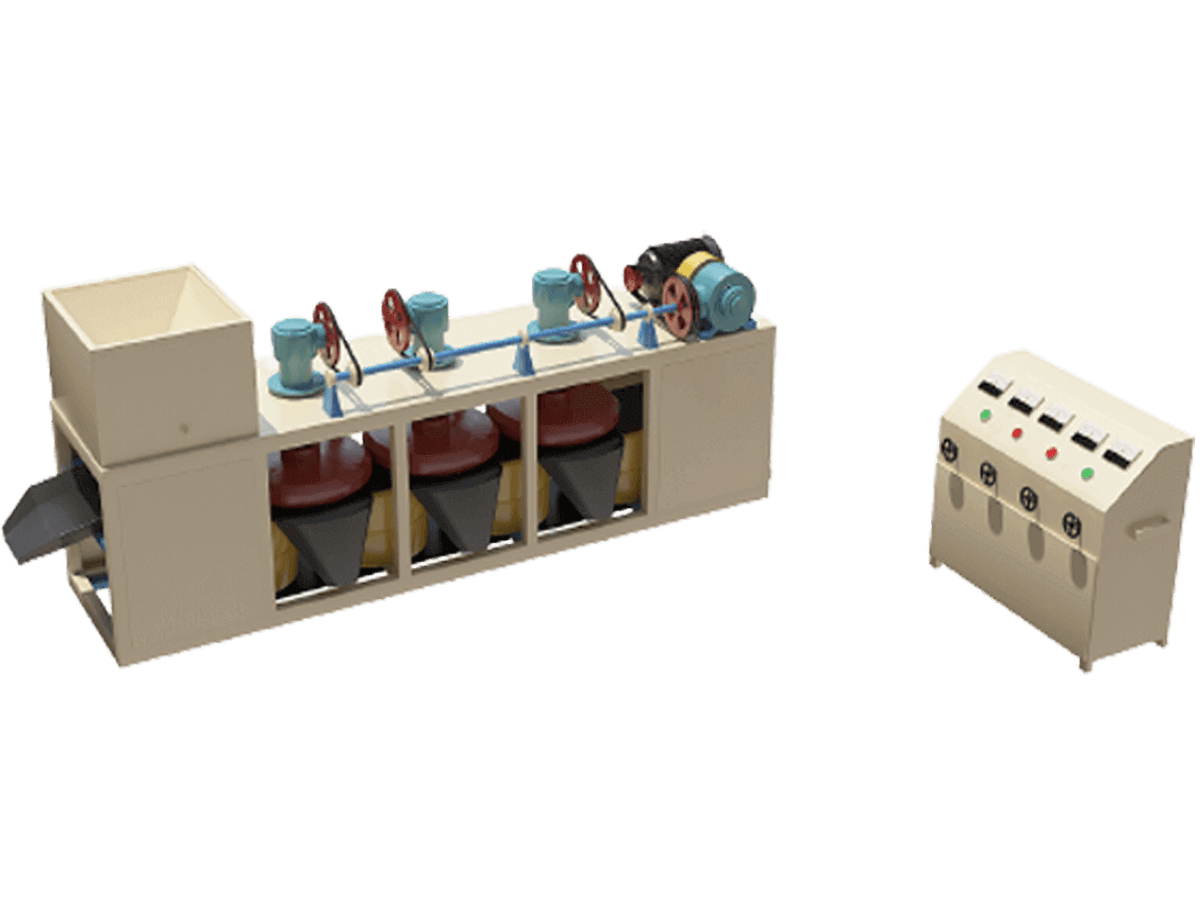
Three disc magnetic separator
Capacity: 100-800 Kg/h
Material Size: ≤2mm
Application: Application: Suitable for dry separation of various metal minerals such as titanium ore, tungsten, tin ore...
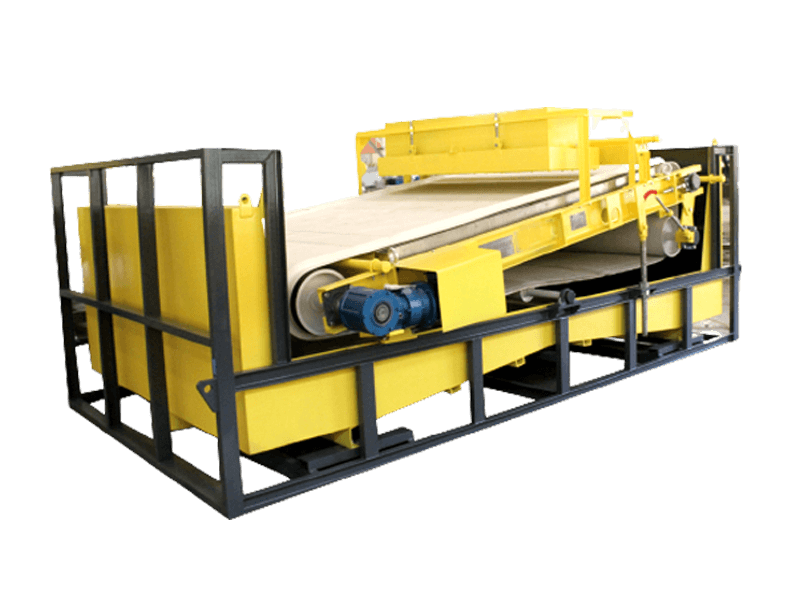
plate magnetic separator
Capacity: 8-35 t/h
Application: Mainly used for wet separation of various weakly magnetic metal minerals such as magnetite, hematite, ilmenite, tungsten ore, and iron removal process of silica sand and kaolin.

High Intensity Dry Magnetic Separator
Capacity: 0.2-9 t/h
Application: It is suitable for the separation of weakly magnetic minerals and non-magnetic minerals such as tantalum niobium, tin, manganese ore, chromium ore, rutile, zircon, beach sand, etc.
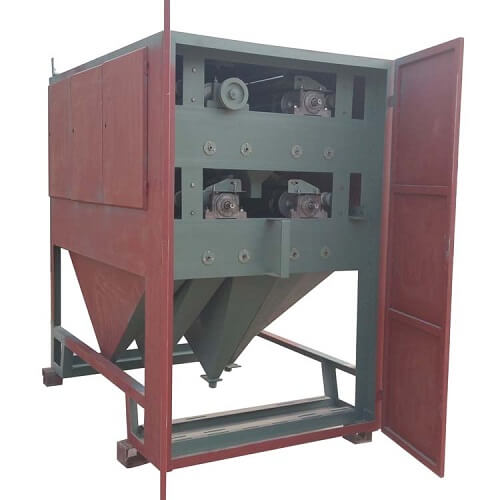
Electrostatic Separator
Capacity: 1-3T/H or customizable
Feeding: 0-3mm
Application: separating magnetite, ilmenite, rutile, monazite, zircon, tungsten, tinstone, zirconite, andalusite, rutile, etc
Recommended Products
Contact Us Now
Please fill out the information below for the quotation price and engineer’s help. We will reply ASAP!
Notice:
- We do not provide jobs and have no interest in investment or partnerships.
- We provide mineral processing equipment and solutions; not buy and sell mineral /ore /materials.
- We value your privacy and keep your information safe.