Chrome ore usually exists in the earth’s crust in the following forms: chromite, which is a dark, black-to-brown-black mineral composed of chrome, iron, and oxygen. It has an affinity for oxygen and iron, so the minerals with industrial value are generally chrome-magnesium spinel or chrome-iron spinel. As an essential raw material for stainless steel, chrome has always been a vital metal resource with a wide range of uses, and its demand is closely related to the demand for steel.
Chrome ore is a magmatic mineral produced in ultrabasic rocks. When the ore-bearing stones are weathered and damaged, they are often transferred to sand mines. The amount of heavy chrome minerals often far exceeds that of chrome ore. Therefore, the ore must be beneficiated before smelting, and most useless materials must be discarded. However, alluvial chrome minerals must be cleaned and processed to present a rich and diverse state. Regarding equipment selection, washing and gravity separation are mainly used to obtain chrome concentrate.
What Is Chrome Ore Washing Plant
The raw materials are mainly soil and clay. The chrome ore washing plant mainly includes washing and gravity separation processes to extract high-quality concentrates. Magnetic separation technology is needed to remove impurities if the ore contains iron minerals.
First, it must be washed, and the ore is separated from the mud by hydraulic flushing or additional mechanical scrubbing. Then, the minerals are separated according to the difference in relative density (usually called specific gravity) of the iron ore. The gravity separation process uses mineral pullers of different densities in the moving medium (water, air, and heavy rolling) to be affected by fluid power and various chromite ore dressing mechanical forces, resulting in suitable loose stratification and separation. However, chrome ore contains more or less iron. Gravity separation–magnetic separation is a commonly used mineral processing process to separate iron from chrome better.
Main Equipment Of Chrome Ore Washing Plant
Trommel screen
The trommel screen is used to screen and clean materials according to their particle size. By continuously rolling the materials up and down, the materials on top will fall under the influence of gravity and centrifugal force and will not block the screen holes. Different screen hole diameters can be designed, and the primary purpose is to remove mud and impurities. This machine is usually used when the surface of chrome ore contains a small amount of sticky mud. It is easy to install, runs smoothly, and costs less.
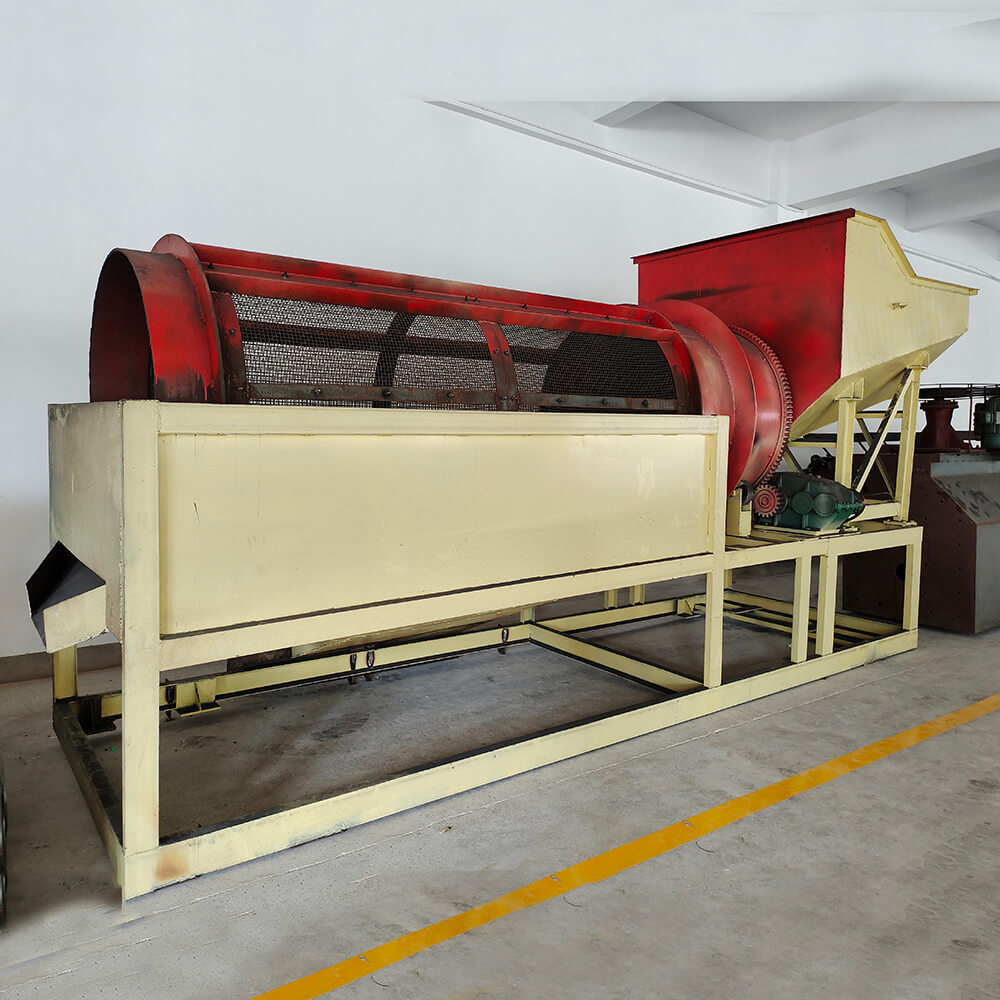
Rotary scrubber
The rotary scrubber is used to clean and screen ore with large mud content but is challenging to wash. The long washing cylinder allows the material to stay inside for a long time, with a vigorous scrubbing ability. The high-pressure washing water washes the inner wall, thoroughly and powerfully dispersing the material completely. The primary purpose is to eliminate the influence and harm of the sticky mud on the remaining operations. This equipment is usually used when the surface of the chrome ore contains a lot of clay and impurities. It has a large processing capacity and a cleaning efficiency of up to 99%.
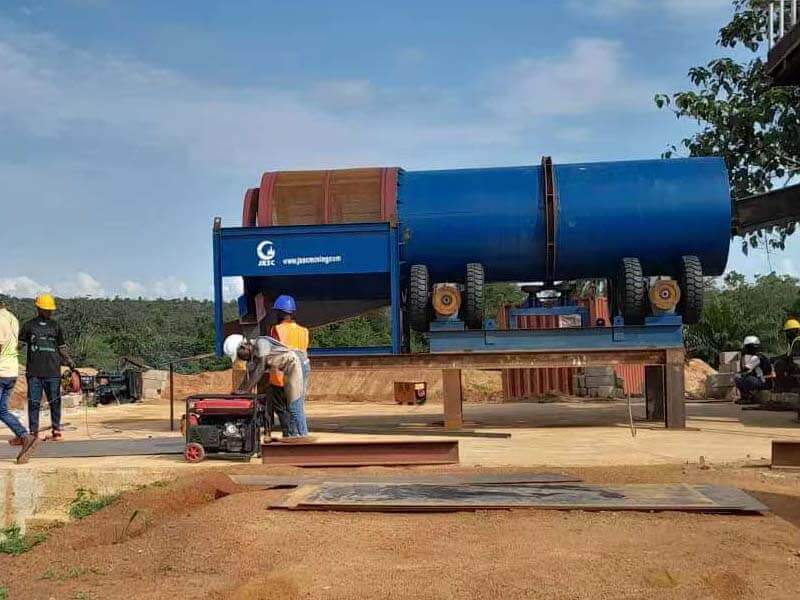
Shaking table
The shaking table is one of the chrome gravity separation equipment used to select fine-grained minerals. The concentrate chosen has a high enrichment ratio. The gravity and the horizontal water flow force make the materials move in different directions according to their density and particle size. The materials spread out in a fan shape on the bed surface and are discharged along the edge of the bed surface in sequence. The discharge line is very long, and the concentrate, middlings, and tailings can be selected at one time. The embedded particle size of chromium ore in the ore is generally coarse, and there is a large difference in specific gravity between ferrochrome and waste rock. This machine is usually used for sorting.
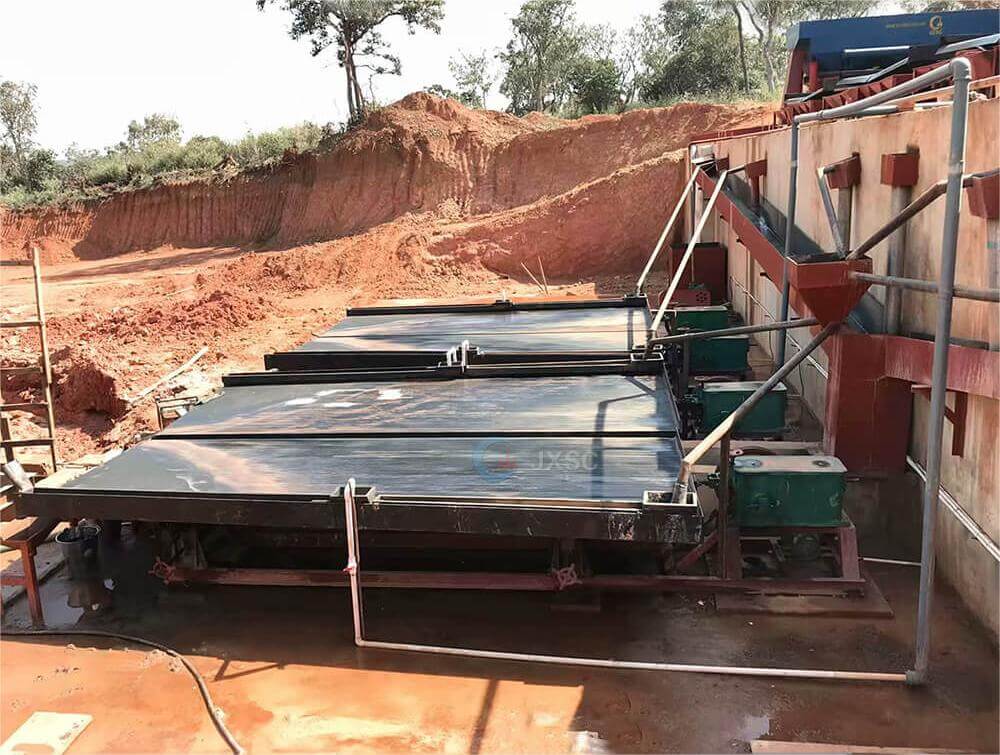
Spiral chute
The spiral chute is a highly efficient gravity separation equipment that uses the inertial centrifugal force generated by the slurry in the spiral rotation motion to separate the light and heavy minerals. It is widely used in iron ore, ilmenite, chromite, tantalum and niobium ore beneficiation plants. It is made of special materials and is durable.
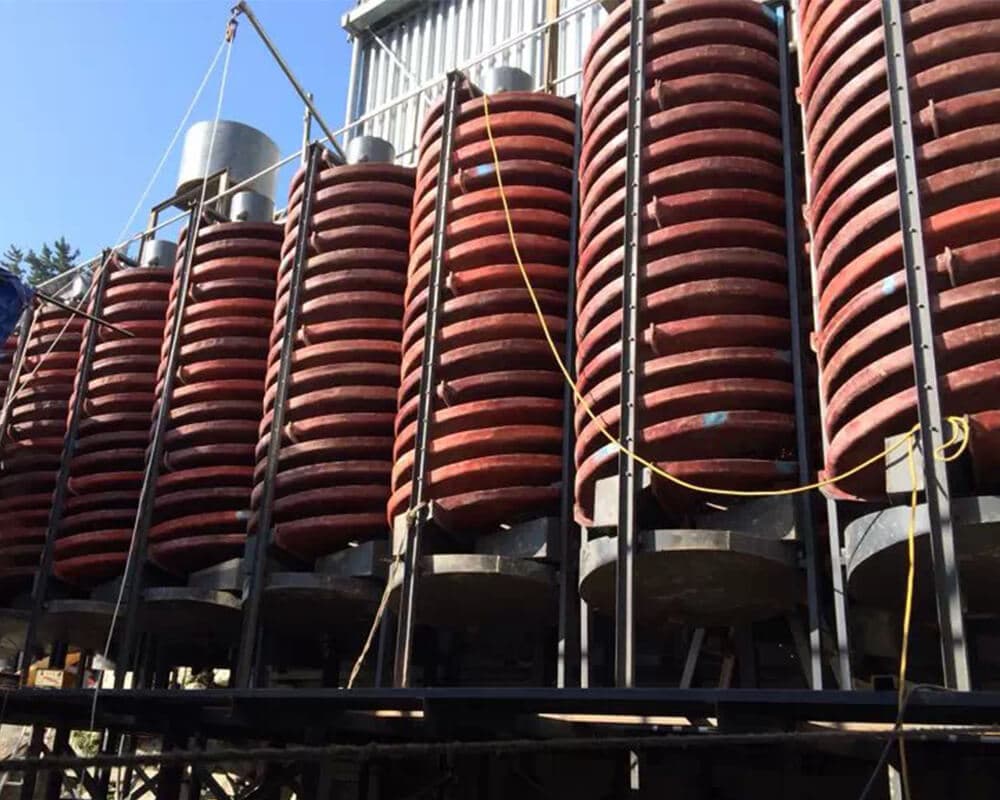
3.Magnetic separation equipment
Drum magnetic separator
The drum magnetic separator is used to separate iron-containing impurities below 3 mm and can automatically remove magnetic contaminants that are difficult to separate from non-magnetic materials. The material is evenly fed to the magnetic field area on the upper part of the rotating drum through an electromagnetic vibrating feeder. The magnetic material is adsorbed on the surface of the drum and rotates with the drum. Since magnetic and non-magnetic particles are subjected to different forces in the magnetic field, weakly magnetic and non-magnetic minerals will be removed after separation. Chromite is an oxide of iron, magnesium, and chromium. Using a drum magnetic separator is an environmentally friendly purification process.
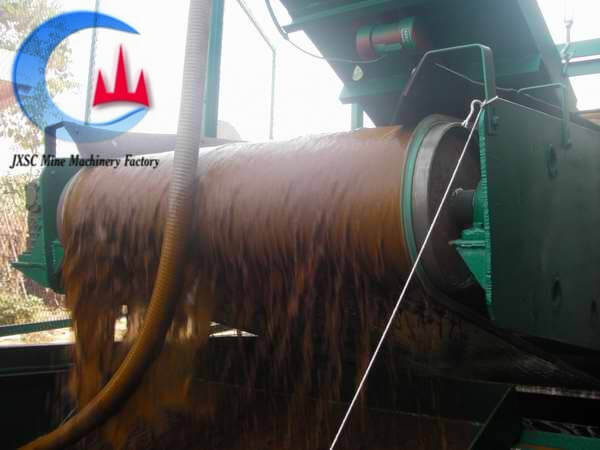
Chrome Ore washing plant
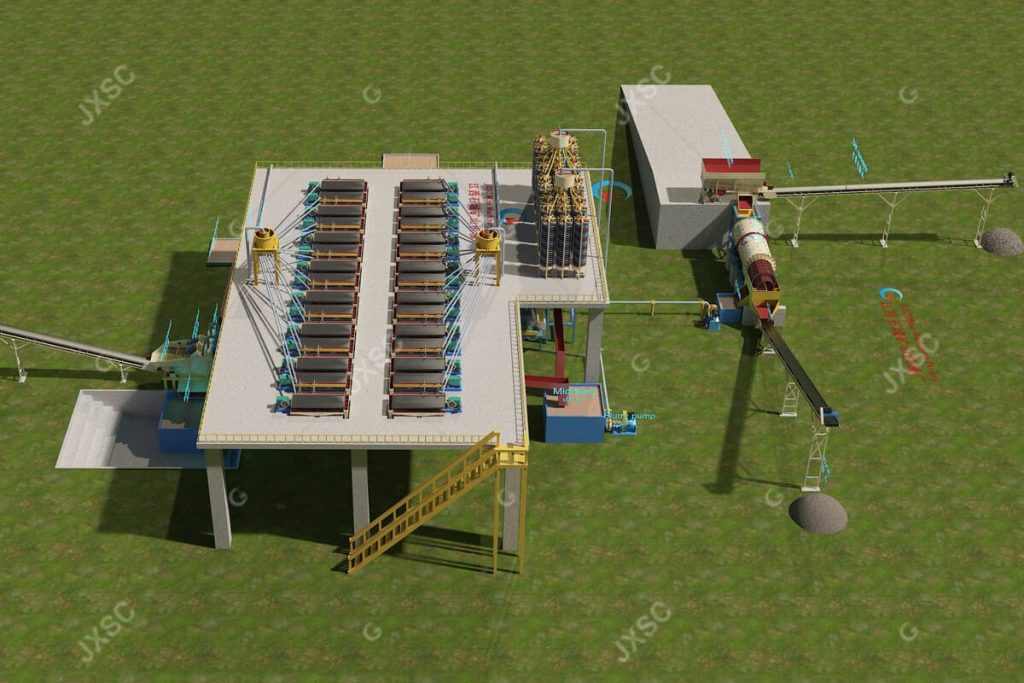
100TPH alluvial chrome ore washing process plant
1. The raw materials are unloaded from the excavator to the raw material bucket and then evenly fed to the drum washer by the vibrating feeder. The vibrating feeder has a screen with a gap of 70mm to prevent large stones from being contained in the raw materials. Large rocks larger than 70mm can be removed from the screen feeder.
2. The trommel scrubber is used to wash the raw materials and screen out waste materials larger than 2mm. The raw materials are mostly soil and clay, which must be cleaned by the drum washer first (2 layers of PU screens) with mesh sizes of 2mm and 20mm. The 20mm PU screen protects the 2mm mesh.
3. After the efficient washing and screening by the drum washer, the -2mm material is swiftly pumped to the roughing spiral chute, a total of 18 sets. The roughing selected materials are then efficiently pumped to the fine spiral chute for further sorting to improve the recovery rate. There are 9 fine spirals, with a total of 27 sets of spiral chutes, ensuring the process is highly productive.
4. All chrome concentrates from the roughing and fine spiral go into the magnetic separator to reduce some magnetite iron, thereby improving the chromium/iron ratio.
5. The chrome concentrate from the magnetic separator, a highly effective tool, is pumped to the shaking table, and a total of 30 sets of shaking tables are used. Every 15 sets of shaking tables correspond to a distribution tank, and a pump is used to send the chrome concentrate to the distribution tank and then distributed to each set of shaking tables. The shaking table – the final fine separator, is a testament to the quality of our process, effectively further improving the chromium grade in the concentrate to meet customer requirements. The middlings from all shaking tables are returned to the selection spiral chute for re-separation to improve the recovery rate. Then, the tailings from the shaking table are sent to the sedimentation tank.
6. The chrome concentrate from all shaking tables is sent to the spiral dewaterer to remove most of the moisture. The underflow of the spiral dewaterer enters the dewatering screen for further dewatering, so the dewatered concentrate can be transported to the finished product pile by a belt conveyor. The overflow of the spiral dewaterer and the under-screen slurry are returned to the hydrocyclone by the pump. The cyclone overflow enters the sedimentation tank, and the overflow enters the dewatering screen, which is the whole process of the dewatering system.
Reasonable equipment selection and scientific production line process design are helpful to improve the grade of chrome ore and promote the recovery efficiency of chrome concentrate. How to choose specific chrome ore washing plant equipment? JXSC supports customized mineral processing equipment and solutions. Contact us online for details!