Bentonite is a water-containing clay rock with montmorillonite as the main component. It has special properties such as excellent swelling, adsorption, cation exchange, catalytic, cohesive, suspending and plasticity, and is known as “universal clay”. It can be used as mud, binder, cat litter, antidiarrheal, beverage clarifier, sauce clarifier, toothpaste additive, etc. It is widely used in daily life. The pure bentonite is very little and often contains various impurities. It needs mineral processing to meet the increasing demand of life and industry. Bentonite processing methods mainly include dry and wet beneficiation.
About Bentonite information
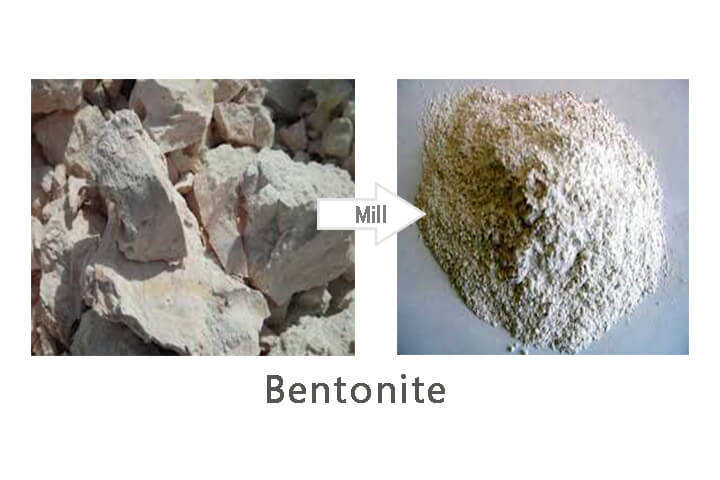
Bentonite often contain a small amount of illite, kaolinite, halloysite, chlorite, zeolite, quartz, feldspar, calcite, etc. Some bentonites are as loose as soil, and some are dense and hard. The main chemical components are silicon dioxide, aluminum oxide and water, and also contain iron, magnesium, calcium, sodium, potassium and other elements.
The main mineral component is montmorillonite, with a content of 85-90%. Some properties of bentonite are also determined by montmorillonite. Montmorillonite can be in various colors such as yellow-green, yellow-white, gray, white and so on. It can be dense block or loose soil. There is a slippery feeling when rubbing with fingers, and the volume of the small block will expand several times to 20-30 times after adding water, and it will be suspended in water, and it will be paste when there is little water.
Bentonite Processing Methods
1. Hand selection
Hand selection is generally carried out in the stope, and the waste rock in the ore is manually selected. Some mines are divided into sections and layers according to user requirements, and are stacked separately and processed separately. The manual processing flow is generally: raw ore – crushing – drying – grinding – packaging.
2. flocculation method
It is suitable for ore with a montmorillonite content of 30-40%, adding sodium hexametaphosphate as a dispersant, and the dosage is 600-800 grams per ton of raw ore. Polyacrylamide is a coagulant, and the amount used is related to the concentration of the pulp. The amount used is very small, and it is carried out in multiple stages. The time of precipitation is related to the concentration of pulp and the dosage of chemicals, and the quality of the product is related to the output. This method can get better quality products. The disadvantage is that the precipitation time is long, the floor area is large, and the production efficiency is low.
3. Dry processing Method
Dry beneficiation is generally used to process bentonite with better raw ore quality, or bentonite-rich ore with montmorillonite content of more than 80%. This method is to dry the raw ore in the sun, air dry it naturally or dry it in the oven. It is first crushed manually or with a jaw crusher, and then crushed with a Raymond mill and other roll mills into 100 mesh, 150 mesh, 200 mesh level products. This method is suitable for ores with high montmorillonite content and fine particle size, and coarse gangue minerals quartz and feldspar.
4. Wet processing method
Wet beneficiation is generally used to process low-grade bentonite with a montmorillonite content of 30%-80%. Since montmorillonite is relatively soft and has strong water absorption, it can disintegrate after being swollen with water. This method is to crush the raw ore to a particle size smaller than 50mm, and add water to make a suspension. Classification is carried out in a hydroseparator and the obtained fine-grade concentrate is concentrated in a precipitator. After drying in a dryer, it is then ground to obtain a product suitable for drilling mud grade.
Bentonite Processing Plant
The bentonite processing process is usually divided into screening, crushing, grinding, and packaging.
1. Screening: Screen the bentonite raw materials mined from bentonite mines to remove impurities and obtain bentonite raw materials;
2. Drying:
- Dry method – The process of dry preparation of bentonite is to dry naturally. Generally, the bentonite ore is spread on the drying yard, and then it can be dried completely by direct sunlight in summer for about one day.
- Wet method – bentonite has a high moisture content and needs to be dried by a dryer to reduce the moisture content.
3. Crushing: Large pieces of bentonite are crushed by the crusher to the fineness that can enter the mill.
4. Grinding: The crushed small pieces of bentonite are sent to the silo by the elevator, and then evenly and quantitatively sent to the ball mill (Raymond mill) by the vibrating feeder for grinding.
5. Finished product: After the qualified bentonite powder is packaged in a unified way, it can be sent to the market for sale.
Bentonite Processing Equipment
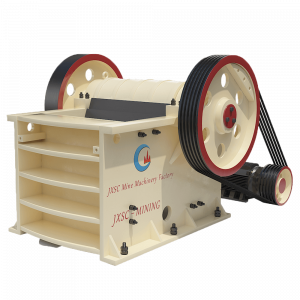
Jaw crusher is the equipment required in the initial stage of bentonite processing technology, mainly for coarse crushing of raw materials. It has advanced manufacturing technology, skilled production technology and good performance characteristics.
(1) The design of the jaw plate is reasonable, which effectively increases the contact area with the material, and then improves the crushing efficiency by more than 75%, and is durable;
(2) The crushing cavity is deepened, and there is no dead zone, and at the same time avoid clogging, so that the equipment operates stably;
(3) The structure is simple, the volume is small, the cost is low, and it can maintain high-efficiency operation regardless of the environment.
The product fineness of bentonite powder processing equipment Raymond mill is generally around 325-400 mesh. With the development of technological progress, the demand for finer powder products is increasing. Improve the ability to capture fine powder and reduce pollution to the surrounding environment. Compared with traditional mills, this mill can increase production by 40%-50% under the condition of consistent production capacity and fineness. The equipment has low wear, low noise, and less dust, which meets the national environmental assessment standards.
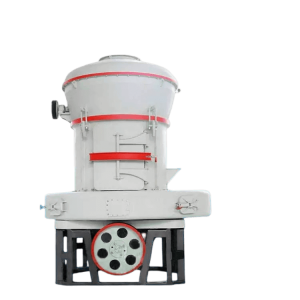
Bentonite is extremely rich in resources, and its reserves rank among the top in the world, accounting for 60% of the world’s total reserves. With huge reserves of bentonite resources and huge industry demand, the bentonite processing plant will be upgraded to a complete industrial chain with high added value. According to the nature of bentonite, the processing equipment used mainly includes jaw crusher, impact crusher, ball mill or Raymond mill, and some auxiliary equipment, such as feeder, powder classifier, conveyor machines, dust collectors, blowers, etc.