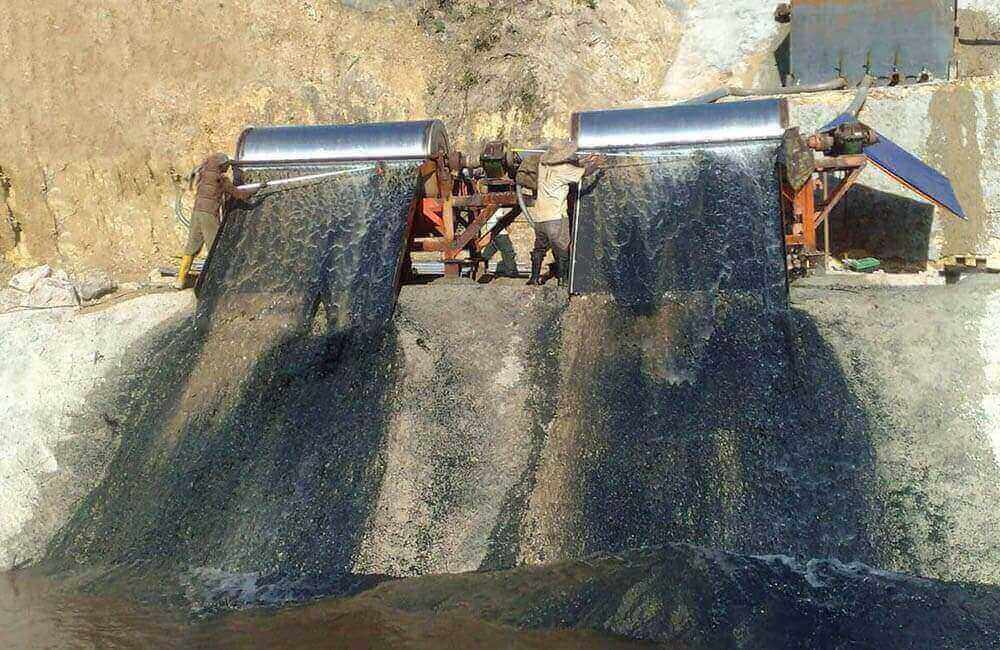
iron ore beneficiation
Industrially valuable iron minerals are magnetite, hematite, limonite, ilmenite and siderite. Iron ore beneficiation mainly includes crushing, grinding, gravity separation, flotation and magnetic separation.
Combining the characteristics of different iron ores, we will provide customized iron ore processing plant flow and equipment latest price, the concentrate extraction and recovery rate is as high as 95%.
Iron ore beneficiation Process
Iron ore beneficiation is mainly a process of separating valuable minerals and iron minerals from ores to extract high-quality iron ore. The iron ore processing mainly includes crushing, grinding, washing, beneficiation, dewatering, etc.
Various iron-bearing ore beneficiation
1. Magnetite beneficiation: The main iron mineral contained in magnetite is iron tetroxide (Fe3O4). And iron in the form of magnetite accounts for more than 85% of iron ore. Strong magnetism mineral, so weak magnetic separation is its main method.
2. Titanium/Ilmenite beneficiation: A weakly magnetic black or steel-grey mineral. The common ilmenite process is “gravity separation – strong magnetic separation – flotation or electric separation (sulfur removal before separation)”.
3. Limonite beneficiation: A typical refractory iron ore with easy sludge. Mainly includes washing-gravity separation process.
4. Siderite beneficiation: A common carbonate mineral with low iron grades. Commonly used methods are gravity & strong magnetic separation.
5. Hematite beneficiation: A weakly magnetic mineral. After crushing, grinding, washing and other pre-separation, magnetic separation is the most common; it is usually combined with flotation and gravity separation.
The specific iron ore mineral processing flow and machine vary depending on the properties of iron mineral. Contact us to customized the iron ore processing plant and mining equipment 100%factory direct price!
Iron Ore Processing Plant
iron ore crushing plant
This is a complete 500tph iron ore crushing plant layout. The raw ore is rock iron ore-magnetite, which uses dry iron ore processing technology. The iron ore process details and mining equipment are as follows:
iron ore crushing plant process
1. The dump truck feeds the raw ore into the hopper and the vibrating feeder. The vibrating feeder feeds evenly to the jaw crusher, which crushes large rocks to less than 200mm.
2. The jaw crusher output is sent to the transfer bin through the belt conveyor, and an electromagnetic vibrating feeder is installed below it. Convey the material less than 200mm to the first coarse cone crusher, and crush it to less than 100mm.
3. The cone crusher output is sent to the first and second vibrating screens through the belt conveyor. Among them, the materials exceeding 20mm are sieved and returned to the other two fine cone crushers for re-crushing through the belt conveyor. Materials smaller than 5mm are sent to the first and second magnetic separators.
4. The 5-20mm material under the first and second vibrating screens is sent to 4 double-roll crushers through the belt conveyor and crushed to 0-5mm. The output from the double roll crusher is sent to the third and fourth vibrating screens. Materials over 5mm are sieved and returned to the double-roll crusher for further iron ore processing. Those under the sieve under 5mm material are sent to the first and second magnetic separators. Then, the output will be sent to the third magnetic separator to separate again. Finally, the concentrate and tailings are sent to the stockpile by belt conveyor.
Iron ore washing Plant
This setup is for 50tph iron ore washing plant, the size range of the iron ore is 0-230mm.
Main processes includes feeding, crushing, washing, screening, grinding & classification, and magnetic separation. The specific iron ore processing plant details and equipment are as follows:
Iron ore washing Plant Flow
(1). The hopper + vibrating feeder (with grate) automatically feeds the material into the jaw crusher, and screens the 0-50mm material to the spiral washing machine.
(2). The jaw crusher crushes 50-230mm iron ore into the fine jaw crusher. Spiral washing machine is suitable for cleaning 0-50mm materials.
(3). The fine jaw crusher crushes the material to 0-20mm. The vibrating screen sends the 0-20mm material into the ball mill, and the +20mm material returns to the fine jaw crusher. Among them, the hopper + feeder is to feed the ball mill more smoothly and evenly. The ball mill and spiral classifier are combined to grind the iron ore to ensure the final product is 0.074mm.
(4). Magnetic separator separates iron ore concentrate and improves ore grade.
Note: If the material is contains slime, we have rotary scrubber, trommel screen or other ore washer optional. Contact us to customized iron ore processing plant and get equipment latest price according to your requirements.
Rlated Equipment
Contact Us Now
Ask us about mineral processing configuration and equipment quote! (No job, No investment)
Notice:
- We only provide mineral processing equipment and solutions; not buy and sell minerals/ ores/ materials.
- We do not recruit, don’t offer jobs, and are not interested in investments or partnerships.
- We value your privacy and keep your information safe.