Vanadium is a transition metal element, which is very dispersed in nature, so it is also called a scattered element. Vanadium is widely used, and it is an indispensable and important element in industrial fields such as steel, non-ferrous metals, chemicals, alloys, superconducting materials, and automobiles. The comprehensive development and utilization of vanadium ore resources has very important strategic significance and industrial demand. Obtaining high-grade concentrates through the vanadium ore beneficiation process lays a good foundation for the rational use of resources.
Vanadium Ore
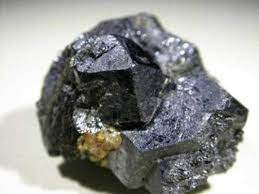
Vanadium is a silver-white metal with a high melting point, and it is called refractory metal together with niobium, tantalum, tungsten and molybdenum. In nature, vanadium is difficult to exist as a single body, and it mainly forms symbiotic ore ore with other minerals. At present, there are more than 70 kinds of vanadium-containing minerals, but the ore metal minerals are mainly vanadium-containing and titanium-magnetite (minerals composed of ilmenite, magnesium-aluminum spinel, ilmenite, and magnetite). Vanadium is in solid solution in magnetite, while titanium exists mainly in ilmenite solid solution in magnetite.
Vanadium Ore Beneficiation Methods
1. vanadium-titanium magnetite ore
Magmatic vanadium-titanium magnetite ore is the main resource of titanium and vanadium in my country. The main useful minerals in the ore are titanomagnetite and ilmenite, which are mainly distributed in medium grains; gangues are mainly silicate minerals, and some also have carbonate minerals and apatite; often associated with vanadium, sulfur and cobalt components. Vanadium and cobalt are often isomorphic to iron and occur in titanomagnetite and pyrite, respectively. The beneficiation of this kind of ore generally uses weak magnetic separation to separate the vanadium iron concentrate, and then uses the combined method of gravity separation, strong magnetic separation, flotation and electric separation. Recovery of ilmenite from tailings and pyrite by flotation. The titanium contained in ferrovanadium concentrate cannot be removed by beneficiation and can be separated in smelting. In order to meet the amount of slag necessary for ironmaking with high titanium slag, it is sometimes unreasonable to increase the iron grade of ferrovanadium concentrate too much. The process of recovering titanium from magnetic separation tailings must first ensure that high-quality titanium concentrate is obtained. Various processes such as gravity separation, flotation, gravity separation-flotation, gravity separation-strong magnetic separation-flotation, gravity separation-strong magnetic separation have been studied. The ilmenite concentrate is selected by electric separation, which can increase the grade of titanium dioxide to more than 48%. The flotation of ilmenite is carried out in acidic pulp, and the recovery of cobalt from flotation of pyrite should be carried out before flotation of ilmenite. If the ore contains carbonate minerals, it must be pre-floated.
There are two smelting methods for the extraction of vanadium in ferrovanadium concentrate: fire method and wet method. Pyrovanadium extraction is the vanadium-containing molten iron obtained by smelting vanadium-iron concentrate in a blast furnace, and then blowing vanadium slag in a converter. The vanadium slag is further refined by wet method to obtain vanadium-containing products. Pyrovanadium extraction has been used in industrial production, but the recovery rate of vanadium is low. Wet method vanadium extraction is to directly carry out sodium roasting and leaching of iron concentrate to obtain vanadium-containing and iron-containing products, and the iron-containing products are sent to ironmaking. Wet vanadium extraction has better comprehensive utilization of resources and higher recovery rate of vanadium, but it is still in the stage of industrial experimentation. The method for extracting vanadium from hydrothermal type vanadium-containing iron ore is the same as above.
2. Placer Ilmenite ore
The titanium minerals in titanium placer are mainly ilmenite, with less rutile, white titanium and anatase. It often coexists with zircon and monazite, etc., and the heavy sand minerals are in a fine-grained state; the gangue is mainly silicate minerals. The combined process of gravity separation, magnetic separation and electric separation is adopted in production. The placer is pre-enriched by conical concentrator, fan chute, spiral concentrator, jig or shaker. The rough concentrate containing heavy sand minerals is obtained, and then the ilmenite is recovered by medium and high-intensity magnetic separation; the monazite is recovered by high-intensity magnetic separation. Shaking table to remove gangue; electroseparation to separate zircon and rutile to obtain various concentrates. In order to obtain qualified concentrates, generally there are many operations in the beneficiation process of rough concentrates, and the changes are large. Sometimes ilmenite concentrates are further dephosphorized by flotation.
In addition to vanadium-titanium magnetite ore and titanium placer, there are also a few veins of titanium. The metamorphic basic rock type rutile ore is tested by gravity separation-strong magnetic separation-electric separation, flotation and flotation-roasting magnetic separation to obtain rutile concentrate. The gabbro-type apatite-containing ilmenite ore was tested by flotation-gravity separation to obtain two concentrates of ilmenite and apatite.
Due to the limited resources of high-titanium minerals, various methods of producing rutile from ilmenite have been studied. For example, choose the chlorination method and the reduction rust method.
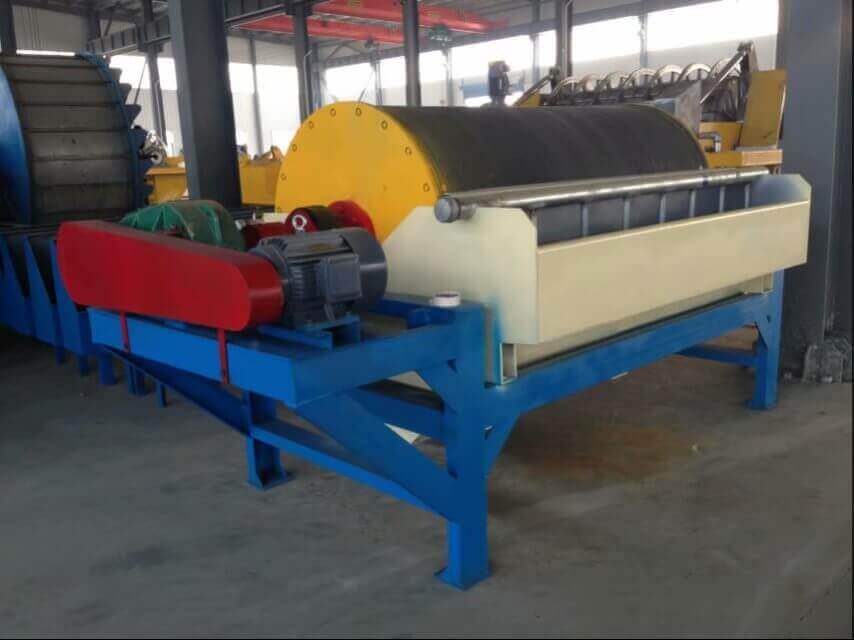
3. Vanadium-bearing carbonaceous slate
Vanadium-bearing carbonaceous slate. Sedimentary vanadium-bearing carbonaceous slate is also an important type of vanadium ore resources in my country, and it is still in the research stage. Vanadium in the ore exists in the form of minerals such as micro-embedded vanadium mica or in an attached state. It is not easy to be enriched by beneficiation method, so the hydrometallurgical extraction of vanadium was studied. The ore is first calcined to remove carbon, and then sodium roasted and water leached. Acid leaching of water leaching residue can further increase the leaching rate of vanadium. Sometimes raw ore is enriched into vanadium-containing coarse concentrate through flotation, and then roasted and leached, which can significantly reduce acid consumption.
vanadium-titanium magnetite ore Processing
Vanadium-titanium magnetite ore benefication process, inclding below equipment:
- Ball mill
- Spiral classifier
- Magnetic separation
- Dewatering machine
- Filter machine
- Thickener
Grinding: The raw ore enters the ball mill for grinding, and works together with the classifier to form a closed-circuit ring mill.
Separation: After two stages of magnetic separation, iron ore and other magnetic impurity minerals are separated.
The concentrate enters the dehydrator for dehydration, and the filter press presses the concentrate into a filter cake. The tailings enter the thickener for concentration, and the overflow water is used as circulating water.
The types of vanadium ore, the embedded particle size, and the properties of the ores are different. It is necessary to design the beneficiation process and equipment configuration according to the actual situation and the properties of the ore. The separation of flotation and magnetic separation processes is finally determined by comprehensively considering factors such as the actual situation of the processing plant, investment budget and other factors. Contact us to get the process and equipment price!