Mineral Processing » Solutions » Gold CIP Processing Plant
Gold CIP Processing
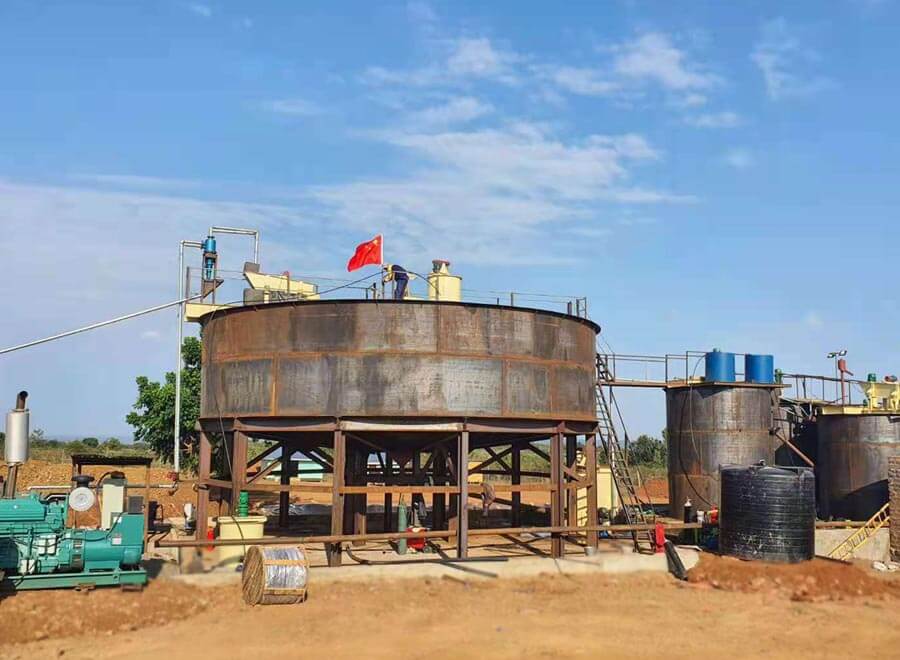
The gold CIP (Carbon-in-Pulp) processing is a gold extraction method that uses activated carbon to absorb gold-cyanide complexes from gold ore slurry. It is mainly suitable for beneficiating gold-containing oxidized ore with high slime content and containing carbon ore.
- High recovery rates up to 98%
- 30-40% Lower operating & maintenance costs
- Fast absorption, Eco-friendly processing
- Adaptability to different ore types
Gold CIP Process
Gold CIP (Carbon-in-Pulp) process uses activated carbon for adsorption based on oxidation leaching, which can increase the gold leaching rate. It mainly involves using activated carbon to adsorb gold from a cyanide solution, then eluting and regenerating the carbon for reuse. The main flow includes crushing, grinding, leaching pretreatment, leaching, and activated carbon adsorption processing, gold-loaded carbon desorption and electrolytic stage, and tailing water recycle system.
Gold CIP Extraction Process
- Crushing, grinding: The ore is first crushed and ground to extremely fine particle size to match the size of the subsequent gold extraction process.
- Leaching: Usually cyanide is added to the slurry as a leaching agent to help dissolve the gold in the ore.
- Adsorption: It involves the introduction of activated carbon into the slurry, capable of selectively adsorbing gold from the slurry.
- Carbon separation: A slurry containing gold-loaded carbon particles is passed through screens or filters to separate the carbon from the slurry.
- Gold elution & electrowinning: Using chemical cleaning agents to gold from carbon → recover 99.9% pure gold via electrolysis cells.
- Smelting: The gold deposited on the cathode is usually melted and refined by smelting to cast it into bullion or other forms.
- Regeneration: Spent carbon is heated to high temperatures, usually in a kiln or furnace, to remove impurities and restore its adsorption capacity.
- Tailings treatment: Tailings contain various chemical substances or minerals, usually stored in tailings ponds for further reprocessing.
Certified Carbon-in-Pulp technology with 98% gold recovery efficiency, contact us to tailor gold CIP solutions for your mine.
CIP Gold Processing plant
Gold CIP Process plant
Gold carbon in pulp process flow
1. Feeding & crushing system: The excavator sends the raw ore into the hopper with a trough feeder. It can evenly send the material into the jaw crusher to crush the 210mm material to below 60mm. Then, the output of the jaw crusher is transported to the next fine jaw crusher by the belt conveyor, which crushes to less than 20mm. The output material is transported to the vibrating screen by the belt conveyor, and the +20mm material is returned to the fine jaw crusher for further crushing. Finally, less than 20mm of material into the hopper with an electromagnetic vibrating feeder and evenly fed into the ball mill.
2. Grinding system: Ball mills grind fine ore rocks into a fine powder to release the gold in the rocks. Then, the output material enters the spiral classifier for classification. The large-grained minerals are returned to the ball mill for re-grinding to ensure that 80% of the final output is less than 200 mesh (0.074mm).
3. Leaching pretreatment: After grinding and classification, the fine powder enters the slurry tank and into the thickener by sand pump. Before the pulp enters the thickener, there is a safety screen to pre-screen to prevent coarse particles, and the pulp under the screen directly enters the inside of the thickener. At the same time, add flocculant to accelerate the sedimentation. The overflow water of the thickener enters the sedimentation tank, and the water after sedimentation can be recycled.
4. Leaching process: The thickener’s underflow will enter the mixing barrel with the height difference. Then, the stirred pulp is driven into the double impeller leaching tank with a sand pump, and sodium cyanide is added.
5. Activated carbon adsorption treatment: After the gold is leached and dissolved in the solution, the slurry flows into the double-impeller stirring adsorption tank at the back. Then, activated carbon is added. It adsorbs the gold in the pulp to become gold-loaded carbon, which is extracted with a carbon extractor.
6. Desorption and electrolysis, recycling of gold-loaded carbon: A vibrating screen removes the gold-loaded carbon, and the gold-loaded carbon enters the normal temperature and pressure desorption electrolysis system, after electrolysis, obtains gold mud. The gold mud is then dried in an oven. Finally, use the gold furnace to smelt the gold bars. After desorption, the gold-loaded carbon is generally reused in a drying oven.
7. Tailings water recovery system: The tailings of the adsorption stirring tank first enter the vibrating screen to screen the carbon. The material under the screen enters the lower tank/pond and is pumped to the large conical pool or tank by the mud pump. Then, the slurry into the filter press by pump for pressure filtration and recovery of tailings water.
Advantages Of The JXSC Gold CIP Process:
- 5-8% higher recovery rate than traditional methods.
- Reduces reagent consumption by 30-40%.
- Advanced carbon regeneration system.
- Automated process control (PLC).
This gold CIP plant uses high-temperature, high-pressure, cyanide-free, and automatically controlled for desorption. JXSC supports the customized full gold processing solutions & equipment according to your mine information. Contact us to get more details and latest equipment quote!
Related equipment
Other Gold solutions
Contact Us Now
Ask us about mineral processing configuration and equipment quote! (No job, No investment)
Notice:
- We only provide mineral processing equipment and solutions; not buy and sell minerals/ ores/ materials.
- We do not recruit, don’t offer jobs, and are not interested in investments or partnerships.
- We value your privacy and keep your information safe.