Fluorite is a non-metallic raw material with strategic significance, mainly used in the three major industries of metallurgy, chemical industry and building materials, followed by light industry, optics, sculpture and national defense industry. In production practice, the beneficiation methods of fluorite ore mainly include hand separation, gravity separation and flotation. Among them, the hand separation method is often used as an auxiliary means, and the gravity separation method is suitable for the production of metallurgical grade lump ore or as a gravity separation operation for the fluorite flotation process. In view of the depletion of fluorite ore and the intercalation of fluorite and gangue, flotation has become the main beneficiation method for separating fluorite and gangue minerals. The purity of fluorite directly affects the use of fluorite, beneficiation and flotation technology directly determine the grade and recovery rate of fluorite. Today, with increasingly stringent environmental protection requirements, the application of fluorite flotation also promotes the improvement and application of fluorite gravity separation technology and equipment to a certain extent.
types of Fluorite ore
According to the different gangue minerals, fluorite ore is divided into quartz-type fluorspar ore, carbonate-type fluorspar ore, barite-type fluorspar ore and sulfide-type fluorspar ore.

Quartz-type fluorite ore: the main minerals are fluorite and quartz, and the fluorite content can reach 80% to 90%. Contains a small amount of calcite, barite and sulfide. Quartz-type fluorite ore is mainly composed of fluorite (up to about 85%) and quartz, with only a small amount of calcite, barite and sulfide. The key to sorting lies in the silicon reduction of the concentrate. To separate quartz from fluorite, it is necessary to dissociate the quartz and fluorite monomers through grinding, so grinding is an important factor affecting the flotation of quartz-type fluorite.
Carbonate fluorite ore: the main minerals are fluorite and calcite. Calcite content can reach more than 30%, with a small amount of quartz, sometimes composed of quartz-calcite-fluorite ore.
Barite-type fluorite ore: the main minerals are barite and fluorite, and the content of barite is 10% to 40%. This type of ore is often accompanied by pyrite, galena, sphalerite and other sulfides, and sometimes the content of quartz increases to form a quartz-barite-fluorite ore. The flotation of barite-type fluorite ore generally first adjusts the pH value of the ore pulp through the process of mixed flotation and Na2CO3, and uses oleic acid and water glass as collectors and inhibitors respectively to obtain the fluorite and barite. The concentrates are mixed and flotation is used to barite separation.
Sulfide-type fluorite ore: its mineral composition is basically the same as that of quartz-fluorite, but it contains more metal sulfides, and sometimes the content of lead and zinc can reach industrial grades. Sulfide ore-type fluorite mines generally use sulfide ore collectors to preferentially select metal sulfide minerals, and then use fatty acid collectors to recover fluorite from flotation tailings.
Fluorite ore flotation methods
(1) For fluorite ore containing sulfide: the sulfide ore is generally floated out with xanthate collectors, and then the fluorite is floated with fatty acid reagents. Sometimes in fluorite flotation operations, a small amount of sulfide ore inhibitors (such as cyanide) are added to suppress residual sulfide to ensure the quality of fluorite concentrate.
(2) For the separation of fluorite, barite and calcite: oleic acid is generally used as a collector to float out fluorite. When using oleic acid to float fluorite, a small amount of aluminum salt is added to activate fluorite, and dextrin is added to suppress barite and calcite. For complex fluorite mines containing more calcite, limestone, dolomite, etc., it is better to use tannin extract and lignosulfonate to inhibit these gangue minerals.
(3) Separation of fluorite and quartz: use fatty acid as a collector to float fluorite, water glass as an inhibitor of quartz, and sodium carbonate to adjust the pH value of the pulp to 8-9. The amount of water glass should be well controlled. A small amount can activate fluorite, but the inhibitory effect on quartz is not enough, and fluorite will also be inhibited when it is excessive. In order to minimize the amount of added water glass and achieve the inhibitory strength of quartz gangue, polyvalent metal ions, alum, aluminum sulfate, etc. are often added at the same time as water glass is added.
(4) Separation of fluorite and barite: Generally, fluorite and barite are mixed and floated first, and then separated. In mixed flotation, oleic acid is used as collector and water glass is used as inhibitor.
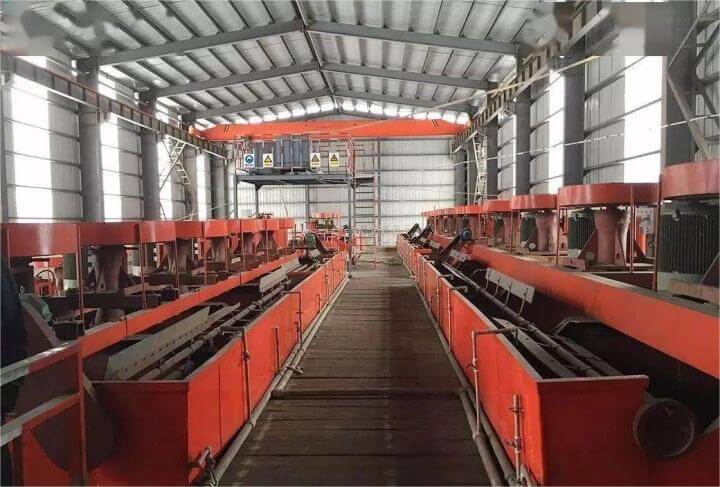
Influencing factors
Comprehensively analyze the properties of ore, and customize a scientific flotation process in combination with the actual situation of the dressing plant and the investment budget. Follow a reasonable flotation agent system to obtain ideal economic benefits and beneficiation indicators.
1. Appropriate grinding fineness
It is necessary to choose the appropriate grinding fineness according to the embedded particle size of the effective minerals, so that the effective minerals and the gangue are generally dissociated, and the joints of the fluorite ore and the gangue minerals are minimized. It is necessary to avoid that the ore grinding fineness is too fine, which will cause the material to be over-grinded and muddy in the fluorite flotation process.
2. Properly increase the slurry temperature
Properly increasing the slurry temperature can improve the flotation index of fluorite
When the temperature is higher, the solubility of the carboxylic acid collector in the pulp increases, and it is easier to disperse, and the ability to collect fluorite ore is also stronger, and the recovery rate of fluorite ore is higher.
However, if the dissociation of fluorite ore is not complete, some gangue minerals will be separated out together with fluorite ore, which will result in lower quality of fluorite ore.
When the temperature is low, the collection ability of carboxylic acid collectors is weak, but some fluorspar ores with better buoyancy will still be sorted out. At this time, the quality of fluorite ore is high, but the recovery rate is low.
3. Dosage of inhibitors
Inhibitors mainly use water glass, followed by sodium metaphosphate, tannic acid, baked gum, starch, dextrin, lignosulfonate and so on. Among them, water glass is a commonly used inhibitor in fluorite flotation machine separation.
In order to improve the selective inhibitory ability of water glass, water glass and soluble salt can be formulated as a combined inhibitor.
4. Maintain proper slurry level
In the process of fluorite flotation beneficiation, the fluorite minerals with better buoyancy will preferentially reach the top layer of the foam layer. When the slurry level is low, the grade of fluorite concentrate is high, but its recovery rate is low; when the slurry level is high, the recovery rate of fluorite concentrate is high, but its ore grade is low.
5. PH value of pulp
When oleic acid is used as collector and the pH value is 8-11, the buoyancy is better, and the recovery rate of fluorite ore can reach 80%-90%.
6. Pre-softened water
When the water quality is relatively hard, the flotation fluorite water needs to be pre-softened before entering the flotation separation stage, such as adding sodium carbonate for softening.
7. Optimize the flotation process
When the middle ore returns in sequence, part of the gangue ore will always circulate in the fluorite flotation system, unable to throw the tail, thus affecting the fluorite flotation beneficiation index.
At this time, some middle ore with high gangue mineral content can be selected for concentrated re-election, and then the fluorite concentrate can be selected and returned to roughing, and the tailings can be directly thrown out.
The types of fluorite mines, the embedded particle size, and the properties of the ores are different. It is necessary to design the beneficiation process and equipment configuration according to the actual situation and the properties of the ore. The separation of fluorite flotation and gravity separation processes is finally determined by comprehensively considering factors such as the actual situation of the processing plant, investment budget and other factors. Contact us to get the process and equipment price!