In nature, it is very common for minerals to coexist with each other. With the gradual reduction of feldspar ore reserves, less and less feldspar can be directly exploited, and more feldspar with associated minerals, such as associated iron ore. In order to obtain high-grade feldspar concentrate, we will remove the associated minerals. The harmful impurities are mainly iron, titanium and other small impurities, which involve the iron removal process. With the rapid development of the industry, the development of special ceramics has caused technological changes in the ceramic industry, and put forward higher requirements for feldspar. Therefore, it is imperative to speed up the application research of feldspar processing.
Feldspar Ore
Feldspar is an aluminosilicate mineral containing calcium, sodium, and potassium. It has many kinds, such as albite, anorthite, barium feldspar, baro feldspar, microplagioclase, orthoclase, feldspar and so on. Widely used in ceramic blank, ceramic glaze, fireproof calcium silicate board, glass industry and enamel industry, abrasive tools, etc. Beautiful color and luster can be used as decorative stones and secondary gemstones. In addition, feldspar can also make potash fertilizer; feldspar with better quality is used to make glass bulbs for TV imaging.
In order to obtain high-grade feldspar concentrate, we will remove the associated minerals. The harmful impurities are mainly iron, titanium and other small impurities, which involve the iron removal process.
The occurrence state of iron in feldspar is:
- It is mainly composed of limonite, hematite and magnetite, with a particle size of >0.1mm, in the form of needles, spheres, and flakes. It is scattered in feldspar minerals and is easy to remove.
- In the presence of iron-containing gangue minerals, such as biotite, pyrite, ilmenite, epidote, amphibole, etc., such gangue minerals are also easy to remove
- The iron oxide formed by iron dyeing penetrates the surface of feldspar ore in a dripping form, or penetrates into it along the cleavage seam of feldspar and the fissure between minerals. The iron oxide formed by such iron dyeing is difficult to remove.
Feldspar Ore Remove Impurities Process
1. Magnetic Separation
The use of magnetic separation technology to remove iron from feldspar is suitable for the ore contained in the ore with strong magnetic properties. Because the magnetic separation process uses the different magnetic properties of iron-containing minerals in the ore to determine the corresponding magnetic separation process. Mainly use the different magnetic properties of iron-containing minerals in the ore to formulate a corresponding magnetic separation process, which can remove most of the strong magnetic ores. However, for some ores with a high degree of weathering, iron minerals are easily sludged during the grinding process, and it is difficult to remove these iron minerals by strong magnetic separation.
For weak magnetic minerals such as iron oxide, mica, and garnet in feldspar ore, strong magnetic separation should be used for separation. The selection of magnetic separation equipment needs to be determined according to the properties of the ore. Commonly used magnetic separation equipment includes wet drum magnetic separators, vertical ring pulsating high gradient magnetic separators, and flat magnetic separators.
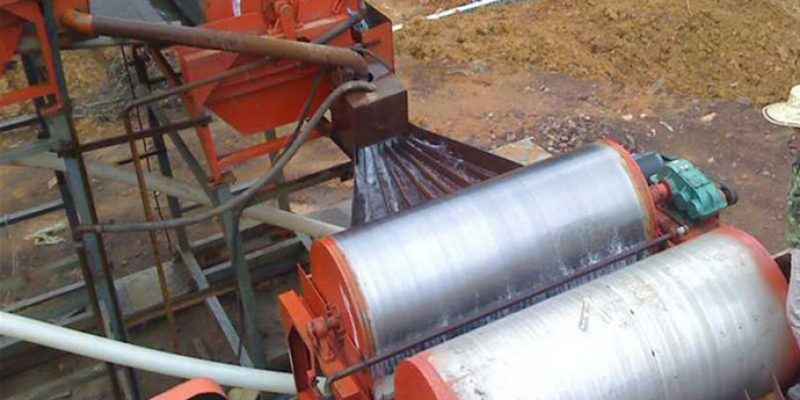
2. Flotation Separation
Iron removal by flotation process can be very good for iron-containing minerals in clay and fine-grained grades, but it is not effective for hard ores. For severely weathered ores, secondary sludge may be produced in the stage of crushing and grinding, which is likely to cause high viscosity of flotation foam, resulting in lower collector selectivity and poor effect. In addition, when the iron-containing impurities in the feldspar are pyrite, mica or garnet, tourmaline, amphibole and other iron-containing alkali metal silicate minerals, the flotation separation method is often used to remove the impurities.
The conditions for removing feldspar impurities by flotation are as follows:
- The sulfide ore is removed by flotation with xanthate collector under the natural pH condition of the pulp;
- For mica minerals, it can be removed in an amine collector system with a slurry pH of 2.5-3.5;
- For silicate minerals, when the pH of the pulp is 3-4, sulfonate collectors can be used to separate them to the surface.
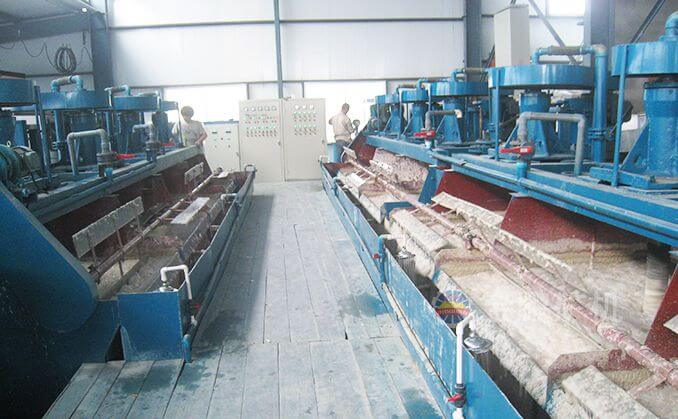
3. Acid Leaching Process
The acid leaching process is a method of using acid to selectively dissolve iron-bearing minerals and remove iron from feldspar. It is an effective method to process feldspar containing impurities embedded in the crystal structure of extremely fine size. Commonly used acids are hydrofluoric acid, hydrochloric acid, sulfuric acid, nitric acid, oxalic acid, etc.
The acid leaching process can well deal with severely weathered ores that are easily sludged by grinding, and the acid leaching process has high iron removal efficiency. However, the acid leaching waste liquid contains a large amount of metal ions such as iron, aluminum, potassium, and magnesium, which must be treated to meet the national emission standards before it can be discharged.
4. Biological Leaching Process
Bioleaching is mainly to remove iron-bearing minerals in fine particles of feldspar. Such iron-bearing minerals are difficult to remove by conventional methods, and the effect of bioleaching is better. Iron can become an energy source and electron carrier for some microorganisms, and it becomes soluble iron ions after oxidation and reduction reactions with microorganisms. The organic acid produced in the reaction process can also dissolve the impurity minerals, and then wash with water to remove the impurity minerals. Microorganisms can not only promote the decomposition of feldspar ore, but also remove iron-bearing minerals between the surface layers of feldspar. Therefore, when the quality of feldspar concentrate is high, other methods should be combined with bioleaching. Bioleaching has little environmental pollution and simple operation. There have been studies on it abroad, but there are few domestic studies.
In short, among the above four feldspar impurity removal processes, the magnetic separation impurity removal process is more environmentally friendly and easy to operate, and is one of the important processes for feldspar impurity removal. For feldspar with non-magnetic impurities, the flotation removal process should be adopted, and attention should be paid to the selection of reasonable flotation reagent system and operating parameters. For the difficult-to-select impurities in feldspar containing fine particles or in the form of iron staining, acid leaching process or combined impurity removal process should be adopted. When a single separation process cannot meet the requirements of the concentrate, a combined impurity removal process should be used. We will tailor the feldspar beneficiation process and equipment for you to help you obtain the ideal beneficiation process.