Mineral Processing » Solutions » Tungsten Ore Processing
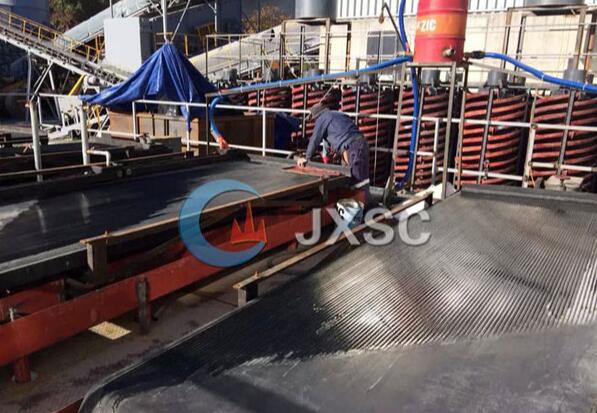
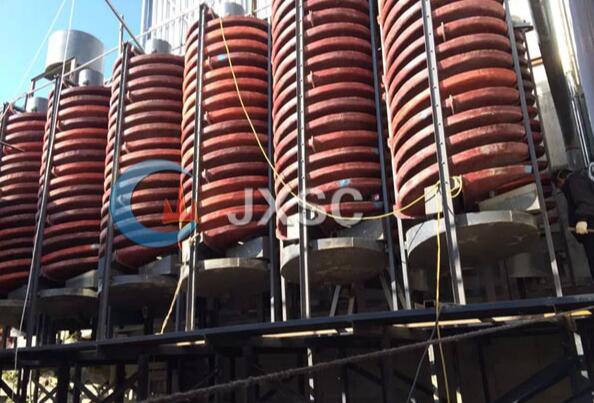
tungsten ore processing
Tungsten ore is divided into two types: wolframite and scheelite. Wolframite beneficiation is mainly gravity separation, supplemented by magnetic separation. Scheelite beneficiation mainly uses gravity separation, magnetic separation and flotation.
Different tungsten ore properties adopt different tungsten ore beneficiation process. JXSC support custom tungsten ore processing plants and equipment to maximize the recovery rate of concentrate.
Tungsten Beneficiation process
1. Wolframite beneficiation process
The main components of wolframite are tungsten, manganese, and iron, and the tungsten content can reach more than 50%. It is the main ore for extracting tungsten. It has high density and weak magnetic properties. Therefore, gravity separation is the main wolframite beneficiation method, supplemented by magnetic separation.
2. Scheelite beneficiation process
For scheelite with coarse particle size, general gravity separation method can obtain alloy scheelite; for scheelite with fine particle size, flotation method is more suitable. Scheelite beneficiation usually combines gravity separation, flotation and magnetic separation. Our scheelite flotation process is roughly divided into two parts: rough separation is to improve the recovery rate of scheelite greatly. To obtain qualified tungsten concentrates, multiple beneficiation is required to achieve the expected results.
tungsten ore processing plant
1. Wolframite Magnetic Separation
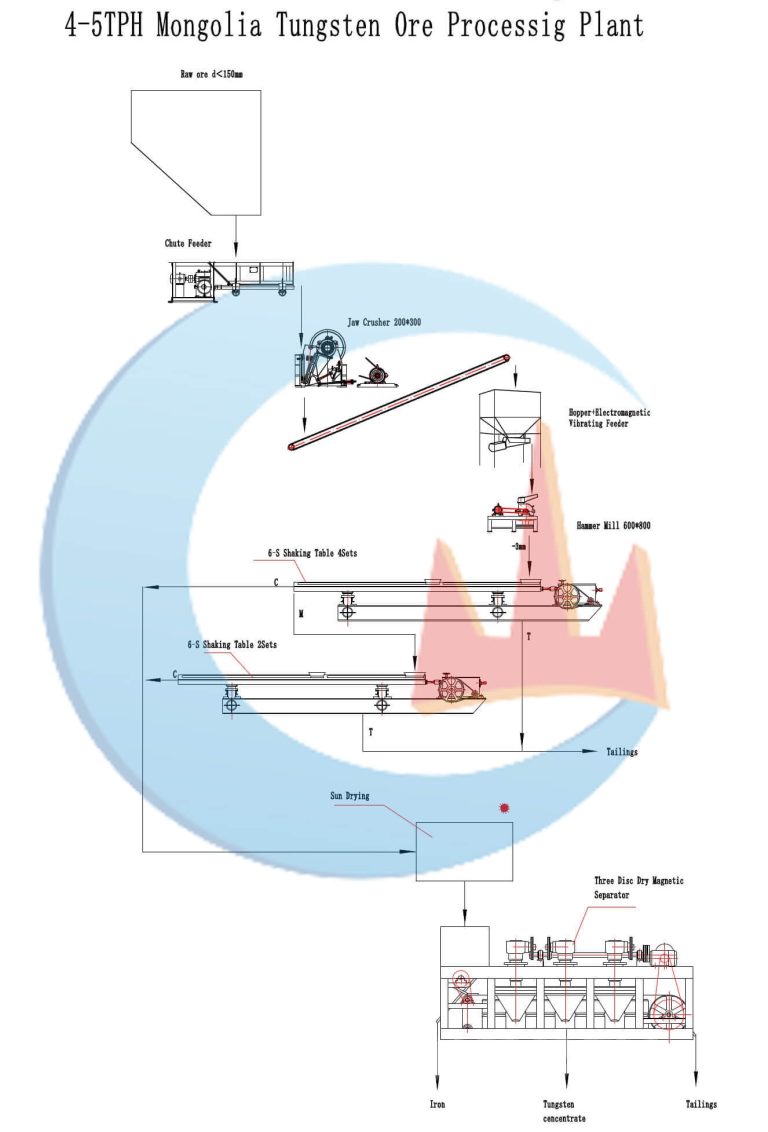
This is a complete set of 4-5TPH wolframite ore processing plant. Among them, the raw ore is 150mm, with a grade of 2-5%, and the equipment provided by JXSC can reach more than 65%. The following are the main processes and equipment:
(1). Crushing & grinding: The jaw crusher initially crushes the mining ore and the hammer crusher for fine crushing. After the crushing to reasonable fineness, the ball mill was evenly sent to the mining machine. On the one hand, it can avoid over -grinding. On the other hand, the particle size of the grinding products is relatively uniform.
(2). Gravity separation: The shaker table is characterized by a high enrichment ratio, high-grade concentrate and waste tailings can be obtained after one separation, the recovery rate is 80%.
(3). Concentration: Generally, gravity separation and flotation, or combined with magnetic separation for separating. Not only recycled magnet concentrates, but improved wolframite concentrates’ quality.
2. Scheelite flotation process
- Crushing & screening: Three-stage crushing is used here to crush ore, enter the vibrating screen for screening and the particle size reaches the following grinding condition.
- Grinding: The crushed ore is further finely ground by grinding equipment to improve mineral particles’ exposure and floatability to meet the flotation treatment’s particle size.
- Flotation: By adding reagents to the flotation machine, the ore particles absorb air bubbles and float up to realize the separation of tungsten. If needed, the impurities and mud in the ore are often separated from the concentrate by cyclone.
- Concentration: Use thickeners to concentrate the deslimed flotation concentrate on reducing the impurity content and improving the grade of tungsten.
- Dewatering: The concentrated ore is dehydrated through vacuum filter press to make it a relatively dry concentrate.
Contact Us Now
Ask us about mineral processing configuration and equipment quote! (No job, No investment)
Notice:
- We only provide mineral processing equipment and solutions; not buy and sell minerals/ ores/ materials.
- We do not recruit, don’t offer jobs, and are not interested in investments or partnerships.
- We value your privacy and keep your information safe.