Lead Zinc Ore Processing
Advanced Mineral Processing Turnkey Solutions | 95+% Recovery Rate | ISO Certified Equipment
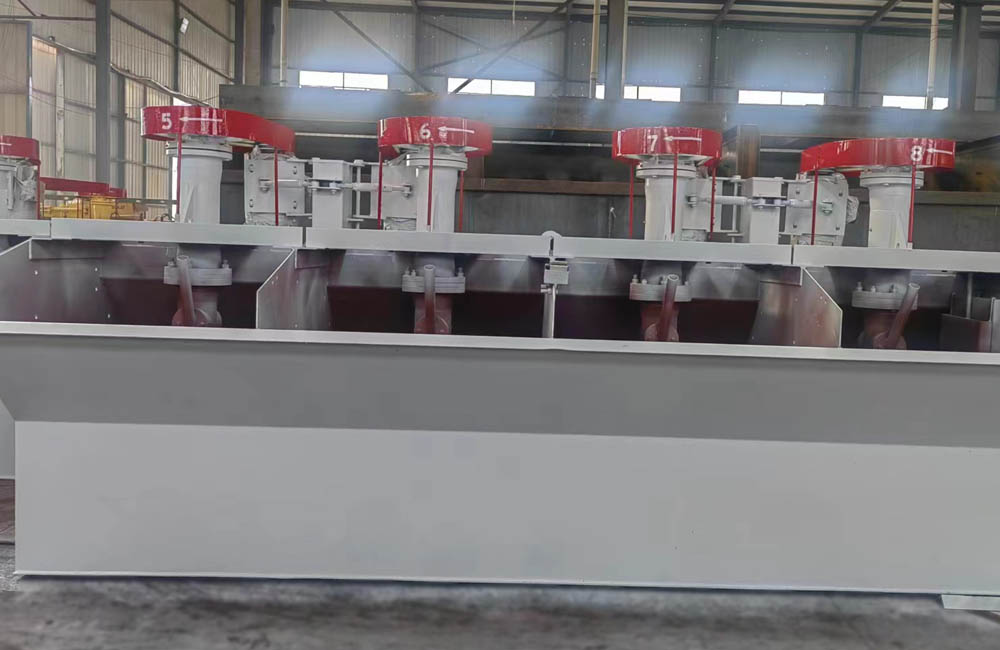
Lead-zinc ore usually exists in the form of sulfide ores, such as sphalerite and galena. Flotation is the most commonly used method. The lead-zinc ore processing solution is customized and used in combination according to ore characteristics, metal grade, and other factors, such as crushing, grinding, gravity, magnetic, flotation separation, concentration, and dehydration, in order to achieve the best beneficiation effect.
Application: Lead zinc processing plant is widely used for sulfide, oxidized lead-zinc ores (white lead ore, smithsonite), high-sulfur/high-arsenic lead-zinc ores, mixed ores, and complex associated ores, etc.
Lead Zinc Ore Beneficiation Process
The lead-zinc ore beneficiation aims to separate valuable metal components such as lead and zinc from raw ore and remove impurities, mainly including flotation, gravity separation, magnetic separation, etc.
Lead zinc ore process
- Flotation: It is one of the most commonly used methods in lead-zinc ore beneficiation. The method adds chemicals to the pulp to generate air bubbles on the surface of the lead and zinc minerals, thereby floating them into the flotation froth. Subsequently, the flotation froth can be collected and further processed to obtain a higher lead or zinc concentrate.
- Gravity separation: If the specific gravity of lead and zinc minerals differs greatly, the separation of lead and zinc ores can be achieved by gravity separation of ores in water.
- Magnetic separation: If the ore may contain some magnetic impurity minerals, the magnetic impurities can be removed from the lead-zinc ore through magnetic separation equipment to improve the quality of the lead-zinc concentrate.
- Electro-separation: A method that uses the different conductivity of ore particles in an electric field to achieve separation. It is suitable for lead-zinc ores with large differences in conductivity.
In practical applications, multiple leaz-zinc ore processes are often combined to achieve the best beneficiation effect and improve the concentrate grade and recovery rate, such as: crushing, grinding, classifying, mixing, flotation, dewatering, etc.
lead zinc ore processing Plant
lead zinc flotation process plant
The full lead-zinc ore flotation plant, main equipment and process details as follows:
- Jaw crusher
- Ball mill
- Spiral classifier
- Mixing tank
- Flotation machine
- Thickener
- Filter machine
1. Crushing & screening: Excavators or loaders send materials into the raw ore bin, and feed them to the jaw crusher through the chute feeder. Jaw crushers mainly crush large rocks to medium sizes of 40-100mm. Then, its output enters the fine jaw crusher through the belt conveyor and is crushed to a size of 20-60mm. The output of the fine jaw crusher enters the vibrating screen through the belt conveyor and sieves above 20mm and below 20mm. The vibrating screen here has one layer of sieve with a hole diameter of 20mm. More than 20mm on the sieve is returned to the fine jaw crusher through the belt conveyor for reprocessing.
2. Grinding & classifying: Materials less than 20mm under the vibrating screen enter the fine ore bin through the belt conveyor and are fed to the ball mill through the electromagnetic vibrating feeder. The ball mill can grind 0-20mm ore to 0-1mm powder size. The discharge from the ball mill is sent to the spiral classifier to form a closed grinding system so that more than 90% of the output is 200 mesh, which meets the flotation conditions.
3. Flotation separation: The underflow of the spiral classifier enters a slurry tank, sends it to the first stirring tank with a slurry pump, and then enters the first flotation machine to separate the lead.
- The concentrate of the first flotation machine enters a pulp tank and is pumped to the first thickener by a slurry pump. The thickener‘s underflow passes through the slurry pump and enters the first disc vacuum filter for dehydration, and the final product is lead concentrate. The tailings of the first flotation machine enter a slurry tank and are pumped to the second stirring tank by the slurry pump, and then enter the second flotation machine to separate zinc.
- The concentrate of the second flotation machine enters the first tank and is pumped to the second thickener by the slurry pump. The bottom of the thickener flows through the slurry pump and enters the second disc vacuum filter for dehydration, and the final product is zinc concentrate. The tailings of the second flotation machine enter a tank and are pumped to the third flotation machine to separate the barite by a slurry pump.
- The concentrate of the third flotation machine is in a tank and sent to the third thickener by a slurry pump. The bottom flow of the thickener passes through the slurry pump and enters the third disc vacuum filter for dehydration, and the final product is barite concentrate.
JXSC provide scientific and customized lead-zinc ore processing solutions, covering flotation, gravity separation, and combined processes, helping to achieve a recovery rate of 95%+. Tailings dry discharge and wastewater zero discharge technology achieve green mineral processing and maximize comprehensive benefits! Contact us now to get your exclusive lead-zinc ore dressing solution!
Reltaed Equipment
Contact Us Now
Ask us about mineral processing configuration and equipment quote! (No job, No investment)
Notice:
- We only provide mineral processing equipment and solutions; not buy and sell minerals/ ores/ materials.
- We do not recruit, don’t offer jobs, and are not interested in investments or partnerships.
- We value your privacy and keep your information safe.